施工の見どころ
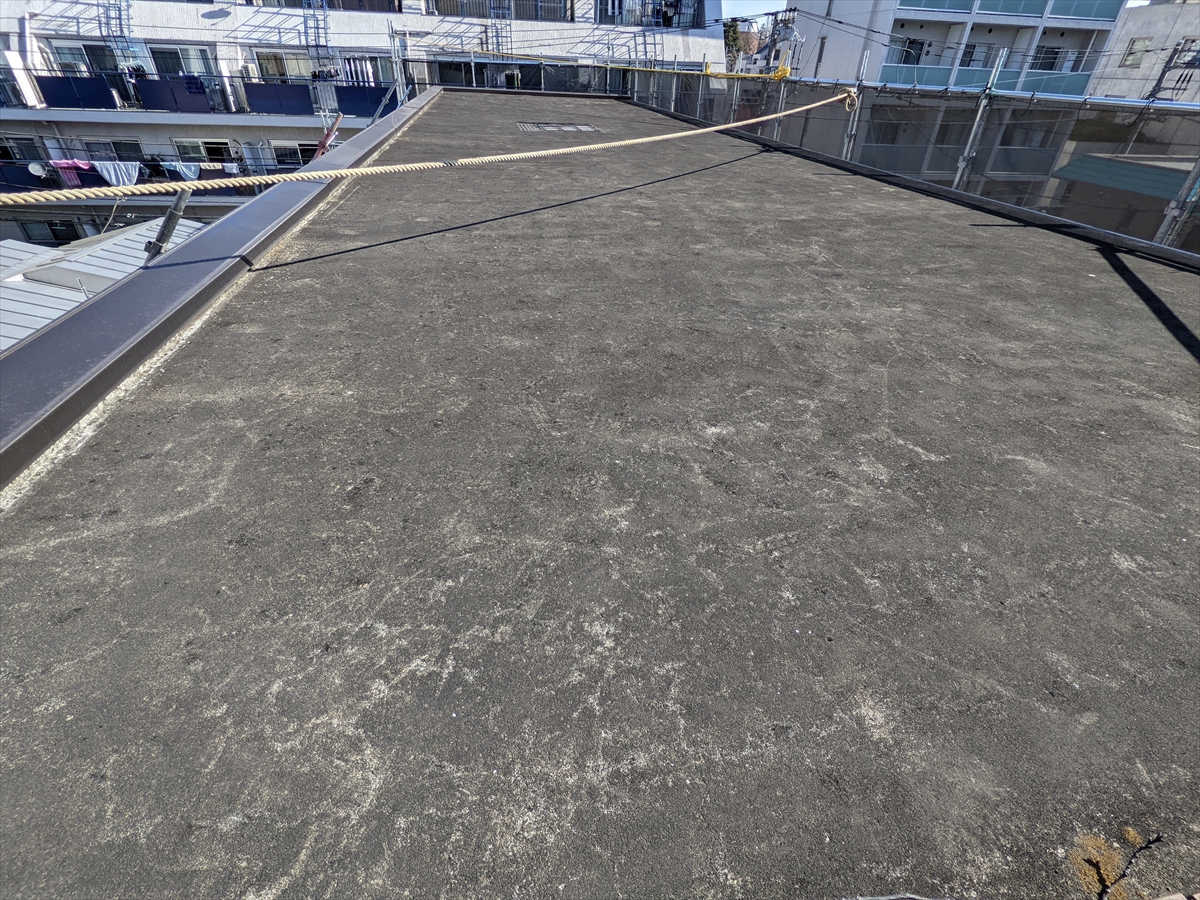
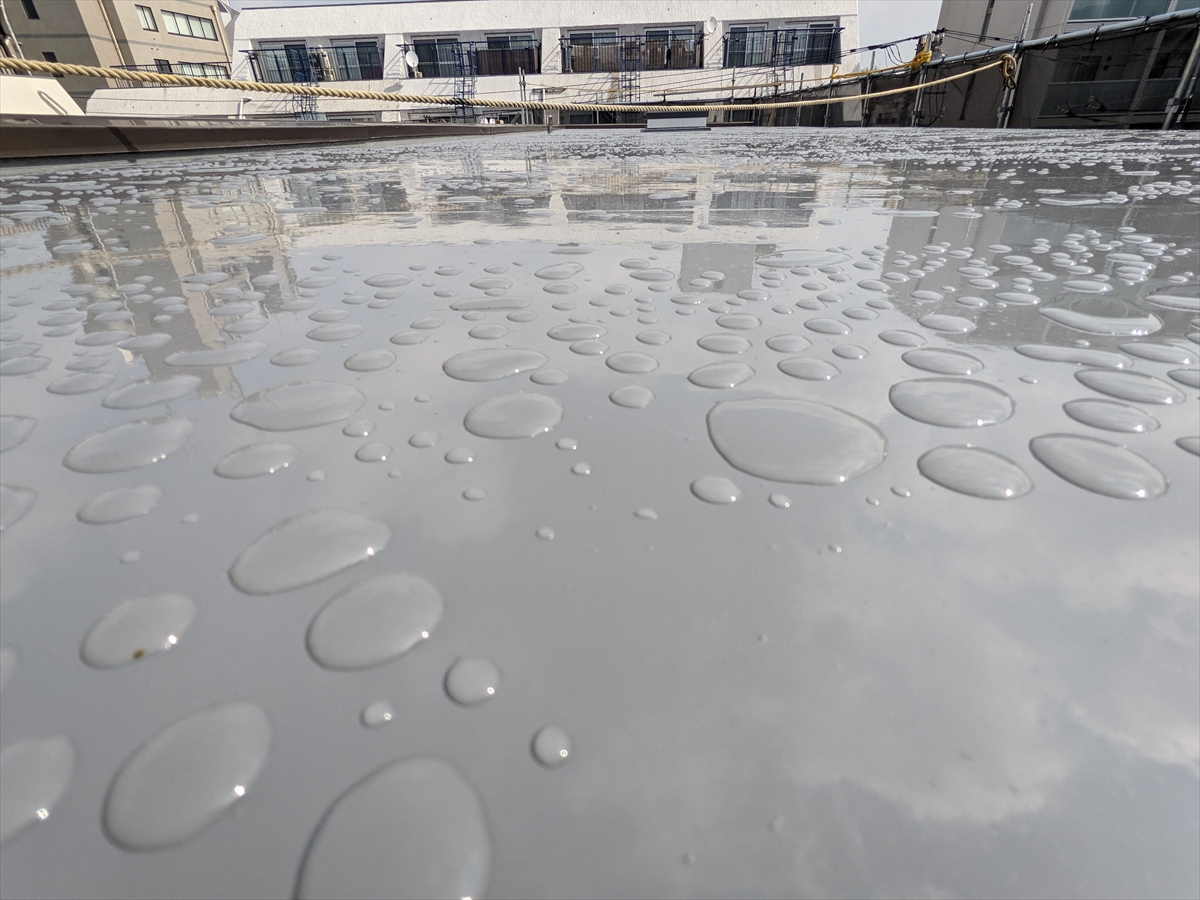
施工前
今回の現場で行うウレタン防水工事は屋上とバルコニー、そして外壁にある庇となります。建物全体の埃などを落とす高圧洗浄、いわゆる「水洗い」と呼ばれる作業を終わらせたので、屋上のウレタン防水から手を付けていきます。まだ何も手付かずの屋上です。だいぶ床面が荒れています。
また、屋上のモルタルが剥き出しになっていることから、既存の防水が無く新規の防水工事であることが分かります。50平米以上あるので、脱気筒の設置が必要となるため密着工法ではなく通気緩衝と呼ばれる工法でウレタン防水を施工していきます。水洗いが終わった、施工前の屋上の様子です。
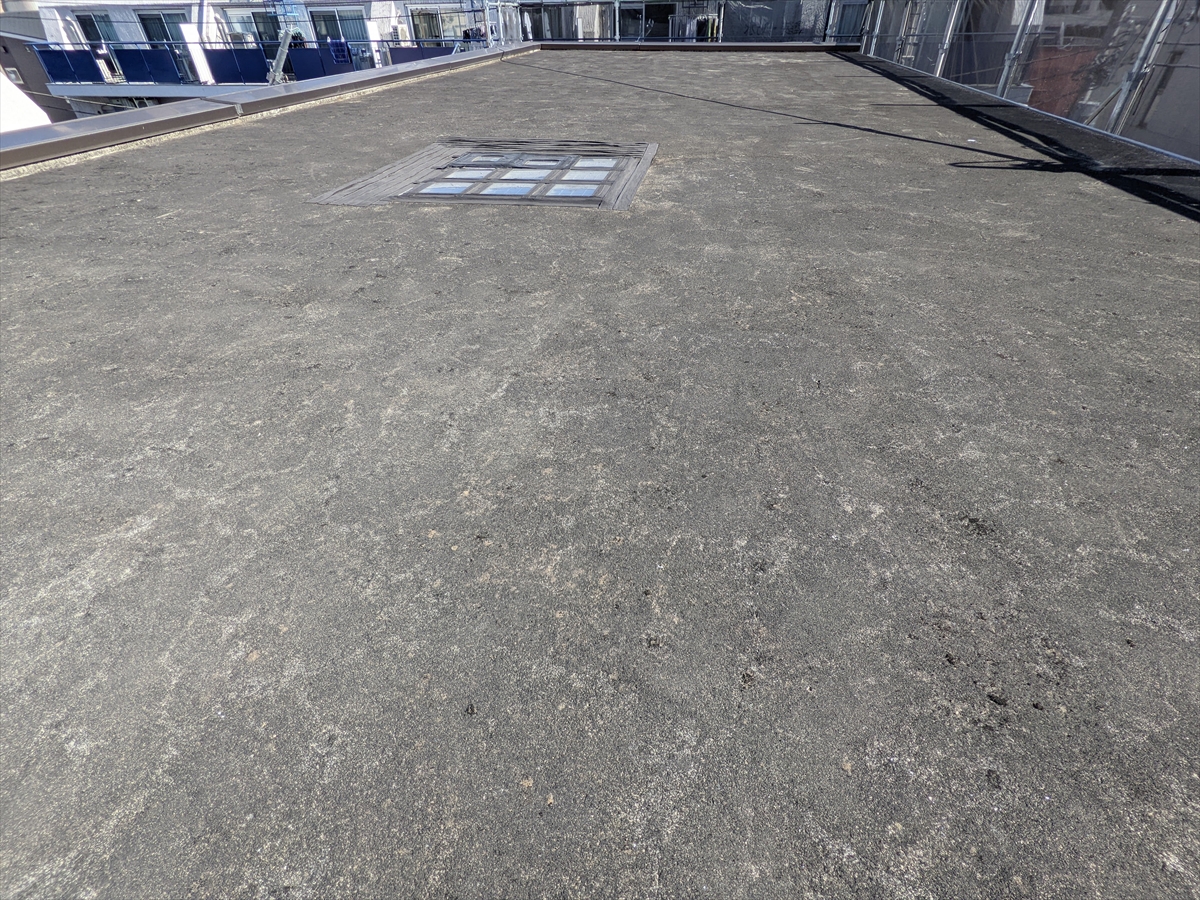
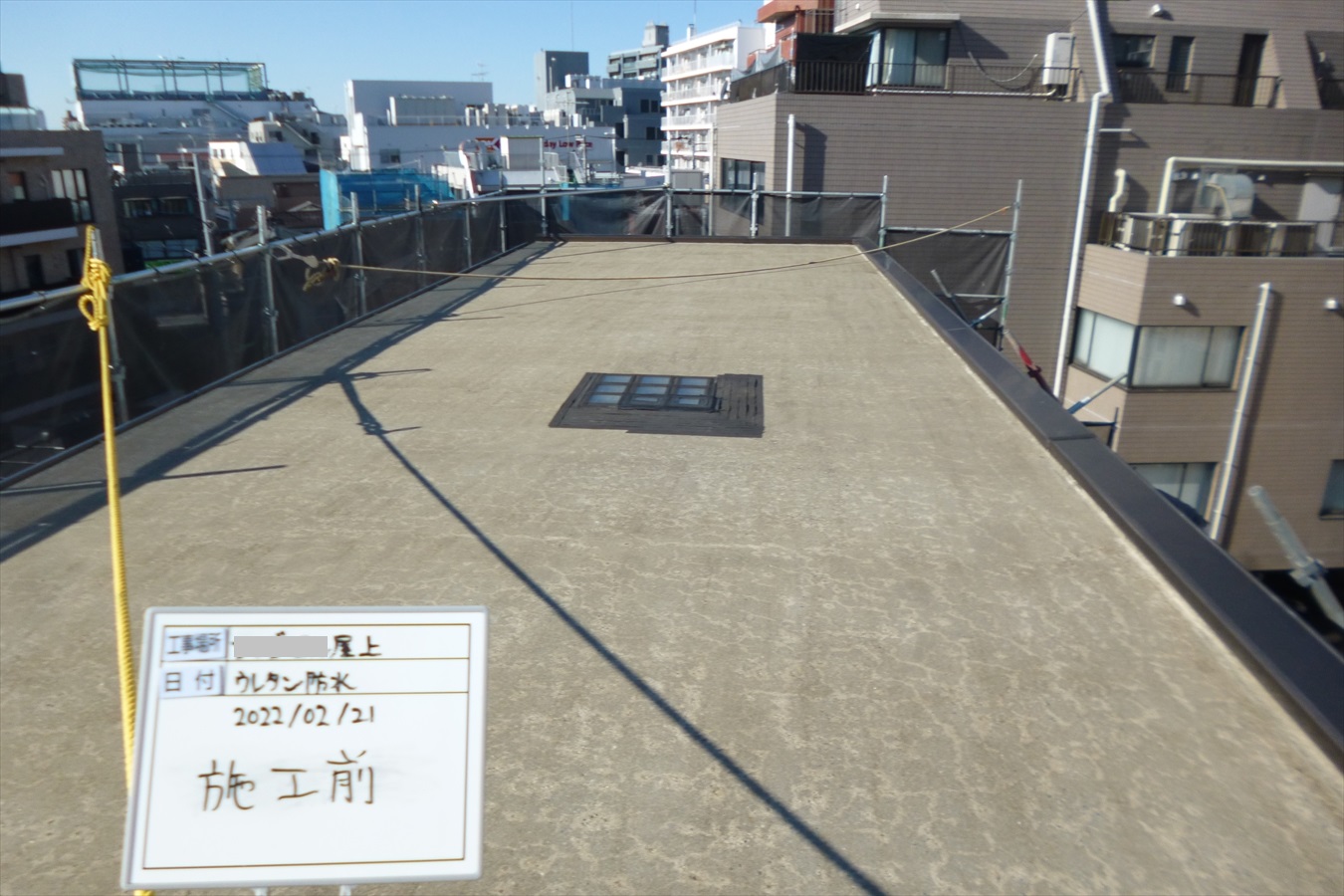
屋上中央にトップライト(天窓)が設置されているのが見えます。そのトップライトの周りに大量のブチルテープが貼り付けられていました。この建物は過去、雨漏りをしたようでその対応として貼られたもののようです。今回新しくウレタン防水を施工するため、このテープは不用となるので撤去する必要があります。
また、一般的な屋上と違いドレンが設置されていません。一般的な屋上であれば、四方に立ち上がりと呼ばれる壁、もしくはフェンスなどが設置されていることが殆どですが、この建物は立ち上がりが三方にしかありません。
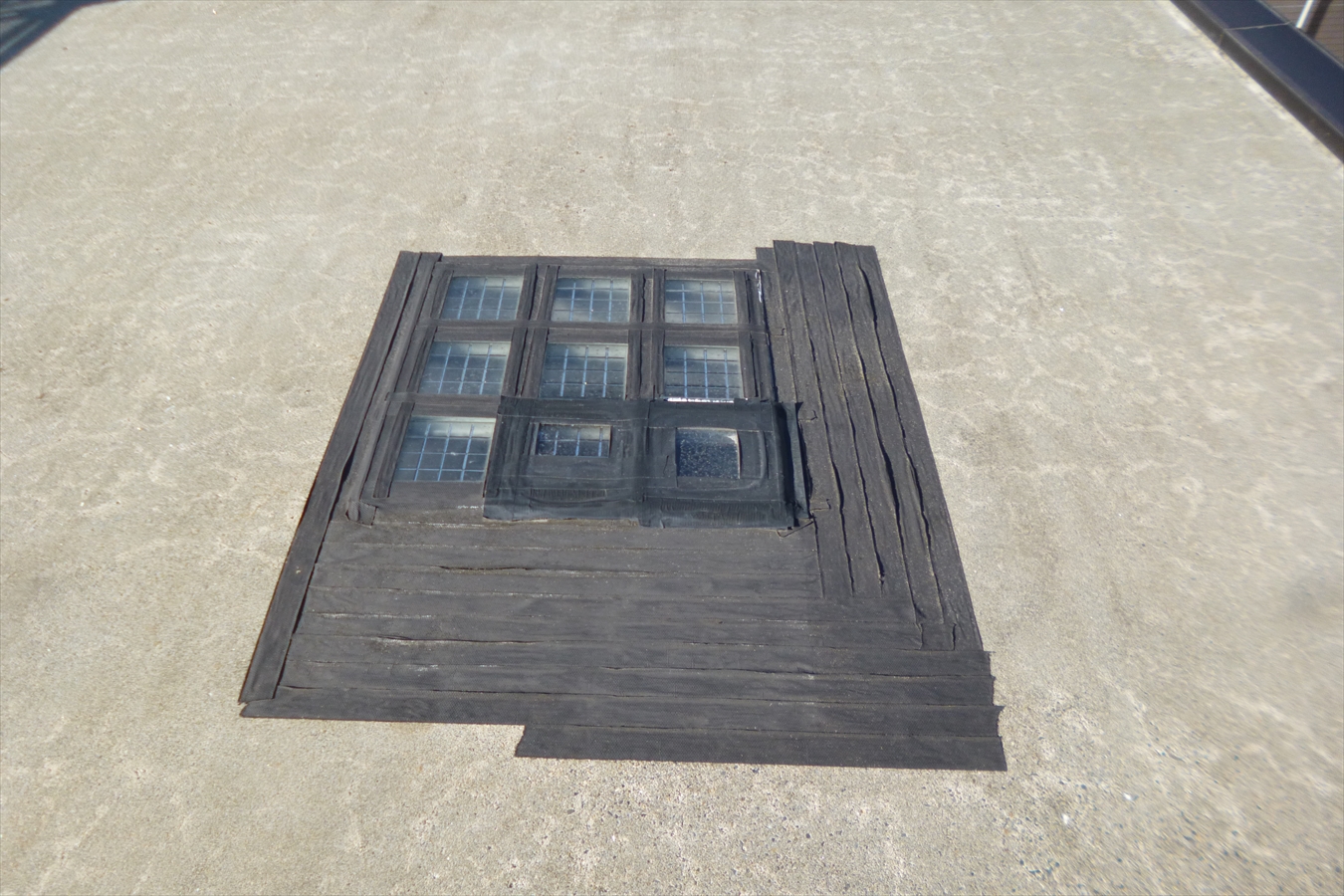
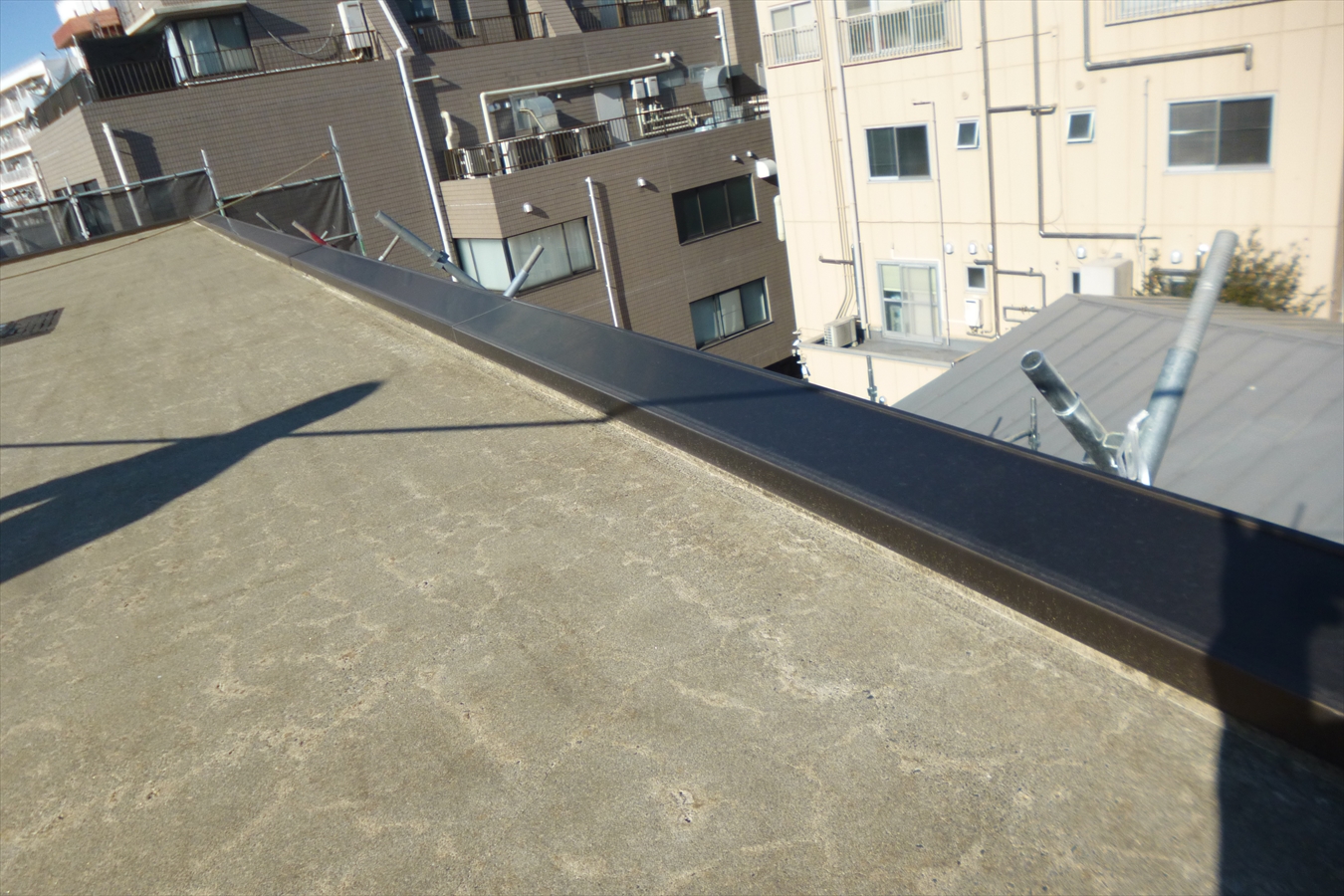
これは立ち上がりの無い箇所が勾配の下と設計されているためで、雨水がこの箇所に流れるようにしているから。そのため雨どいがこの箇所のみの設置となっています。このような設計のため、屋上の土間から雨どいの間もモルタルとなっており、ここにもウレタンを巻いておく必要があります。
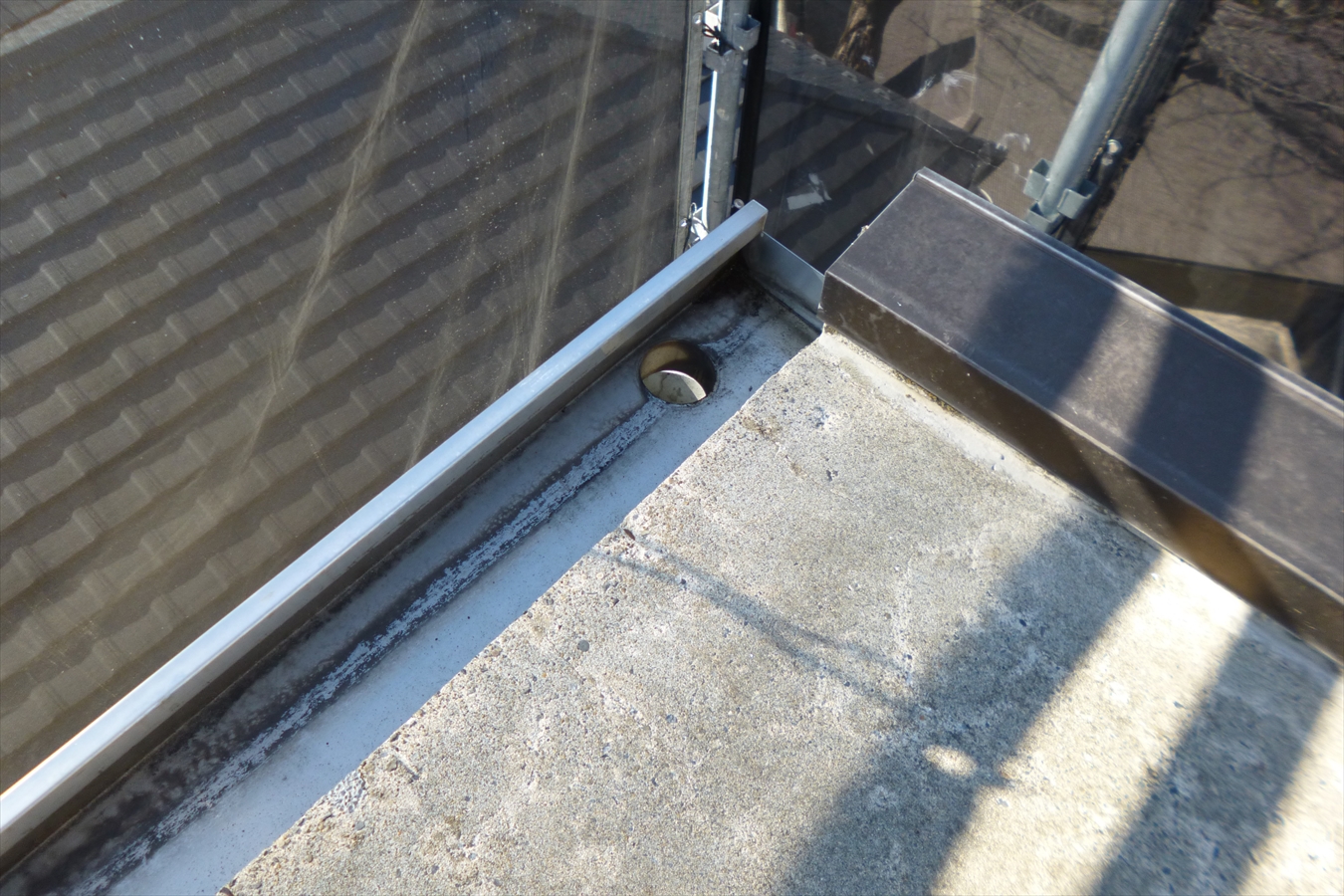
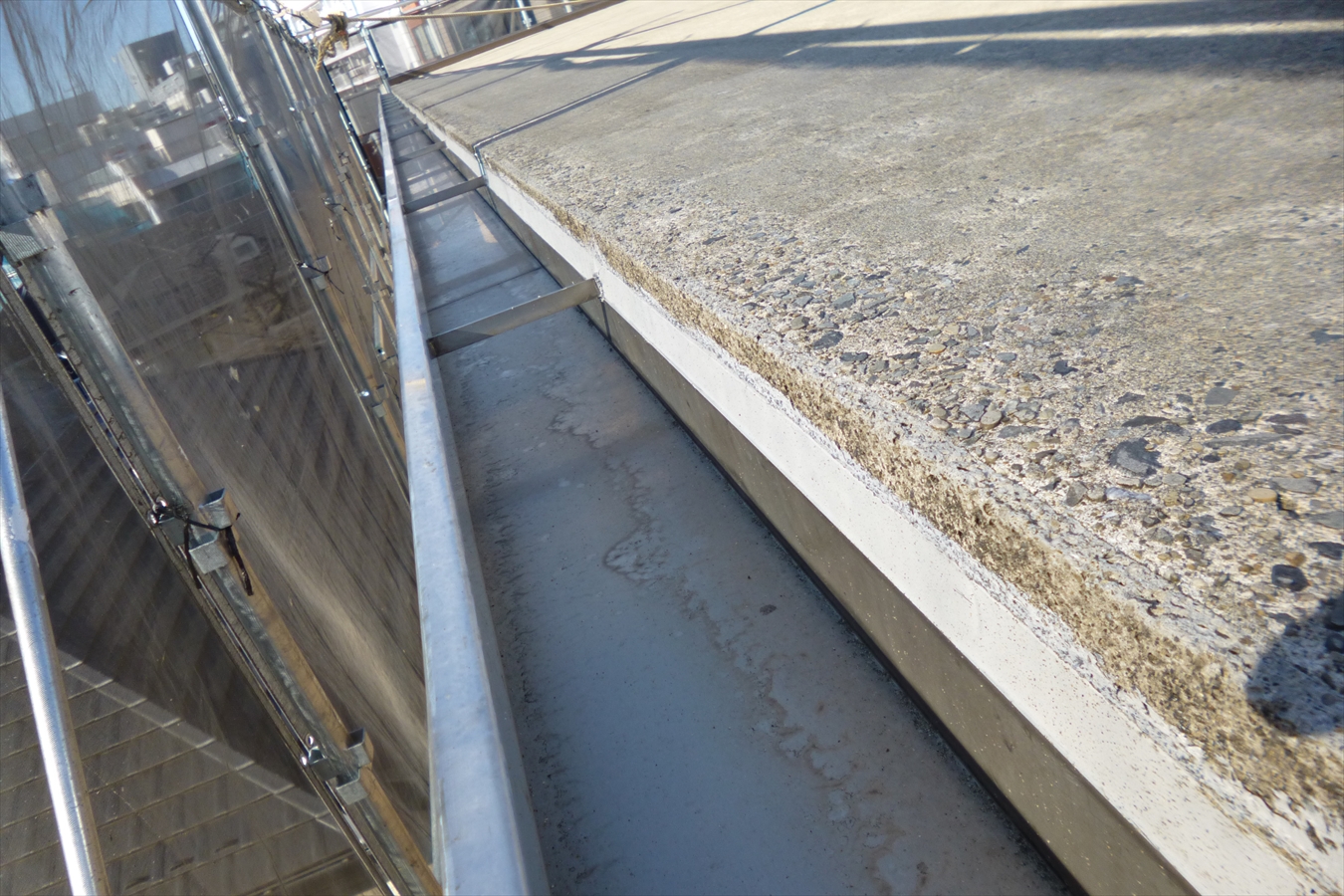
実測
ウレタン防水工事は、1平米辺りにどれくらいウレタンを流すのかと規定量が定められています。最低でも1平米に1kgで、それを2回に分けて流すので2kg必要になります。実際にどれくらいのウレタンが必要になるのか、を事前に把握する必要があるため、作業に入る前にスケールなどを使い実測して実際の平米数を把握しておきます。
事前の実測をせず、適当に作業へ取り掛かってしまうとウレタンを流した時に、材料が足りない、または余計に材料を発注してしまった、ということが起こり得るため、この実測はとても大切です。
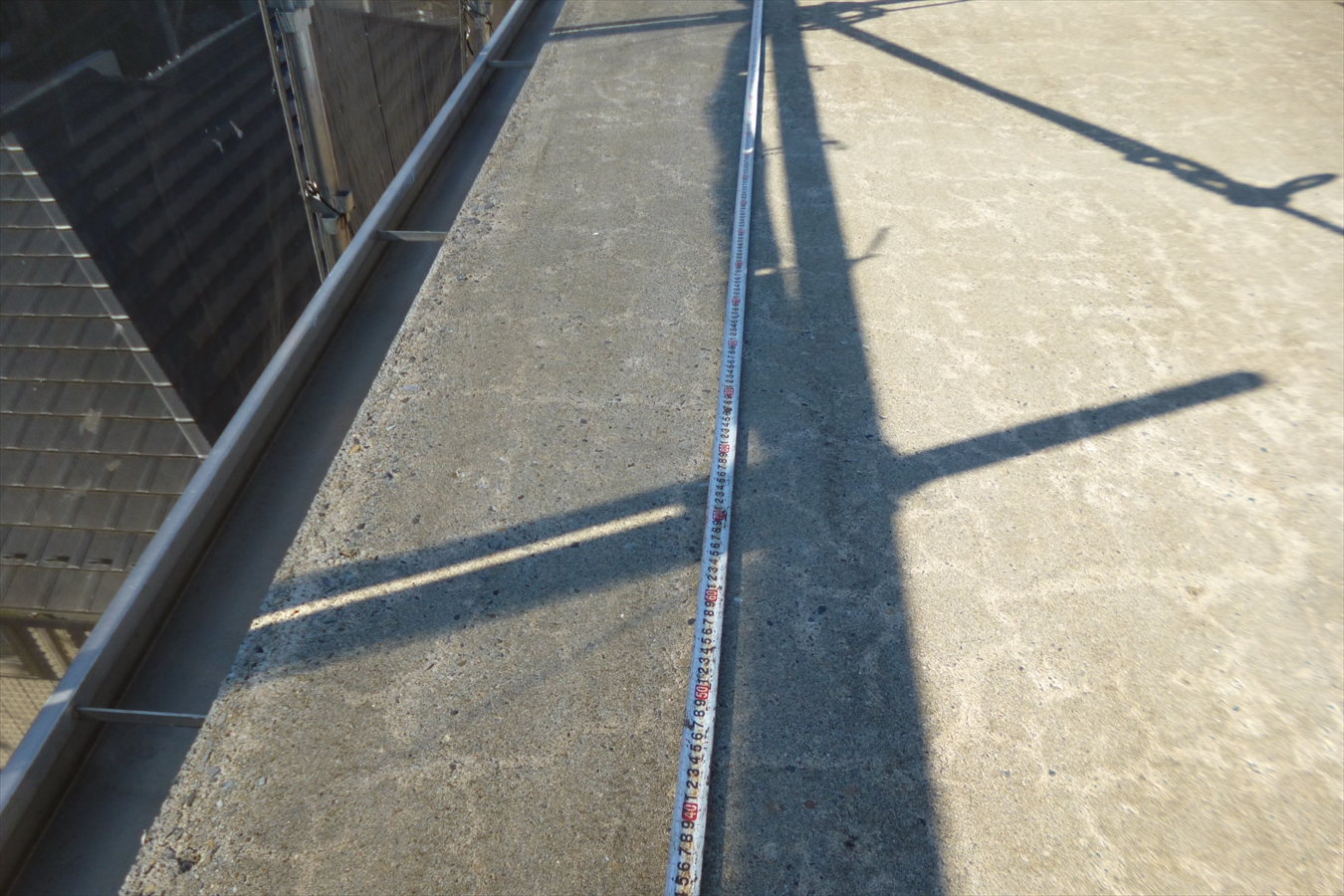
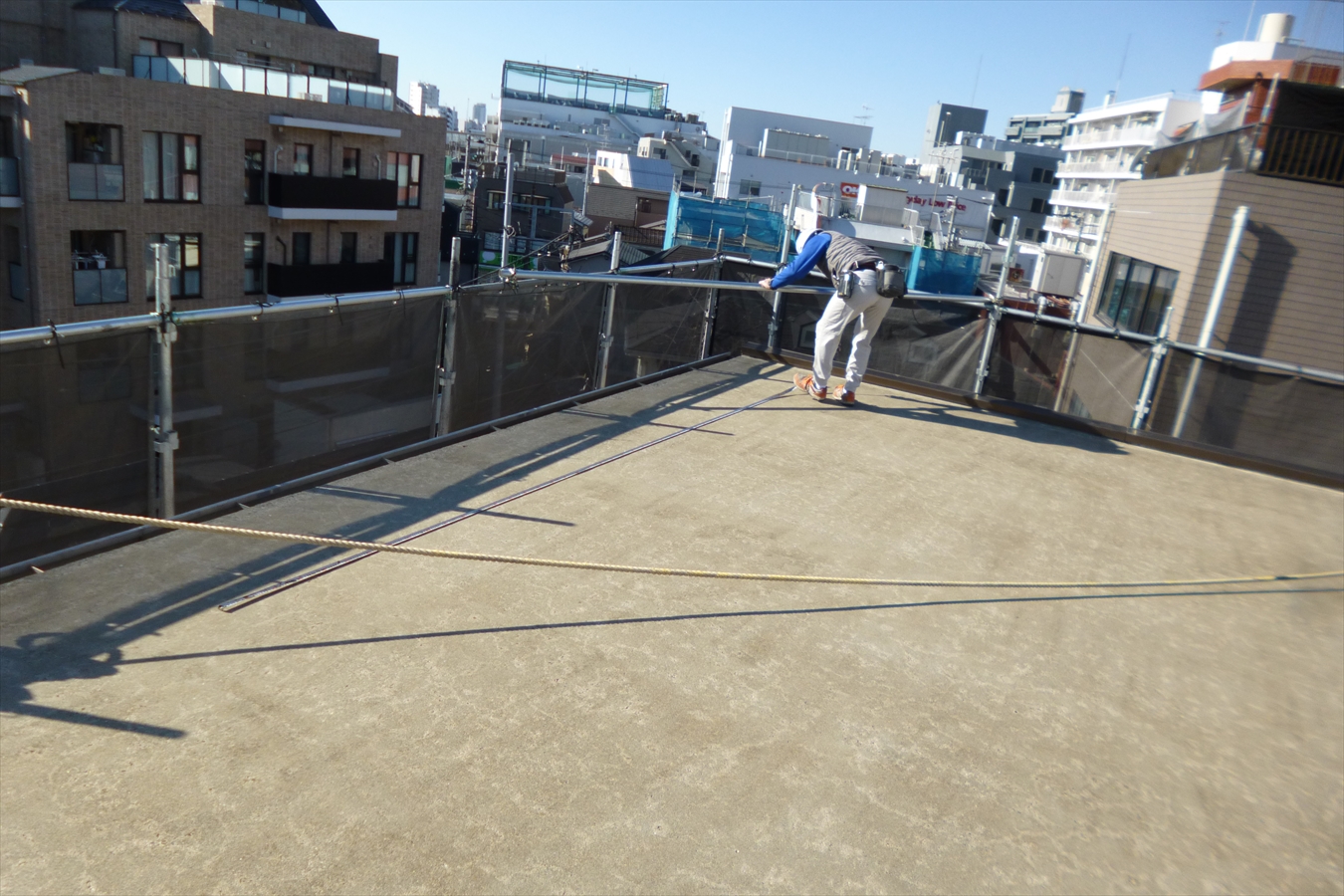
ケレン
実測し実際にどれくらいの量のウレタンが必要なのかを把握できたら、早速作業へ取りかかっていきます。最初に行うのは「ケレン」と呼ばれる作業です。これは英語の「クリーン」が訛ったものだとされており、塗装など何かを塗る箇所をキレイにする、という作業です。
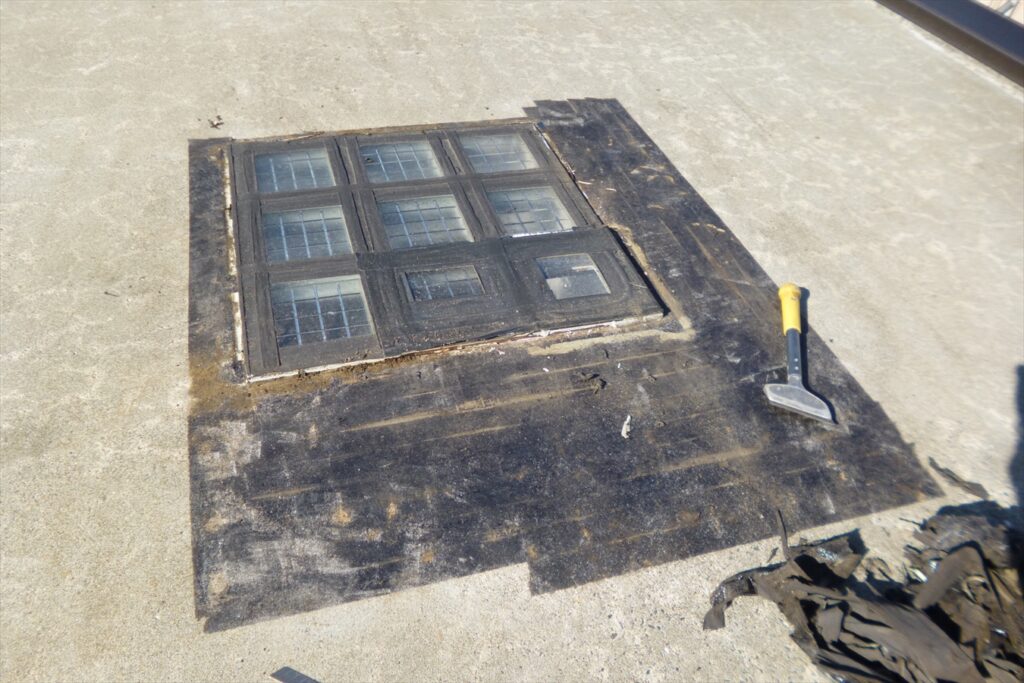
防水工事における「ケレン」は、モルタル面の突起物、ザラつきを取りキレイにするものが殆どですが、今回はトップライト周りのブチルテープの撤去作業そのものがケレン作業となります。
ブチルテープとはタールで作られたテープのこと。ノリの代わりにタールを使用しているものですが、タールは冷えて固まるとかなり硬くなるため手で剥がして撤去することはできません。なのでここではスクレーパーを使いブチルテープを剥がしていきます。
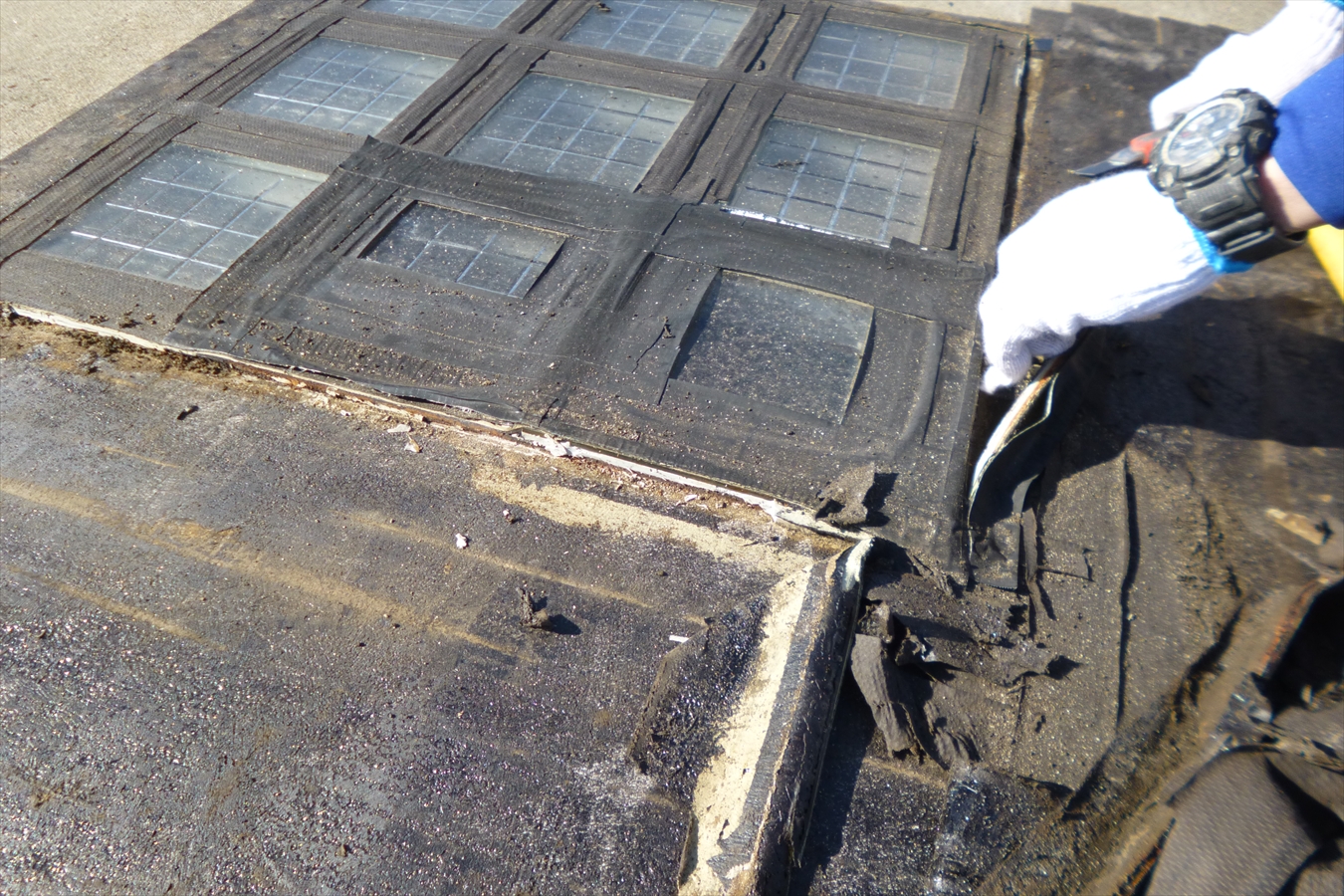
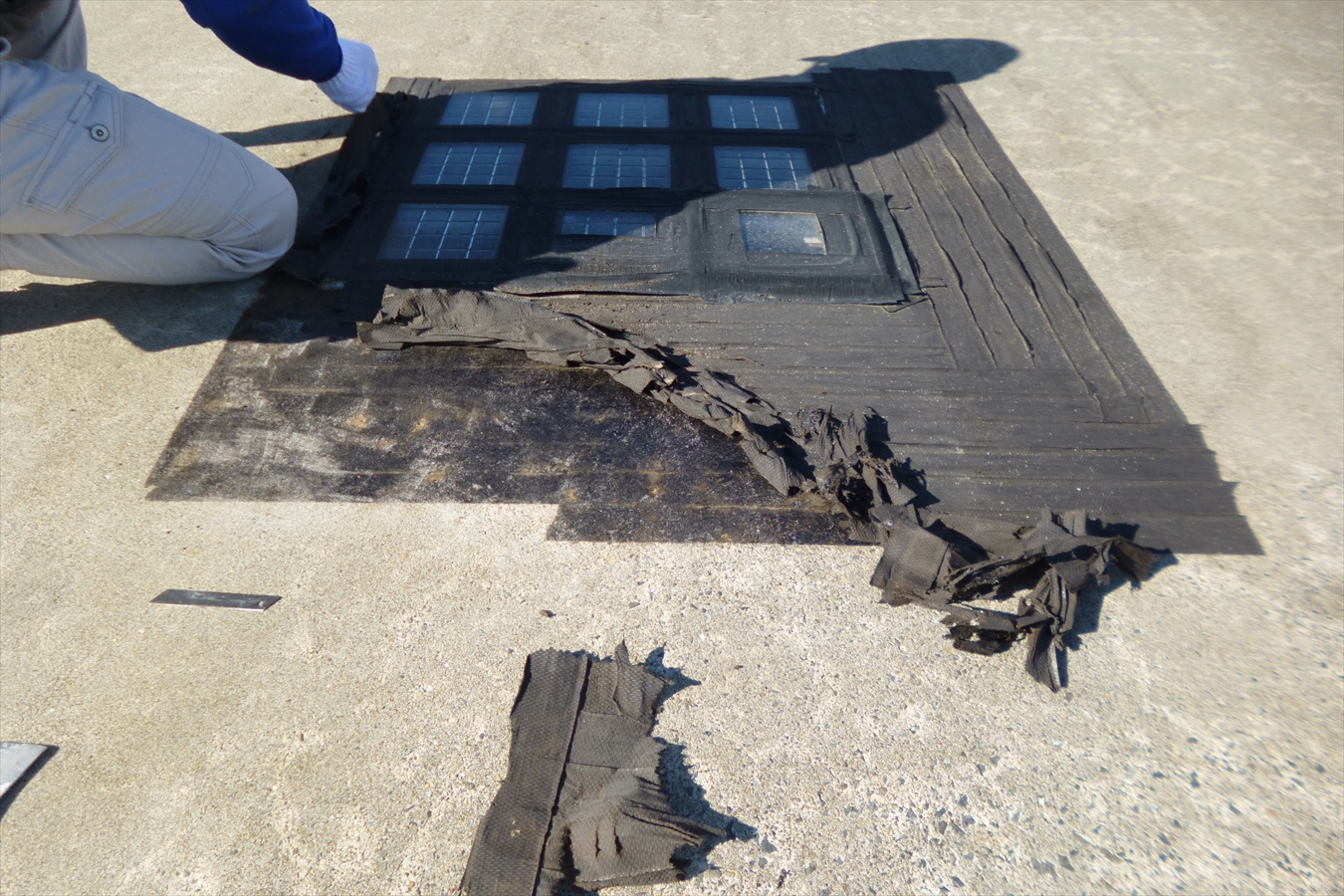
清掃
ブチルテープの撤去が終わったら掃除をしてキレイにしておきます。一般的な、ただの掃除…防水工事で行う掃除でも、チリ取りで拾いきれないような多少の埃が残ってもあまり問題はありませんが、今回のようにタールの撤去の場合は念入りに行う必要があります。
タールはウレタンと非常に相性が悪く、ウレタンに混ざるとウレタン自体が硬化しない、硬化したとしても指で触る程度でもボロボロと崩れるような状態で硬化する、など様々な不具合を引き起こしてしまうものです。そのため、僅かでもタールが残っていて、ウレタンを流した時に混ざってしまわないようするためにもタールを撤去した後の掃除に関しては、通常の掃除より気を使わなければいけません。
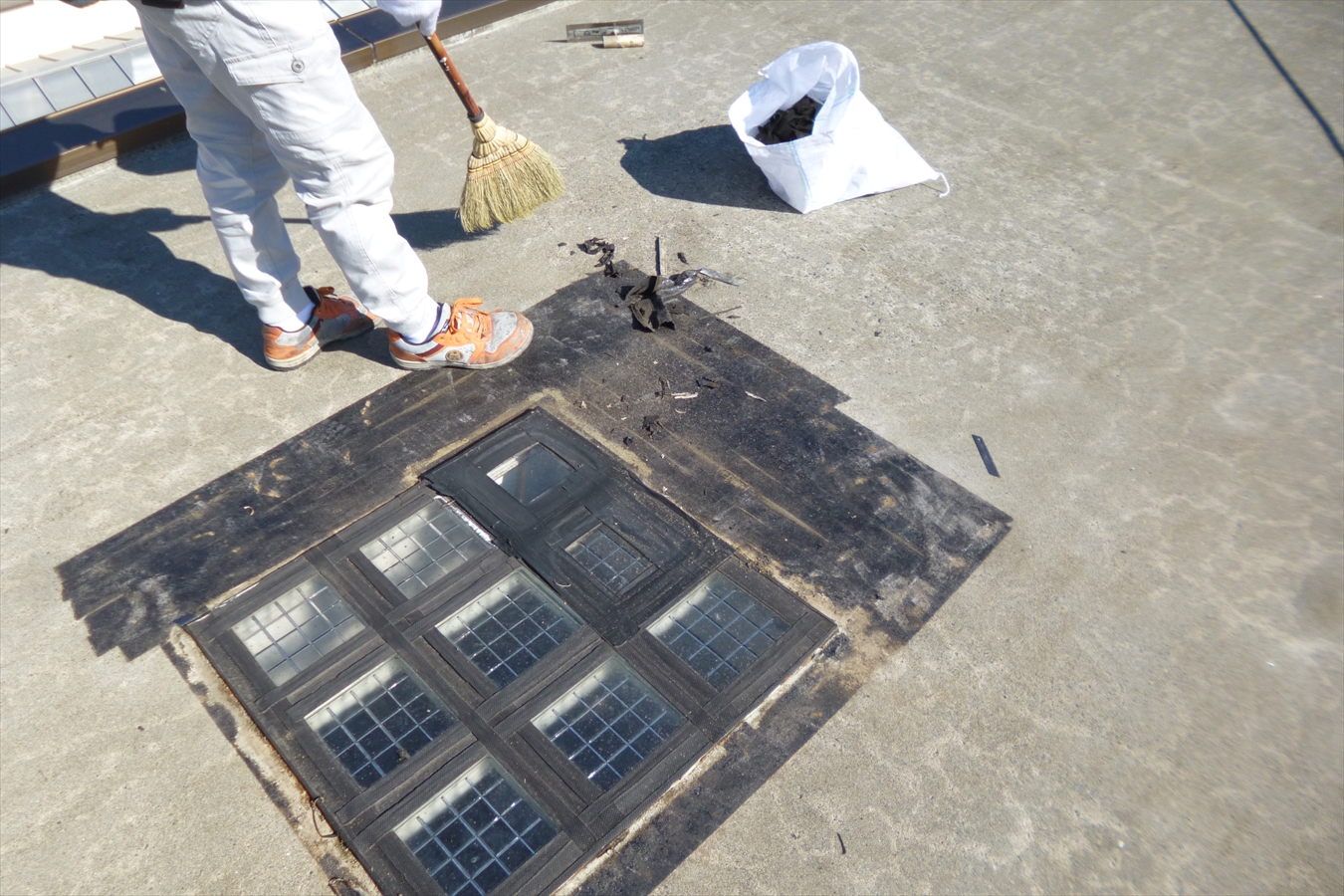
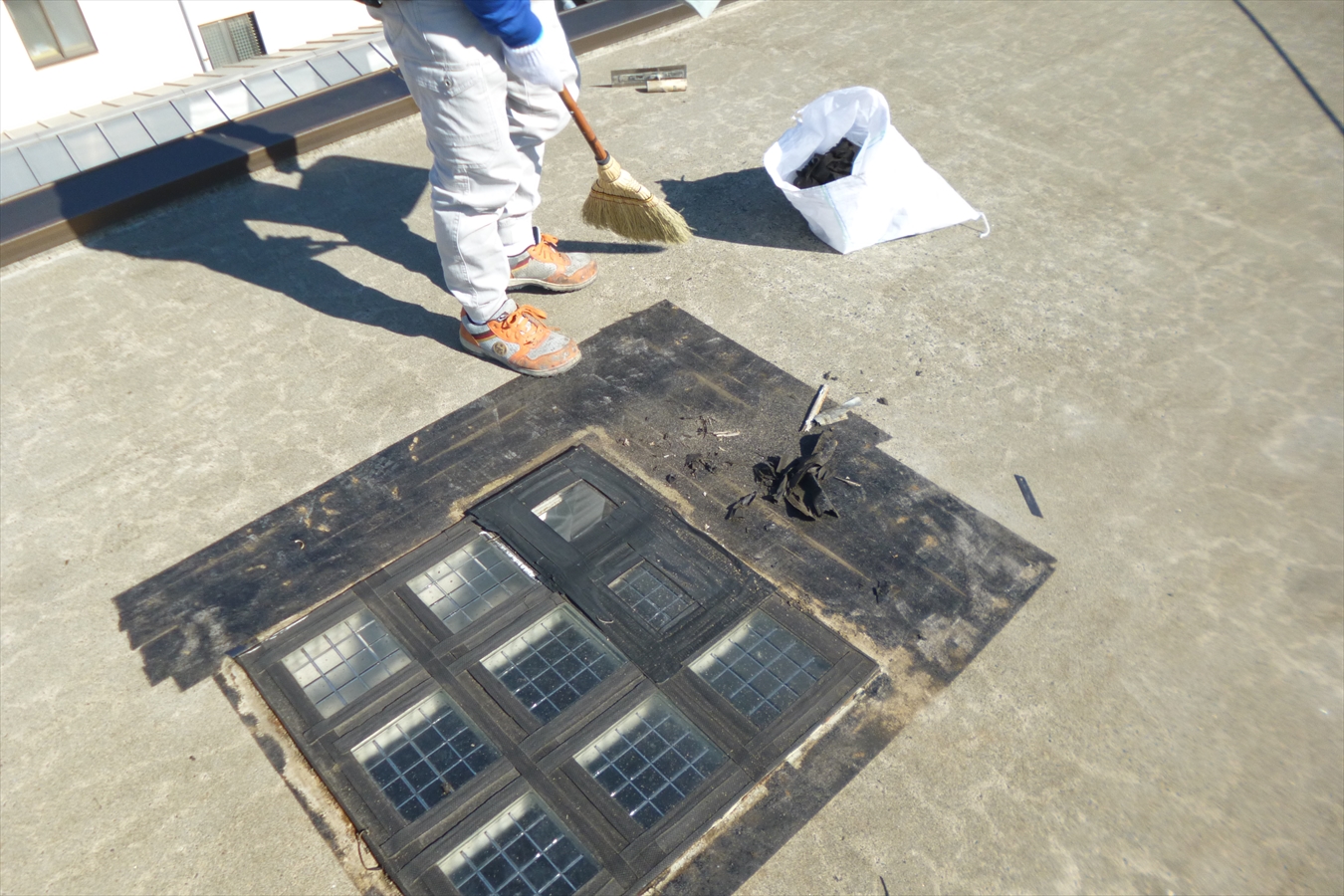
下地処理
施工前
ブチルテープで使われているタールの掃除が済んだら次は保護モルタルの補修作業です。この作業はウレタン防水工事の工程で、絶対にやらなければならない工程という訳ではありません。この建物の屋上の保護モルタルはというと、正直、この工程をやる、やらないは人によって変わるといったところでしょうか。しかし前の工程で、ブチルテープの撤去を行っています。
テープそのものは無くなっていますが保護モルタルの隙間に入り込んだタールは残ったままです。このままウレタンを流してしまえば確実にウレタンを劣化させてしまうことになるでしょう。なので下地調整は必須ですね。今回は下地調整というより、取り切れないタールとウレタンを絶縁するための作業と言った方が正確かもしれません。
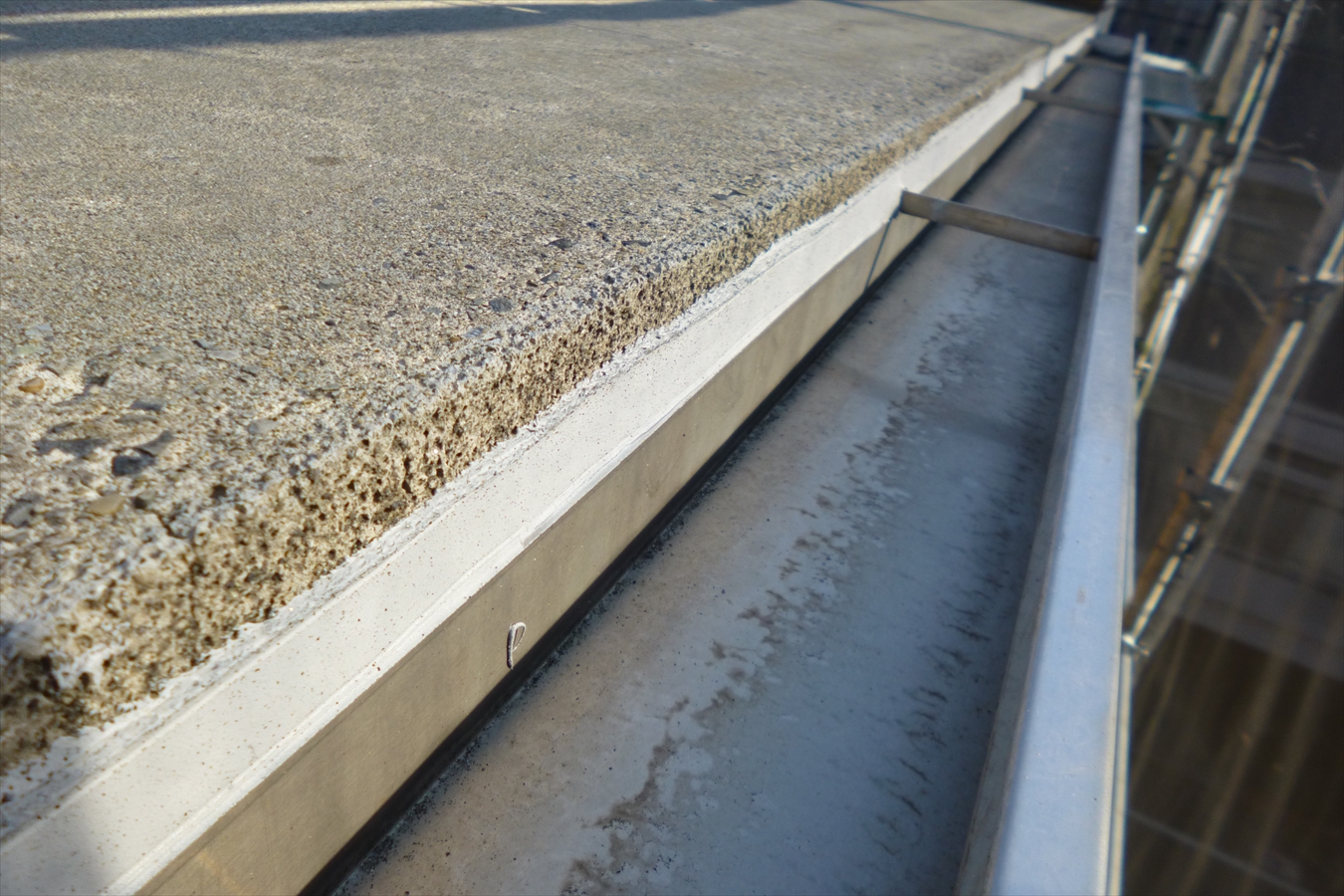
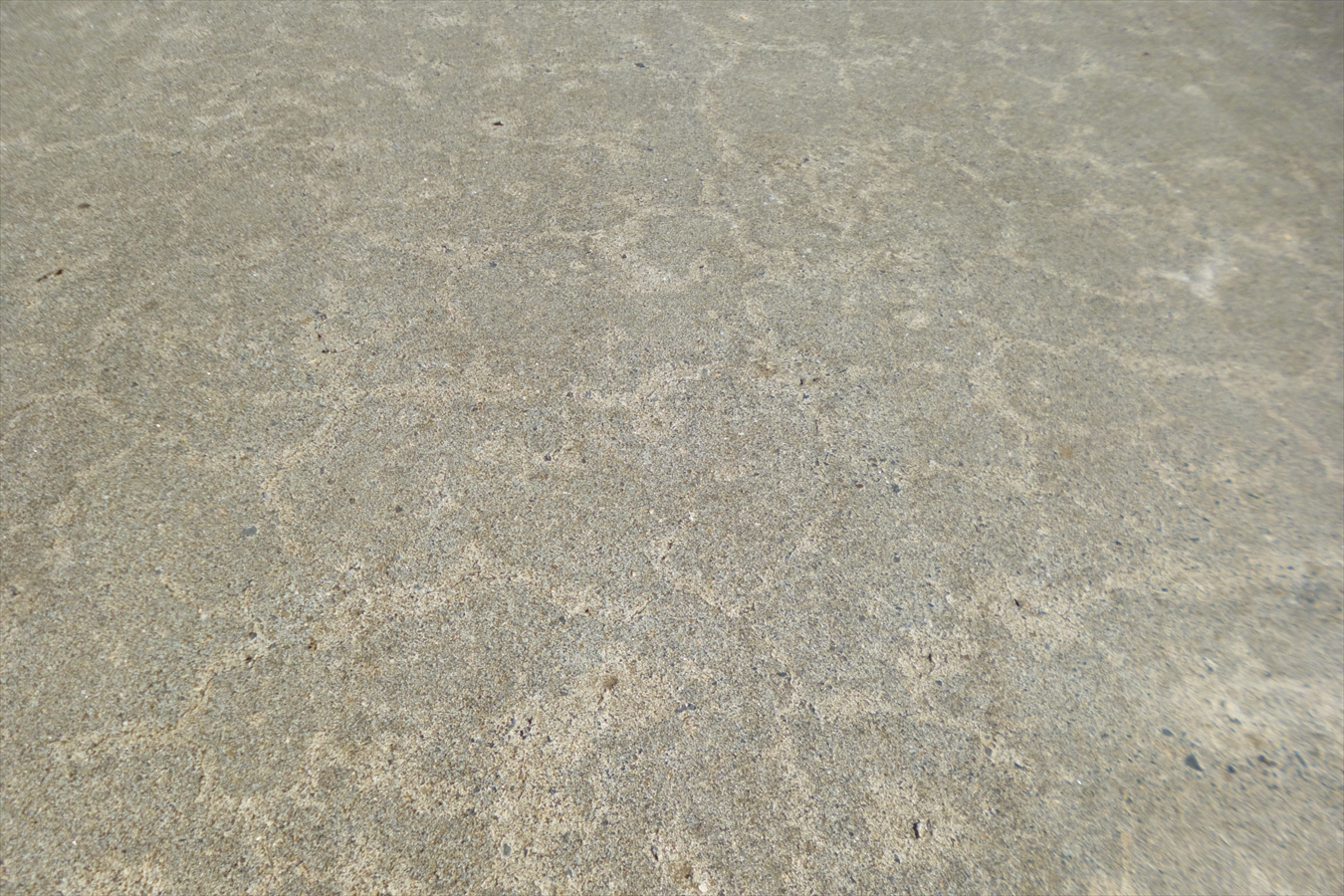
下地補修・絶縁の材料
ここでは実際に下地補修と絶縁で使われる材料を説明していきます。保護モルタルの補修や、タールとの絶縁で使われるのは一般的にモルタルを主剤とした、「下地補修材」と呼ばれる材料となります。
このモルタルには数種類あり、セメントモルタル、樹脂モルタル、ポリマーセメントモルタルがこの代表とされています。いずれのものも、セメントに何かを混ぜた材料となっており、それぞれ混ぜられているものに違いがあるものの、セメントが主剤であるということに間違いはありません。
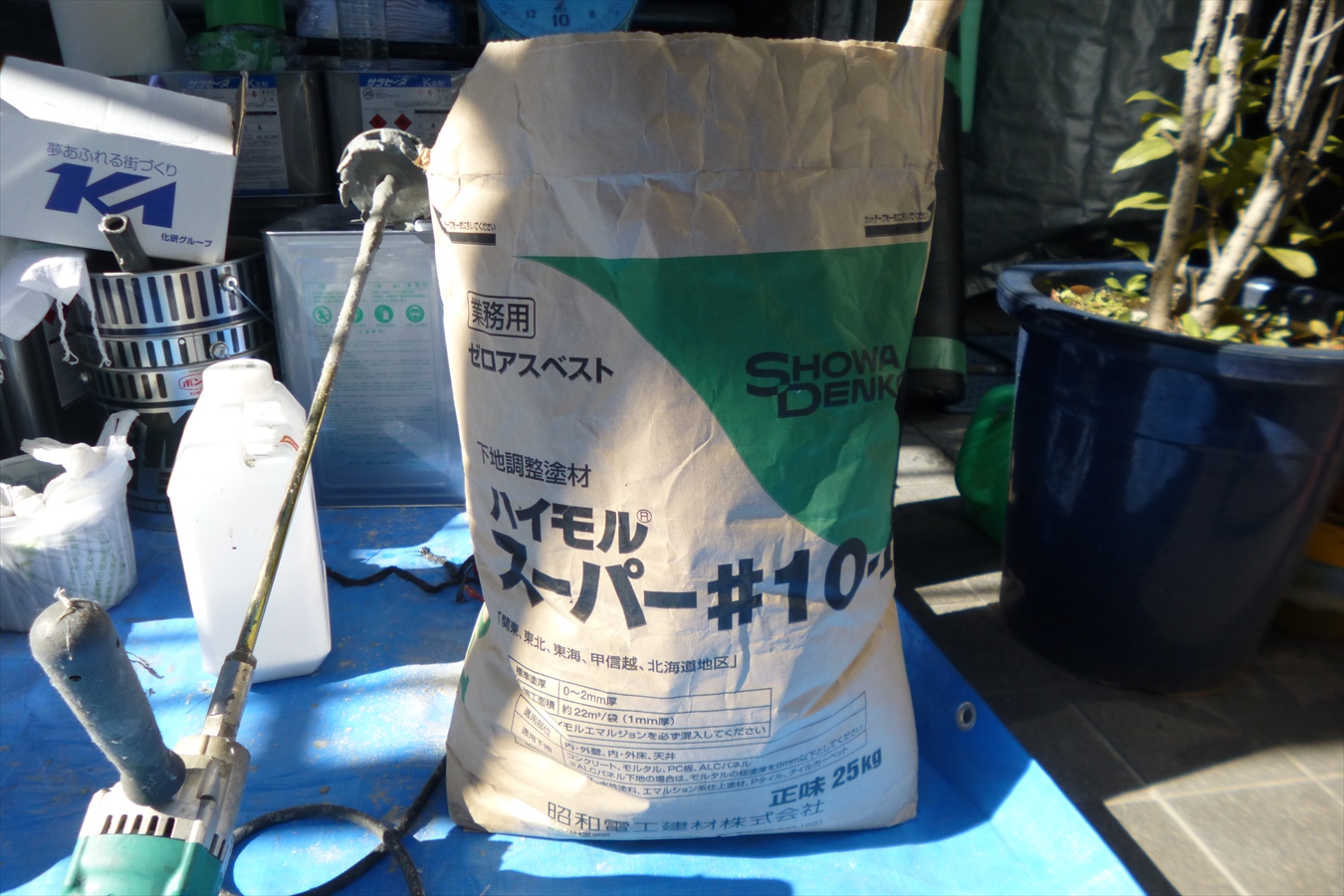
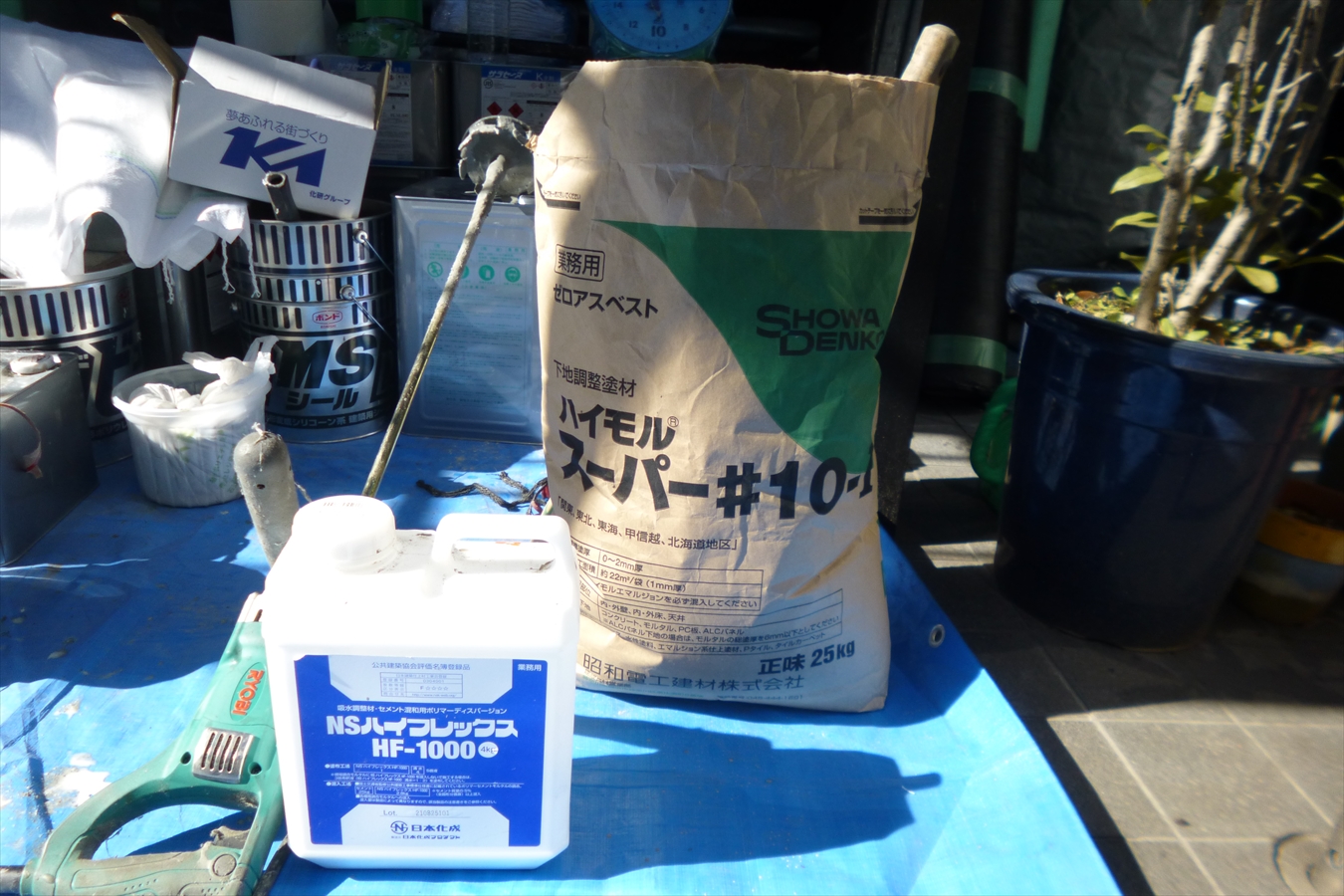
今回使用した材料は、ポリマーセメントモルタルの「ハイモルスーパー#10」という材料です。これは「乳液」と言われる接着剤と、水、そして材料のハイモルスーパー#10を攪拌して使う仕様となっています。NSハイフレックスHF-1000というのが乳液です。
実際に材料を攪拌したものがこちら。これを使い、保護モルタルの補修と、タール箇所の絶縁を行っていきます。
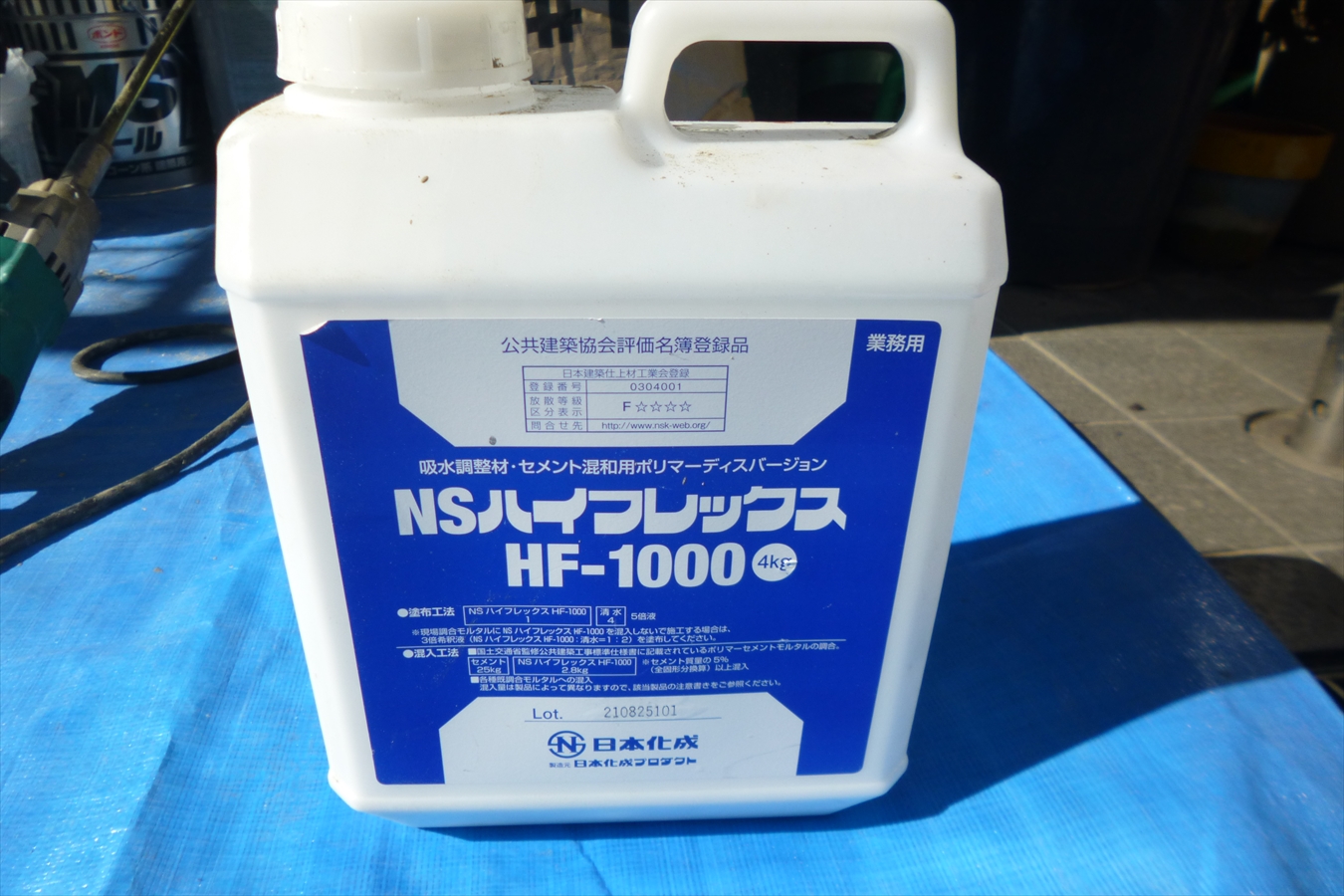
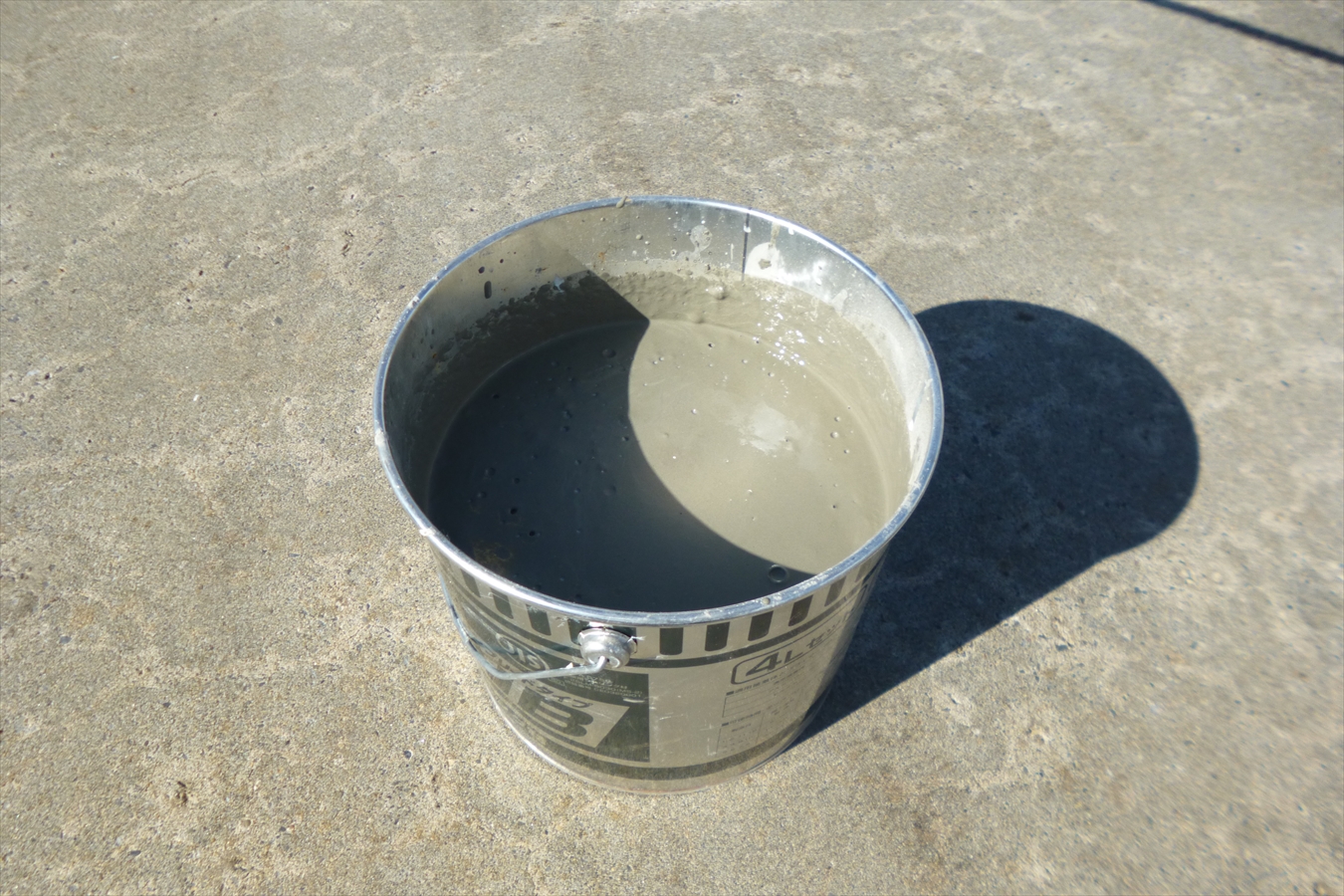
下地材塗布
攪拌したハイモルスーパー#10を使い、実際に下地補修、絶縁作業を行っていきます。規定で1mm以上の厚みを付ける、とありますが、このような雨に打たれ劣化した保護モルタルの補修作業では、厚みよりも雨に打たれてザラついた保護モルタルの表面を平らにするように作業する方が重要視されているかもしれません。
写真では小手を使い作業していますが、この作業はローラーでも全く問題ありません。両者共に、小手ムラ、ローラームラが付かないように作業することが大切です。また、一定量のハイモルスーパー#10を予め土間に撒いて、それを伸ばすように作業することで一定の厚みが出るように作業しています。
作業している手前側と、既に作業が終わった中央、奥側とで色が違うのが分かると思います。一番奥は白く乾燥している箇所が多く、中央は少ないです。塗布した箇所全体が白くなったら次の作業へ移ります。
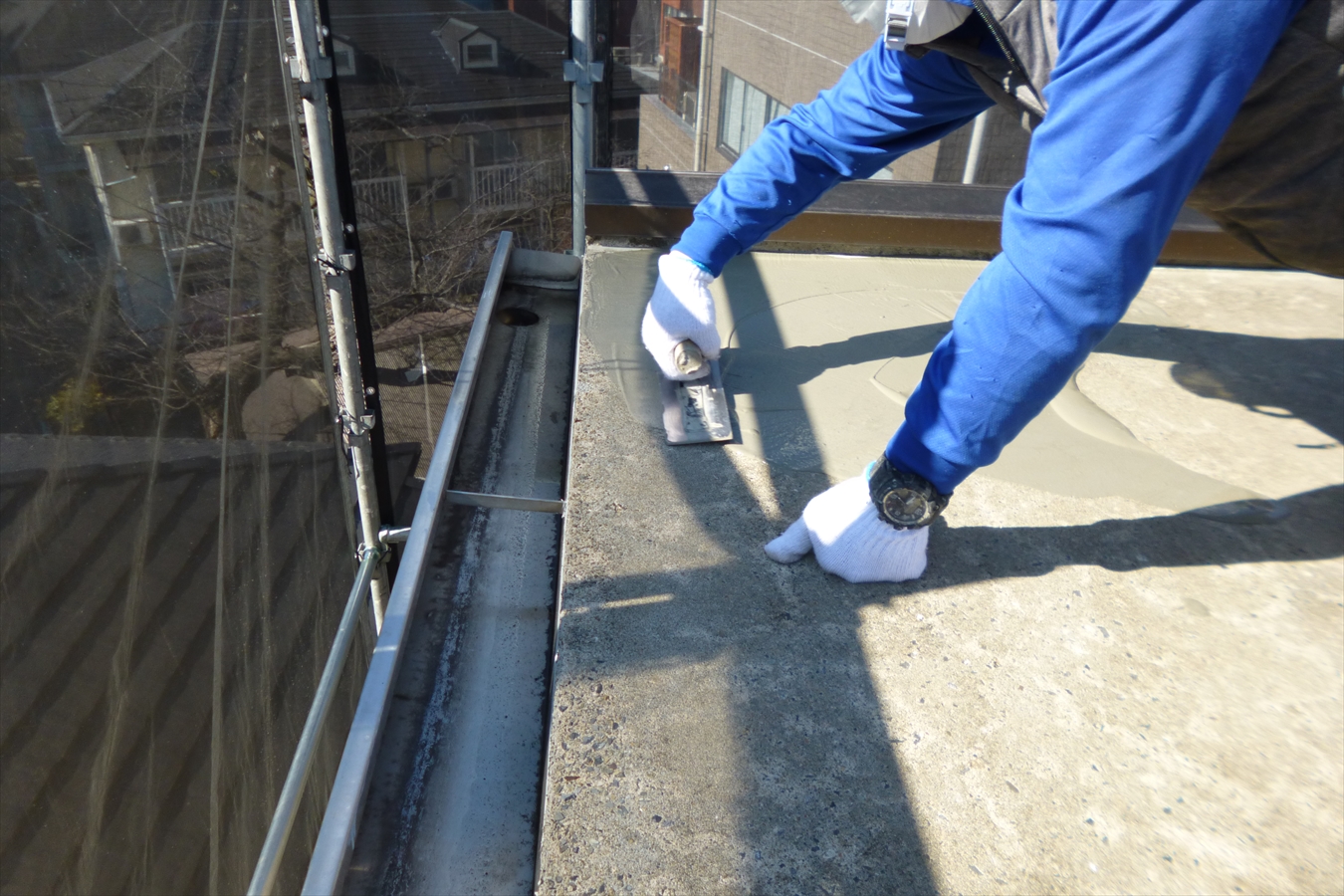
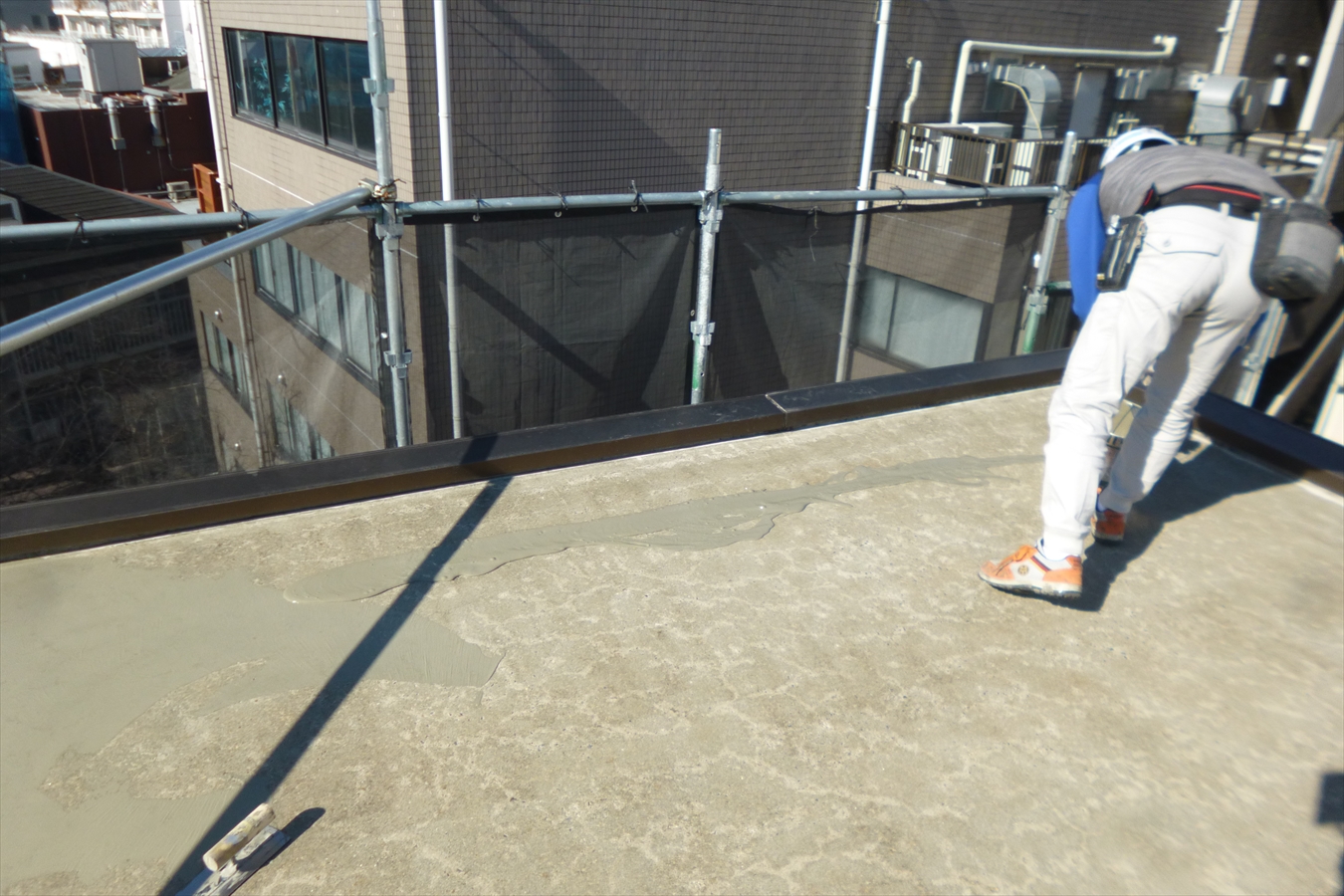
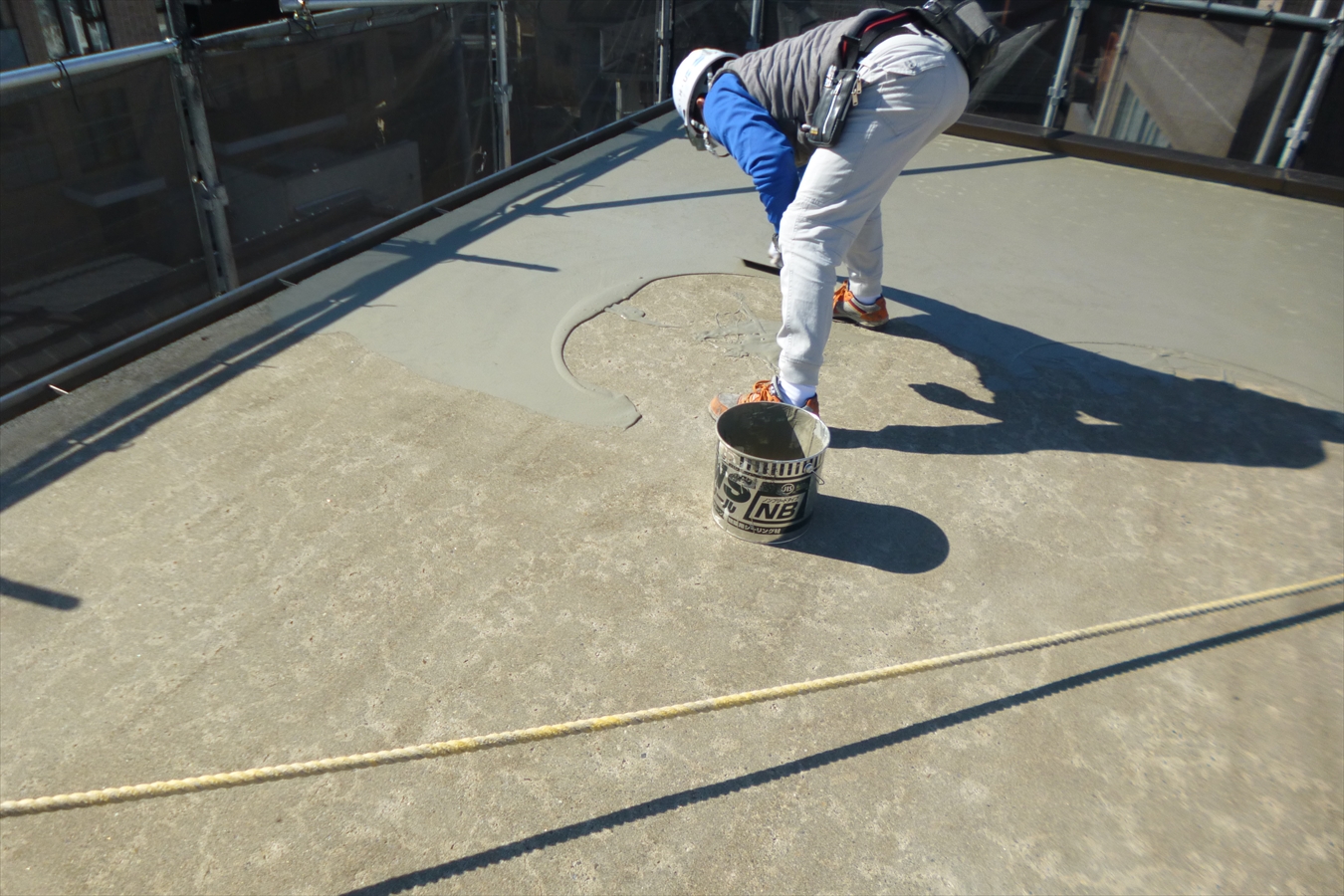
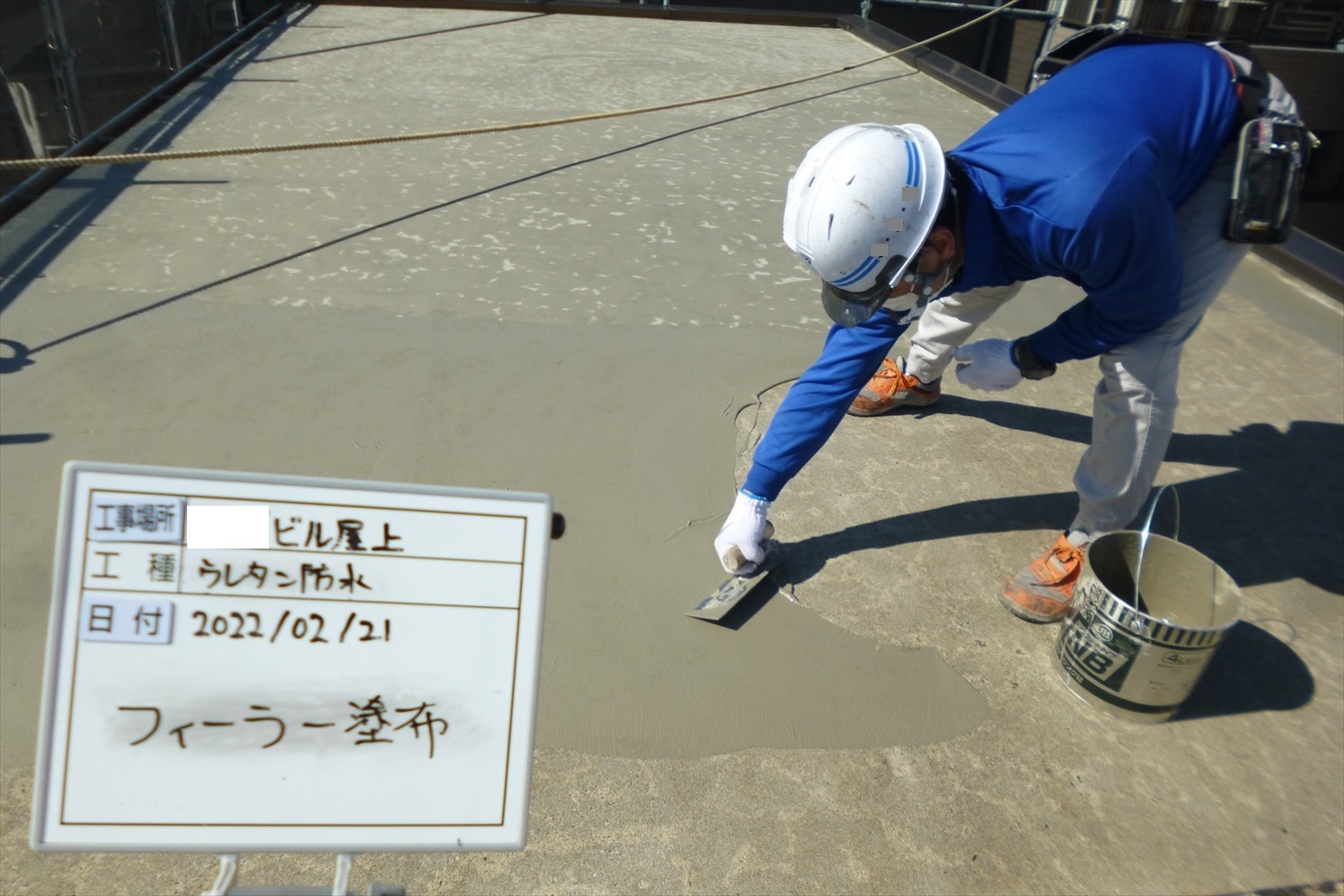
施工後
土間全体にハイモルスーパー#10の塗布が終わった後の写真です。写真で写っている、奥側から手前側へと作業を進めたため、先に作業をした奥側が乾燥が進み白く変色しているのに対し、手前側はまだ変色していないことが分かりますね。時間を置いて、全体が白くなるまで乾燥するのを待って次の作業へ移ります。
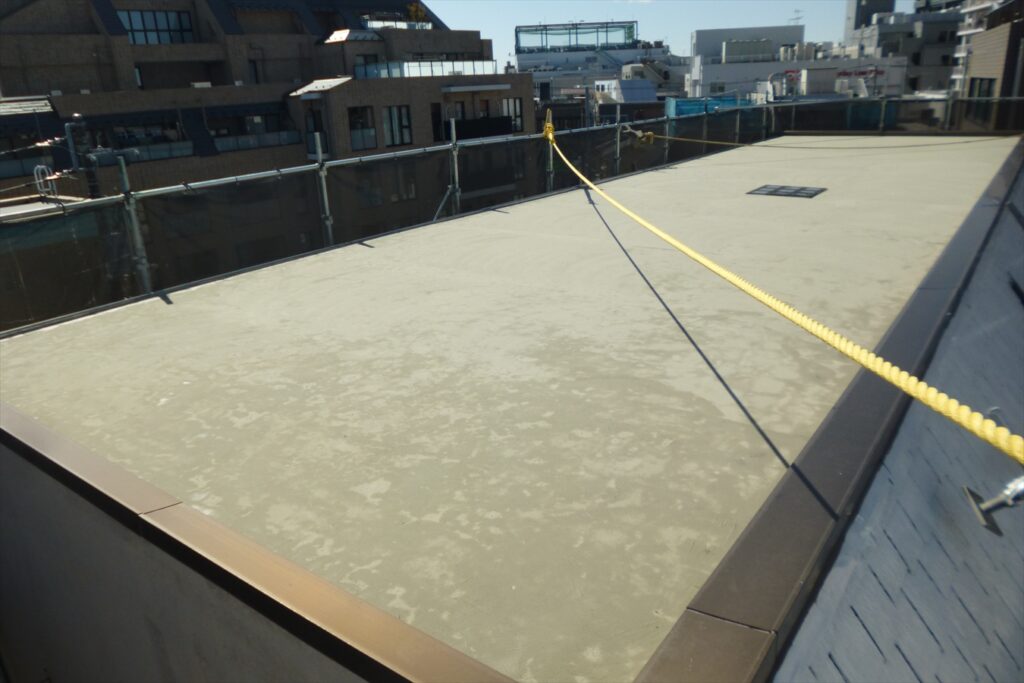
プライマー塗布
施工前
筆者の都合によりプライマーを塗る前の段階に居合わせることができなかったため、途中の写真からになってしまいますが、全面にプライマーを入れた訳ではなかったのでそこから説明していきます。尚、中途半端にプライマーが塗られているのは、中央にあるトップライトの枠を作る作業があり、枠を作る大工さんのために通り道と作業スペースの確保のためです。土間の色が黒く変色している箇所が既にプライマーを塗った箇所で、白いままになっているところがまだプライマーが入っていない箇所になります。
実際に使用した材料はサラセーヌPという材料です。これはAGCポリマー建材株式会社という会社が出しているウレタン材料の商品名で、サラセーヌという素材が存在している訳ではありません。別の会社が販売している材料を使用した時は、別の商品名のものとなりますが、同じウレタン材料となります。AGCポリマー建材株式会社が出しているウレタン防水に関連する材料の多くに、「サラセーヌ」という名前が付けられています。
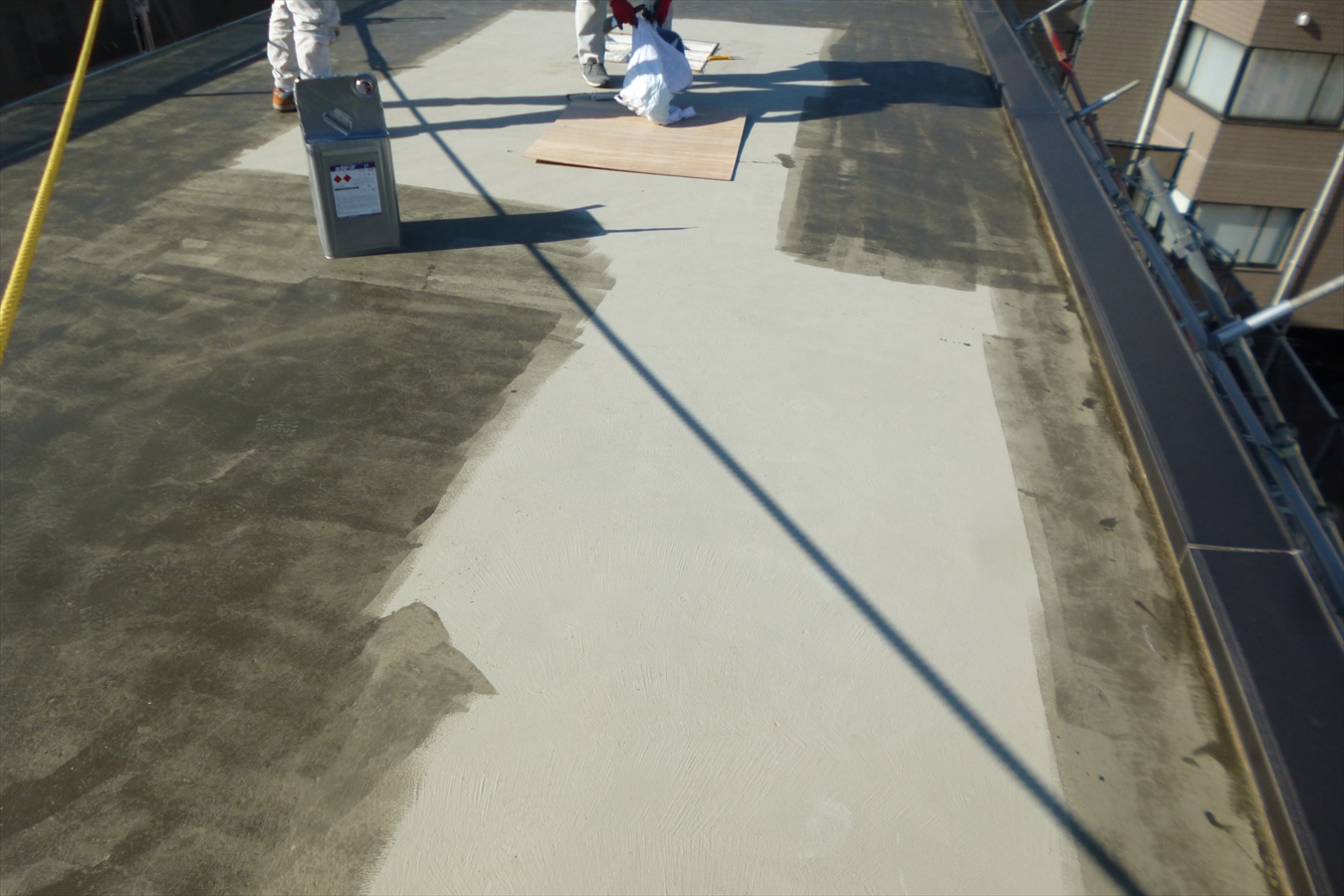
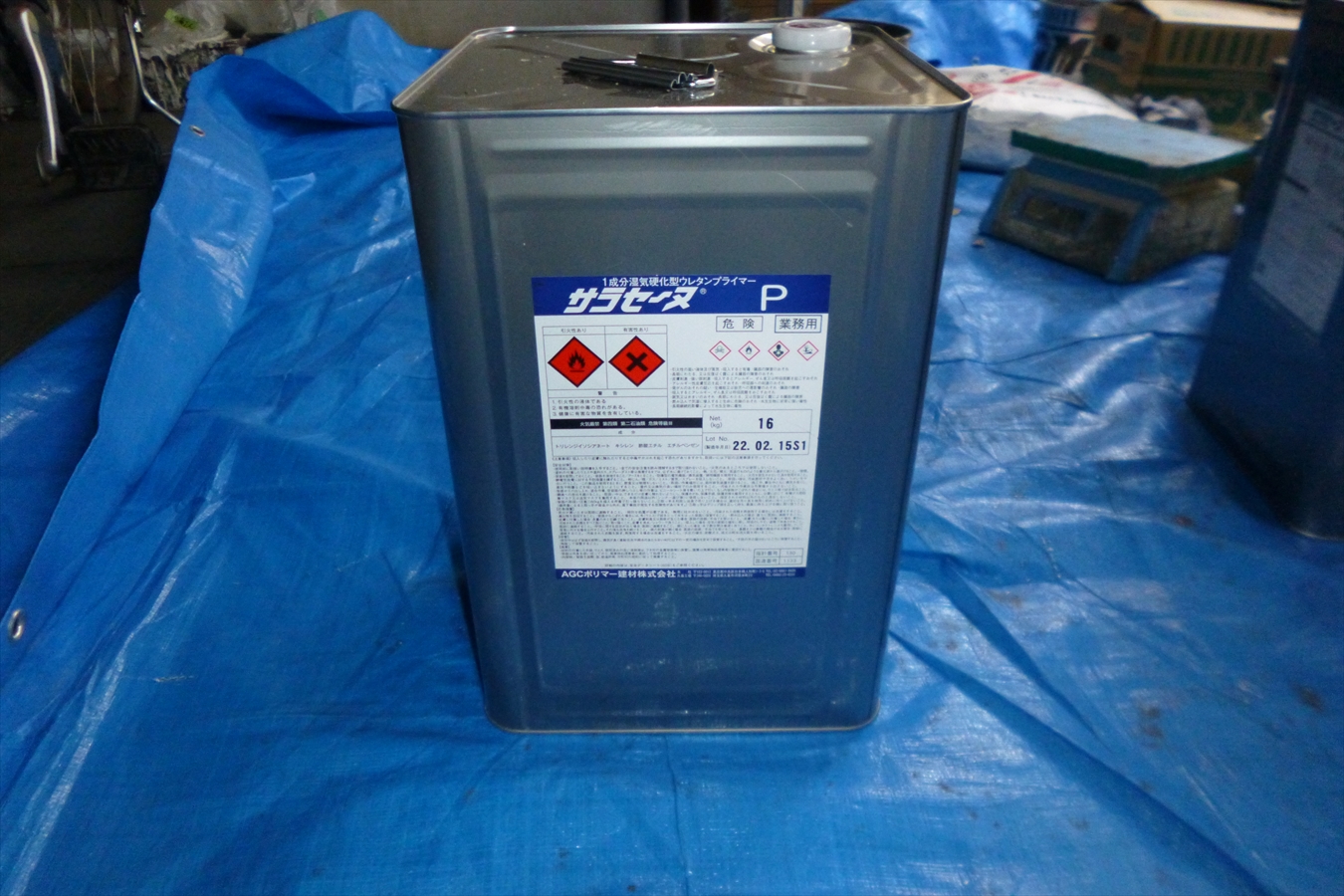
プライマー塗布
早速、まだ施工がされていない箇所にプライマーを塗布していきます。最初はトップライト周辺から塗り込んでいきます。何かを塗り込むような作業の場合、土間のように広い箇所からではなく、細かいところから塗り込んでいくのが一般的です。このような作業のことを「ダメ込み」と呼んでいます。
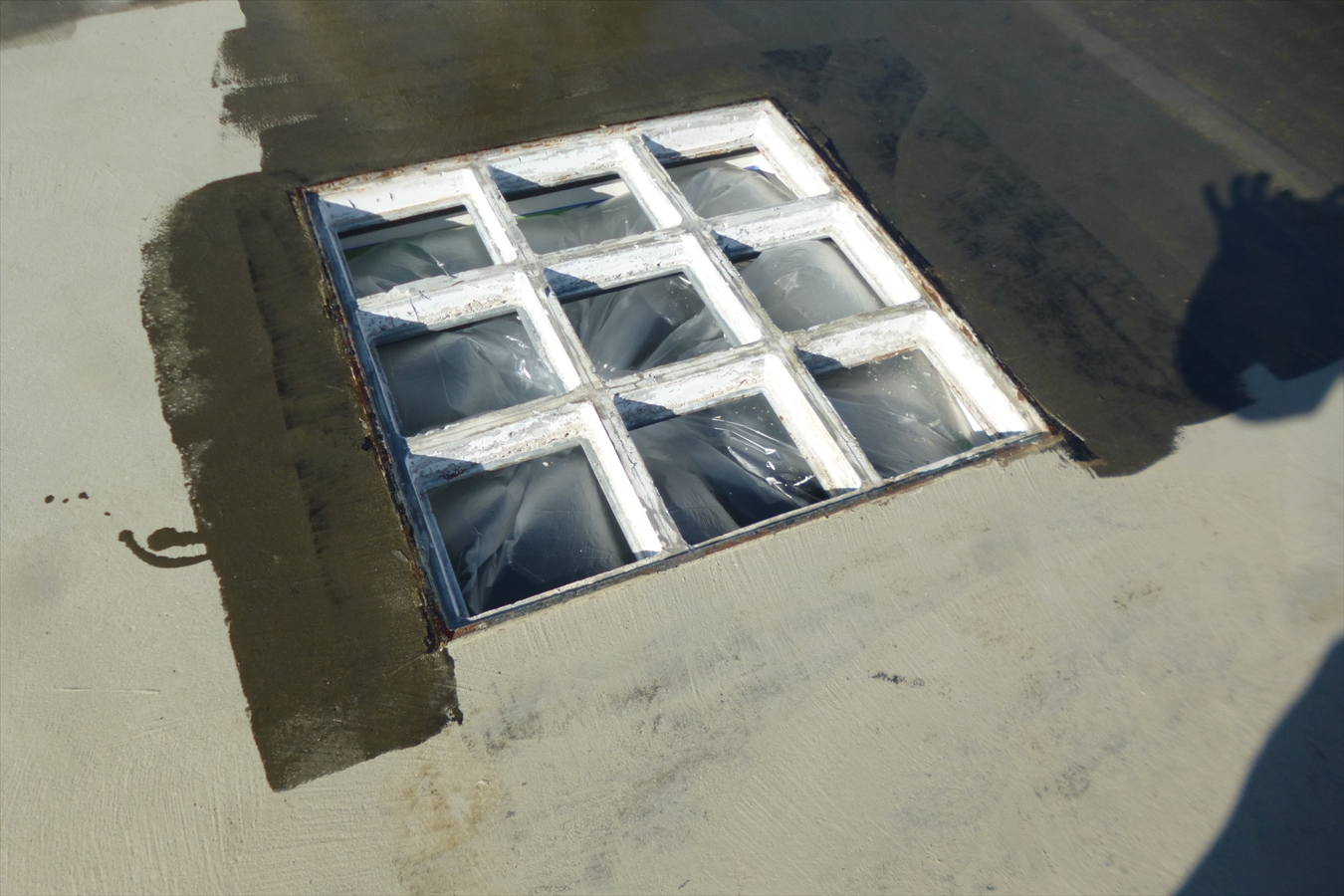
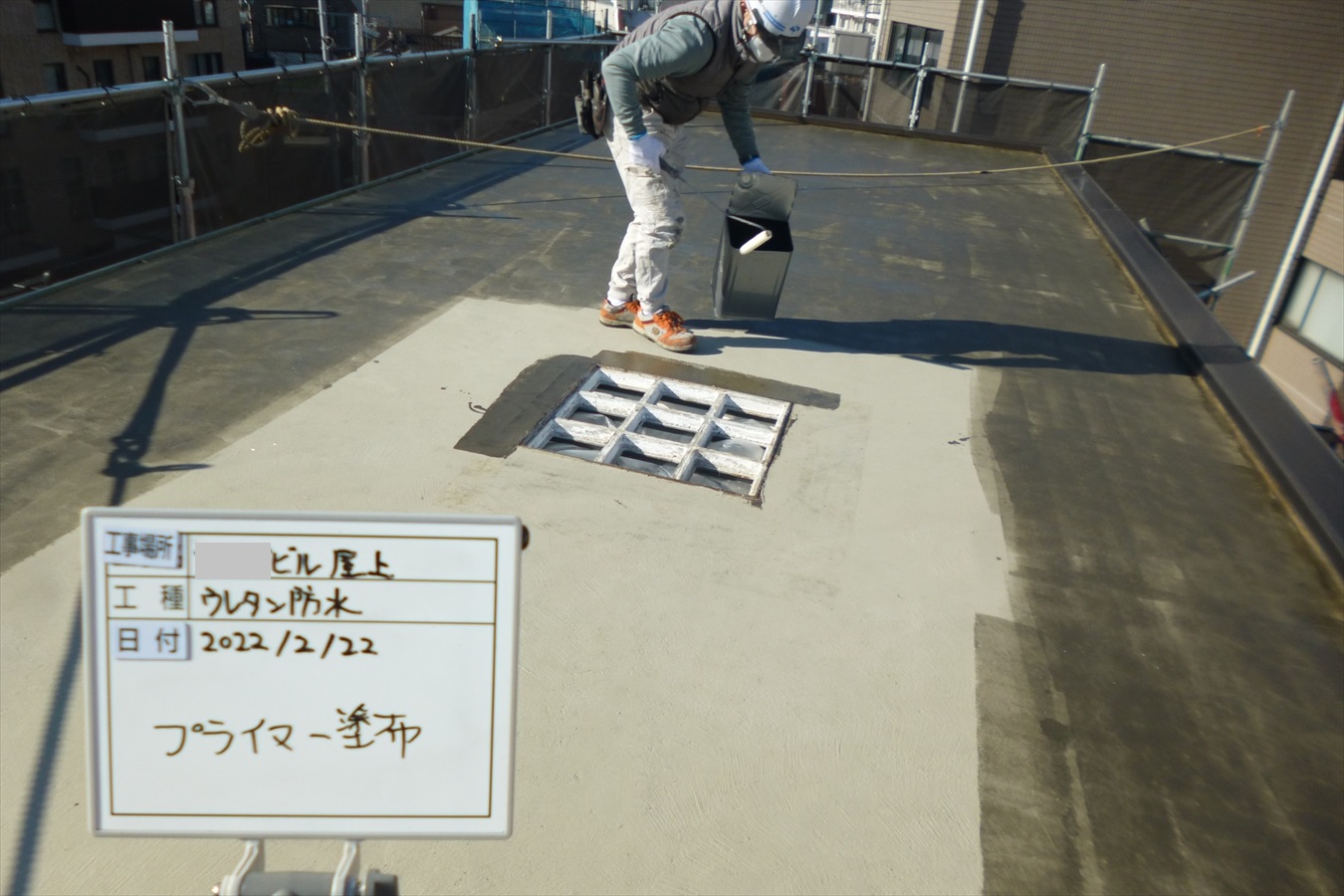
ダメ込みが終わった後に、広い土間にプライマーを入れていきます。ここでも適当に好きなところから塗るのではなく、入口から離れているところから塗っていくのが一般的。写真ではトップライトの周りが入口から一番奥となっているので、そこから入口へ向かってプライマーを入れています。
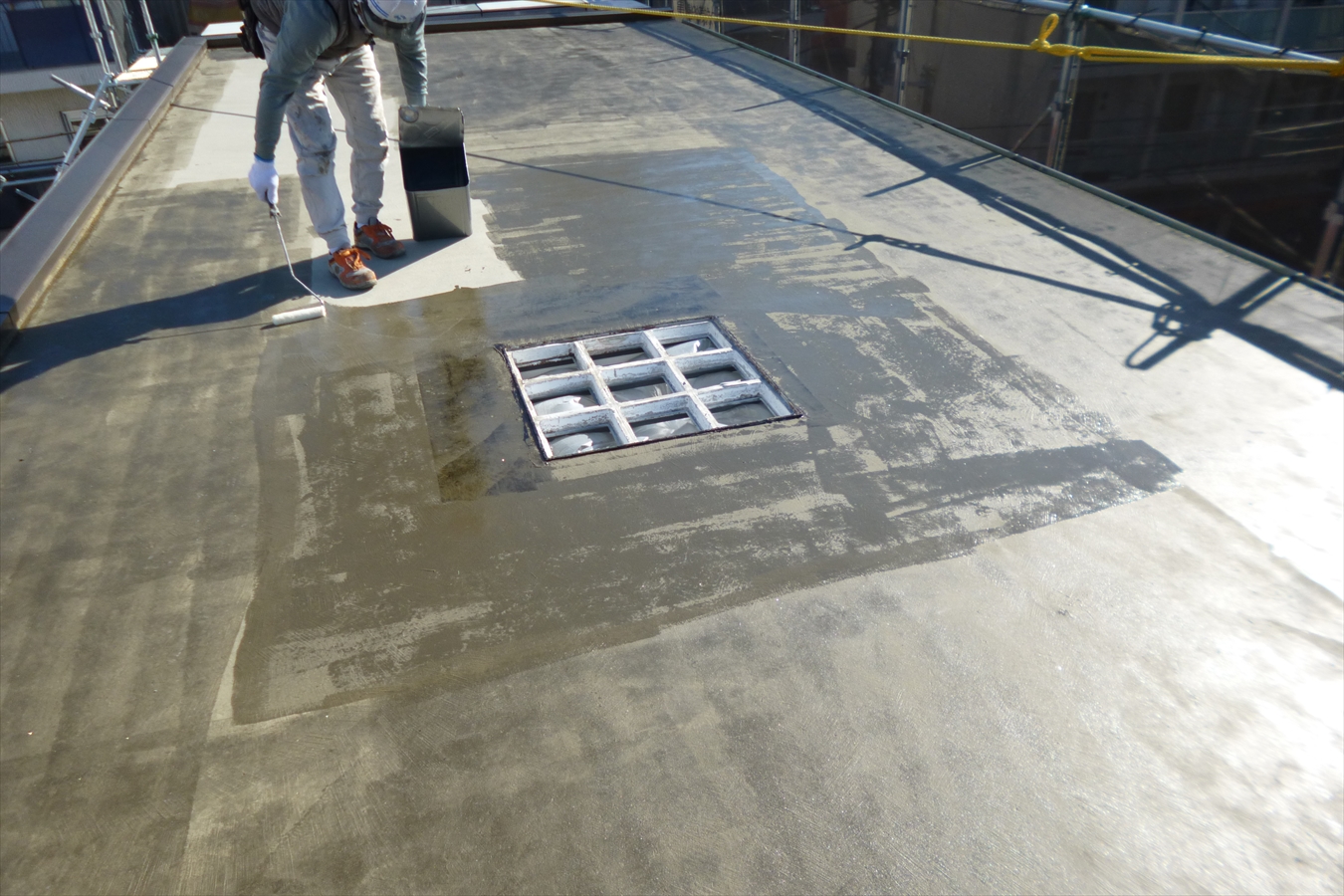
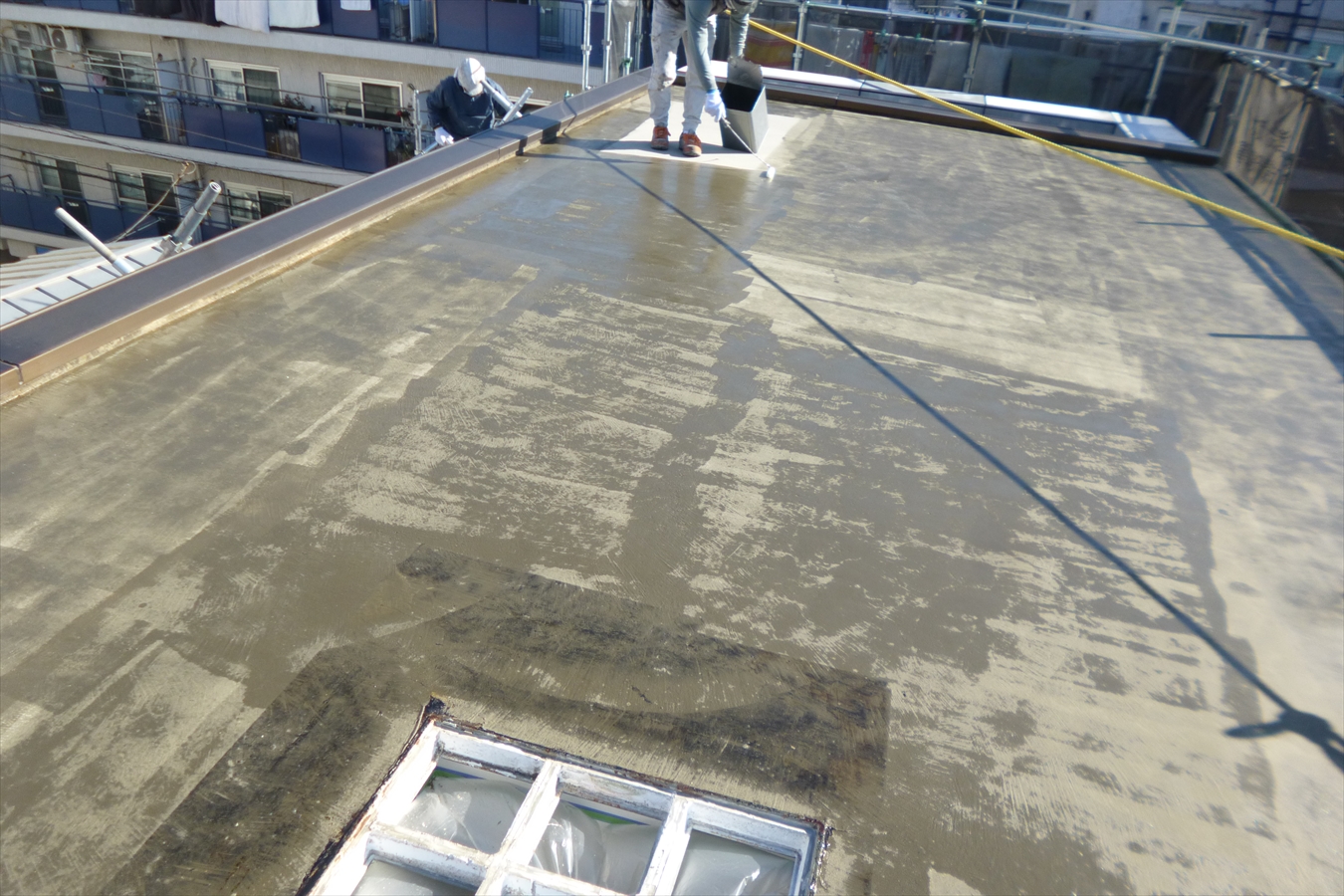
プライマー補修
プライマーを塗った箇所は黒く変色するのは見て分かるかと思いますが、ところどころ白いままの箇所があります。これは塗りムラがあるだとか、手抜きをしているからという訳ではなく、乾燥したモルタルが極度にプライマーを吸い込んでしまっているから起きる現象です。
プライマーを吸い込んでしまった箇所は、プライマーを塗っていない状態とあまり変わらない状態のため、そのような箇所は再度プライマーを塗り込む必要があります。写真で行っているのは、そのような極端にプライマーを吸ってしまった箇所に再度プライマーを塗っている作業です。塗り直したため、プライマーの十分な効果が期待することができます。
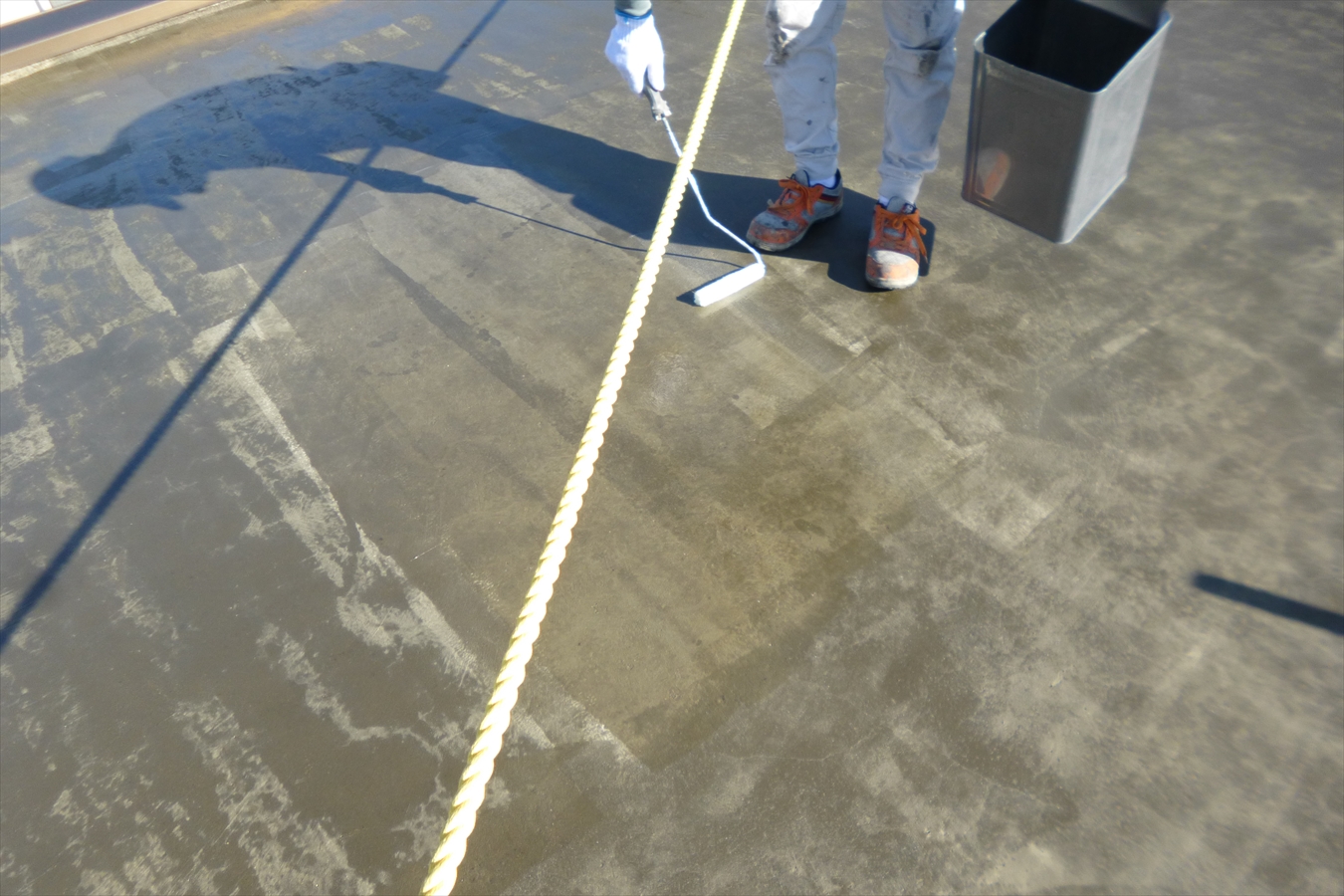
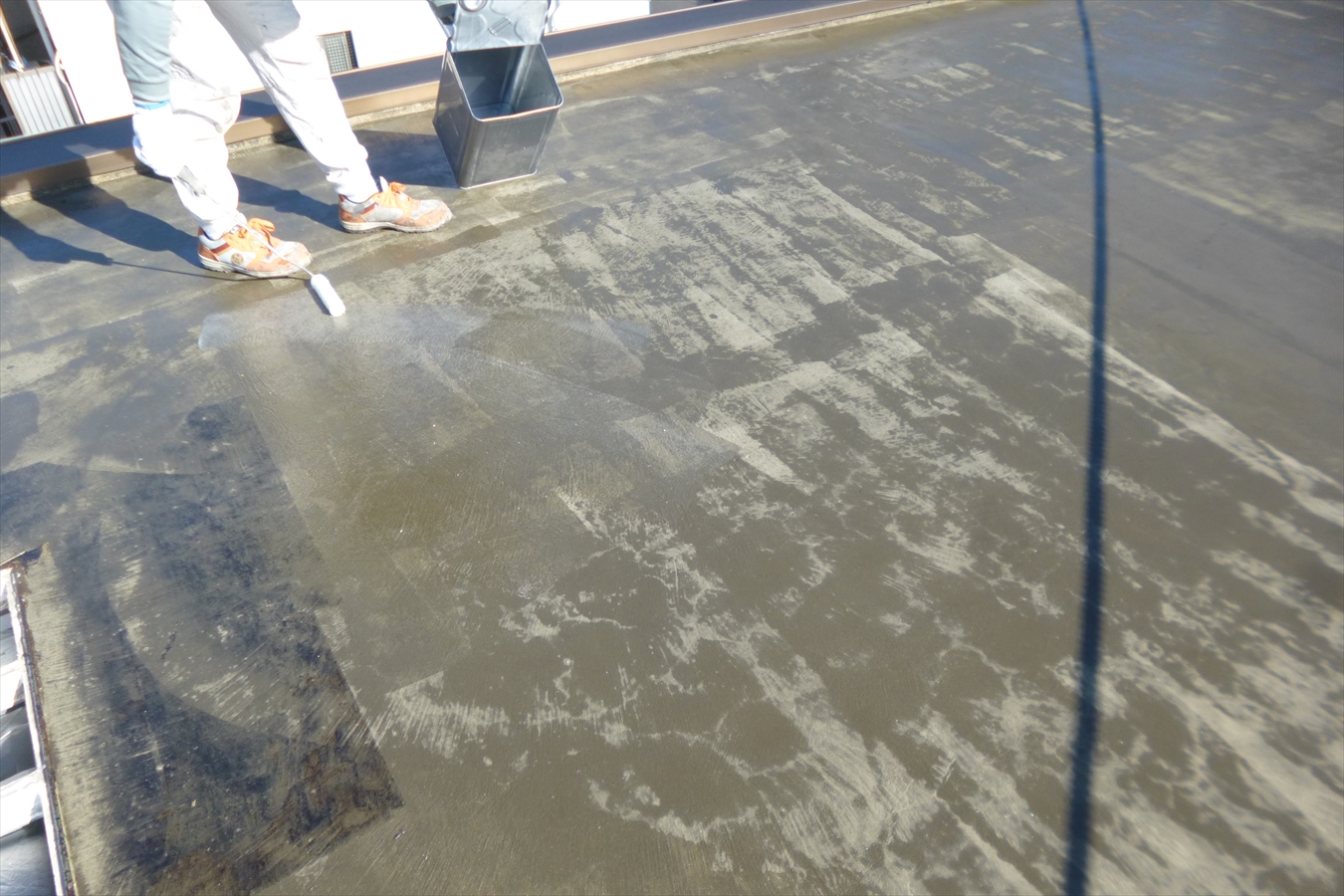
施工後
塗っていなかった箇所と、極度に吸い込んでしまった箇所のプライマーの塗り込みが終わった後の写真です。色がまだらで、ところどころ白いままの箇所もありますが、これはプライマーが入っていない訳ではないので心配はいりません。下地補修の時と同じようにプライマーの乾燥を待ち、完全に乾かしたら次の作業を始めていきます。
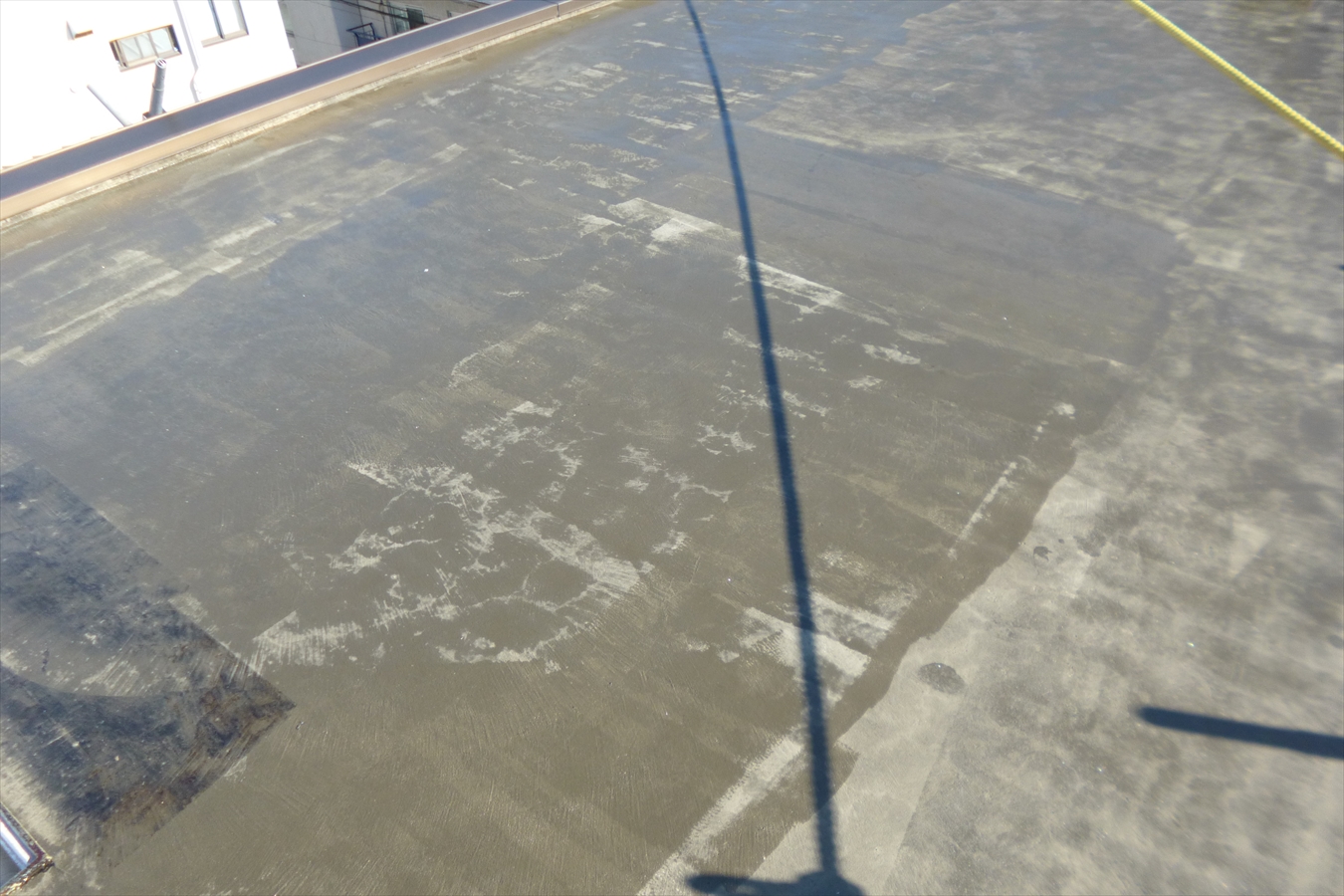
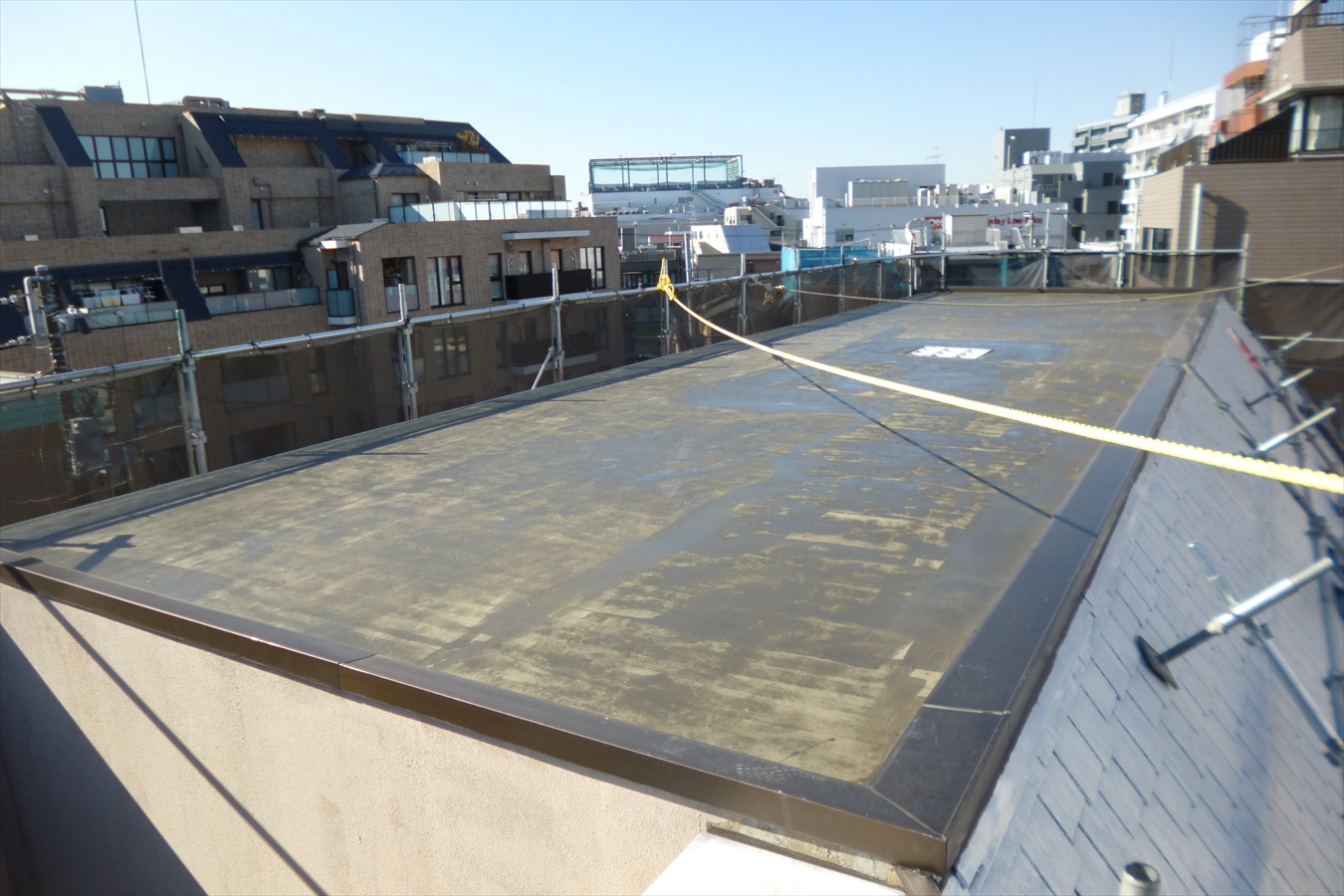
シーリング
プライマーの乾燥が済んだらより強固な防水力を得るため、ここでひと手間加えていきます。この建物は、過去に雨漏りをしたことがあり、屋上のトップライト周りにブチルテープを貼ることで対応しとりあえず雨漏りを止めていました。絶対にトップライト周りからの雨漏りが原因だ、とは断定できませんが、ここが雨漏りの原因である可能性も完全に否定することもできません。
一見、トップライトの周りはモルタルがしっかりと充填されて隙間がないように見えますが、実は僅かな隙間がありそこから雨漏りをしていた…というのはよくあること。そういった経験則から、ここにシールを打ちました。
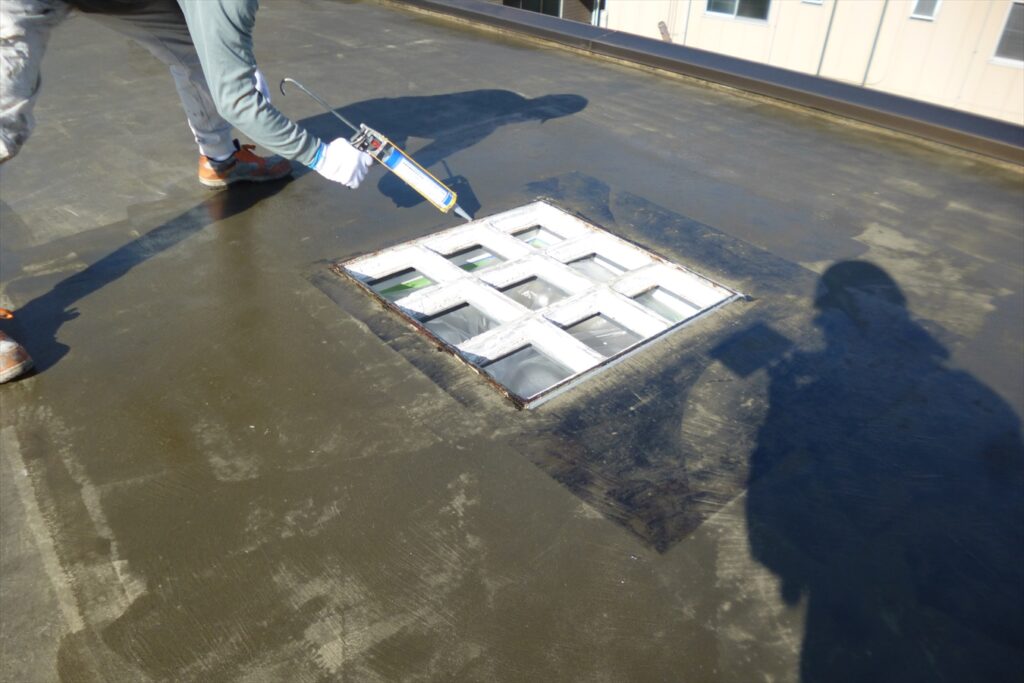
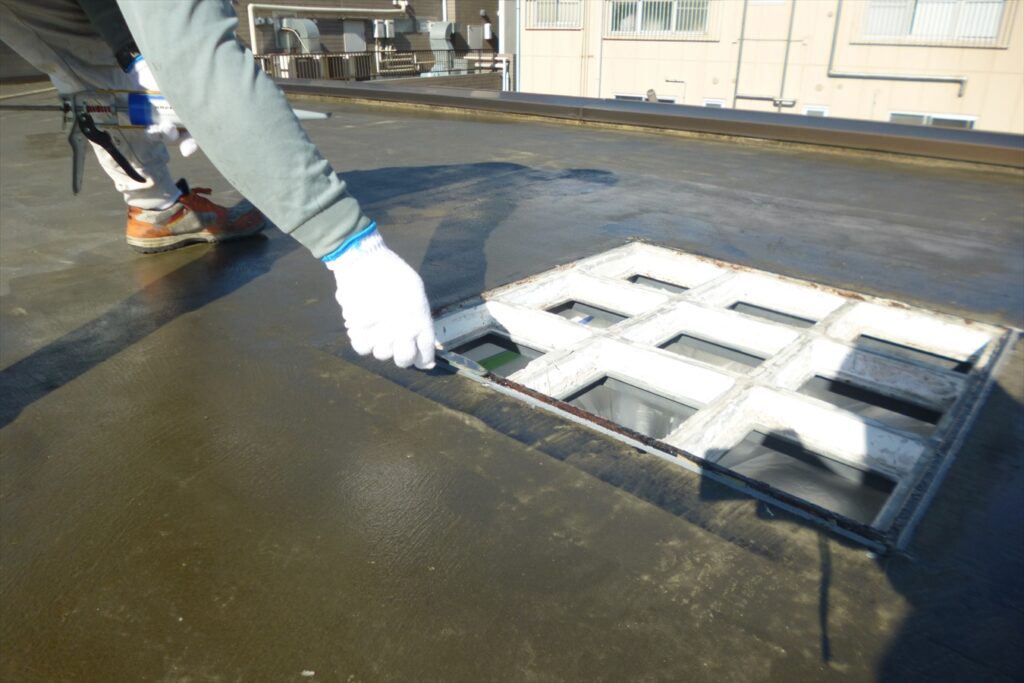
QVシート貼り
施工前
トップライト周りにシールを入れ、補強したところで通気緩衝シートの貼り付けの施工を行っていきます。ウレタン防水には密着工法と呼ばれるものと、通気緩衝工法と呼ばれる2種類があります。密着工法はその名の通り、ウレタンをモルタルやコンクリートに直接密着させる工法で、通気緩衝は通気を得るシートの上からウレタンを被せる工法となっています。
屋上のような広い場所にウレタンを巻く場合、躯体から出る蒸気を逃がす必要が出るため、密着工法は不向きです。これを無視して密着工法で施工してしまうと、躯体から出る蒸気が、内側から巻いたウレタンを圧迫し膨れさせ、最悪ウレタンを突き破って雨漏りの原因となってしまいます。そのような事態に陥らせないためにも、屋上では蒸気を逃がす事ができる通気緩衝工法が採用されるのが一般的となっています。
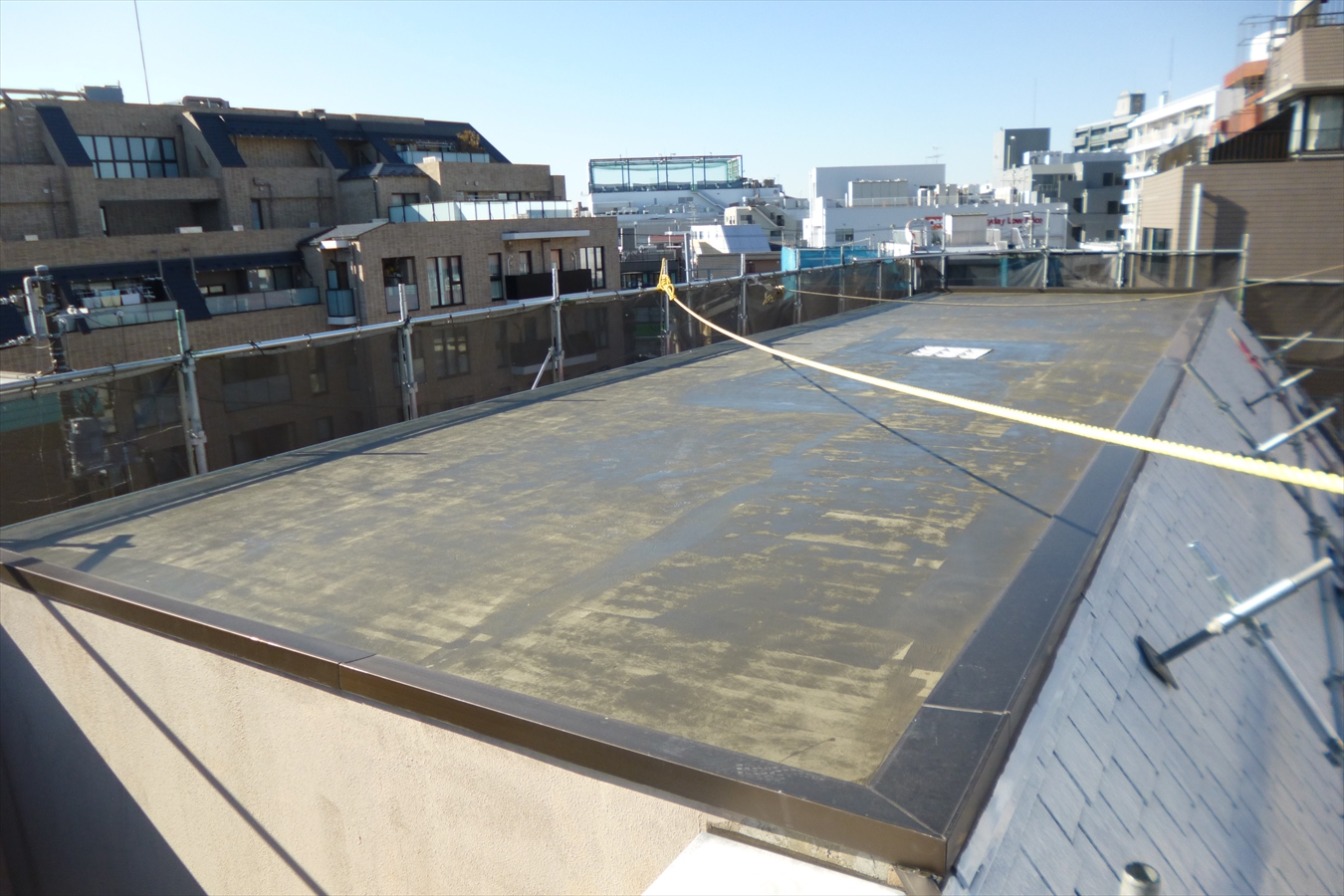
シート貼り付け
実際に通気緩衝となるシートを貼り付けているところです。メーカーごとにこのシートの呼び方は違いますが、機能は同じ。サラセーヌの一式に入っている通気緩衝シートはQVシートと呼ばれるものになります。一目見ただけでは分かりづらいですが、このシートは土間に完全に密着するように作られておらず、意図的に土間とシートの間に隙間ができるように作られています。
その隙間が躯体から出る蒸気の通り道になるようになっており、最終的には脱気筒と呼ばれる筒から抜けていく仕組みです。写真はその通気緩衝のシートであるQVシートを実際に貼り付けているところです。
シートがヨレてしまったり斜めに貼り付けてしまうと、ヨレた箇所に蒸気が溜まってしまったり、斜めになると蒸気を受ける面積が少なくなってしまうので、真っ直ぐに貼り付ける必要があります。また、シートの幅が1mほどしかないため、土間全体に貼り付けるのには何回も同じ作業が必要になってきます。
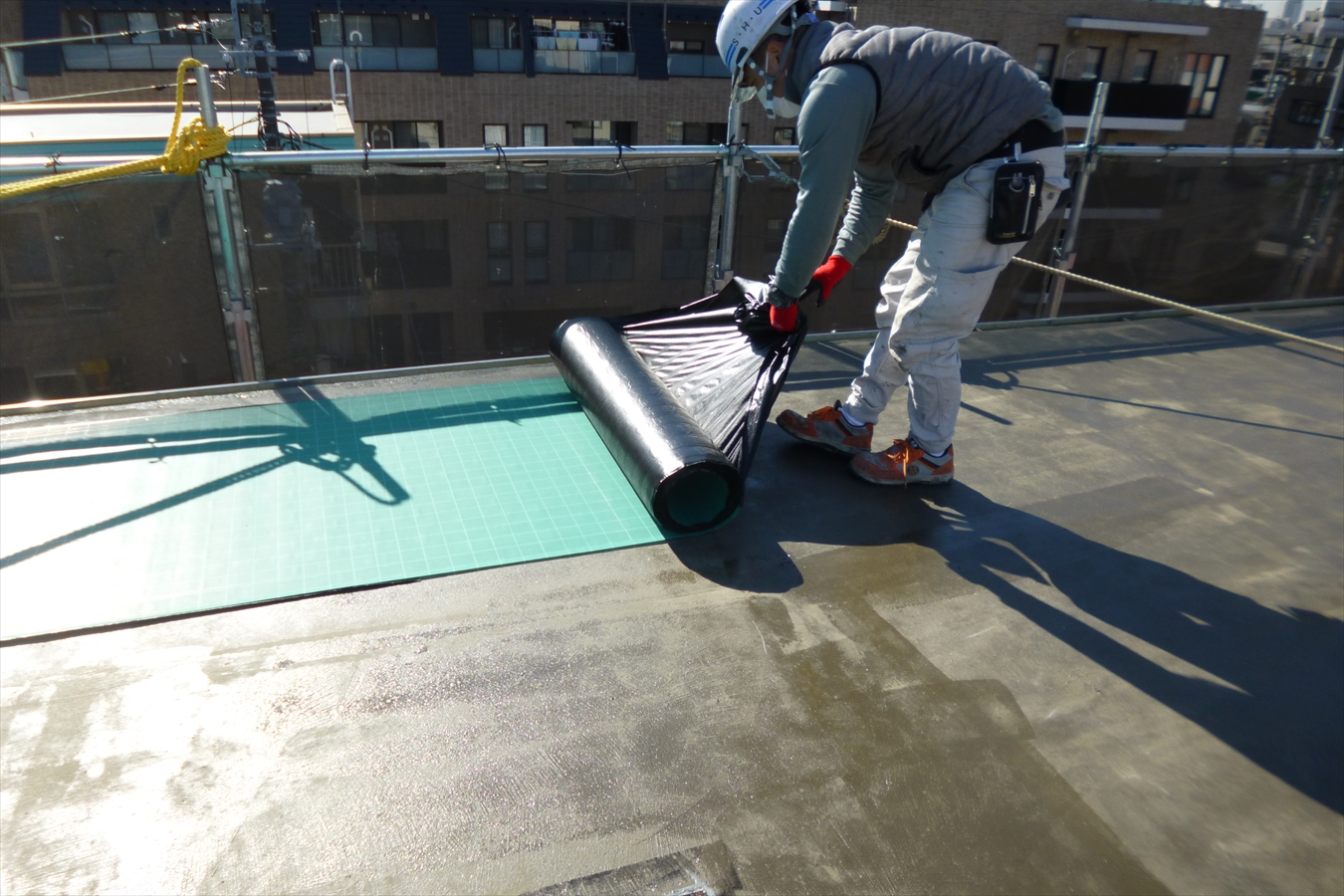
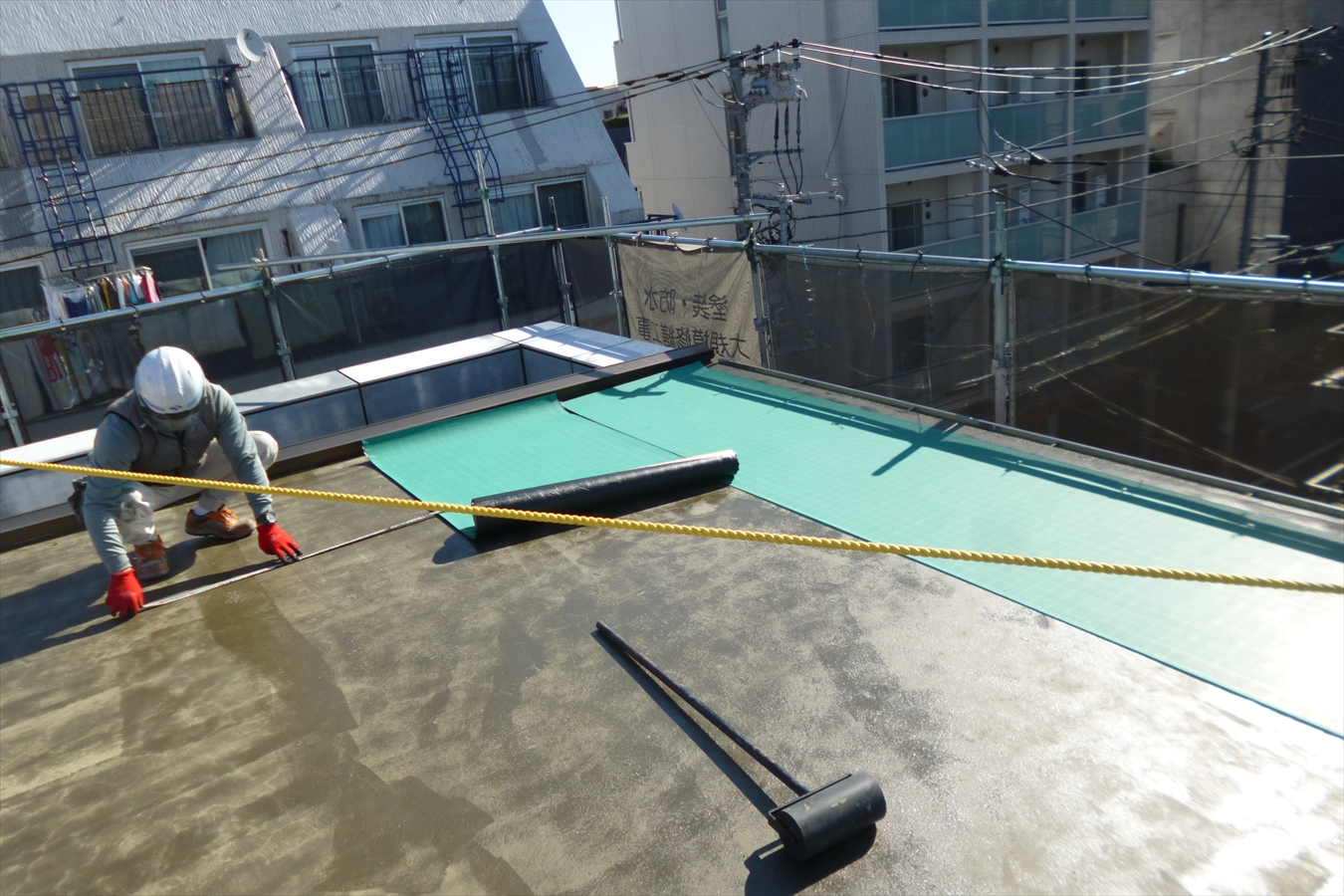
シート加工
土間に小さな役物があったり、この建物のようにトップライトの穴が開いているような場合、QVシートをカットし加工して貼り付ける必要があります。役物そのものを避けられる場合、加工の必要はありませんが、写真のようにどうしてもシートが被るような場合は加工が必要です。
QVシートを伸ばして、トップライトを塞いでしまう箇所をカットしました。この隣にもシートを貼り付けていきます。上手い具合に、トップライトとシートの幅がちょうど同じくらいなので、次に貼るシートは加工せずに済みました。
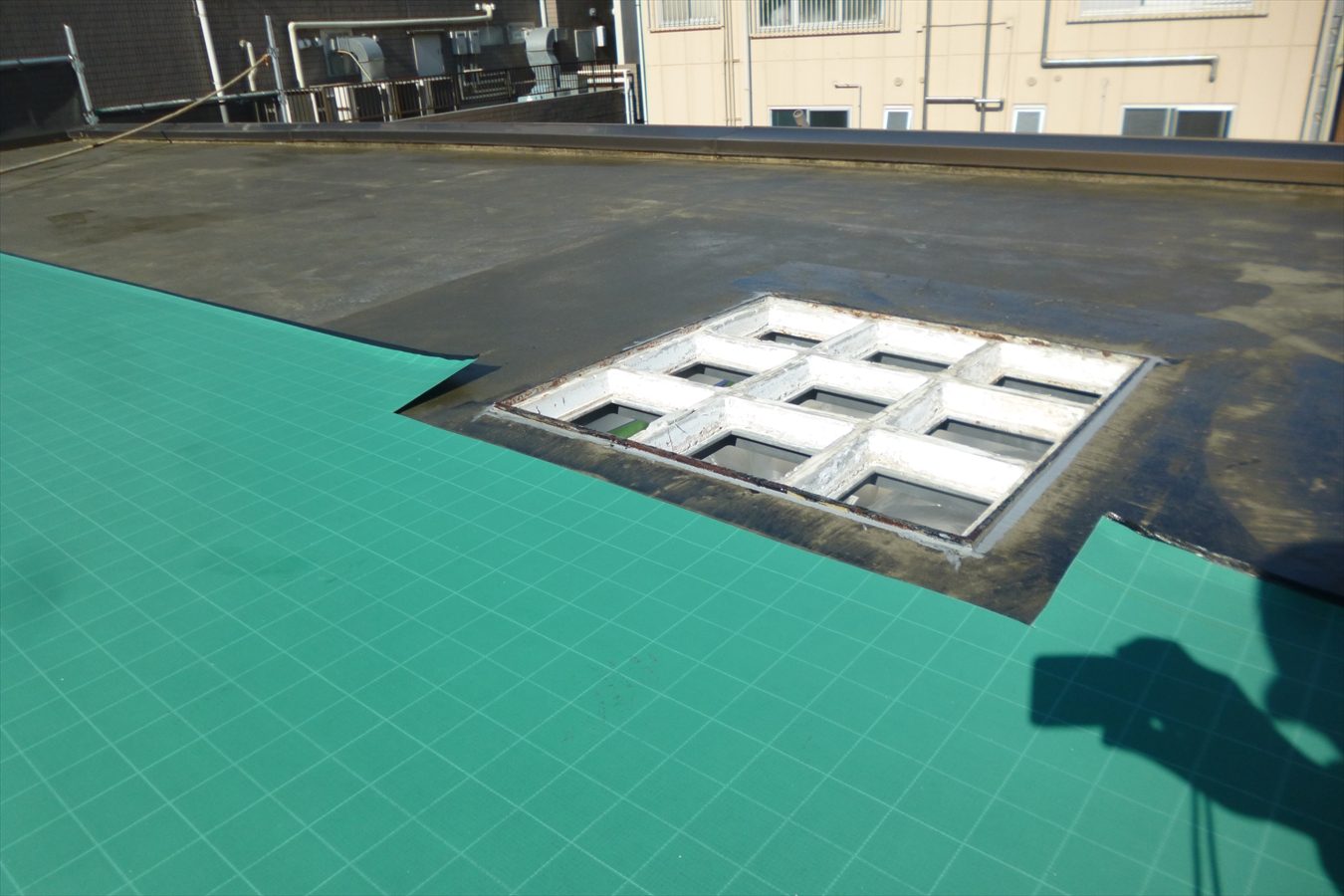
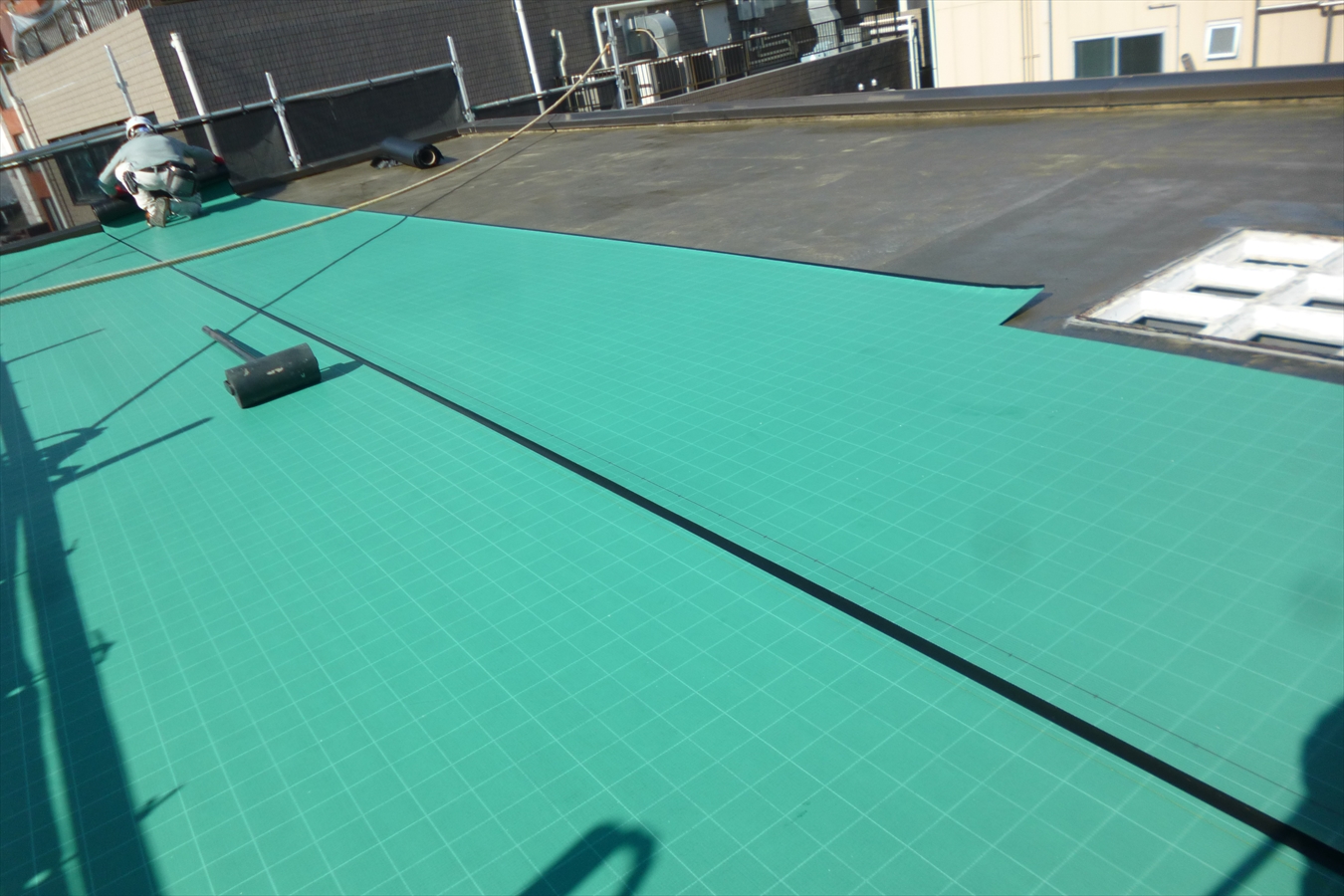
転圧
土間全体にシートを貼り終わったら、転圧ローラーと呼ばれる道具を使いシートをしっかりと接着させていきます。この道具はシートを密着させるための道具で、手だけではどうしても貼りムラが出るため使用される道具です。また、手で密着させるより早く押え貼り付けることができるため、時間効率も考えれば一石二鳥です。
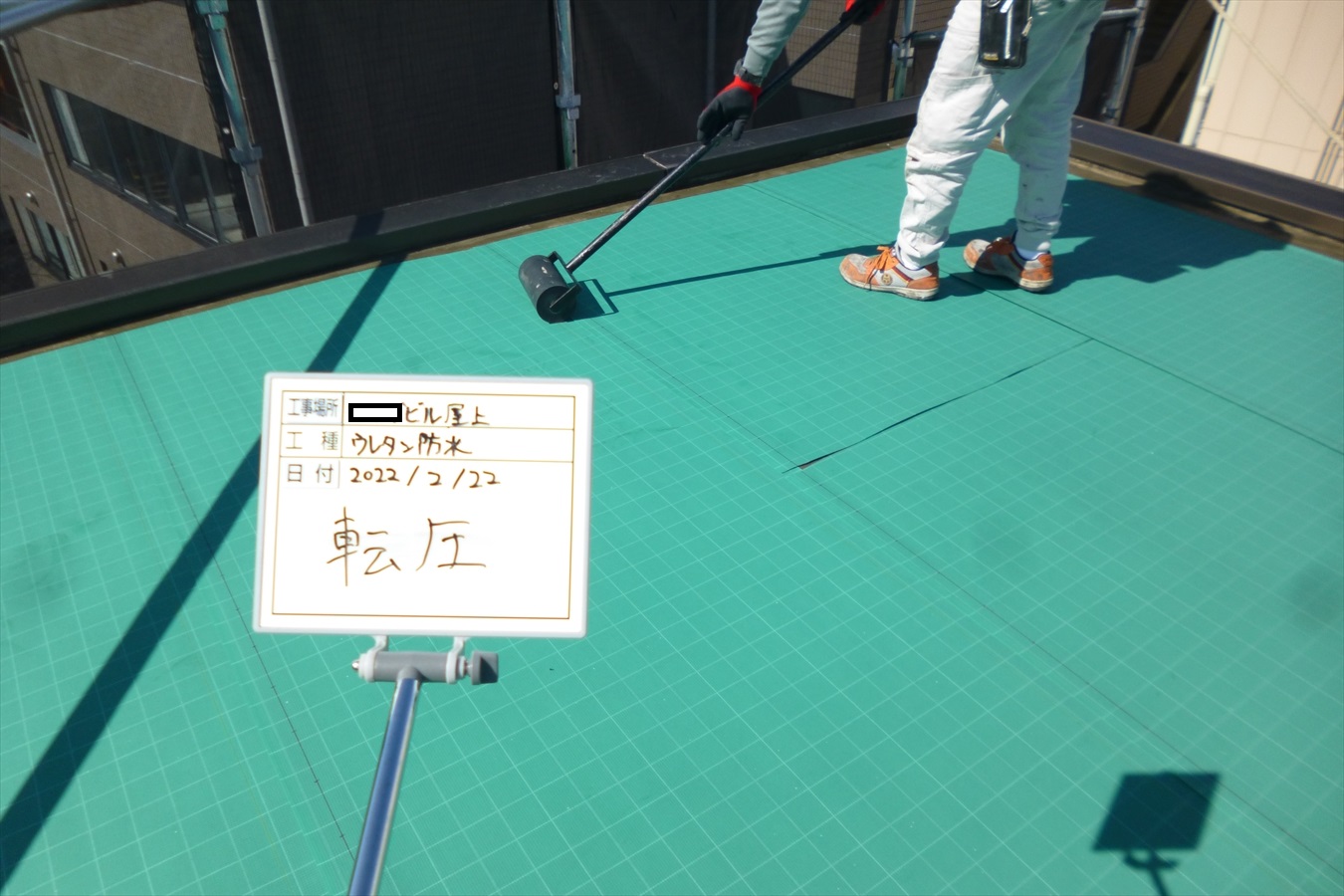
施工後
QVシートを貼り終わった後の写真です。サラセーヌのシートの場合、シート同士を重ね合わせていますが、メーカーによってはここに1mm~2mmほどの隙間ができるように貼り付け、その隙間自体も蒸気の通り道にするようにするタイプのものも存在します。シートを貼った後はシートの端末部や重なった箇所に、後で流すウレタンが回り込んでしまったり、突然の雨で水が入り込んでしまわないようテープを貼り付けていきます。
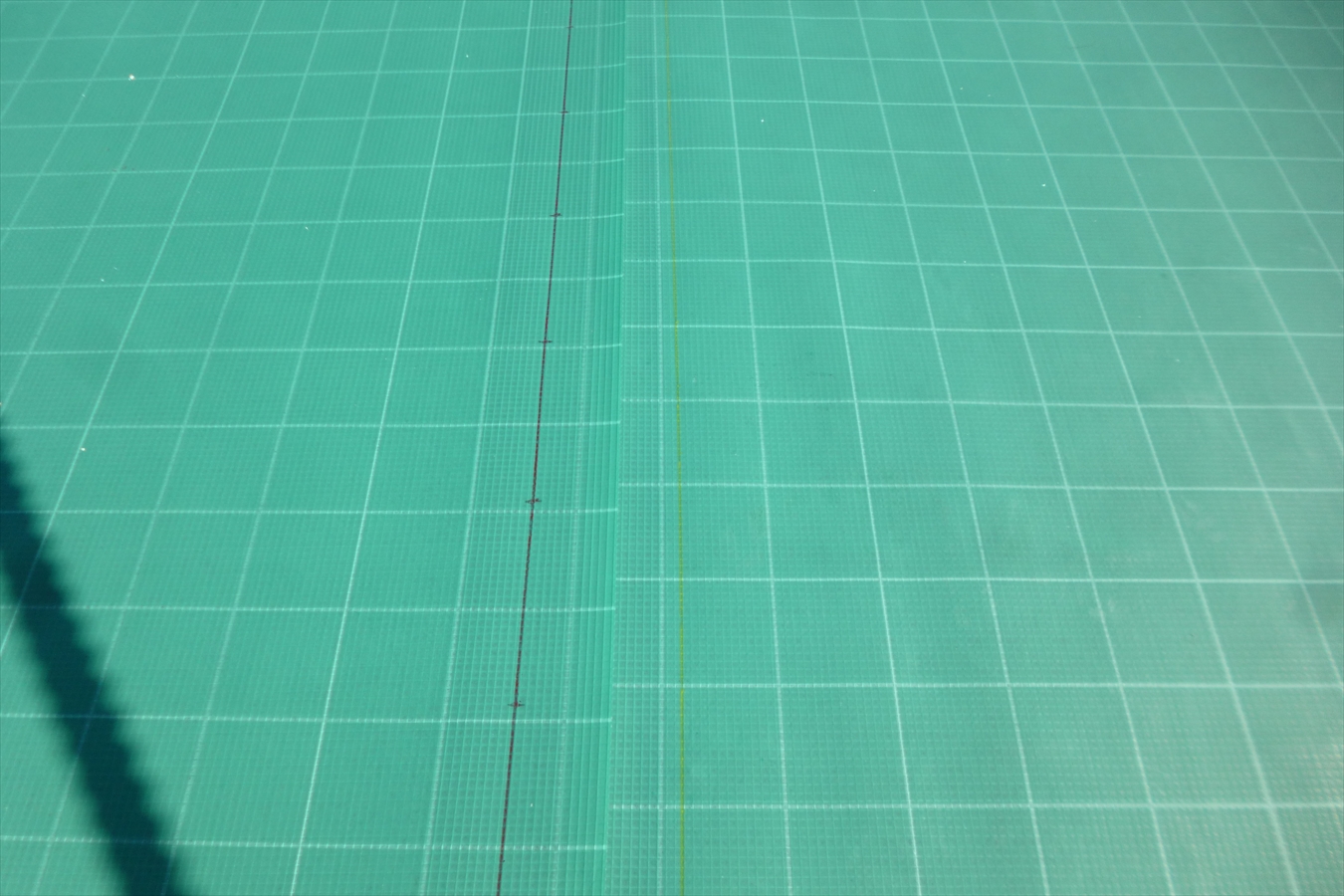
ジョイント・端末テープ貼り
QVシートの重なったジョイント部分と、端末箇所にテープを貼り付けていきます。今回はジョイントテープ、端末テープが別のものとなっていますが、メーカーによっては同じものを貼り付ける仕様になっていることもあります。
QVシートのように転圧ローラーを使うことはありませんが、これらのテープもしっかりと密着させるように貼り付け、ウレタンが漏れてしまわないようにします。
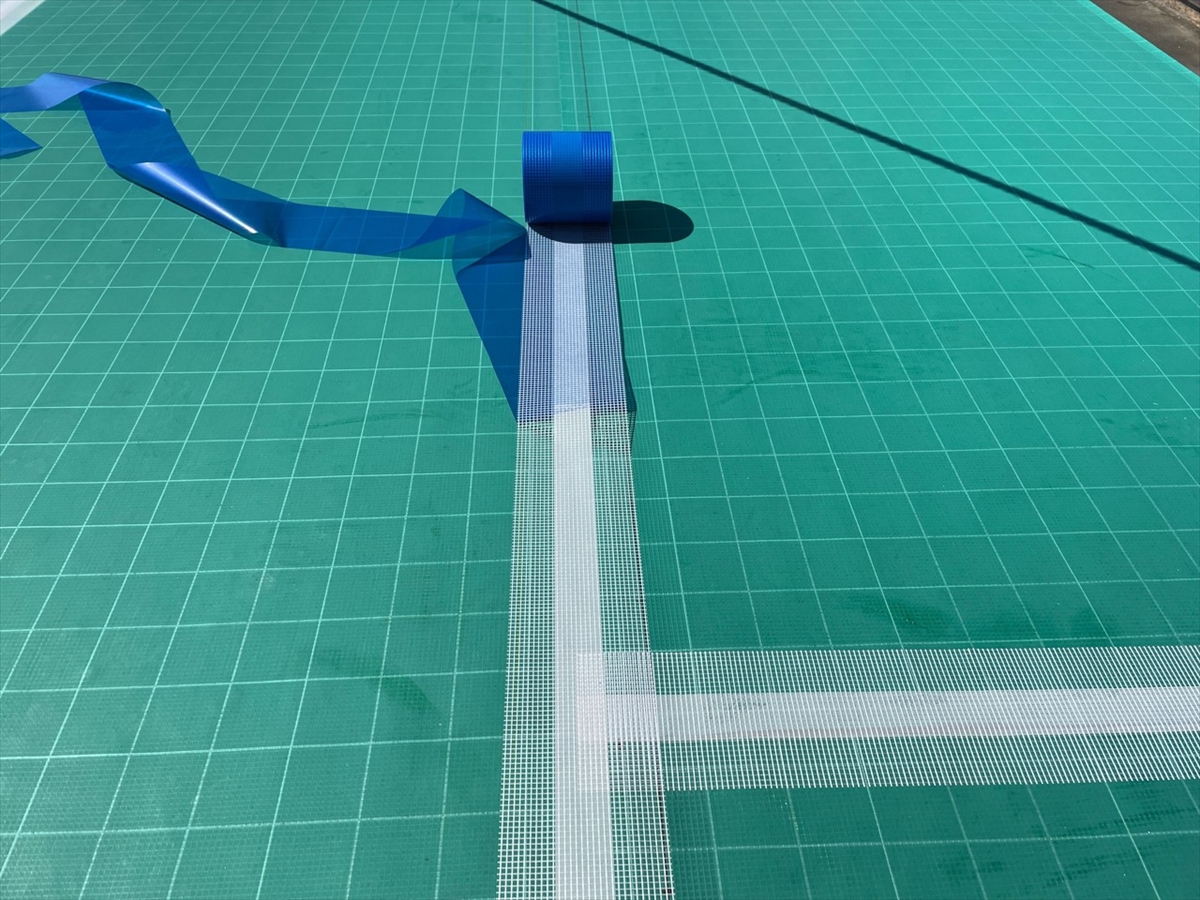
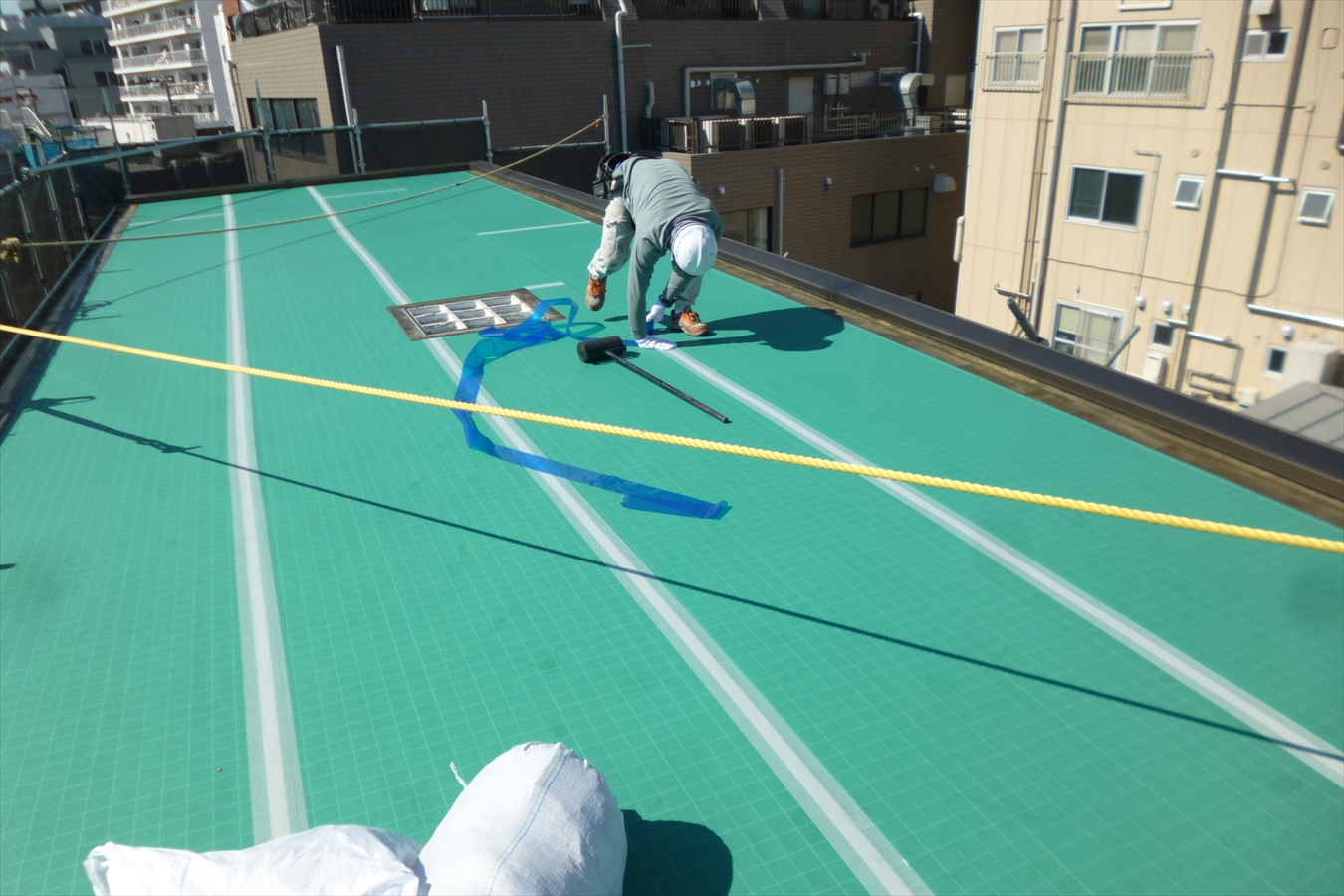
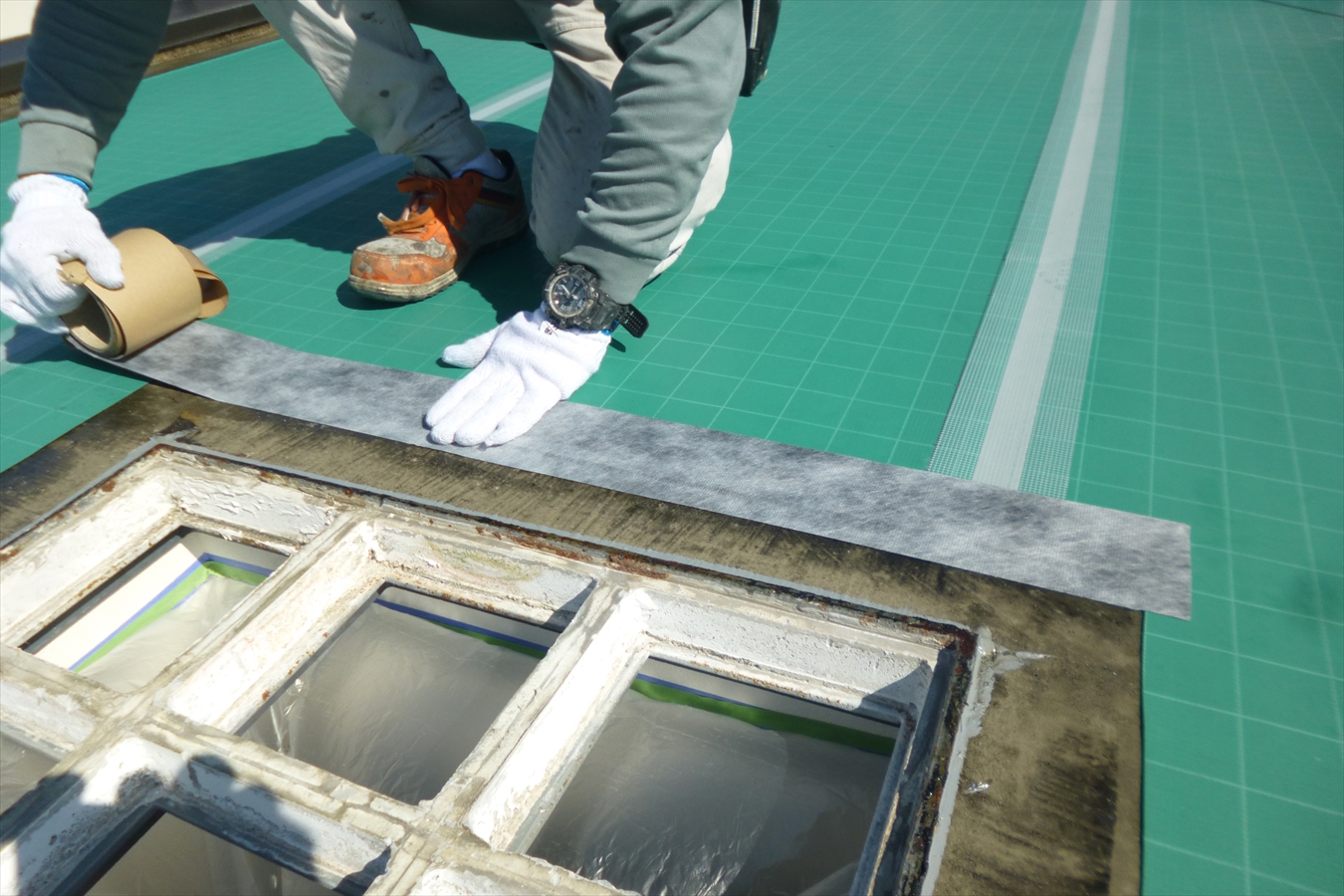
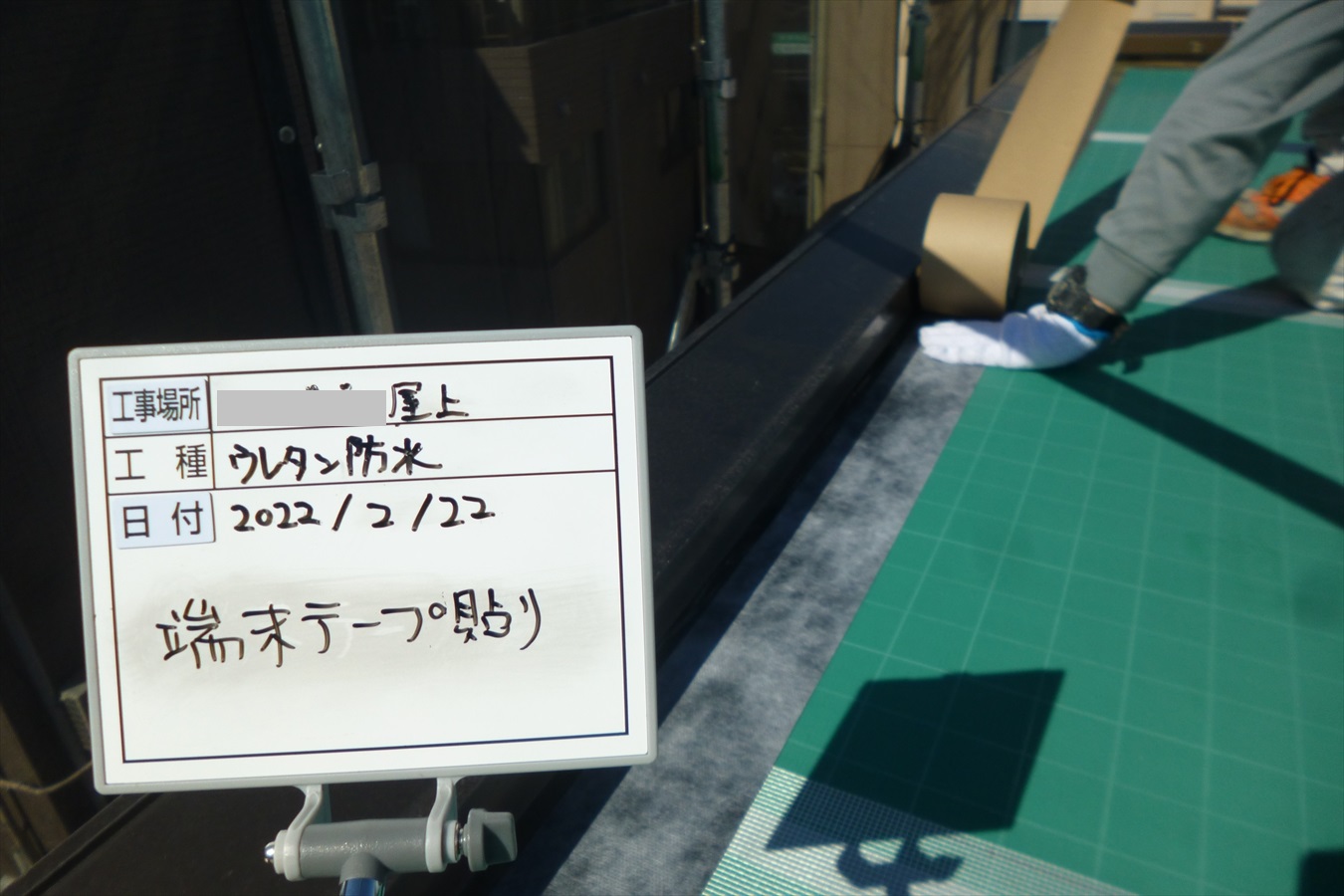
脱気筒設置
脱気筒 設置箇所シート切開
QVシートの工程の最後は、蒸気を逃がすための脱気筒設置です。脱気筒は勾配の高い位置に設置するのが一般的となっています。脱気筒はドリルで穴あけをしそこにネジ止めすれば良いのですが、いくら設置してもシートに逃げ道が無ければ蒸気の逃げようがありません。
そのためまずは脱気筒を設置する箇所のシートをカットし切開しておく必要があります。写真は脱気筒を設置する箇所のシートの切開が済んだところです。これからこの上に脱気筒を設置していきます。
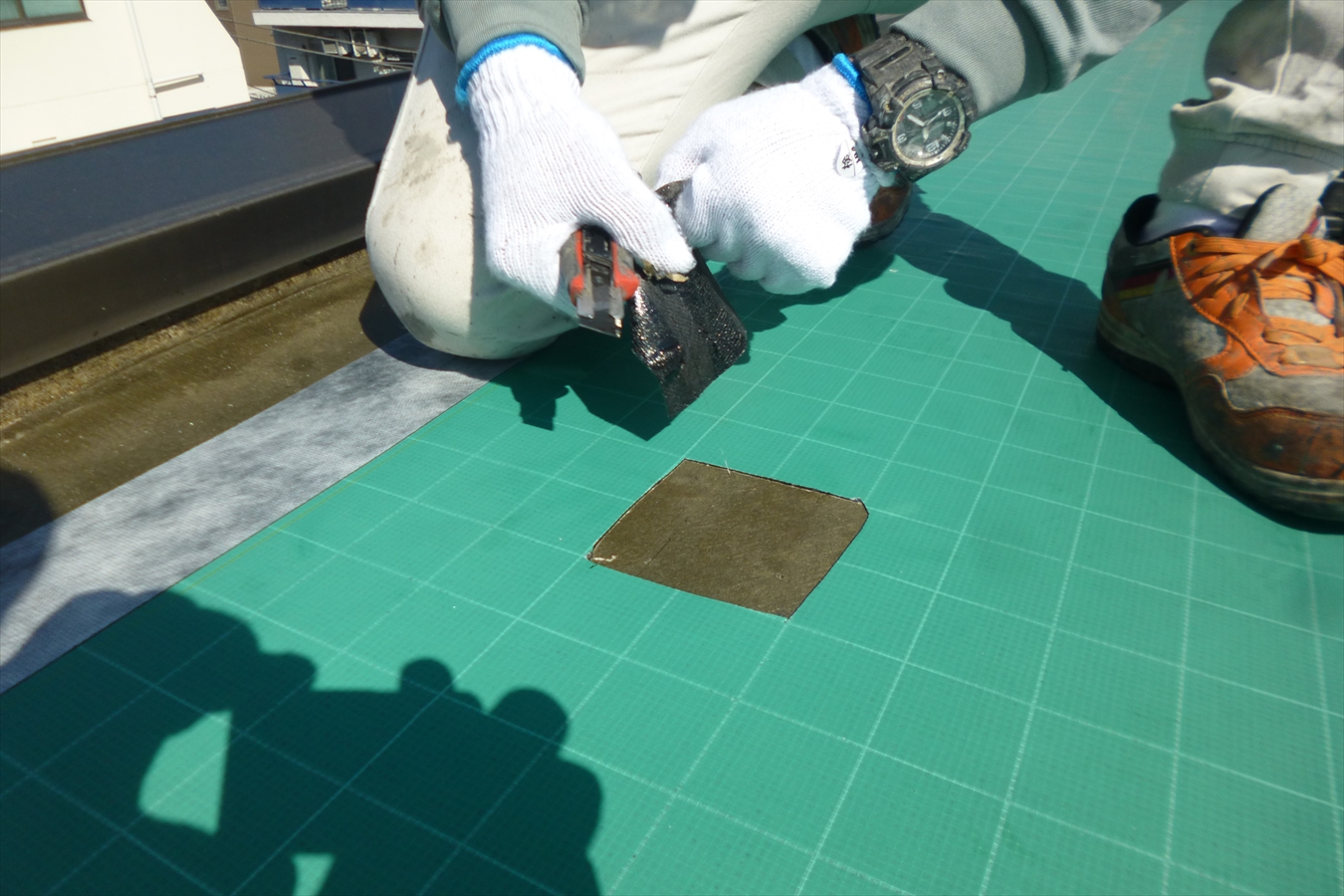
穿孔
脱気筒を設置するために穿孔(穴あけ)をします。特に難しいことはなく、脱気筒にあるネジ止めの穴に合わせて土間に穴あけをするだけです。穴を開けただけではネジで固定することができないので、穴にアンカーを差しておきます。
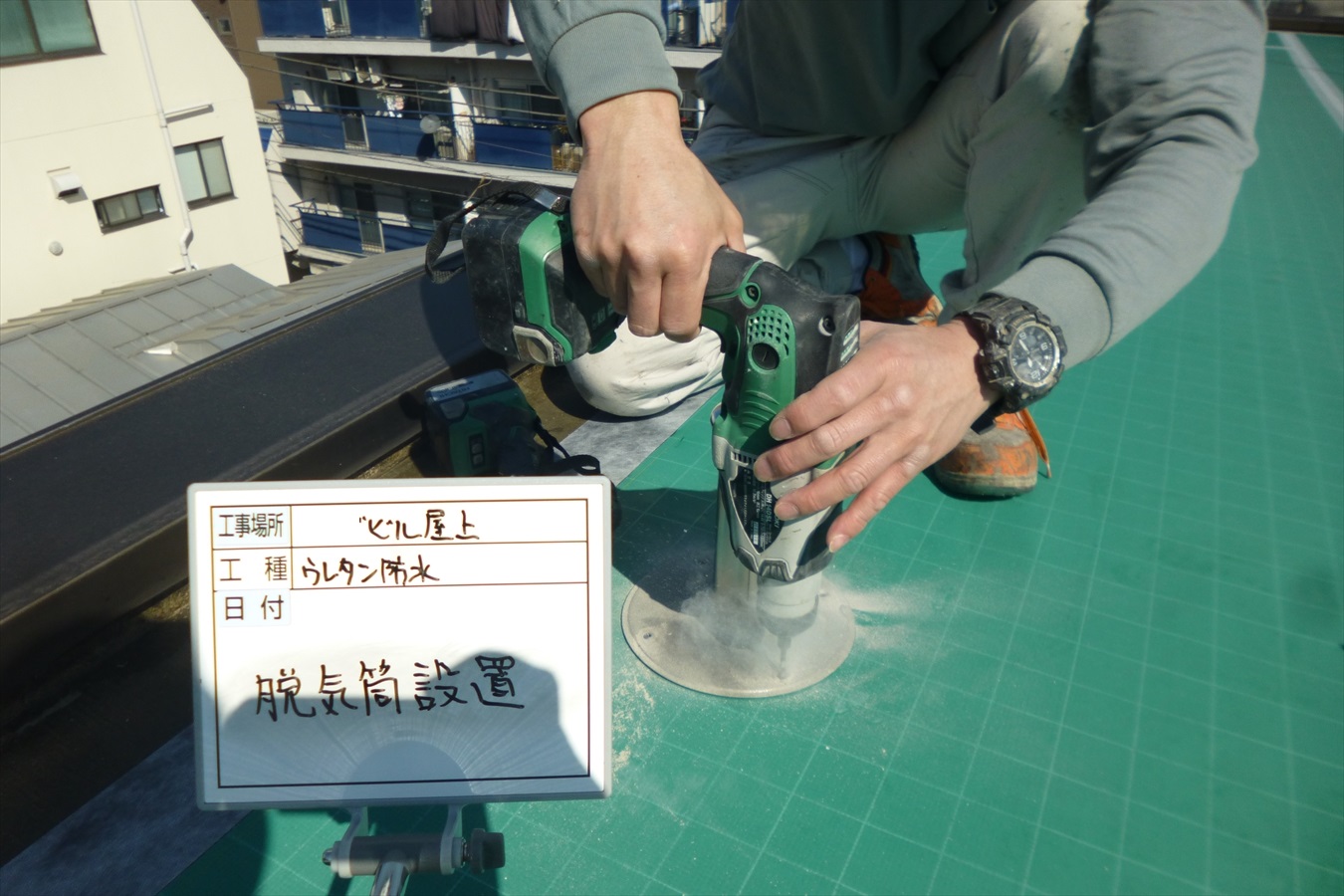
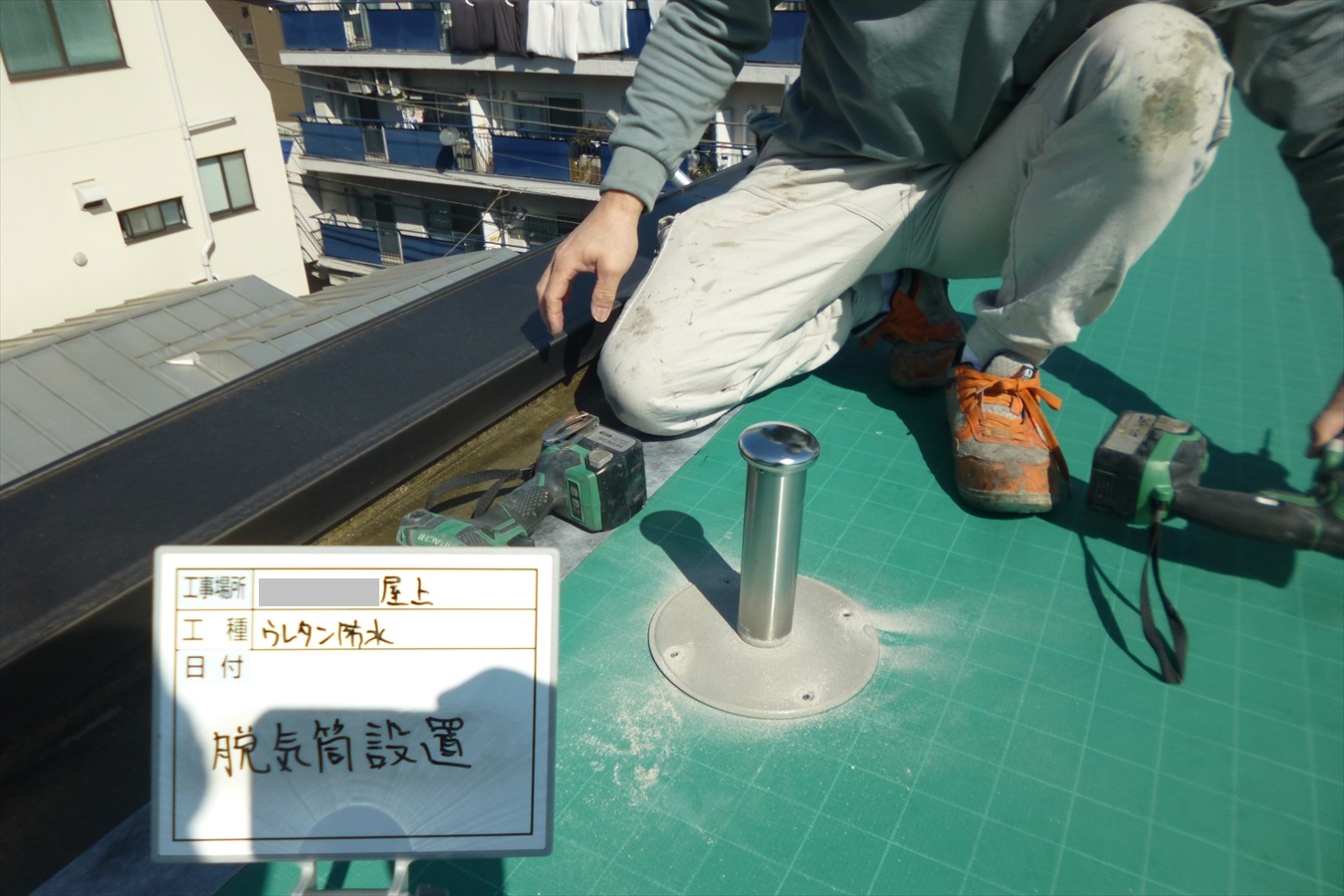
脱気筒設置完了
アンカーの上に脱気筒を置いて、最後にネジ止めをすれば脱気筒の設置は完了となります。天候の悪い時期など、ネジの周りや脱気筒の周りにシールを打つこともありますが、当面晴れていることが分かっている場合は、そのままメッシュクロスを入れてウレタンで押え補強します。
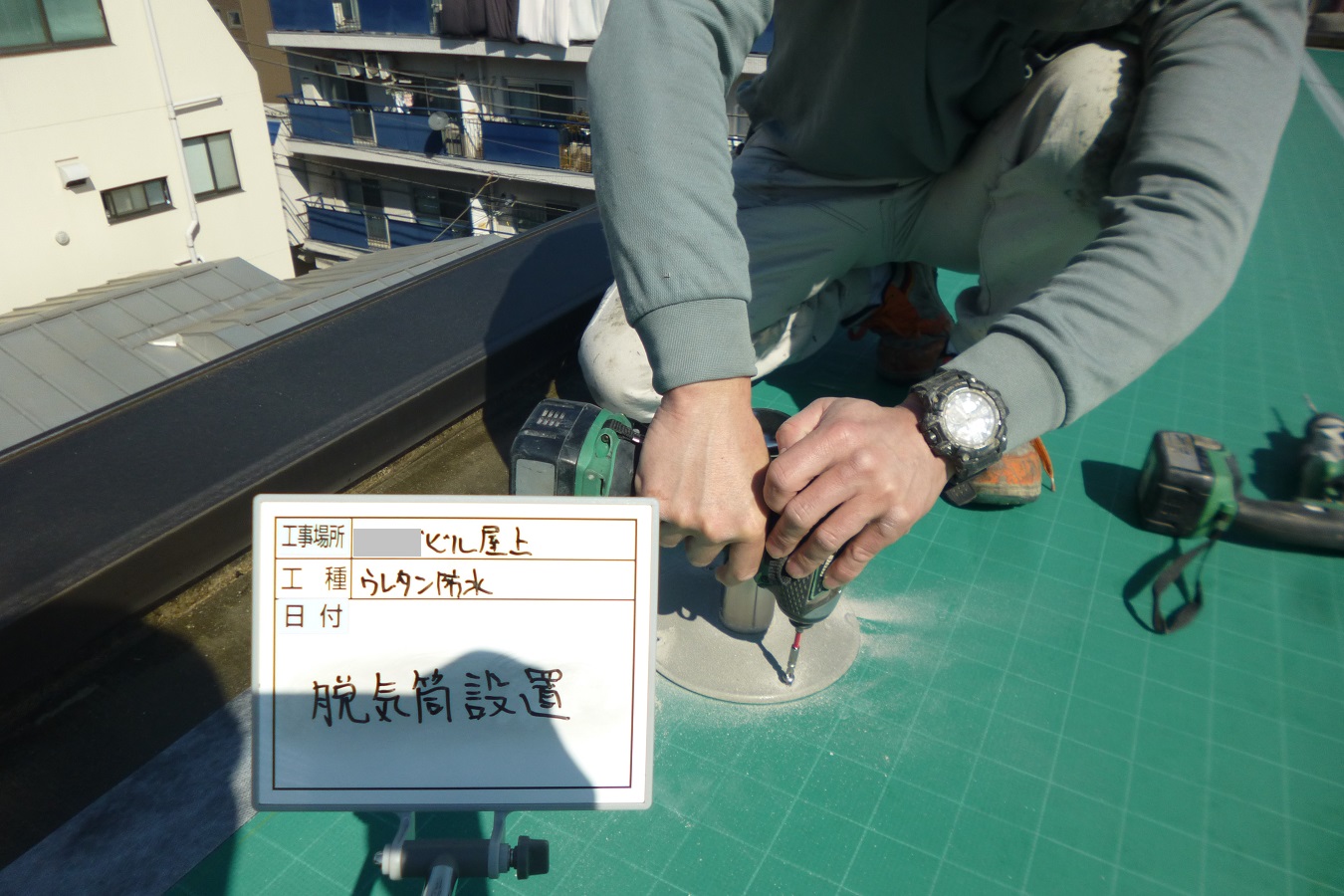
ウレタン塗布・施工前
QVシートを貼り終わったらいよいよウレタンを使った作業となります。前日のQVシート貼り付けの後、トップライト周りの囲いが取り付けられました。囲いを固定しているネジを外し、作業へ取り掛かっていきます。屋上の防水であれば、本来なら立ち上がりと呼ばれる屋上を囲う壁や、アンテナ架台などから手をつけていくのが一般的ですが、この建物にはそのようなものが基本無い現場です。
しかしトップライトの周りに新たに囲いを新設し、それが唯一の架台となったため、まずはそちらから対応していきます。本来立ち上がりや架台は「立ち上がり材」と呼ばれる材料を使うのが一般的。しかしこの現場では「平場材」と呼ばれる材料と立ち上がり材をブレンドした材料で仕上げることにしました。二つの材料をブレンドすると、ゴムベラで均した時のムラをキレイに消せるというメリットがあり、ウレタン防水では結構な頻度で使用されています。
写真に写っているのが実際に使われた材料です。立ち上がり材に関してはそのまま、立ち上がり用と書かれたもの。平場材は、サラセーヌKと書かれた材料がそれに該当するので、こちらを使用していきます。
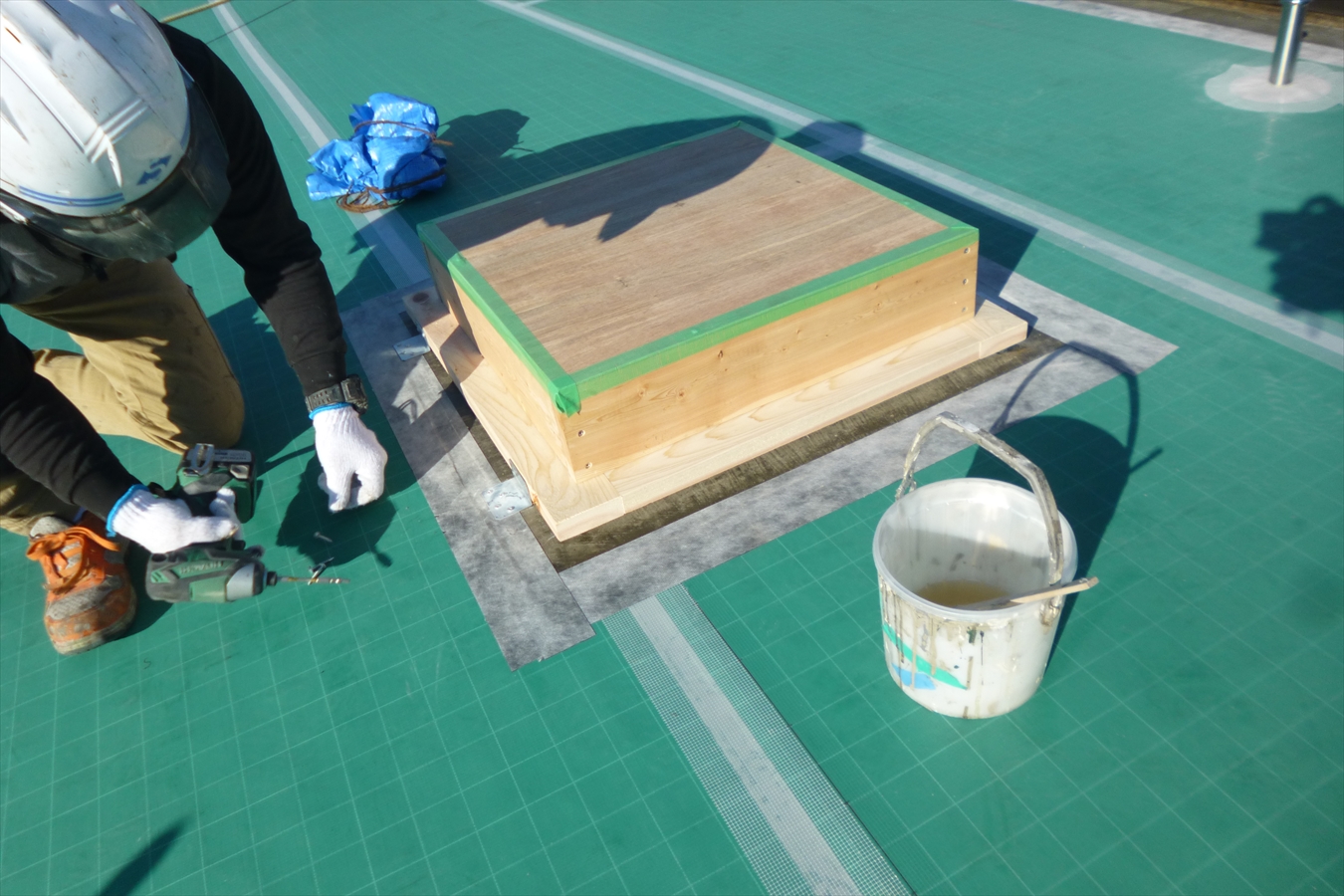
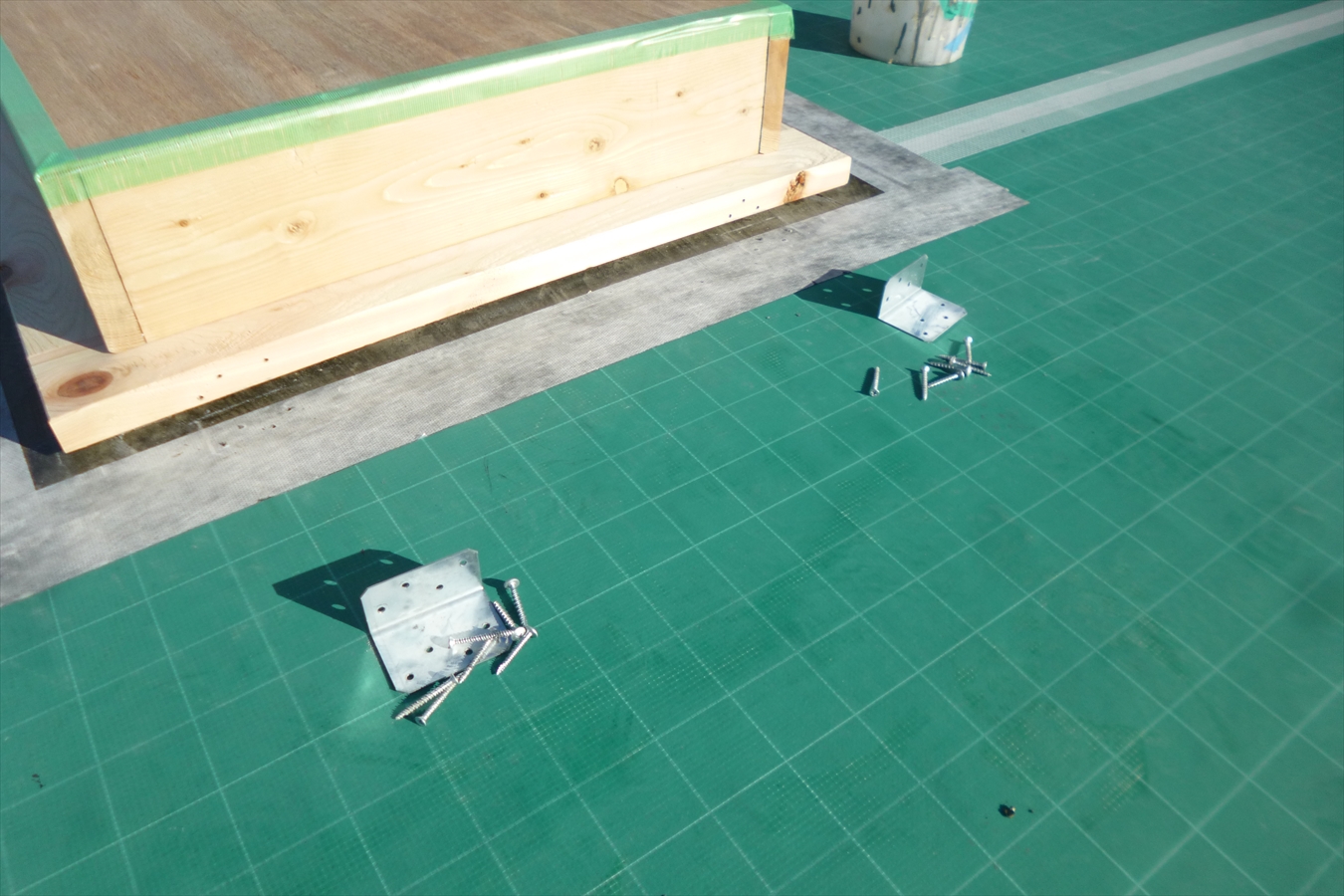
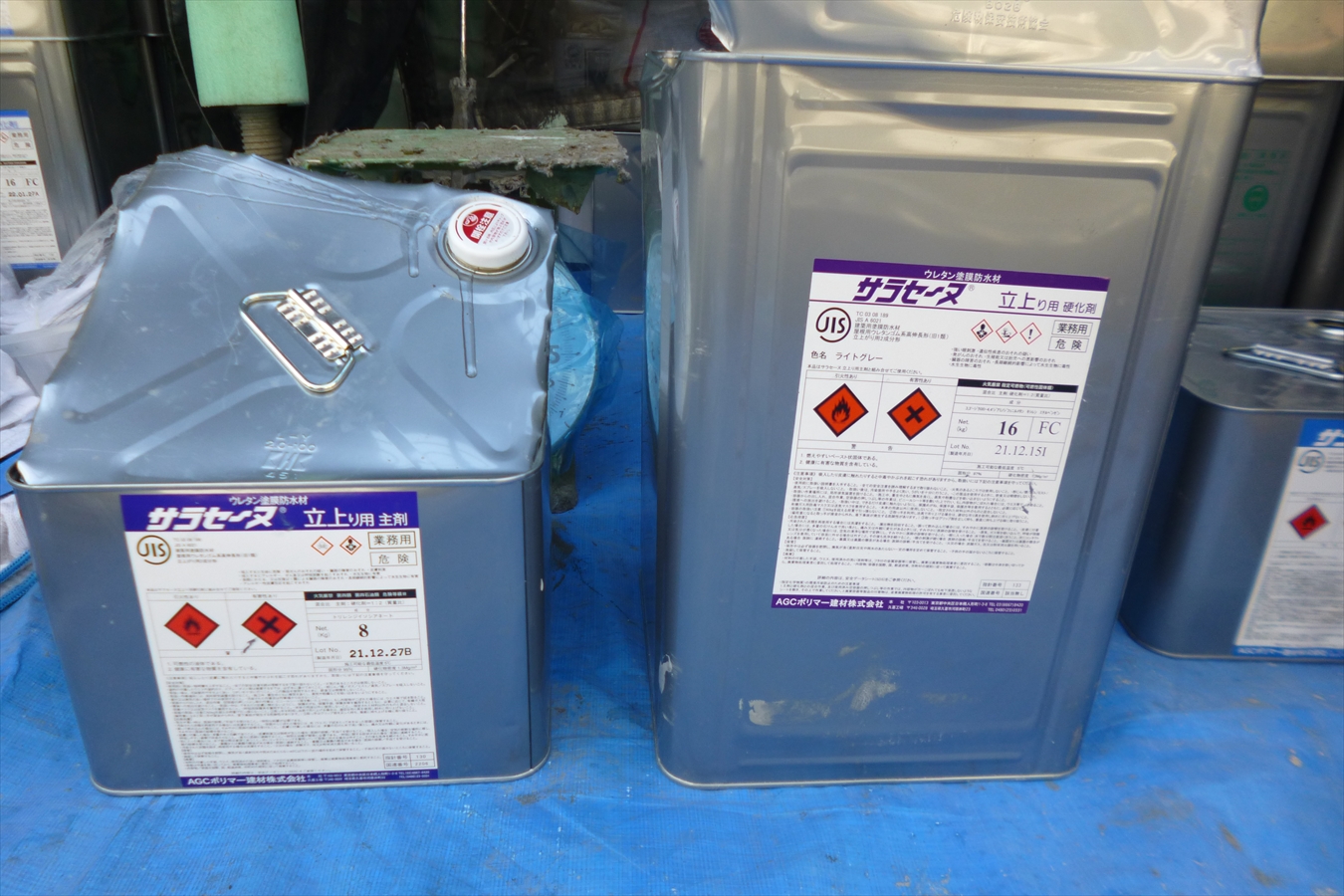
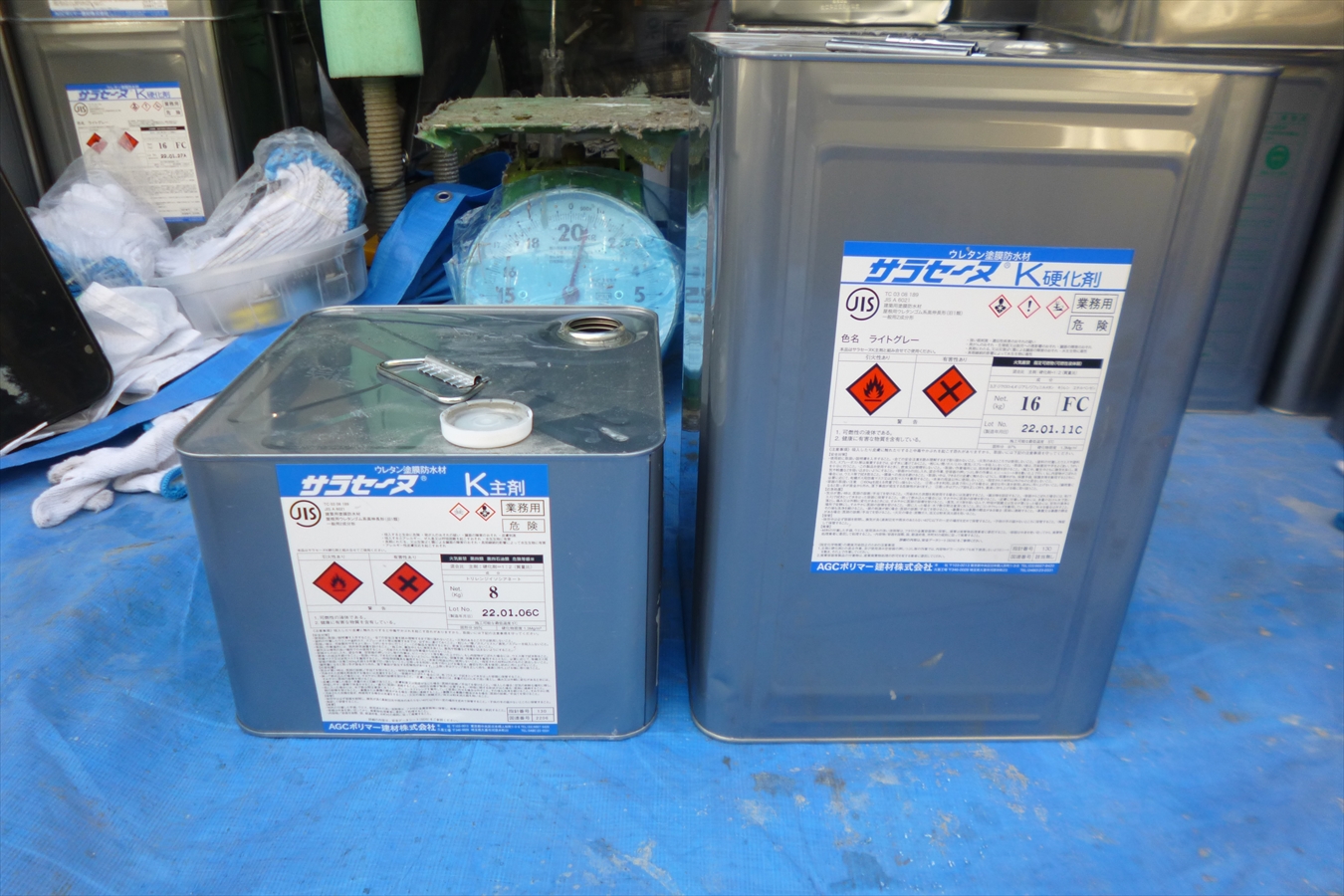
トップライト周り・プライマー塗布
枠にプライマーを塗っていきます。細かい面が多いので刷毛を使い塗っています。ローラーなら幅があるので一気に塗れて楽なのは確かですが、その反面塗りたくない場所を塗ってしまったり、周囲を汚しやすいというデメリットもあります。今回それに当たるのは枠の内側です。
内側は養生をしているものの、直接建物内部へ直結している箇所となっています。出来上がった枠は、上の開口部は勿論、下の箇所の土間の近接部は隙間があるため、ローラーを転がしてしまうと枠の下の隙間からプライマーが浸透し、建物内部まで入ってしまう可能性がありました。そのような危険を避けるため、今回はローラーを一切使わず刷毛のみで仕上げました。
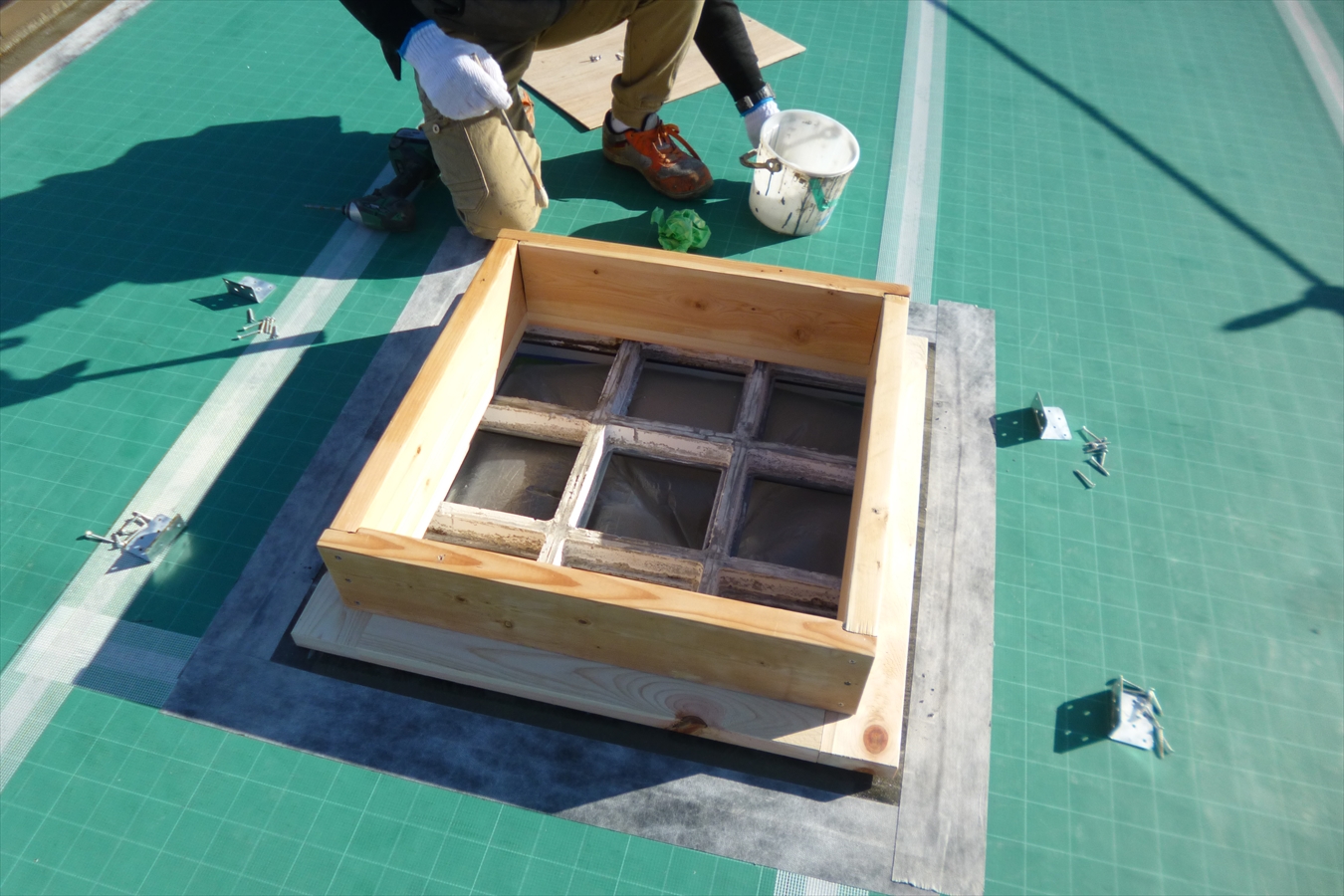
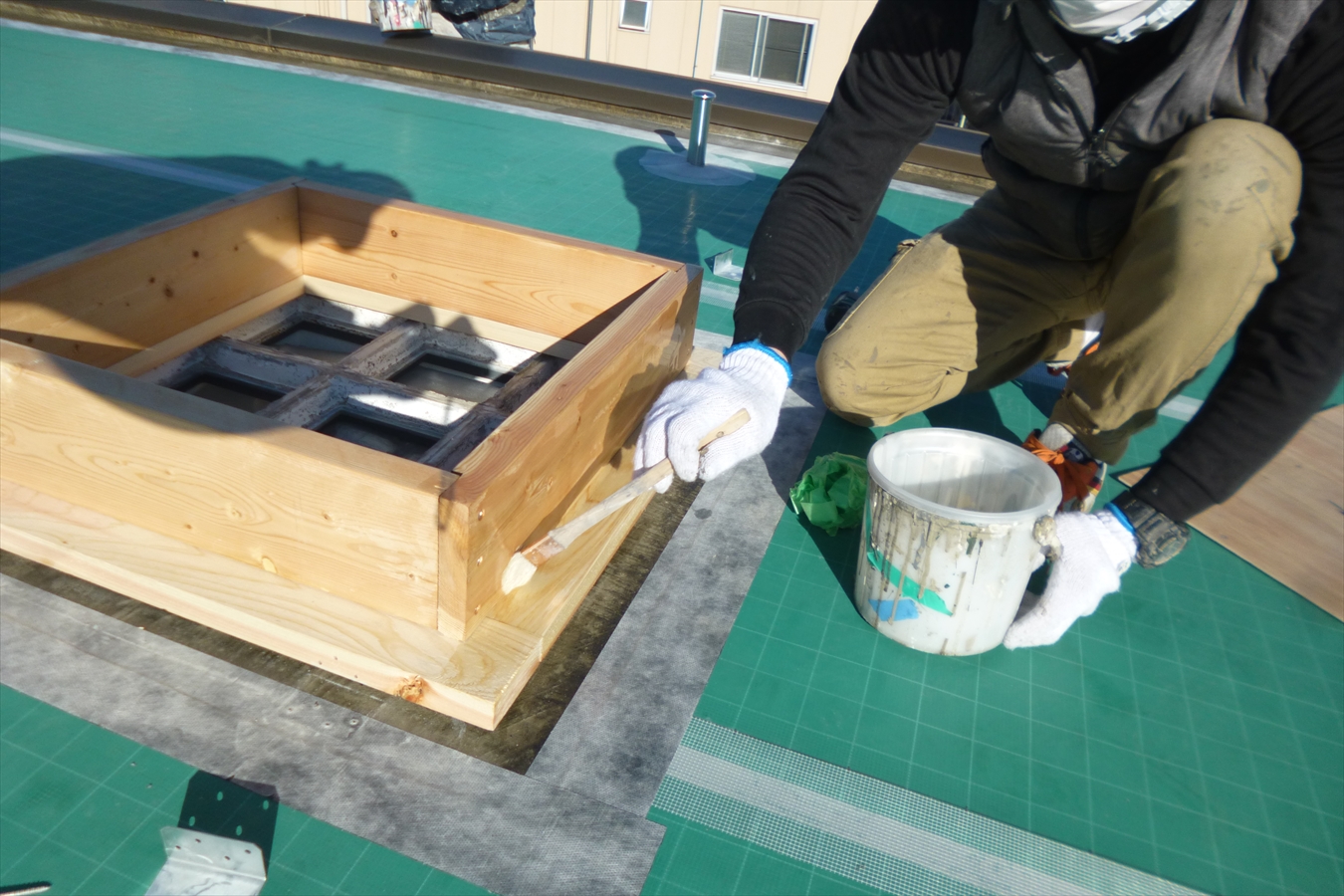
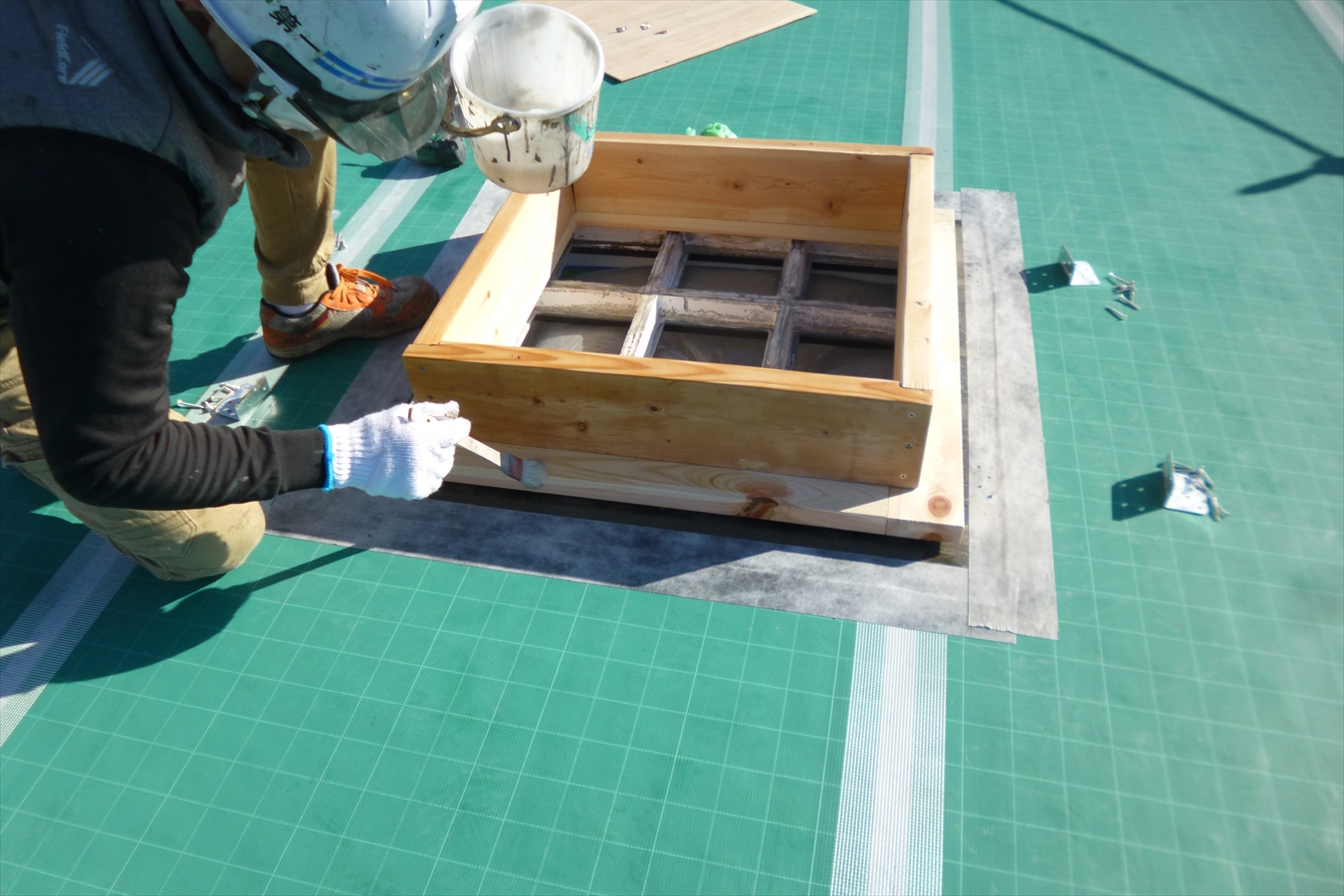
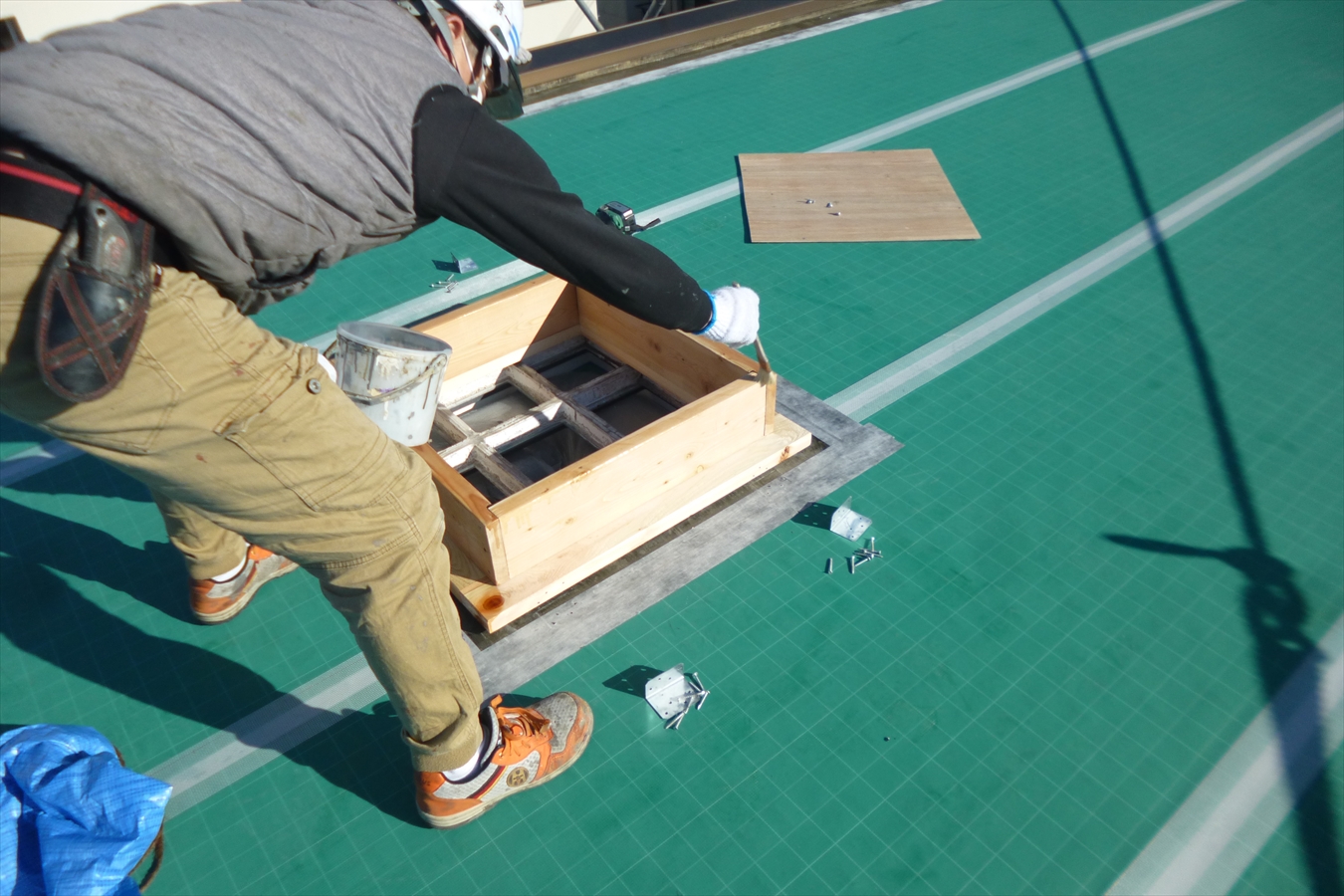
トップライト周りシール
プライマーを塗ったら、枠の下に隙間があるのでシール材で埋めておきます。トップライトの枠そのものには防水性はありません。そのためいくら枠で覆ったと言っても、枠と土間に隙間がある限り、そこから雨漏りすることを避けることはできません。
そのためこの箇所へのシールは必須となります。また、元々雨漏りの原因の疑いのあったトップライト周りにもシールと、枠のシールとで、シール防水の2段構えとなり、より防水性を高めるという効果も狙っています。
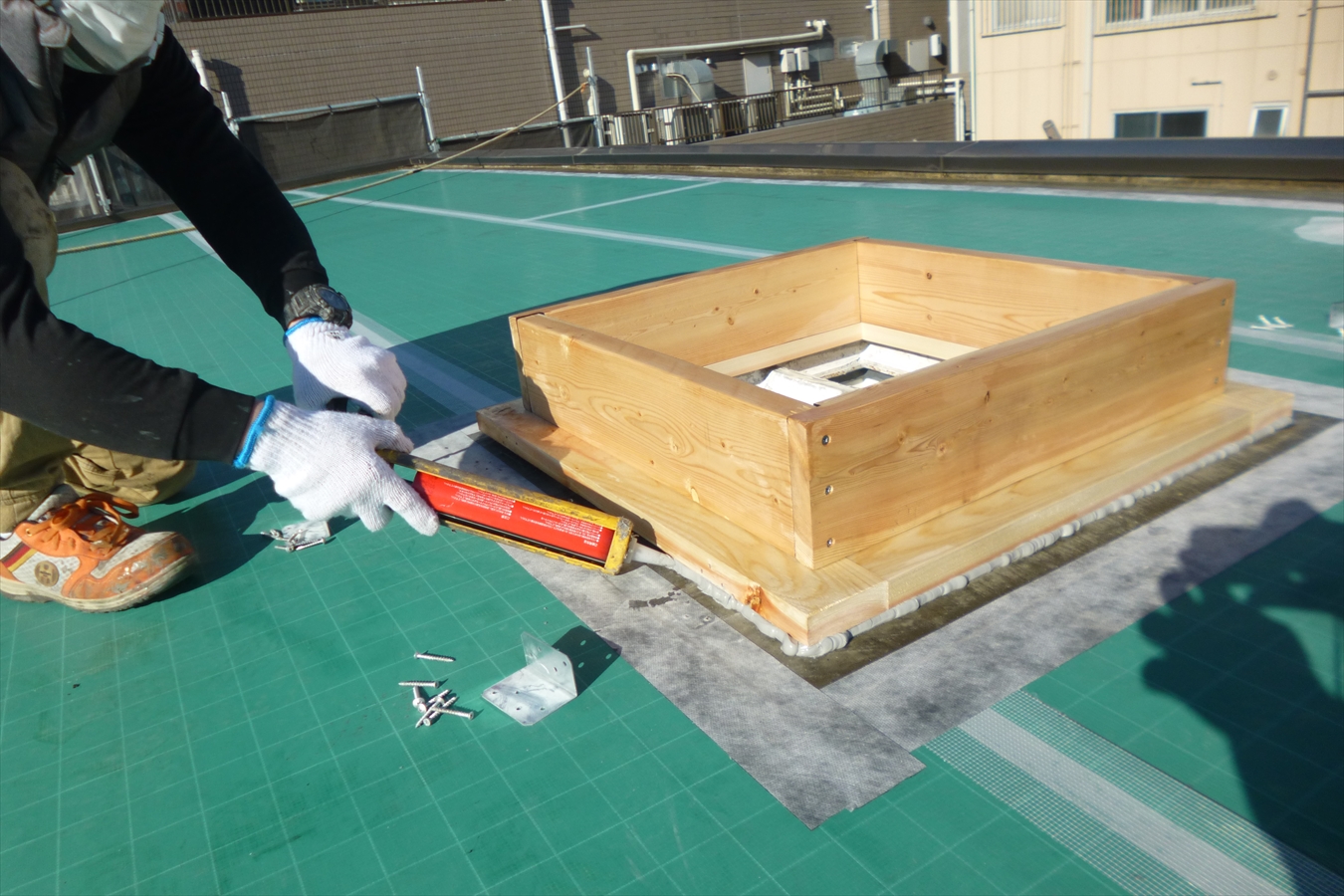
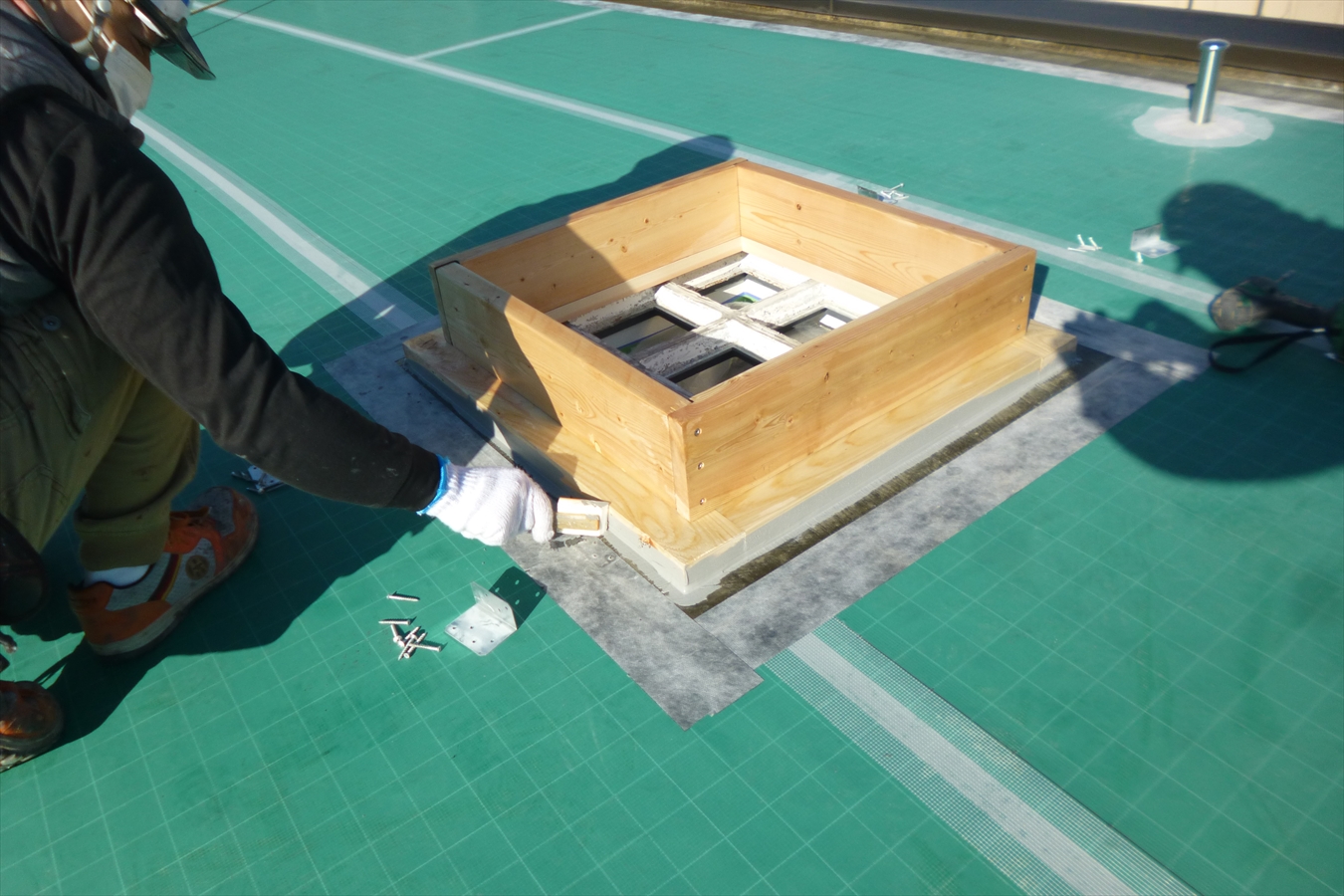
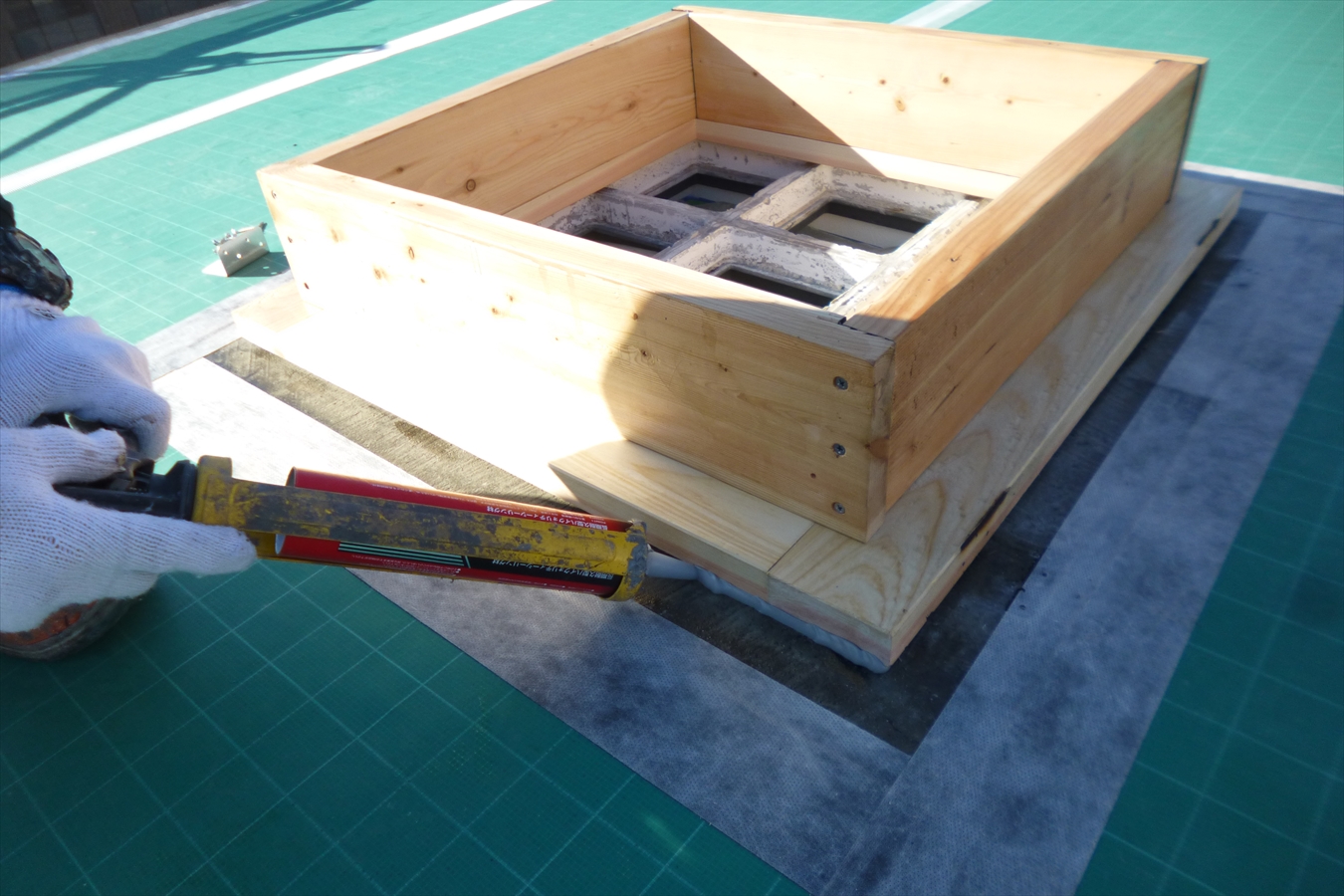
役物・メッシュクロス貼り
施工前
トップライトの枠下のシールも打ち込んだところで、本格的なウレタン防水の施工となります。ウレタンを塗布するだけでは強度に問題があるので、まずはその補強のためにもメッシュクロスを貼り付けていきます。この作業がウレタン防水で一番手間と時間のかかる作業かもしれません。メッシュクロスを入れる前のトップライトの枠です。これからここにクロスを入れていきます。
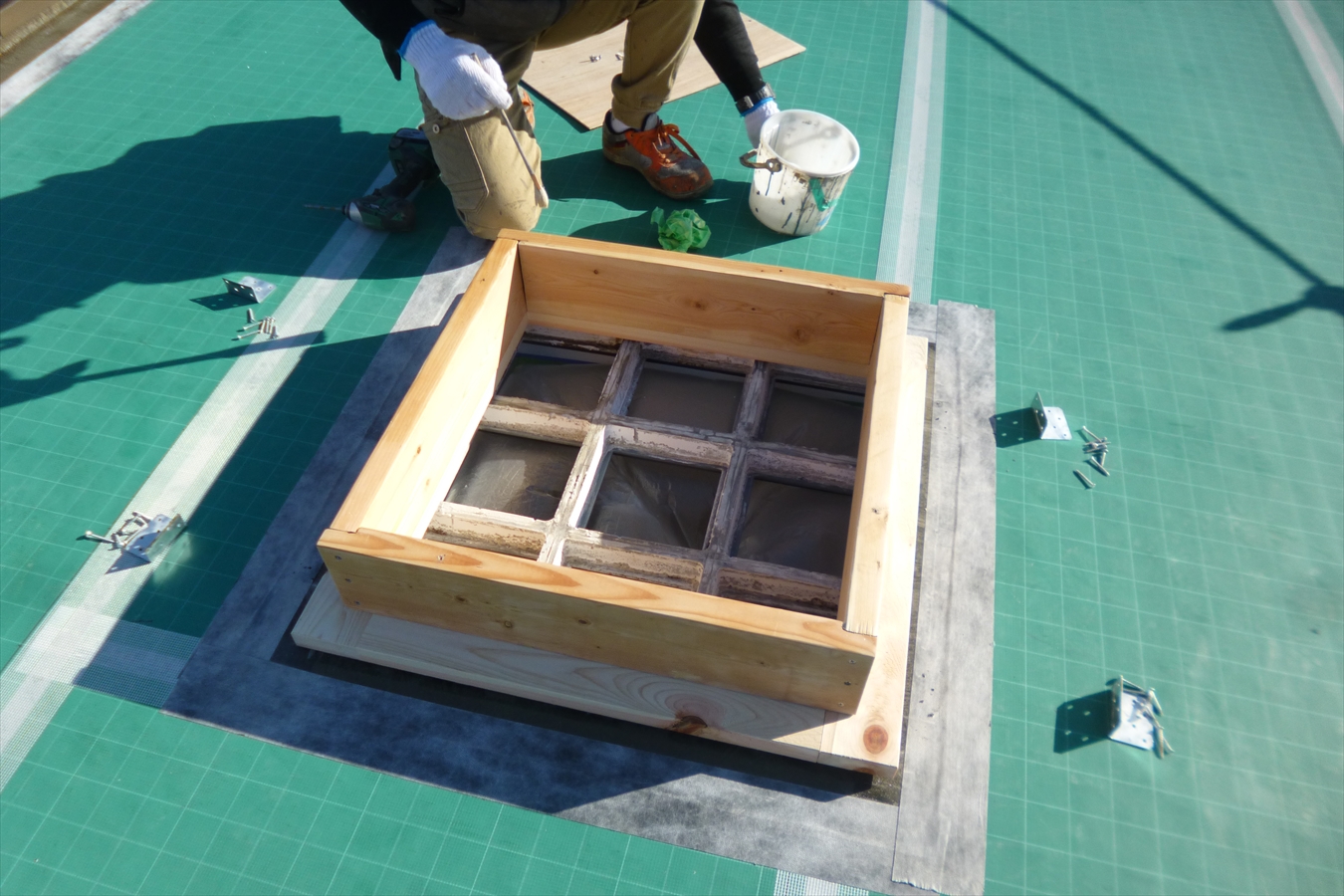
立ち下がりウレタン塗布
メッシュクロスは本来、ウレタンとウレタンの間にあるのが正しいものです。近年ではこのメッシュクロスそのものに糊がつけられたものが売られるようになり、メッシュクロスを直接躯体に貼り付けてウレタンで押える、というやり方もできるようになりましたが、今回は従来通りのやり方でクロスを貼り付けていきます。
ウレタンとウレタンの間に貼り付ける、必要があるので、まずはウレタンを塗布していきます。本来なら枠全体にウレタンを塗っておきたいところですが、枠そのものに角が多いため、角の少ない上部と、角の多い下部に分けて作業します。まずは上部にウレタンを塗っていきます。
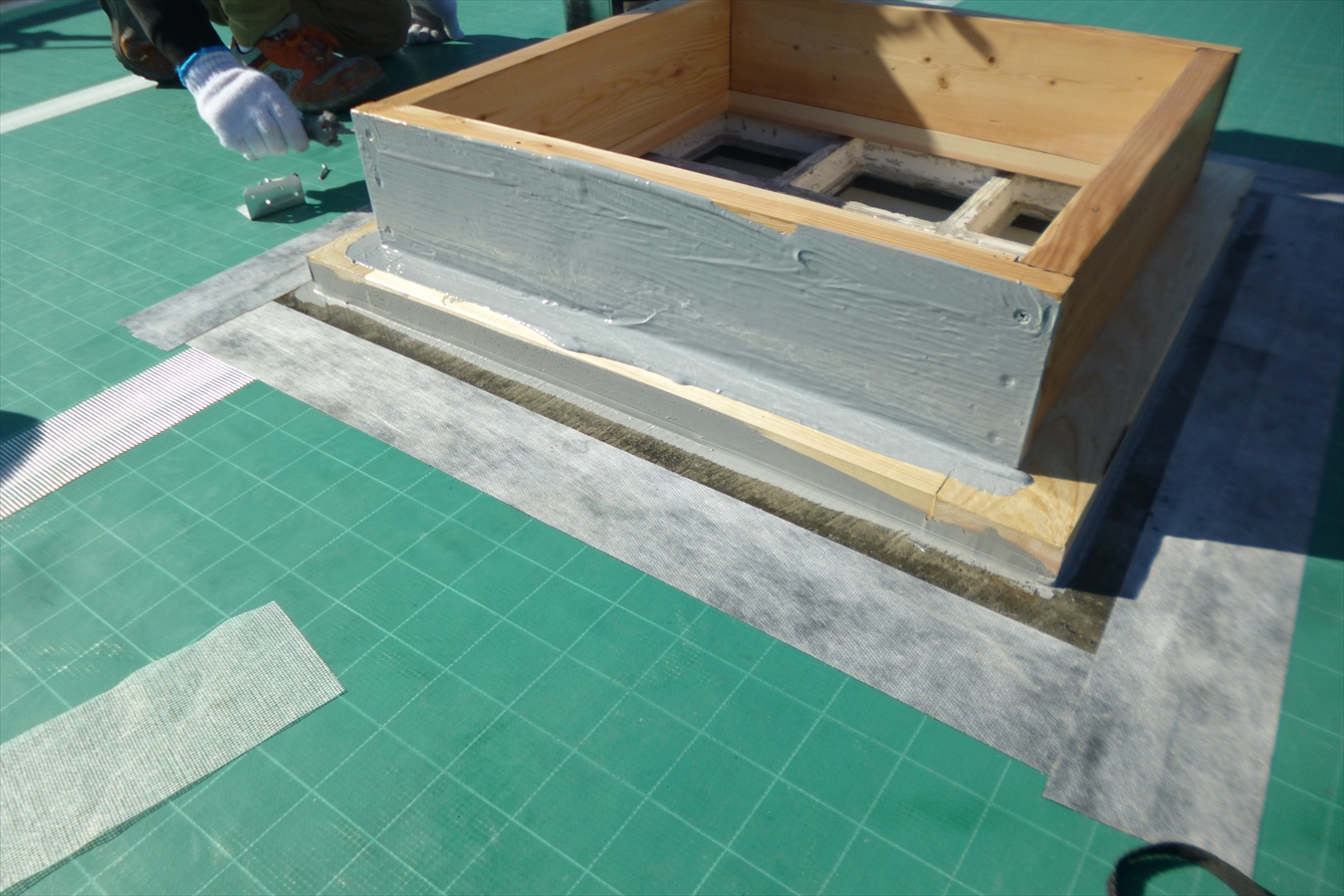
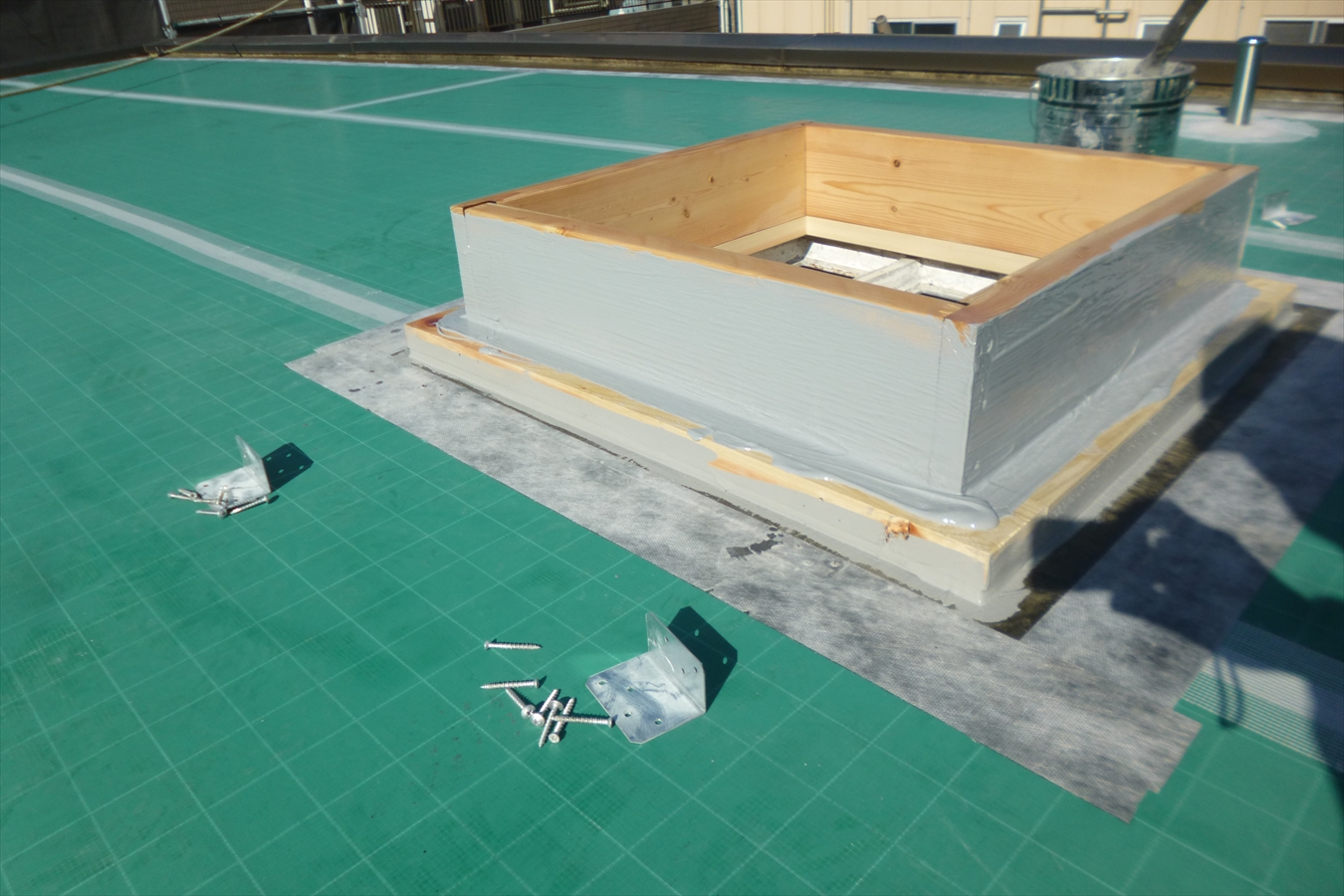
役物上部 立下り メッシュクロス貼り付け
役物の上部4面にウレタンを塗ったら、ウレタンが硬化する前にメッシュクロスを貼り付けていきます。ゴムベラを使いクロスを貼り付け、最後にウレタンを均すように撫でてクロスを押えています。
メッシュクロスも通気緩衝のQVシート同様、最初は1m幅くらいの巻物になっています。そのため実際にクロスを使う時は、この巻物そのものからクロスを入れる場所に合わせて、必要な幅の巻物になるように切断しています。
この現場でクロスを入れる必要がある箇所は、トップライトの枠とQVシートの端末箇所のみです。どちらも幅10cm程の幅があれば十分なため、幅10cm程度のクロスの巻物を切断し用意しました。
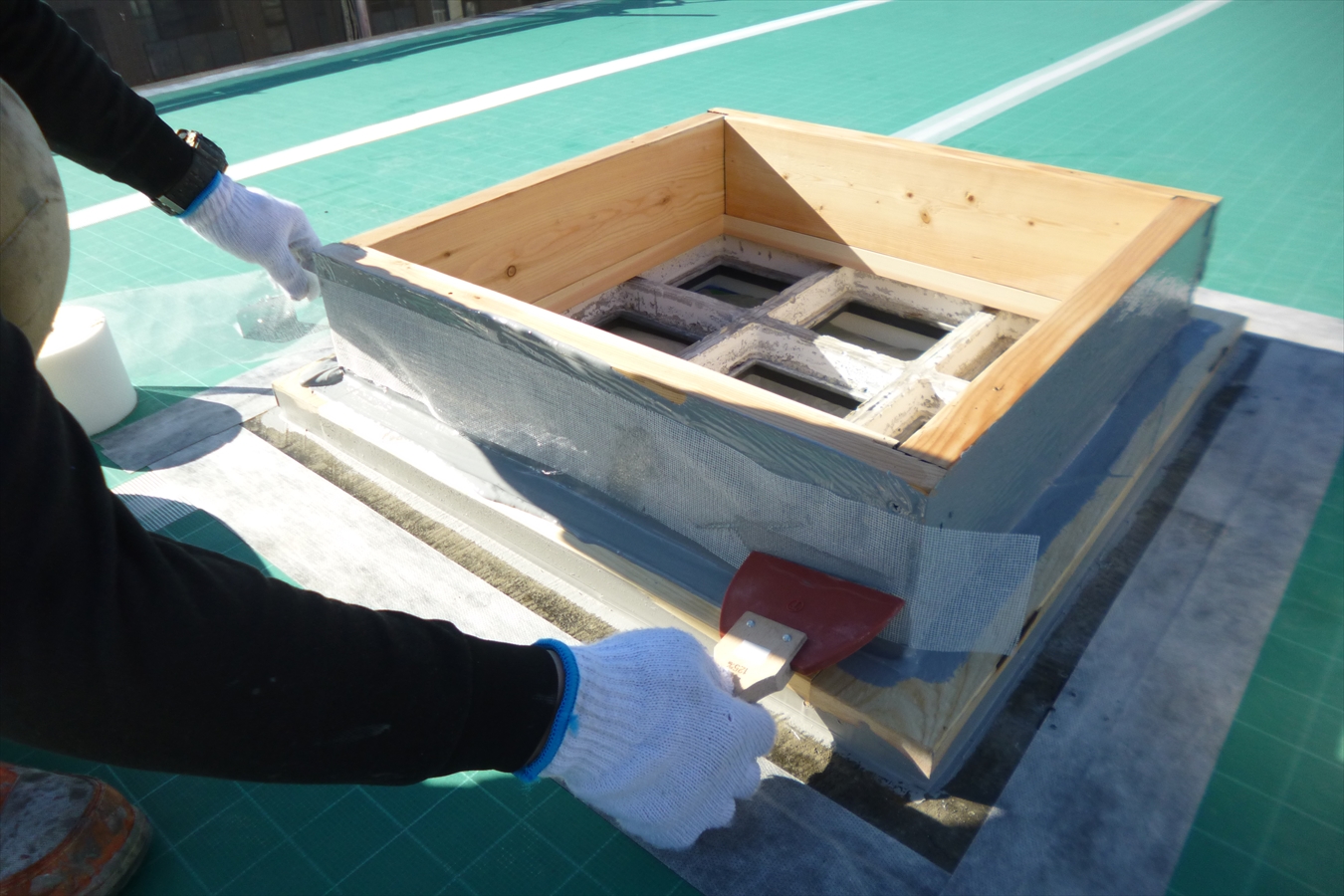
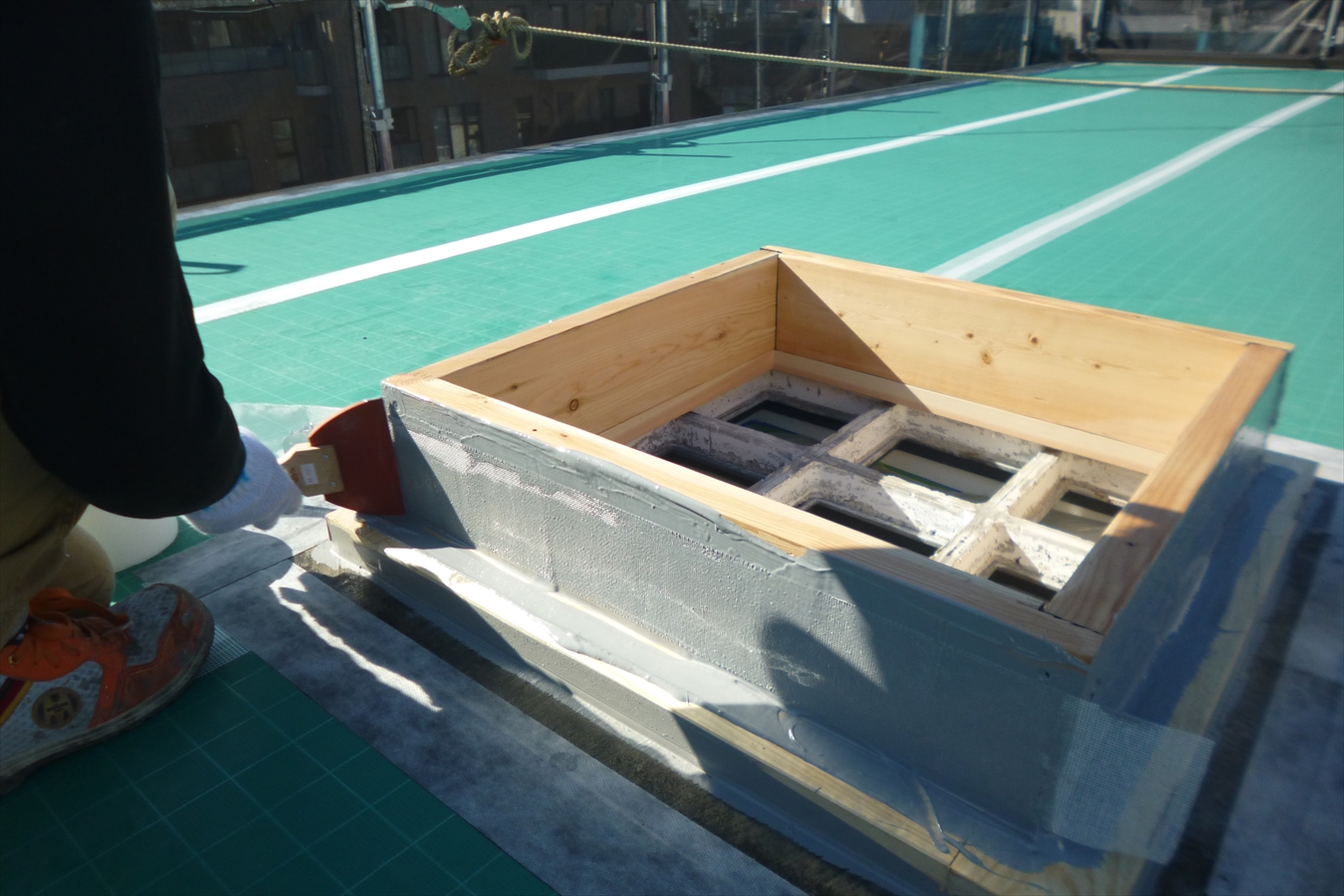
役物上部 立下り クロス貼り詳細
この枠の場合だと、クロスをぐるりと一周させるようにして貼り付ければ良いのですが、丁度一周した箇所はクロス同士が5cmほど重なり合うようにしておく必要があります。今回はクロスを貼る時、枠に合わせて貼るようにするのではなく、ワザと枠からクロスを5cmほどはみ出させて貼りました。クロスを1週させた後で、最後にこのはみ出させたクロスを被せるように貼り付けています。
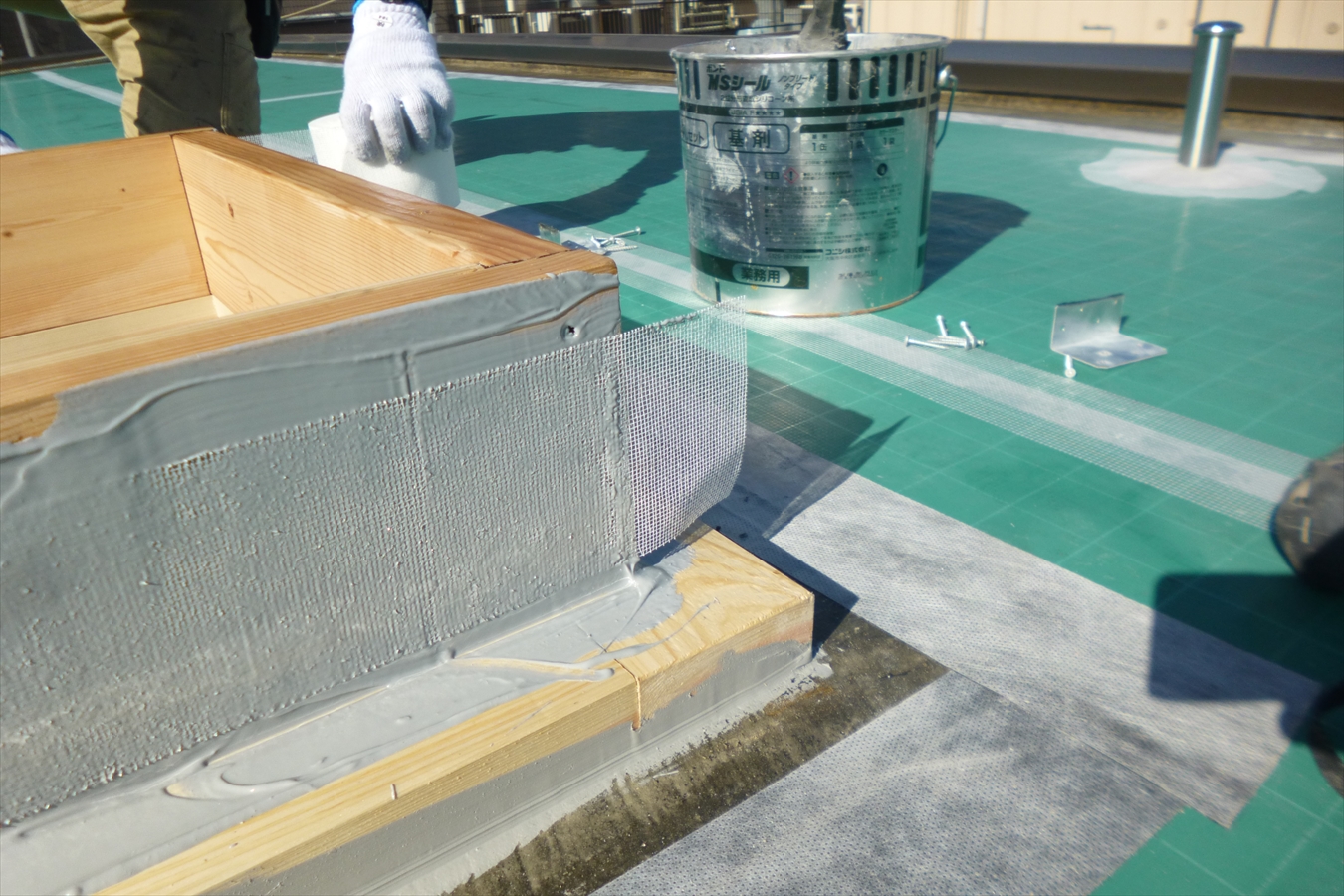

役物上部 立下り 施工後
トップライトの上部箇所、4面にメッシュクロスを貼った後の写真です。ウレタンは単に塗ってあればいいというものではなく、ある程度の厚みが必要です。その目安の一つとなるのがメッシュクロスを貼り付けた時、クロスの目がウレタンで塗りつぶされていることです。それだけの量のウレタンが塗布されていれば、その時点で一定の厚みは確保できているということですね。
クロスそのものが見えなくなるような量でなくて問題ありません。この後、更にウレタンを2回に分けて重ね塗りすることになるので、写真に写っているくらいの量のウレタンが塗布されていれば十分です。
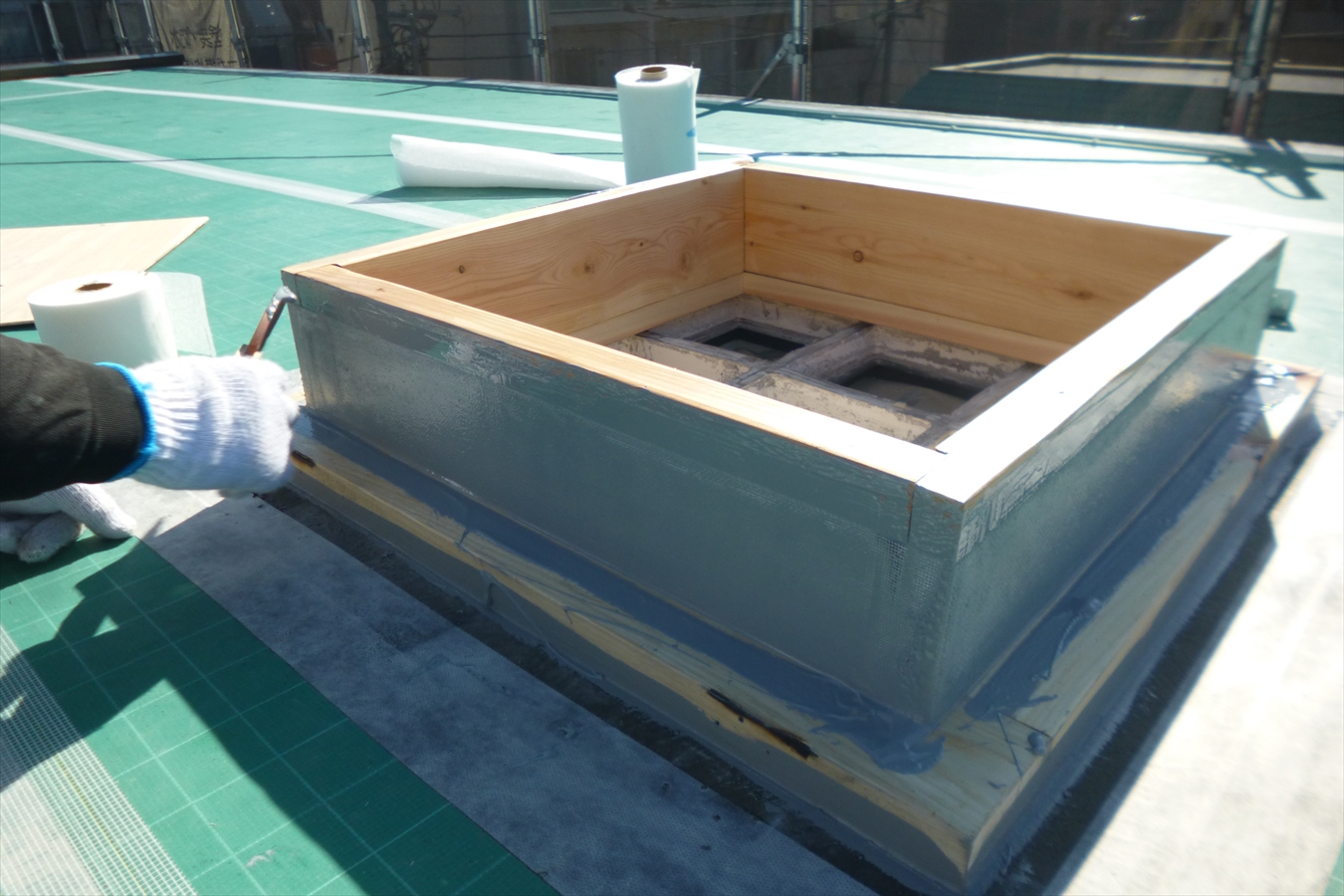
役物下部 メッシュクロス裁断
トップライトの枠上部のクロス貼り付けが終わったら今度は下半分の箇所のクロス貼りです。クロスの貼り付けはウレタンを塗布し、硬化する前に貼り付ける必要があります。ウレタンは時間経過と共に硬化していくもの。
つまり時間勝負となるわけです。なので、ウレタン塗布した後の作業時間を確保するため、クロスをその度にカットするのではなく、予め用意してから作業を始めていきます。
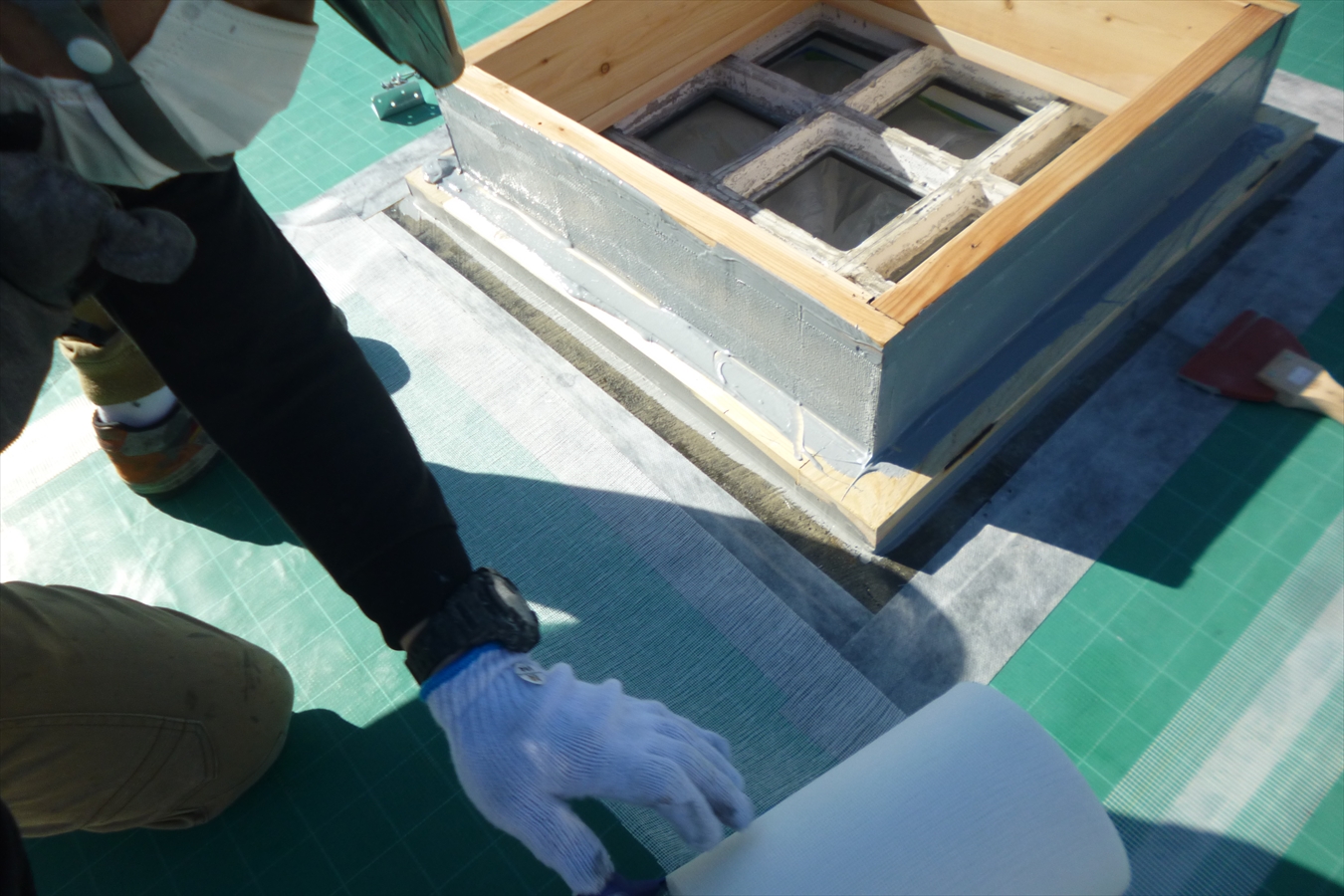
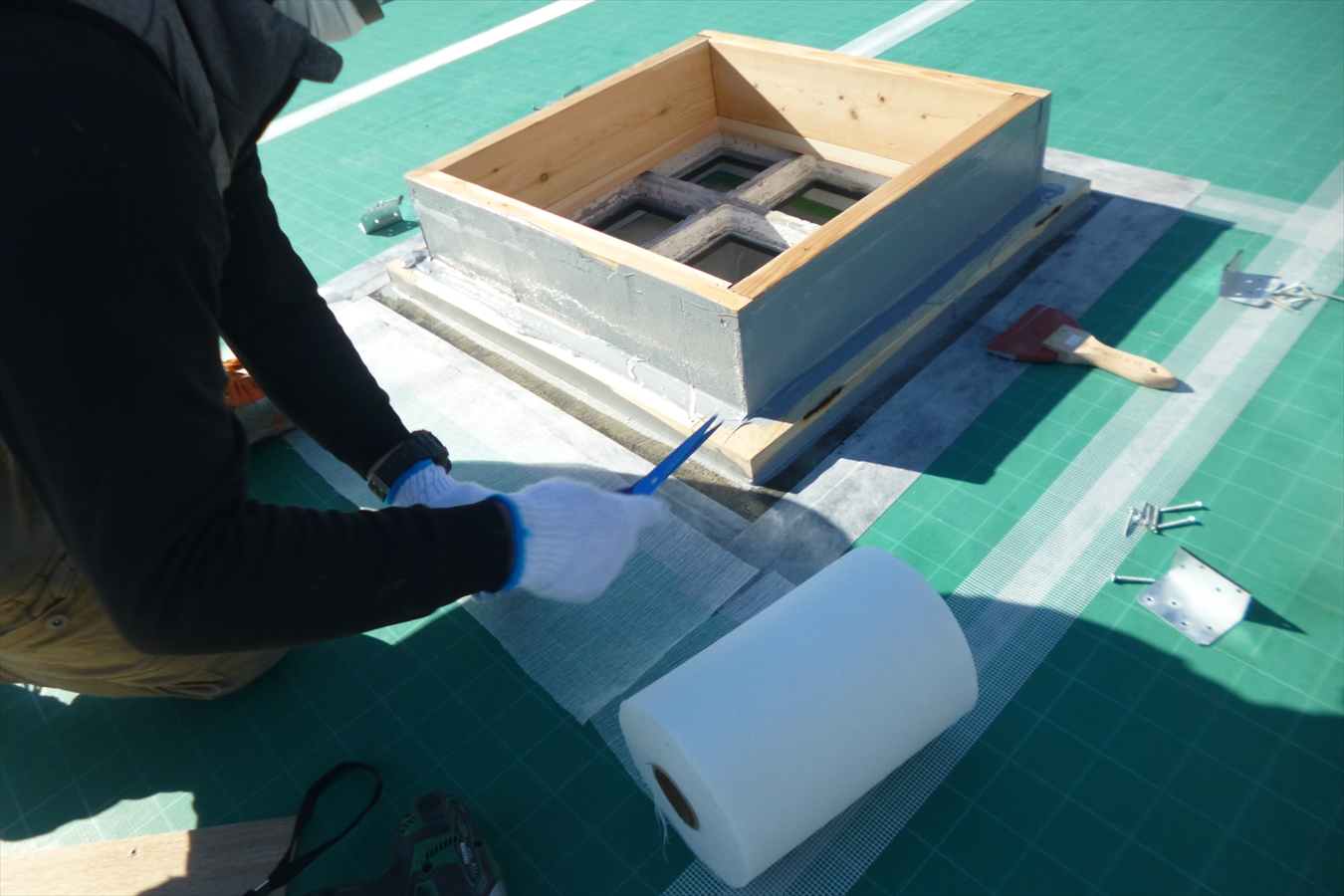
写真はクロスの寸法を計ってカットしているところです。本来ならスケールなどを使いカットしていくのが普通ですが、小さな役物なので直接役物に合わせて必要な寸法にしてカットしています。4面分のクロスをカットしたら施工していきます。
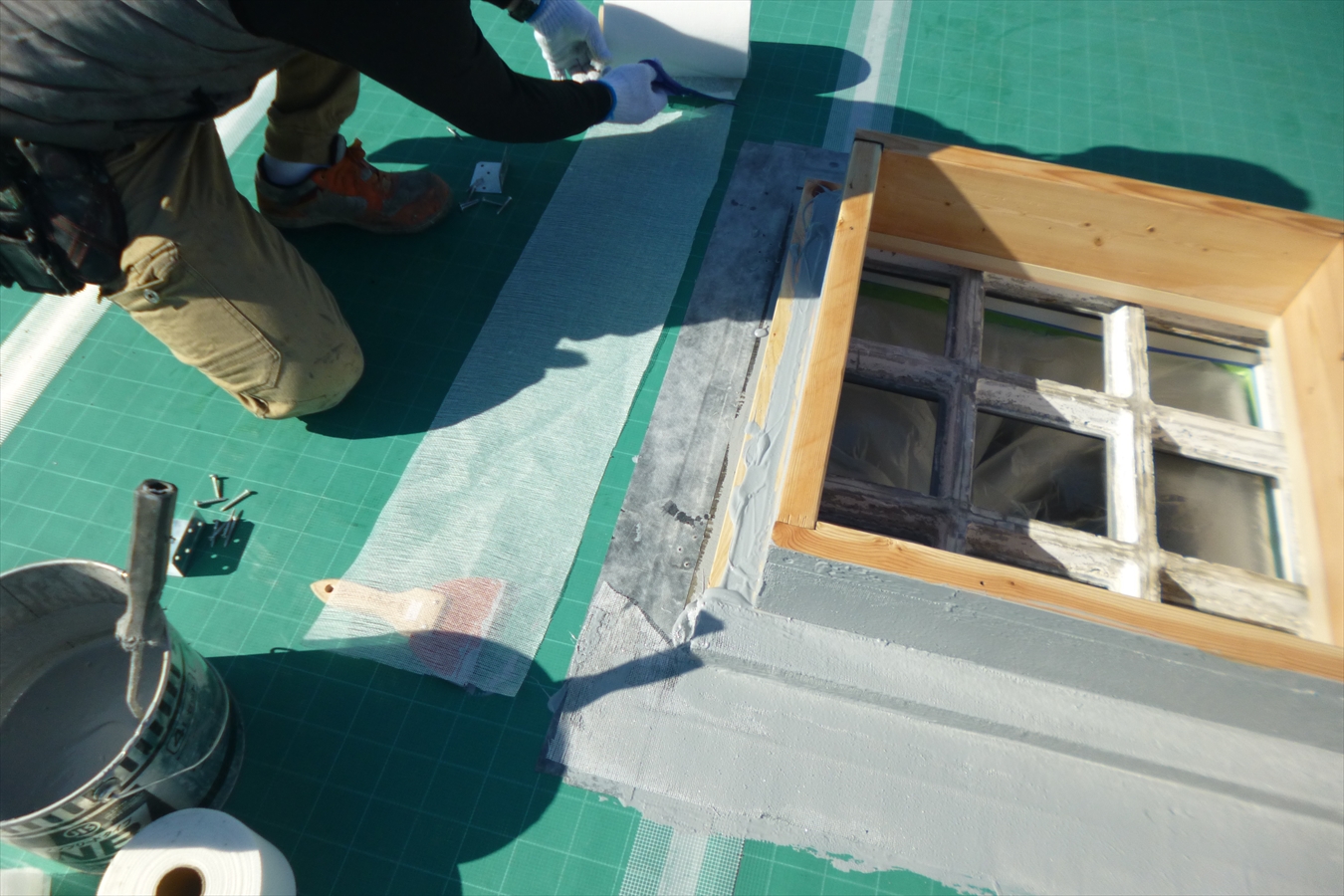
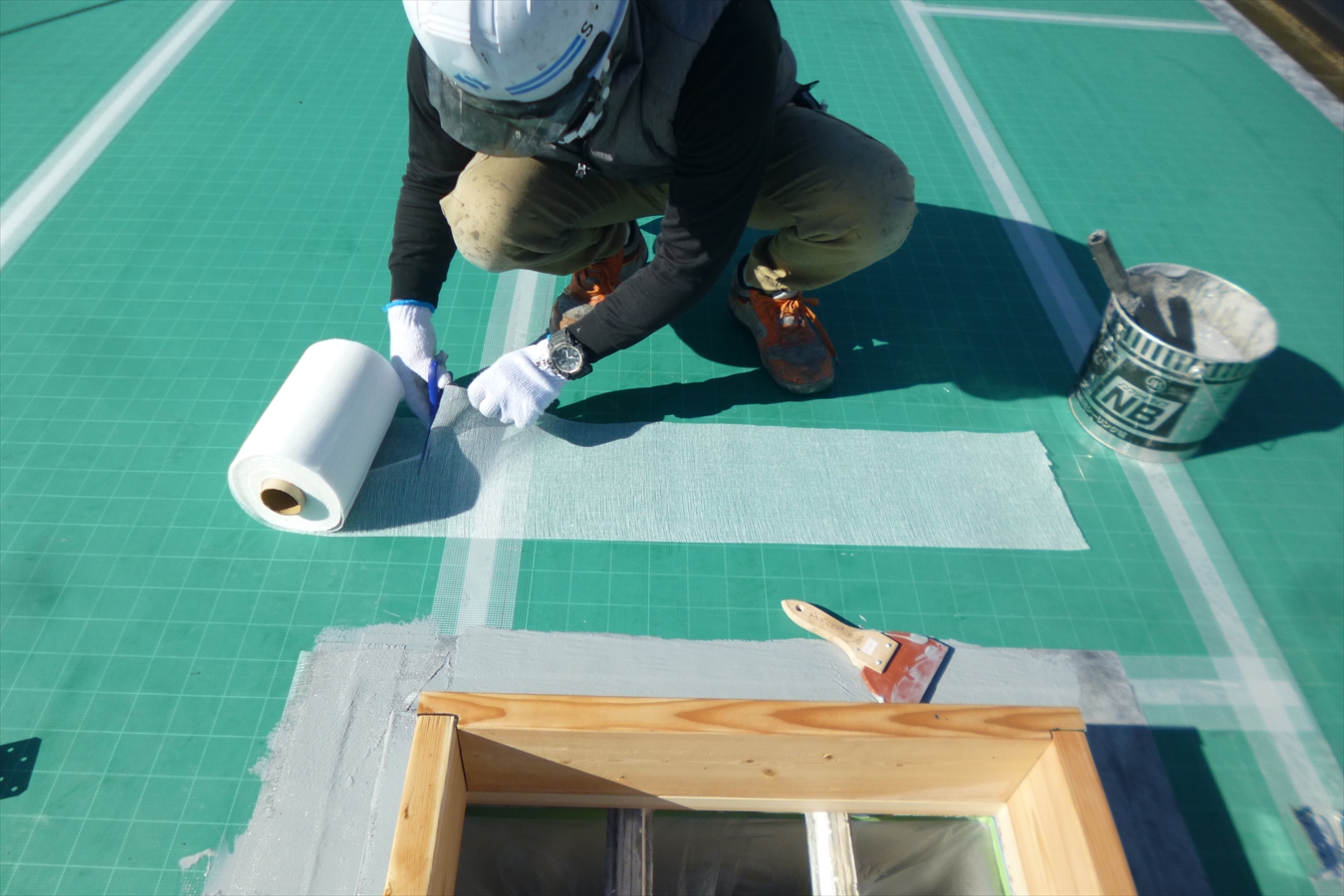
役物下部 メッシュクロス貼り
クロスの用意ができたら実際に役物へ貼り付けていきます。まずは平坦なところから、上から順番にクロスを貼り付けていきます。この時まとめて一気に貼るのではなく、1面ずつ貼り付けるのがポイントです。1面ずつ貼るようにしないと、入隅の箇所を押える時にクロスが動いてしまいズレてヨレてしまうからです。
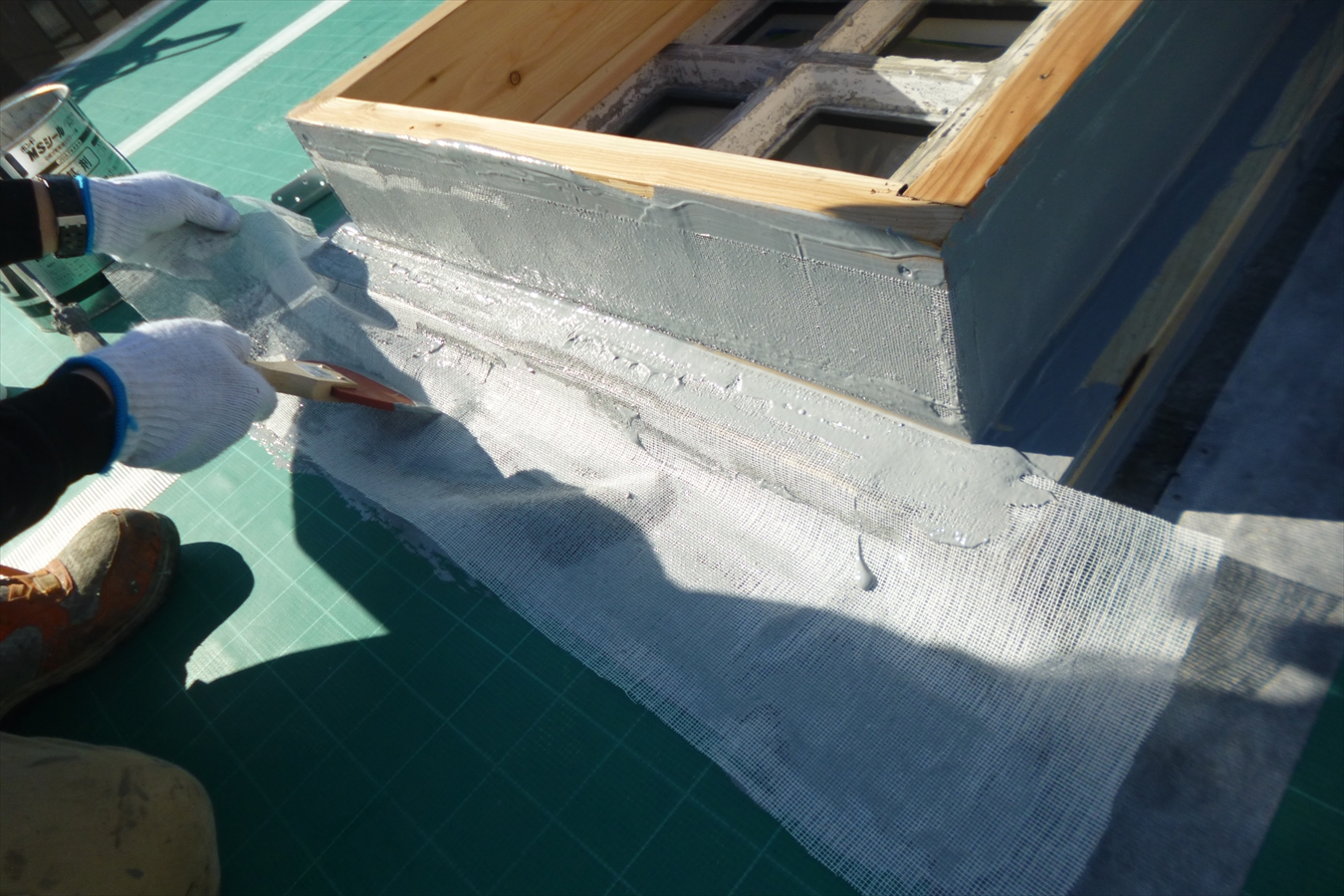
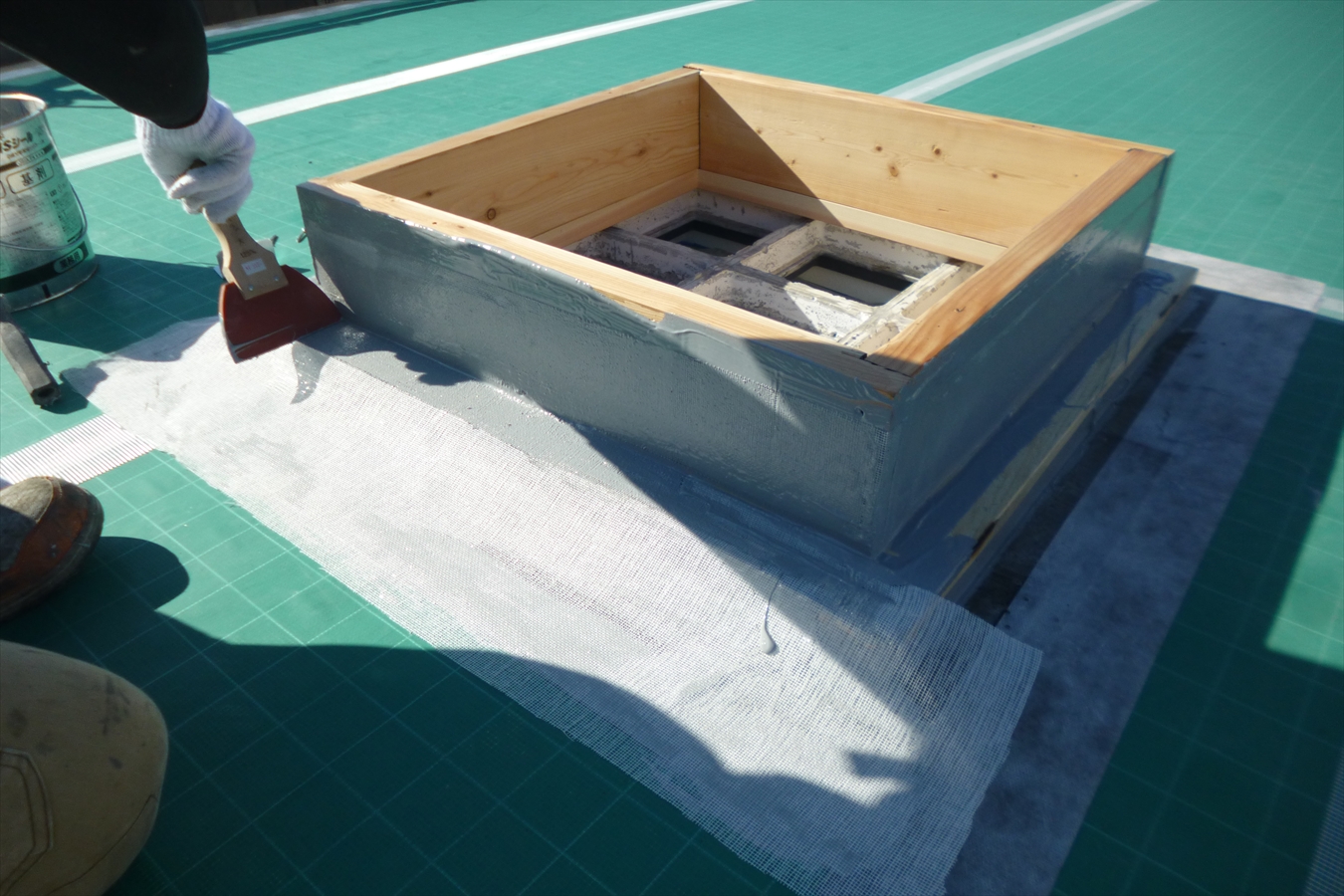
そしてこの時、写真のように両端は貼り付けないように浮かした状態にしておくことが大切です。ここも貼り付けてしまうとヨレるだけでなくクロス自体がグチャグチャになってしまう可能性が高くなってしまいます。
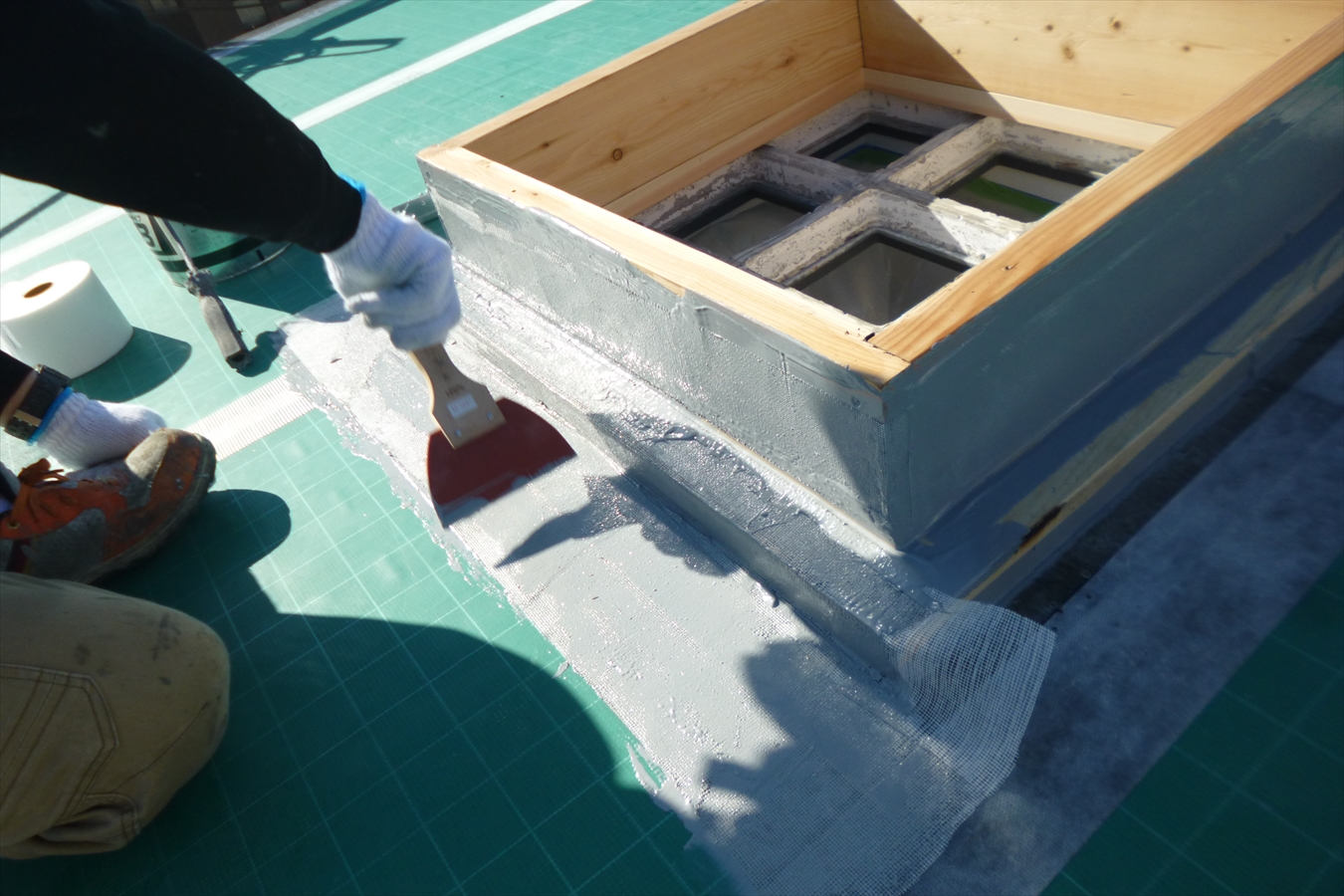
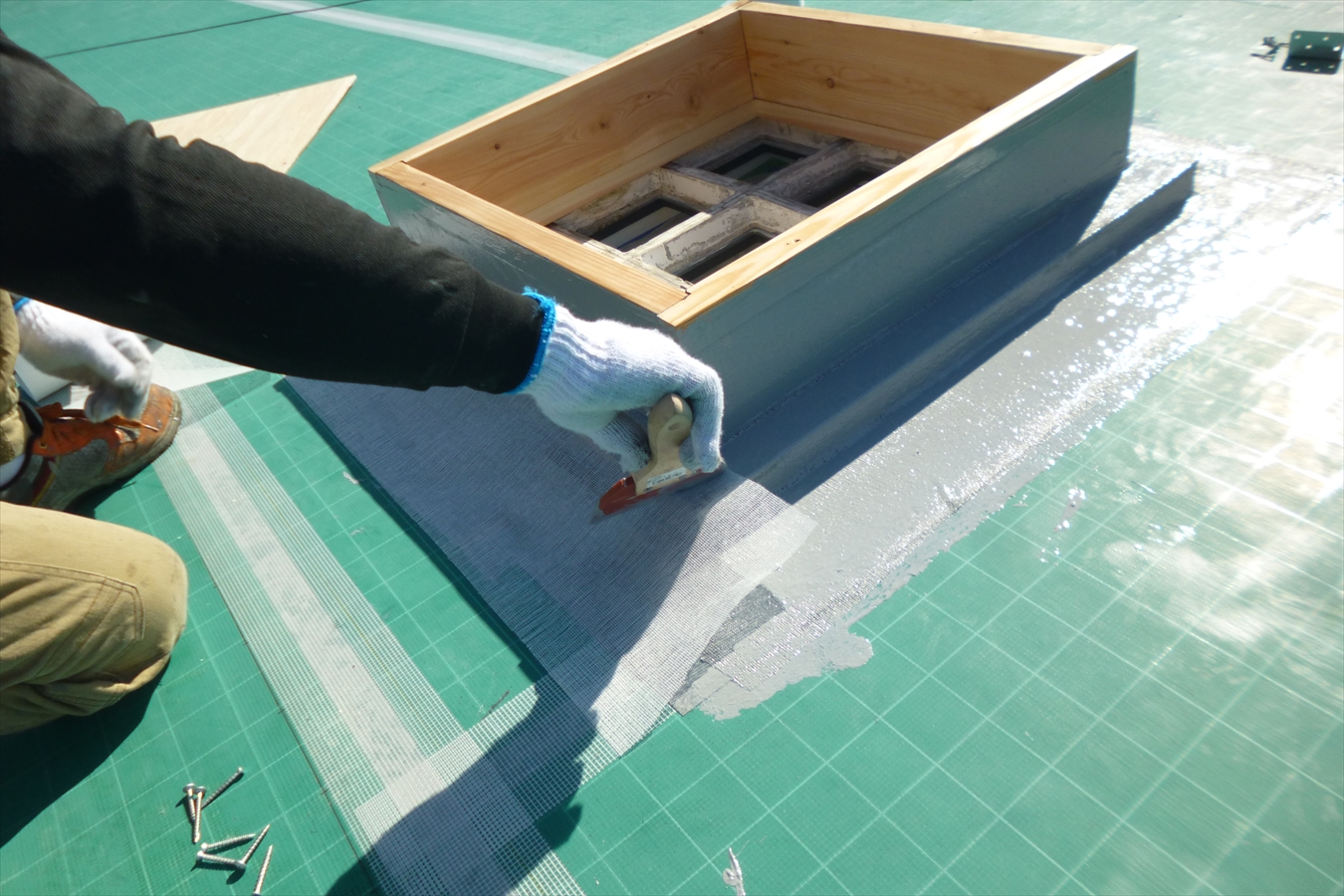
メッシュクロス 加工
角に貼り付けるメッシュクロスの加工をしていきます。ここがクロス貼りで一番難しいところです。ある程度慣れてしまえばどうということのない作業ですが、慣れるまでが大変です。
クロスは折り曲げて貼り付けるということができない素材です。折り曲げても戻る力が非常に強く、ウレタンが硬化する前に戻ってしまうためハサミで切り込みを入れて貼り付ける必要があります。ここではその切り込みの説明をしていきます。
切り込みを入れて加工というと難しく感じますが、基本的には一か所、もしくは二か所切り込みを入れればキレイにクロスを貼ることができます。ただ問題なのは、どこに、どの角度で切り込みを入れるのか、という点になります。
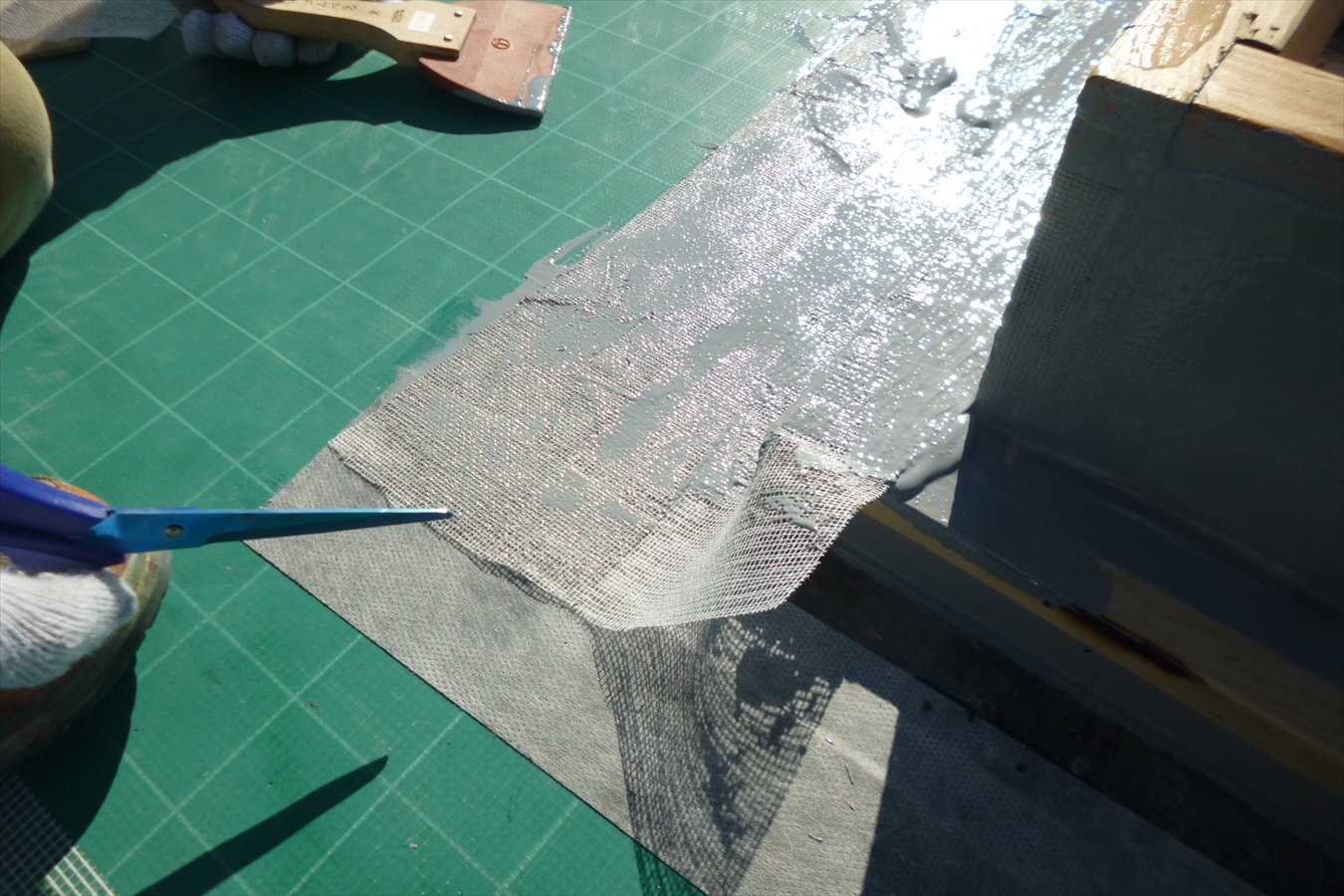
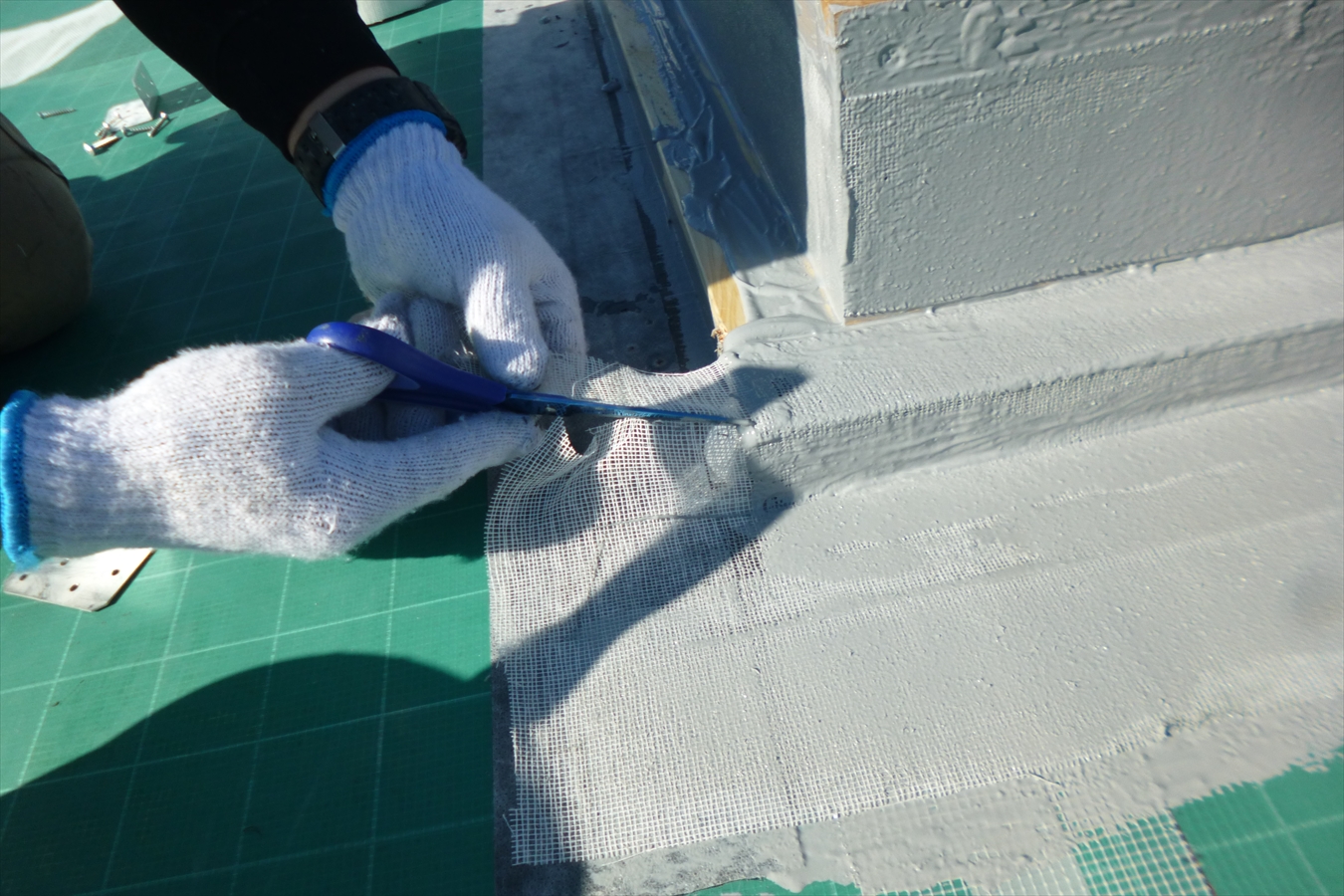
まだ貼り付けていない角の箇所に切り込みを入れます。切り込みを入れる前の写真です。
一つ目の切り込みはここにハサミを入れます。親指で押さえている方が後で上から被さるようになります。ハサミを入れた箇所から角へ向かってハサミを入れていきますが、この時切り込みの終わりの箇所と角を少しズラしておくことがポイントになります。
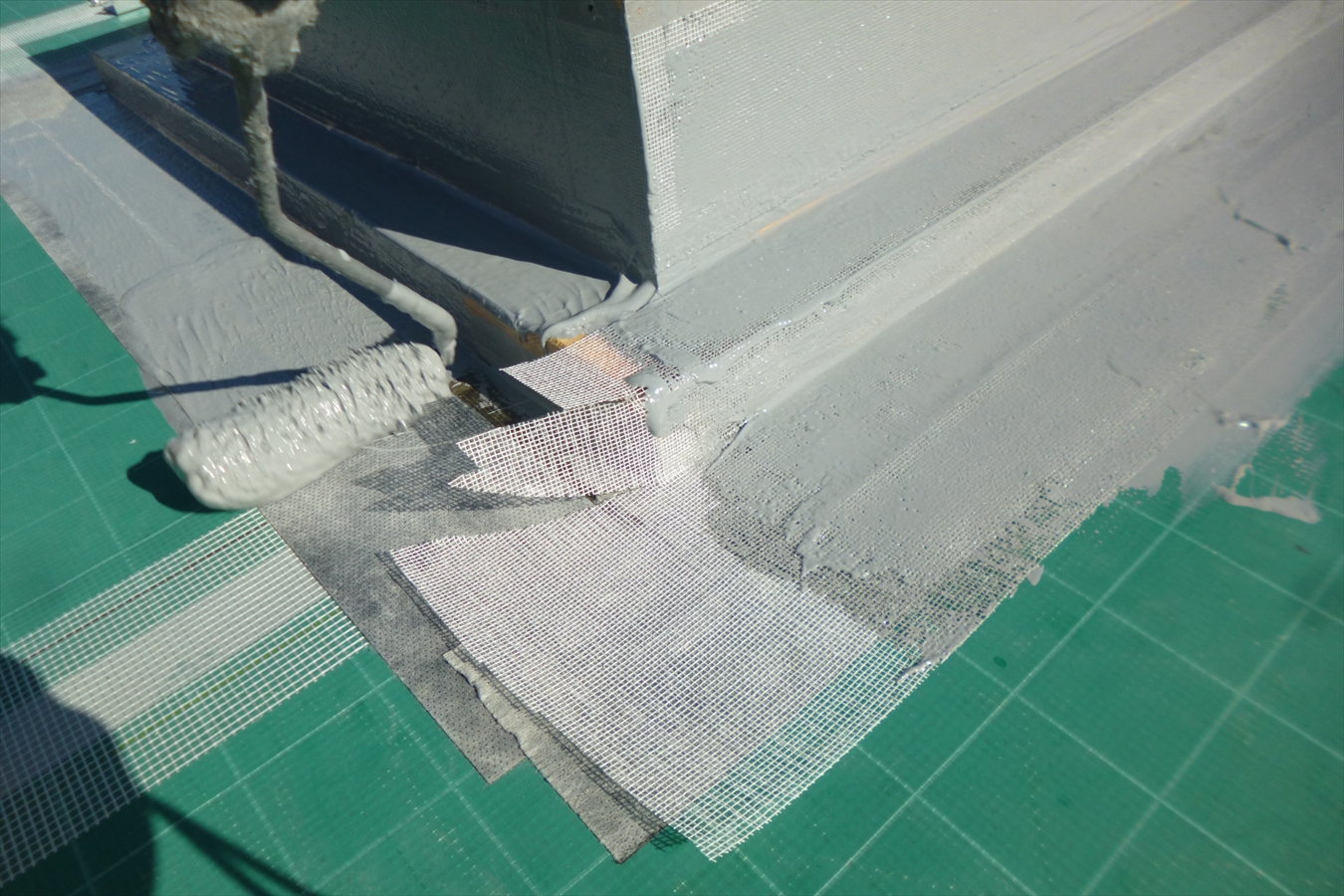
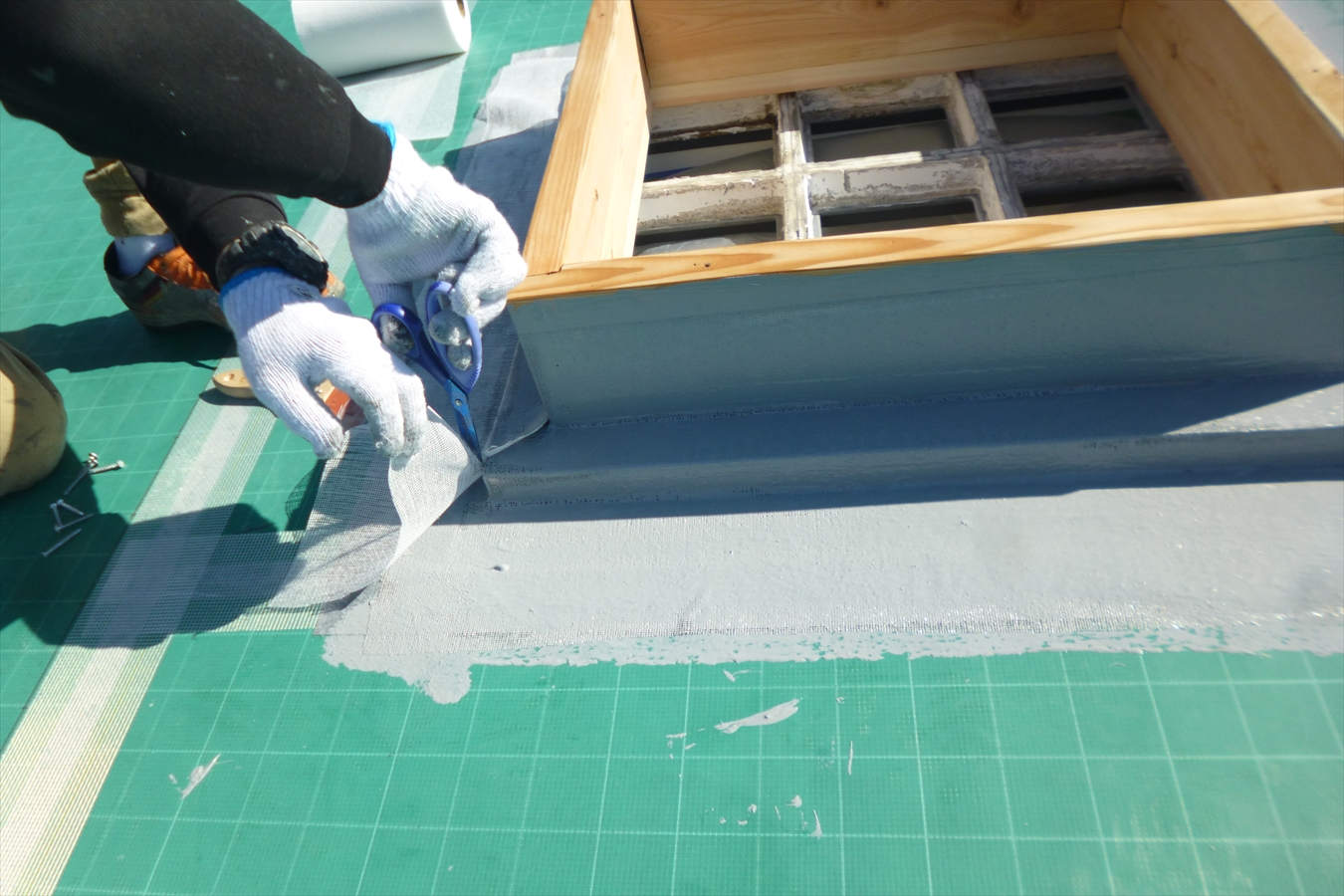
二つ目の切り込みは、最初の切り込みから少しズレた位置になります。土間の高さに合わせた位置での切り込みです。二か所切り込みを入れた状態のクロスの写真です。
切り込みを入れてクロスが三つに分かれている状態です。最初に貼り付けるのは真ん中のクロスからで、それを貼り付けた上から被せるように一番上のクロスを貼り付けます。同じ要領で角の箇所には切り込みを入れて仕上げていきます。
メッシュクロス 押さえ
加工したメッシュクロスをゴムベラで押えていきます。クロスはほつれやすいものなので、力を入れすぎないように気を付けながら押えていきます。
ハサミを入れて加工したところは特にほつれやすいため、注意が必要です。加工したところは、横から押えて上から被せるように仕上げていきます。これが逆になると押えたクロスが剥がれてしまいやすく、後で再度補修することになるので必ず横から仕上げるようにしています。
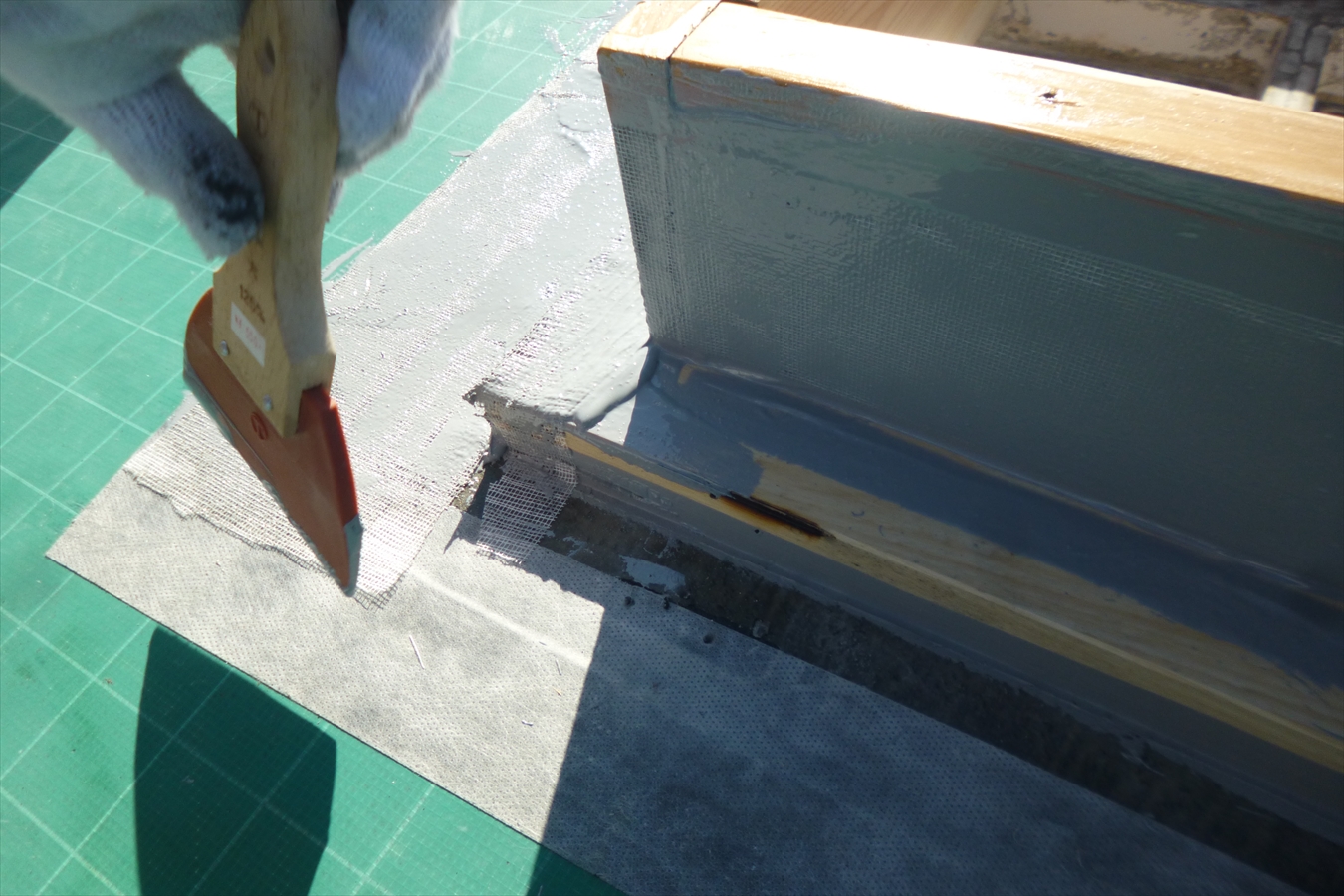
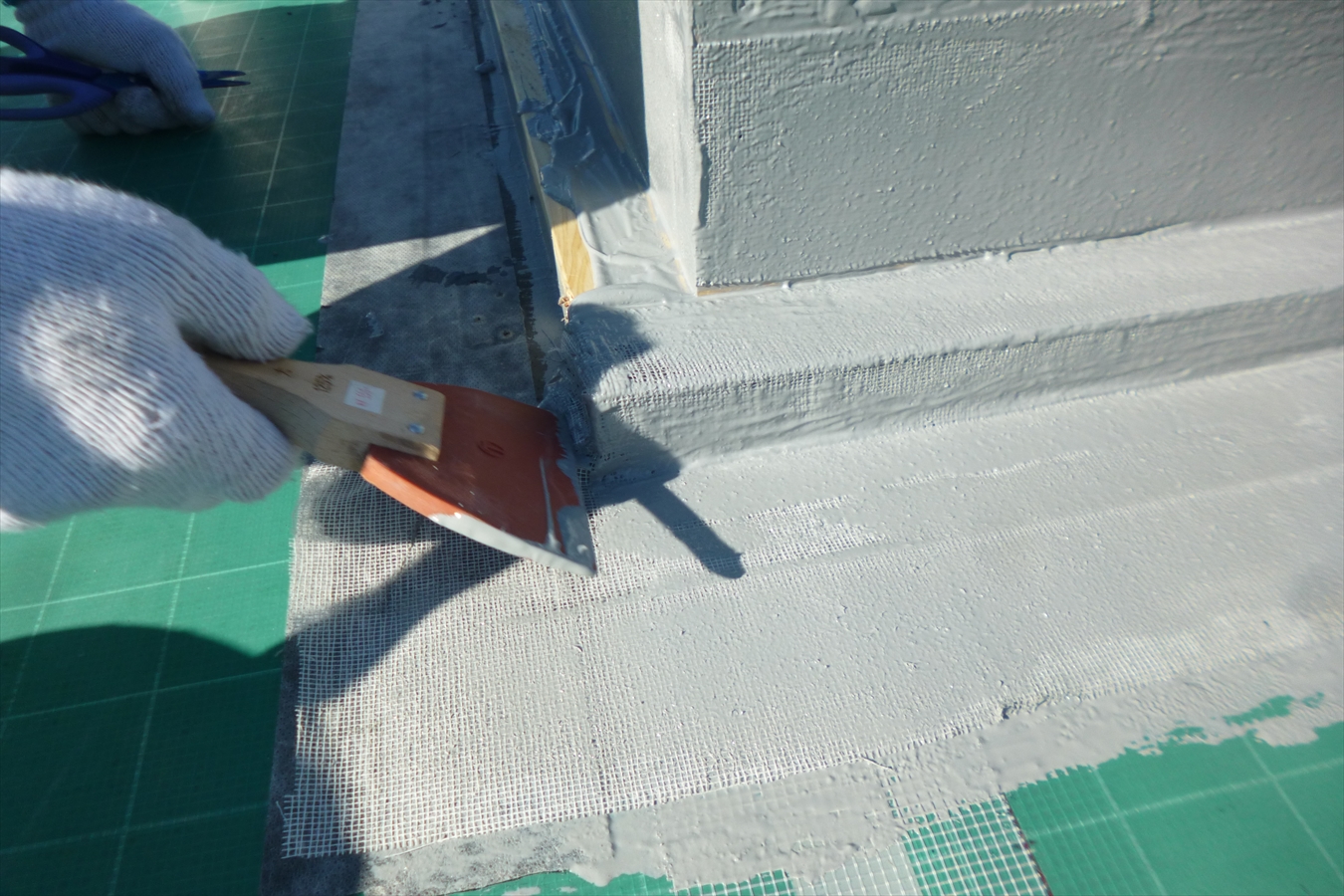
施工後
メッシュクロスの貼り付けが終わった後の写真です。慣れてない職人や、腕の悪い職人がクロスを入れた後のものだと、角の部分のクロスを上手く押えられずはねていたりするものですが、キレイに収まっていることが分かると思います。
ここまでだけでもかなりの手間と労力が費やされていますが、ここからがメインの工程となります。ウレタンを硬化させた後、厚みをつけるために更にウレタンを重ねていきます。
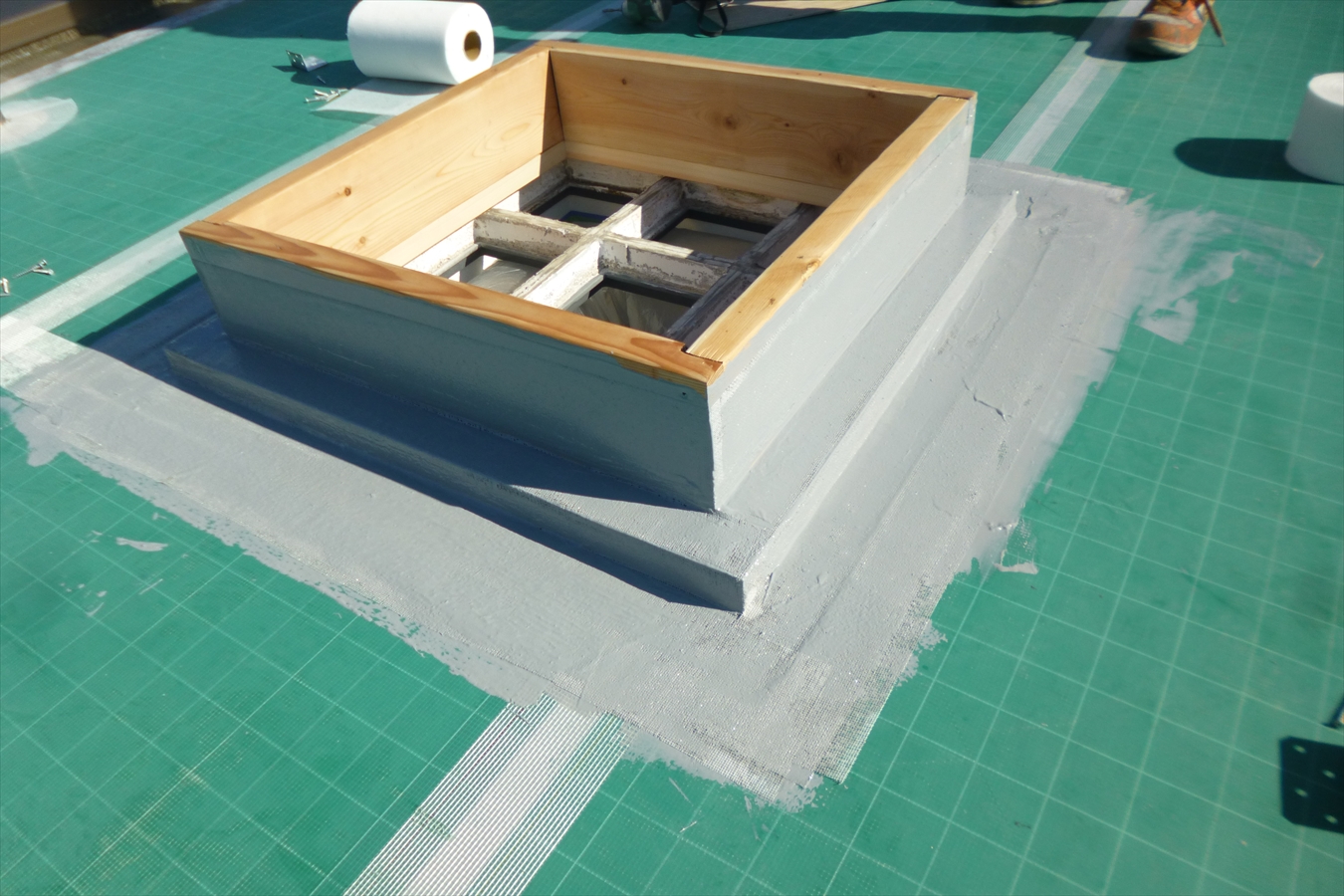
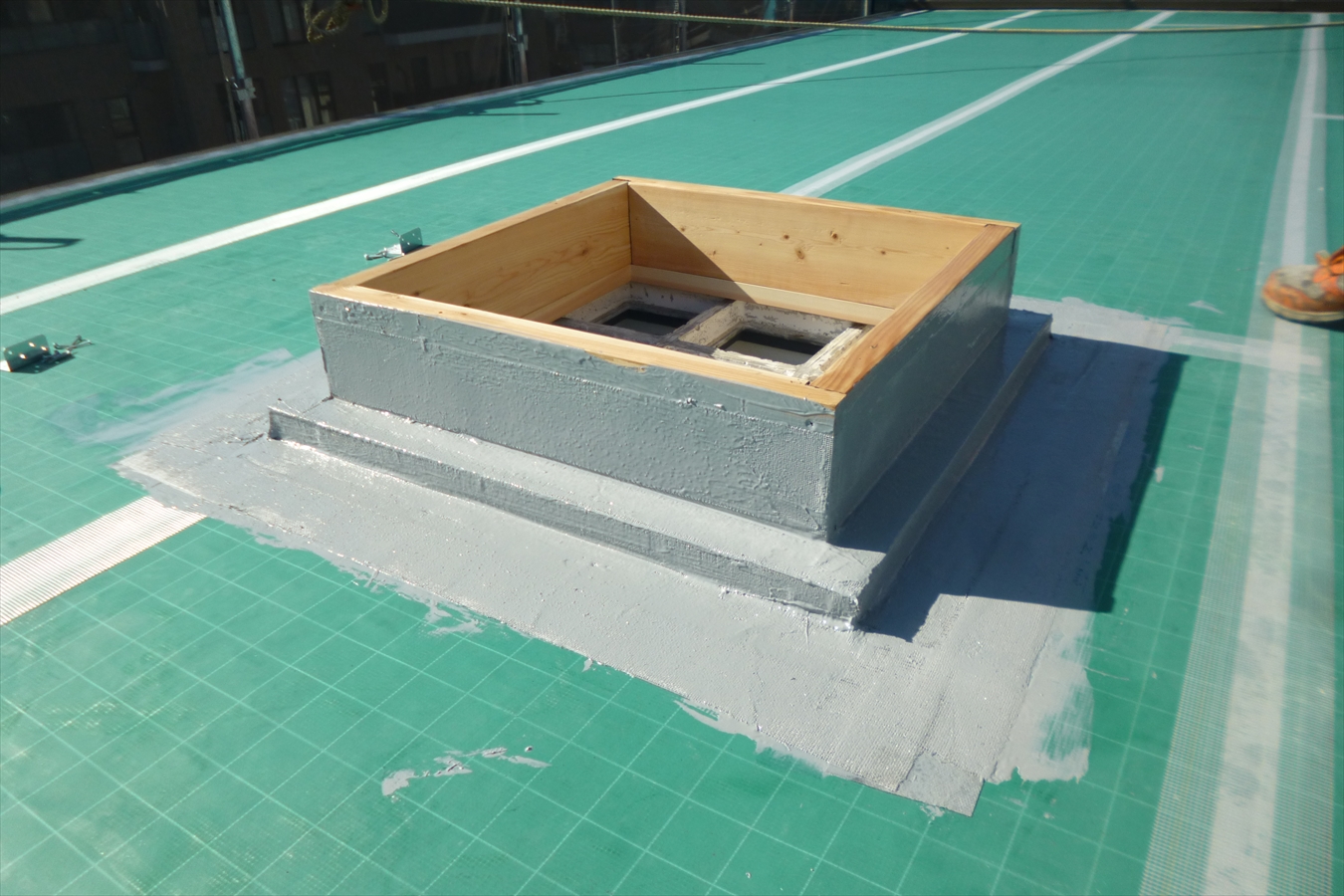
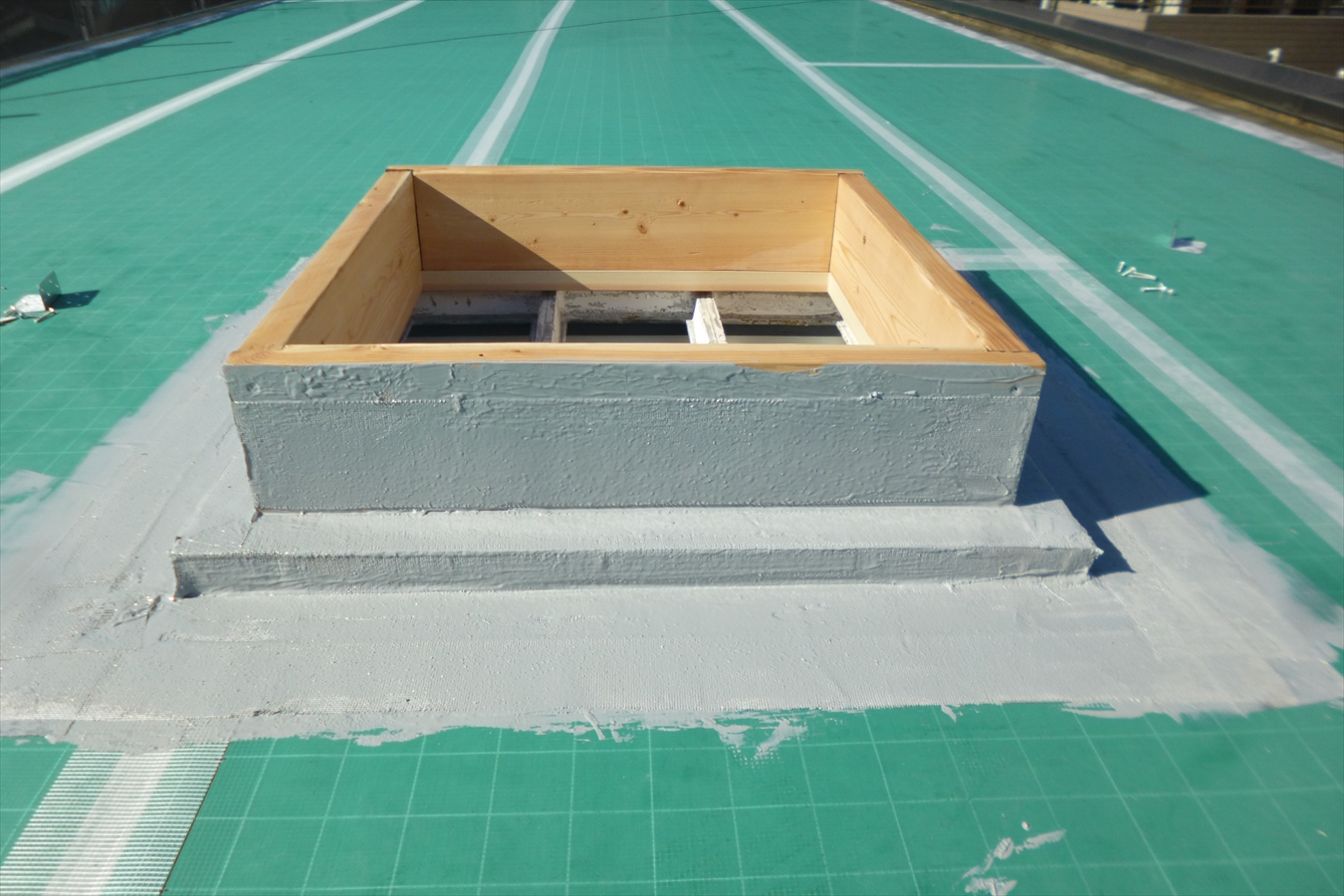
シート端末・メッシュクロス貼り
メッシュクロス貼り
トップライトの枠のような、役物だけでなくQVシートの端末箇所にもメッシュクロスを貼り付けていきます。ここにクロスを入れるのはシートの端が剥がれやすいからであり、それを防ぐための補強の役割となっています。トップライトの枠ほど手間はかかりません。
土間は役物のように角がある訳ではないので、ウレタンを塗った上からクロスを重ねていけば問題ありません。
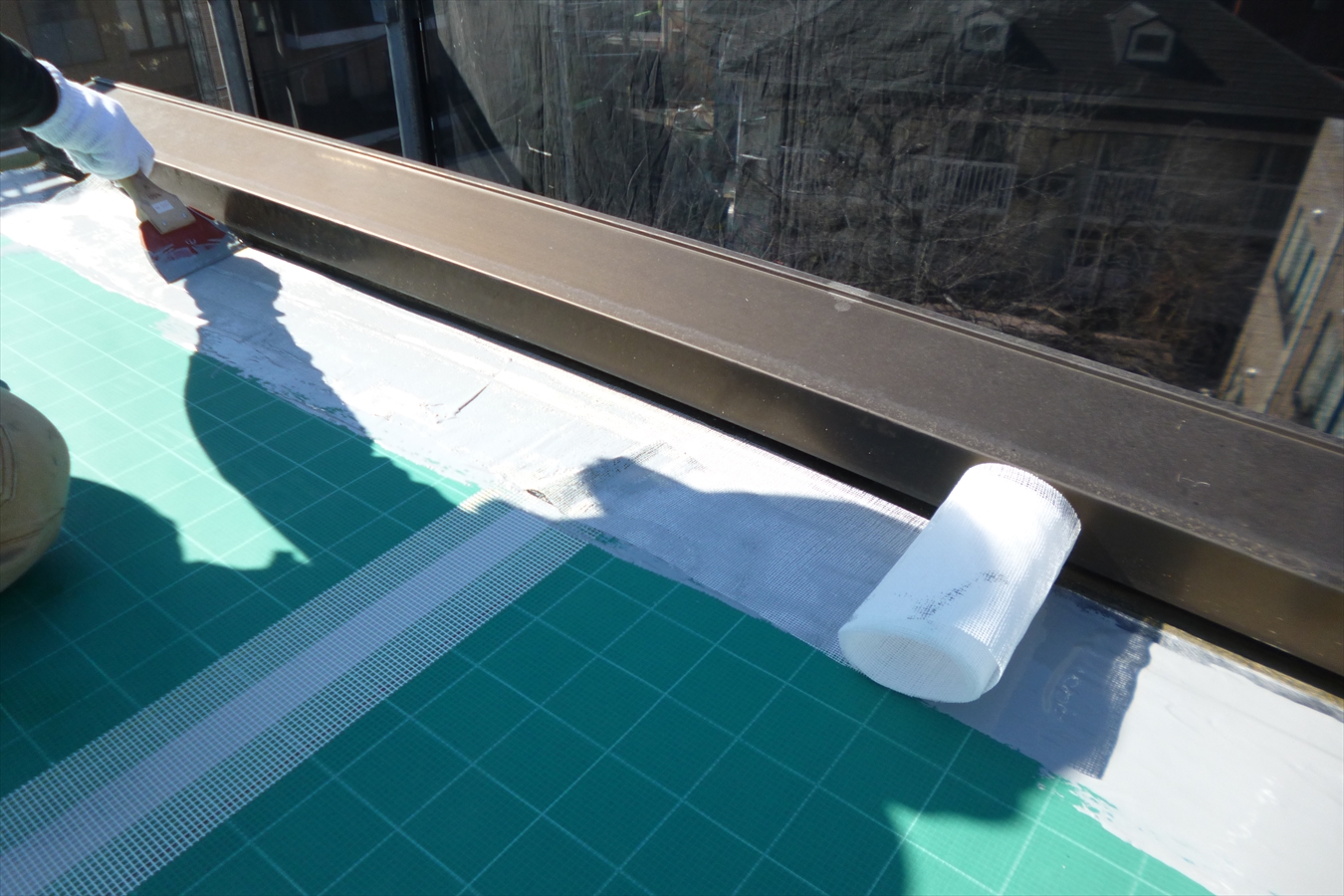
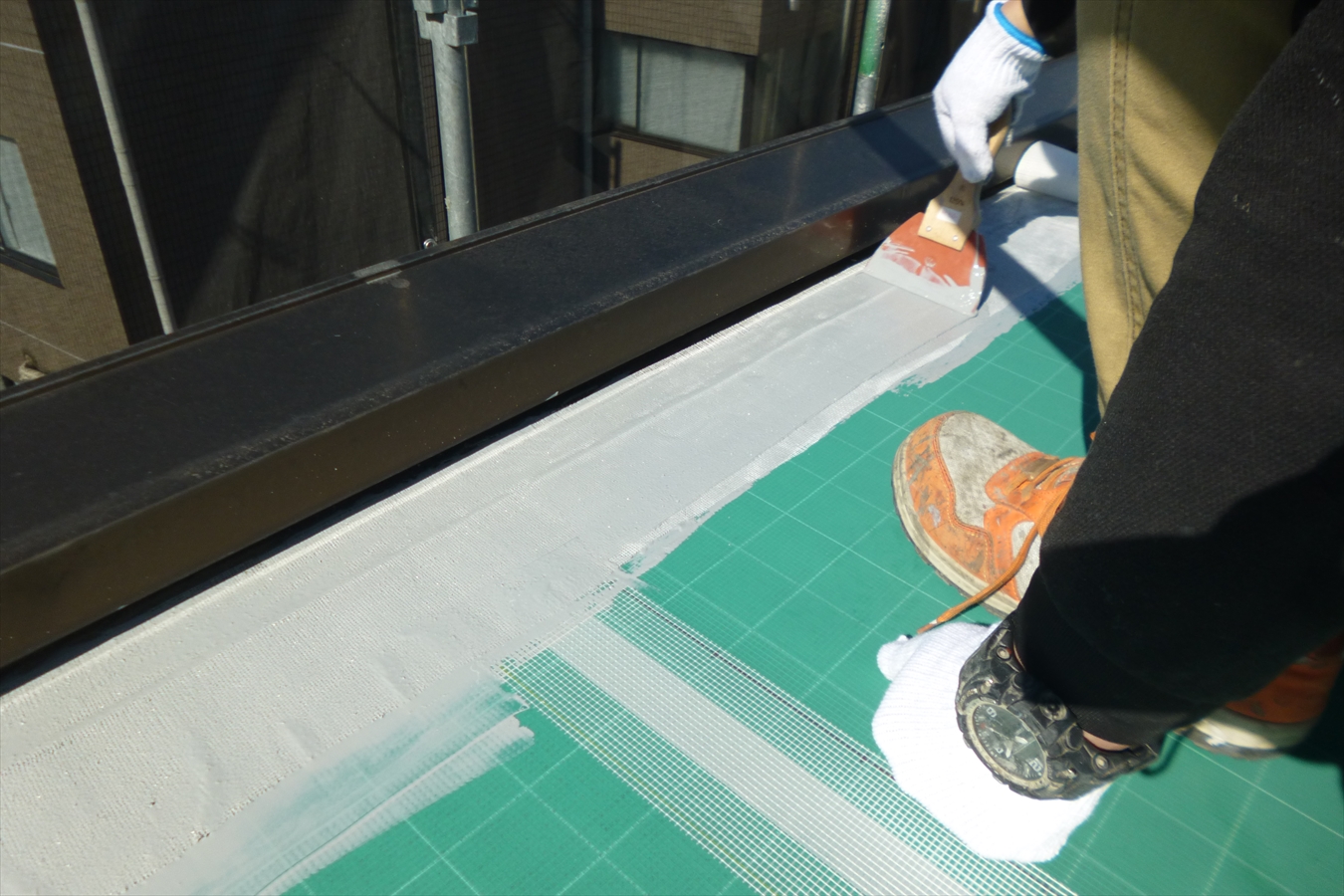
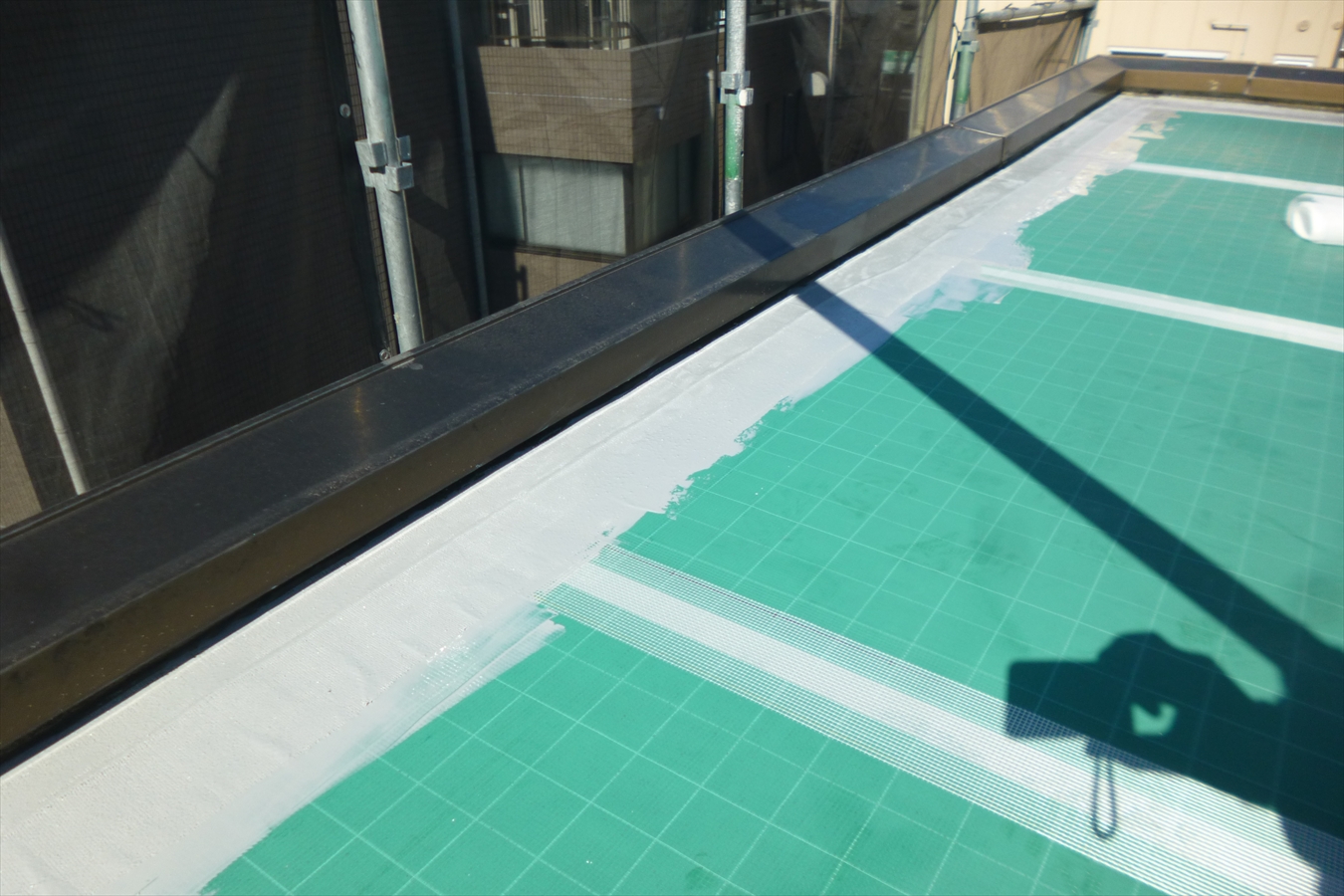
施工後
トップライトの枠と比べるとかなり楽な作業にはなりますが、貼り付けたクロスの目がしっかりと埋まるように作業しています。この目つぶしをしているかどうかで、仕上がりに差が出てくるのでしっかりと潰しておきます。
実際に仕上がった後の写真です。クロスがうっすらと見える程度の厚みがつけられているのが分かると思います。トップライト同様、ここで一旦ウレタンの硬化を待ってから次の作業へ移っていきます。
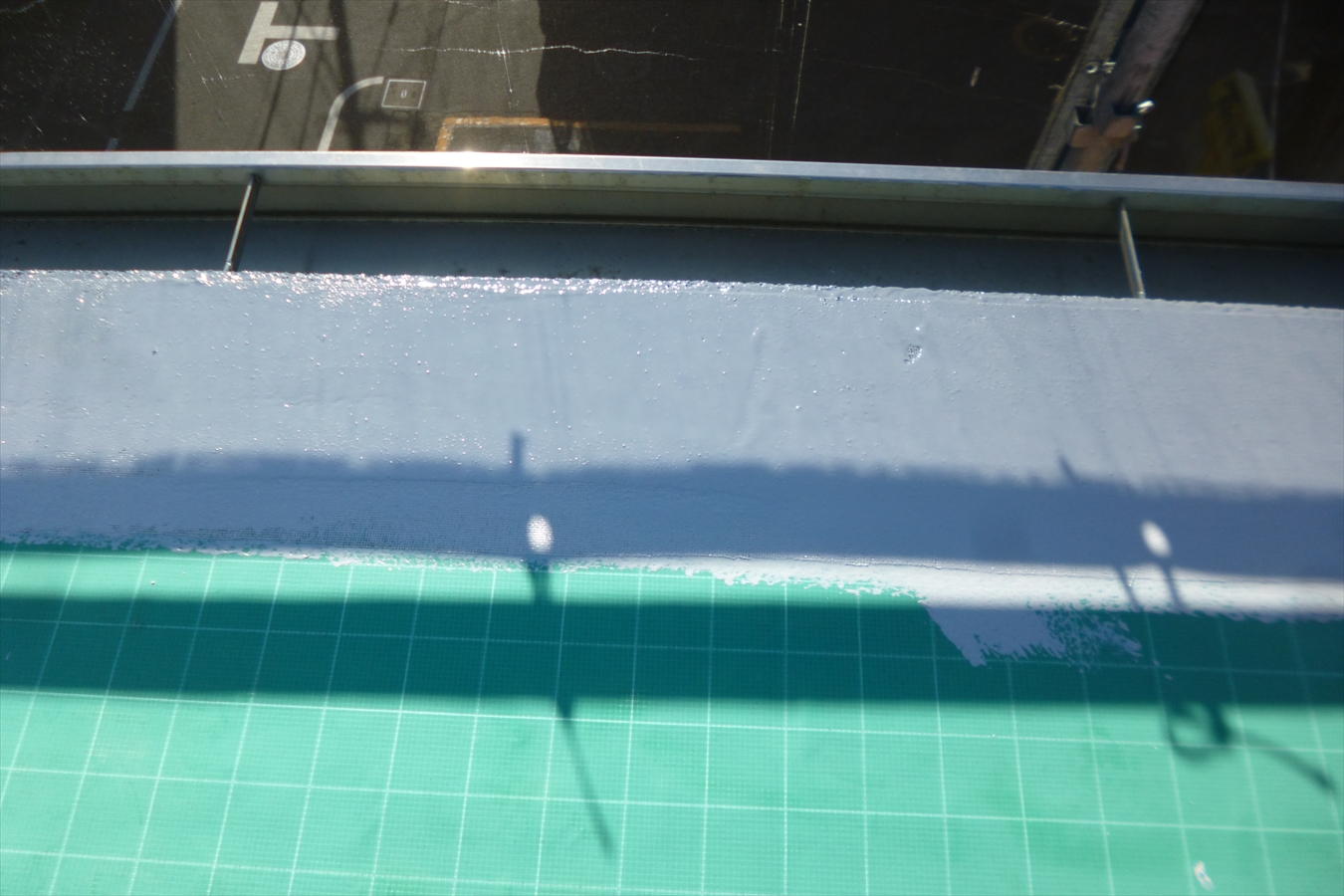
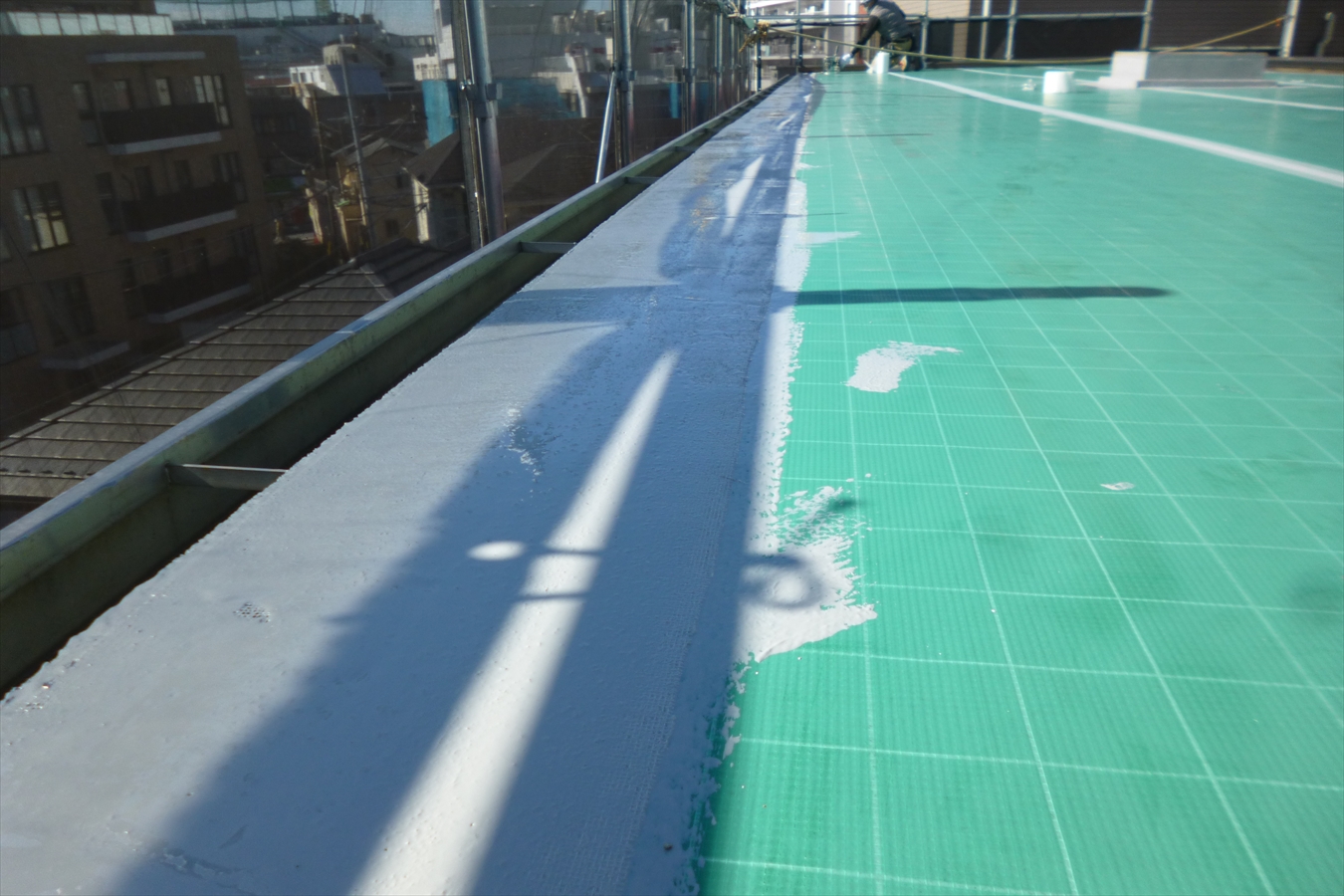
ウレタン1層目
役物 ウレタン1層目塗布
ウレタンは攪拌した瞬間から硬化が始っており、1時間も経たない内にまともに作業ができなくなるほどの硬さになりますが、完全に硬化させるとなるとかなりの時間が必要です。真夏の炎天下であれば、2時間もすれば人が乗っても問題無いくらいまでに硬化しますが、それ以外の季節であれば1日時間を置くのが一般的です。
トップライト周り、QVシートの端末箇所のウレタンが硬化したので1層目を入れていきます。この時は立ち上がり材と平場材をブレンドした材料を使いました。枠だけ1層目を入れるのであれば、立ち上がり材のみで仕上げますが、この後周囲のアルミ笠木下の立ち上がりにもウレタンを入れるため、あえてブレンドした材料を使用しています。
枠の1層目はブレンドした材料なので、ゴムベラを使わずローラーで仕上げました。
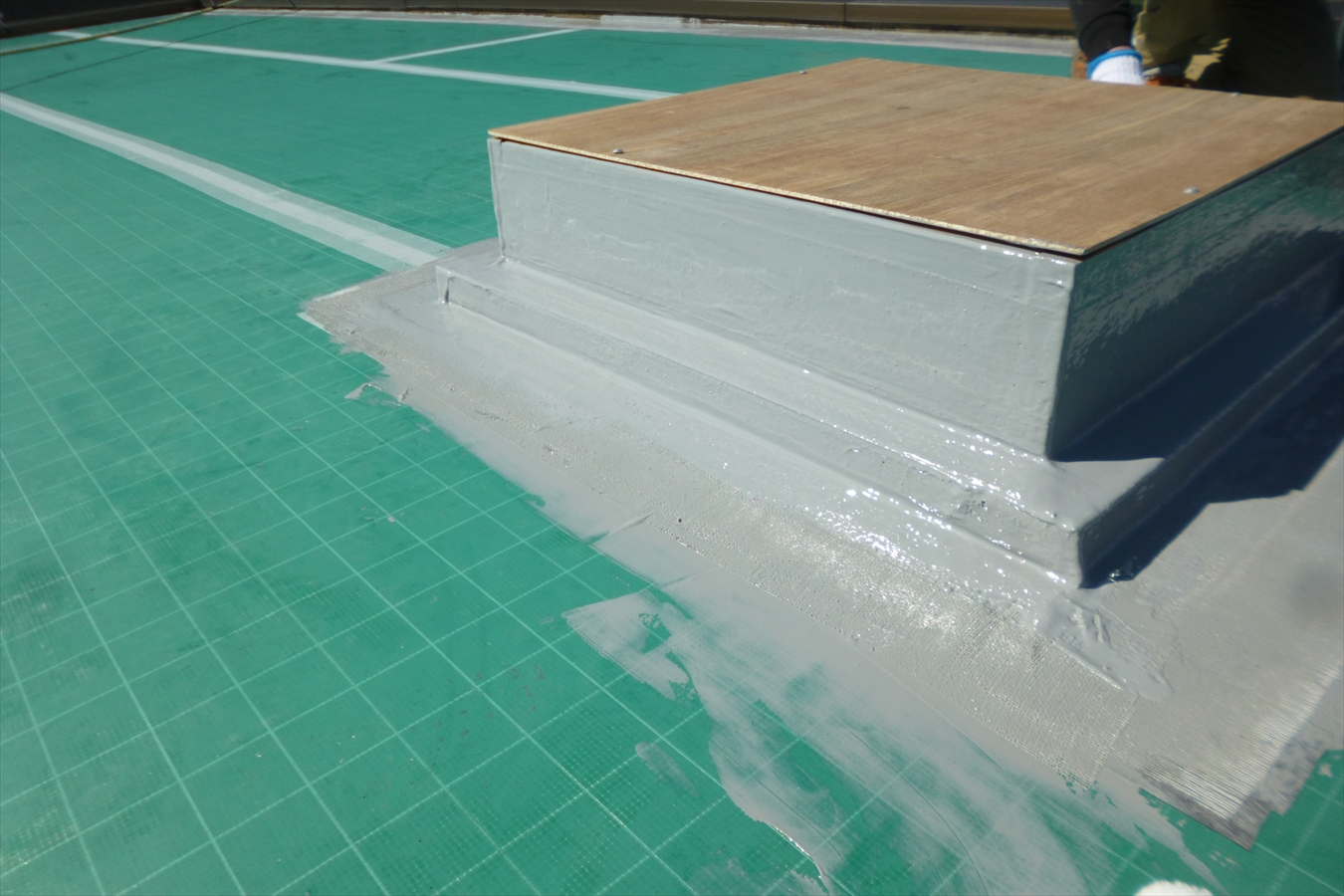
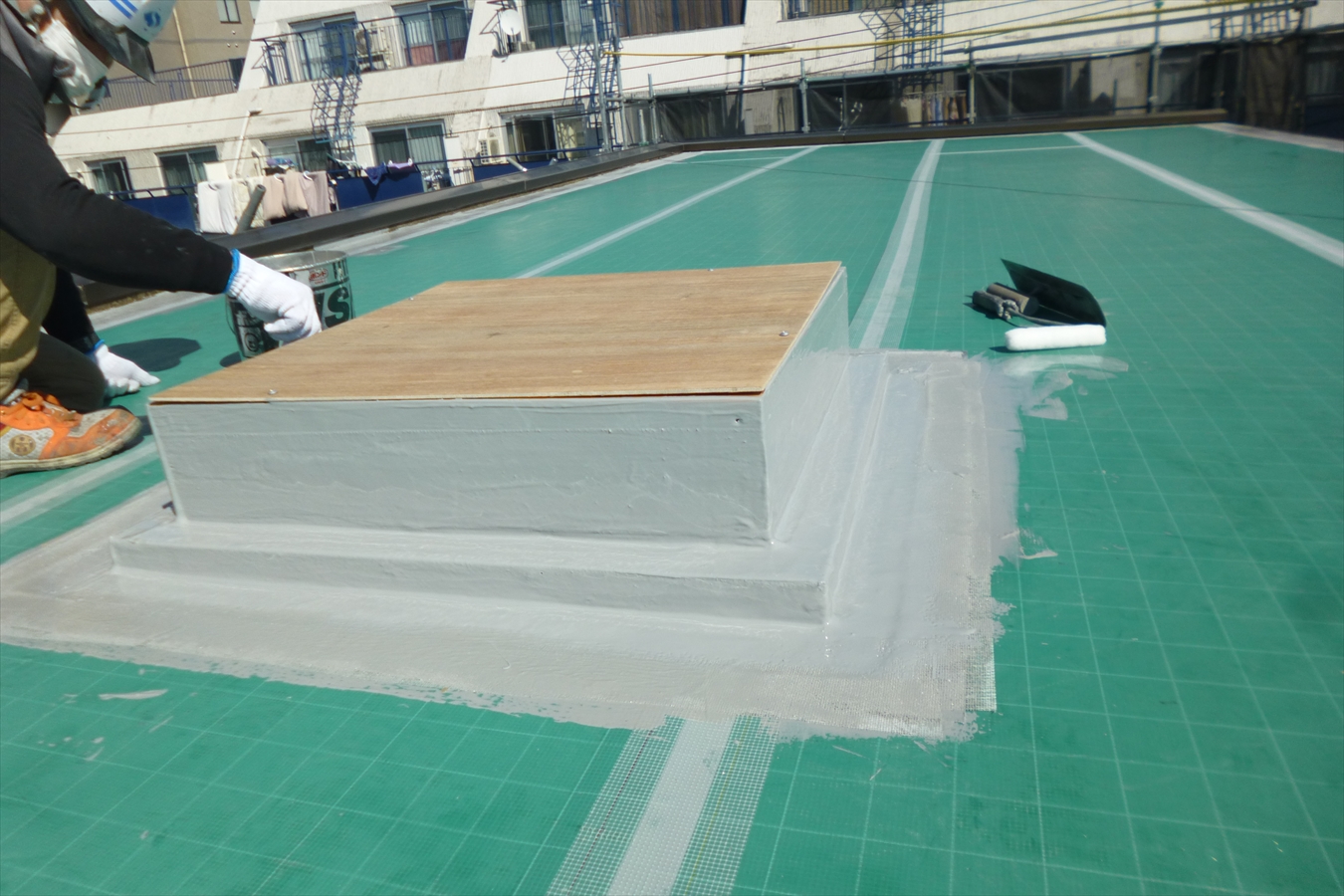
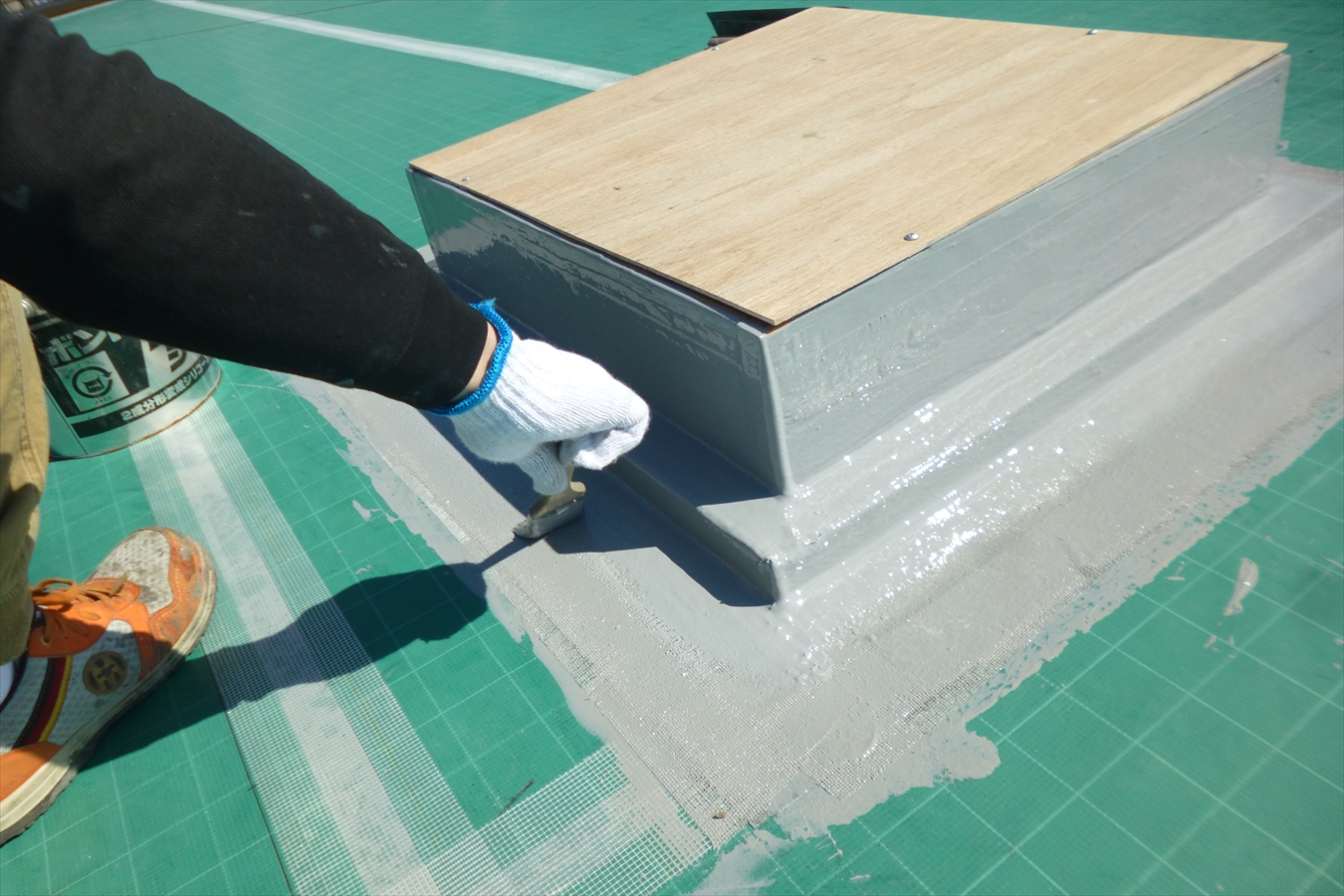
立ち上がり ウレタン1層目塗布
周囲のアルミ笠木の下はほんの僅かな高さですが立ち上がりがあるので、そこにウレタンの1層目を塗布していきます。本来ならこの立ち上がりにもメッシュクロスを入れる必要がありますが、極端に高さが無い上に、アルミ笠木そのものを外しようがなかったためクロスの入れようがありませんでした。そのため、クロスは入れずウレタンを直接塗り込むことになりました。
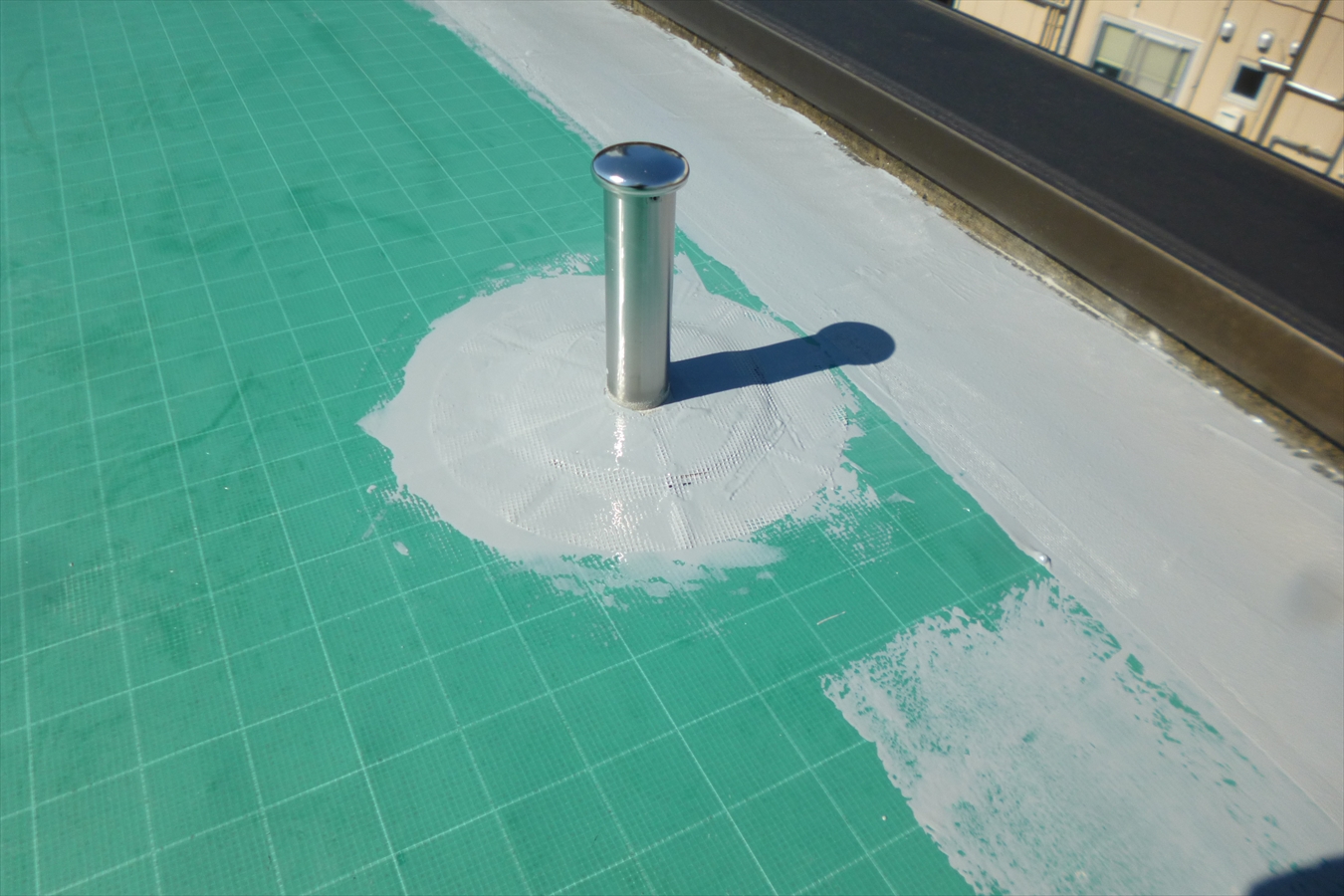
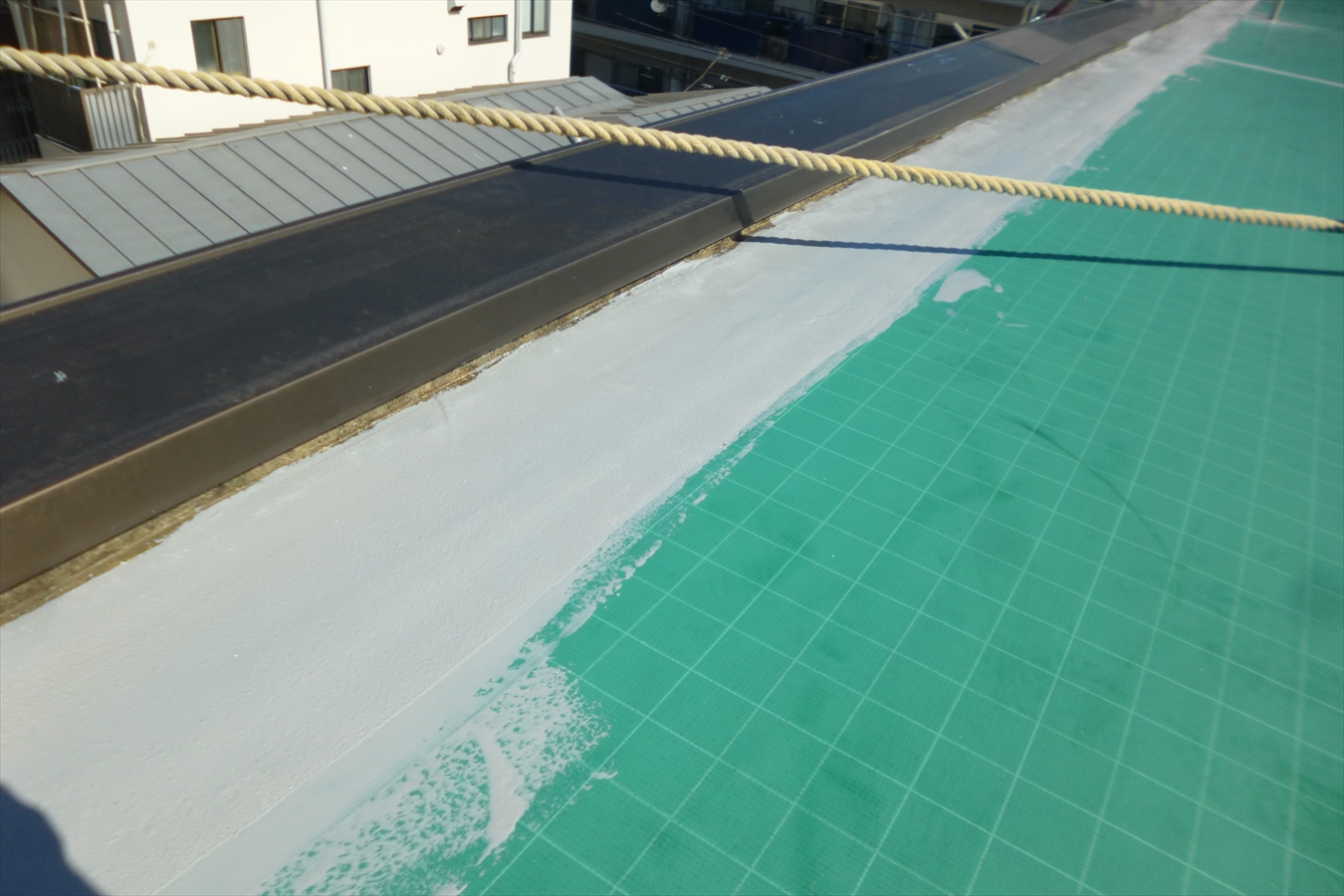
笠木があり、ゴムベラの入れようがないためブレンドしたウレタン材を刷毛で塗り込んで1層目を入れていきます。また、脱気筒の周りや、シートの端末箇所にもウレタンを入れておきました。
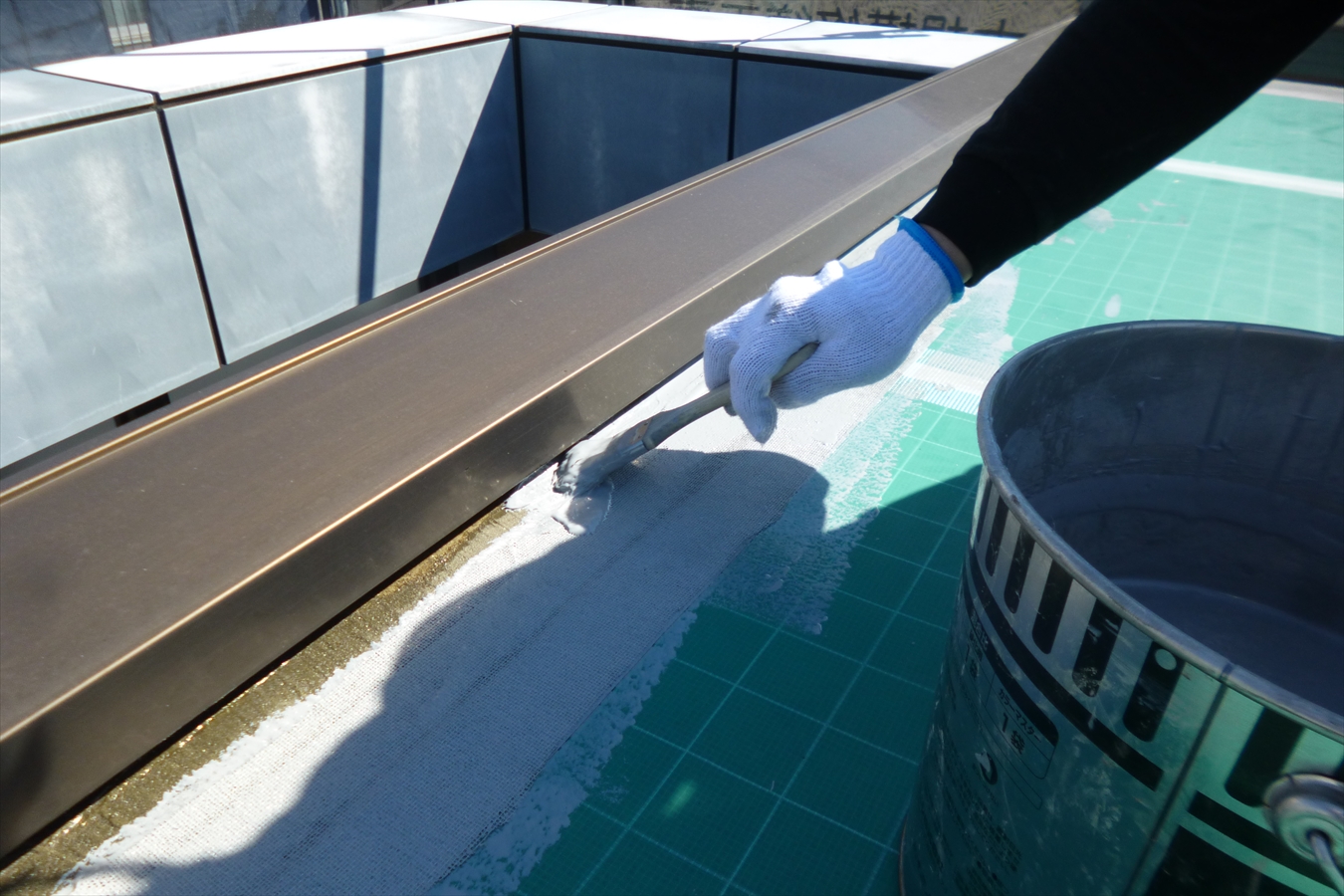
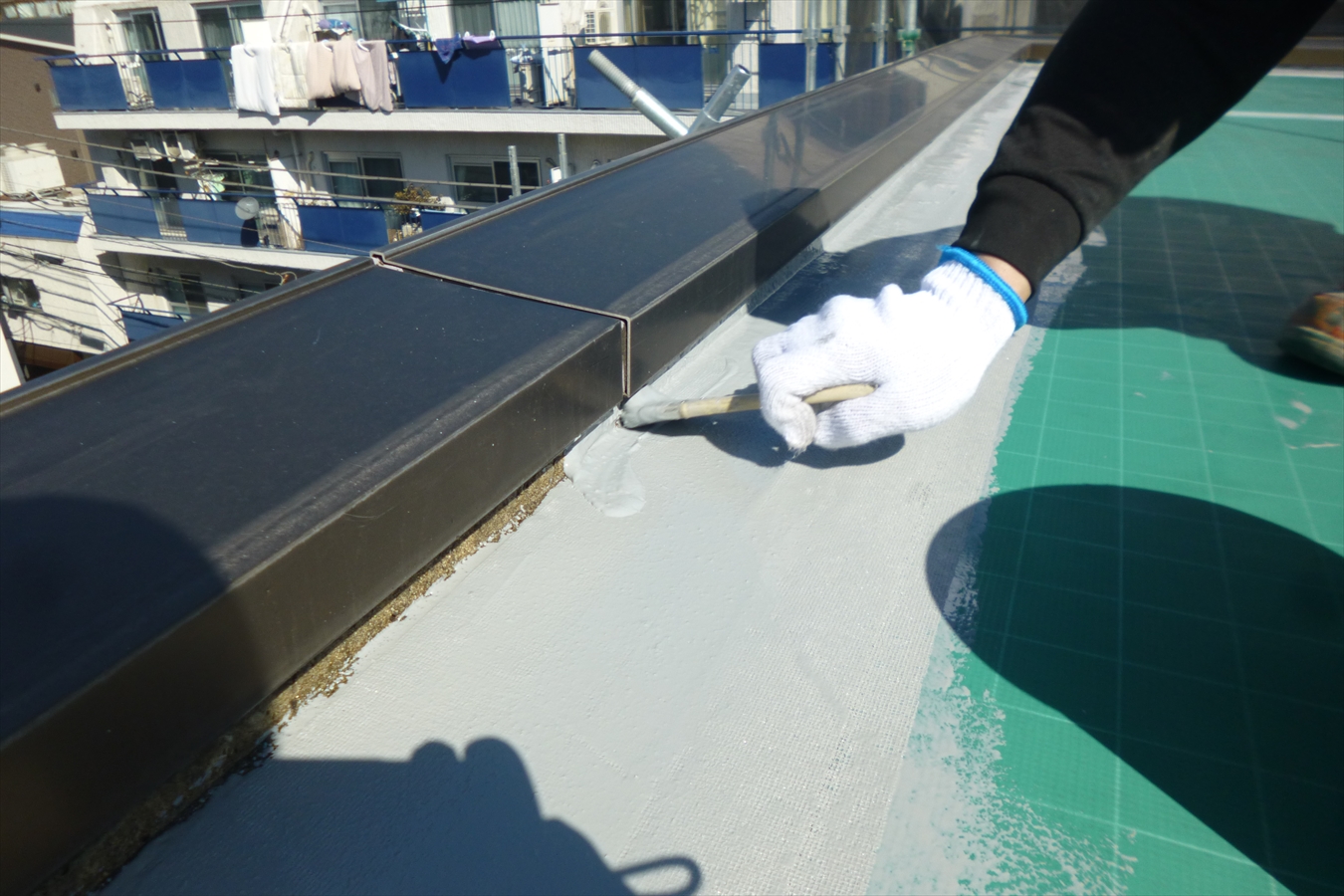
土間 ウレタン1層目塗布
ようやくウレタン防水一番のメイン作業の土間のウレタン1層目です。
ウレタン防水はこれがメインの工程となりますが、ここに来るまでが非常に長いです。実際に使用した材料は、平場材であるサラセーヌKです。
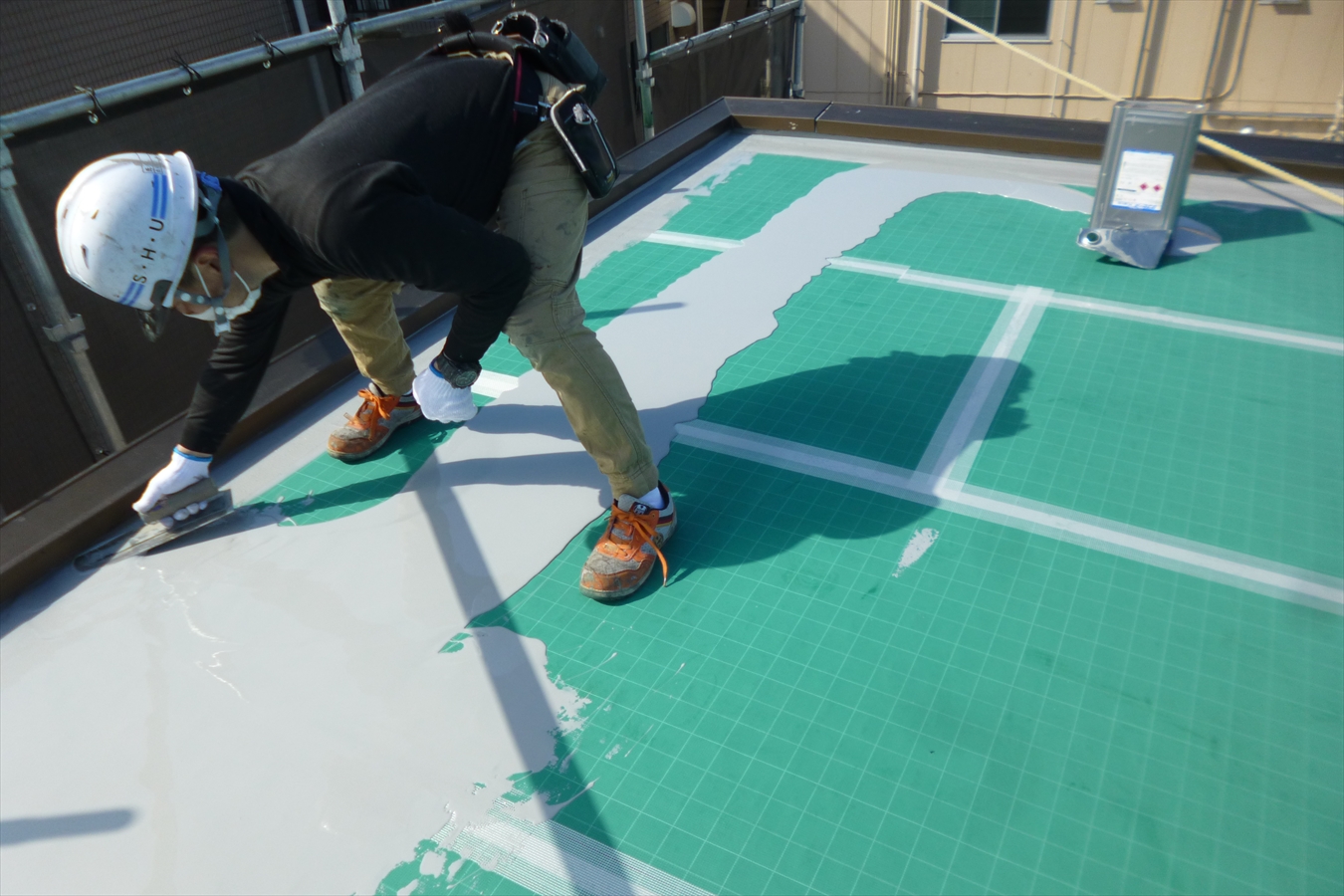
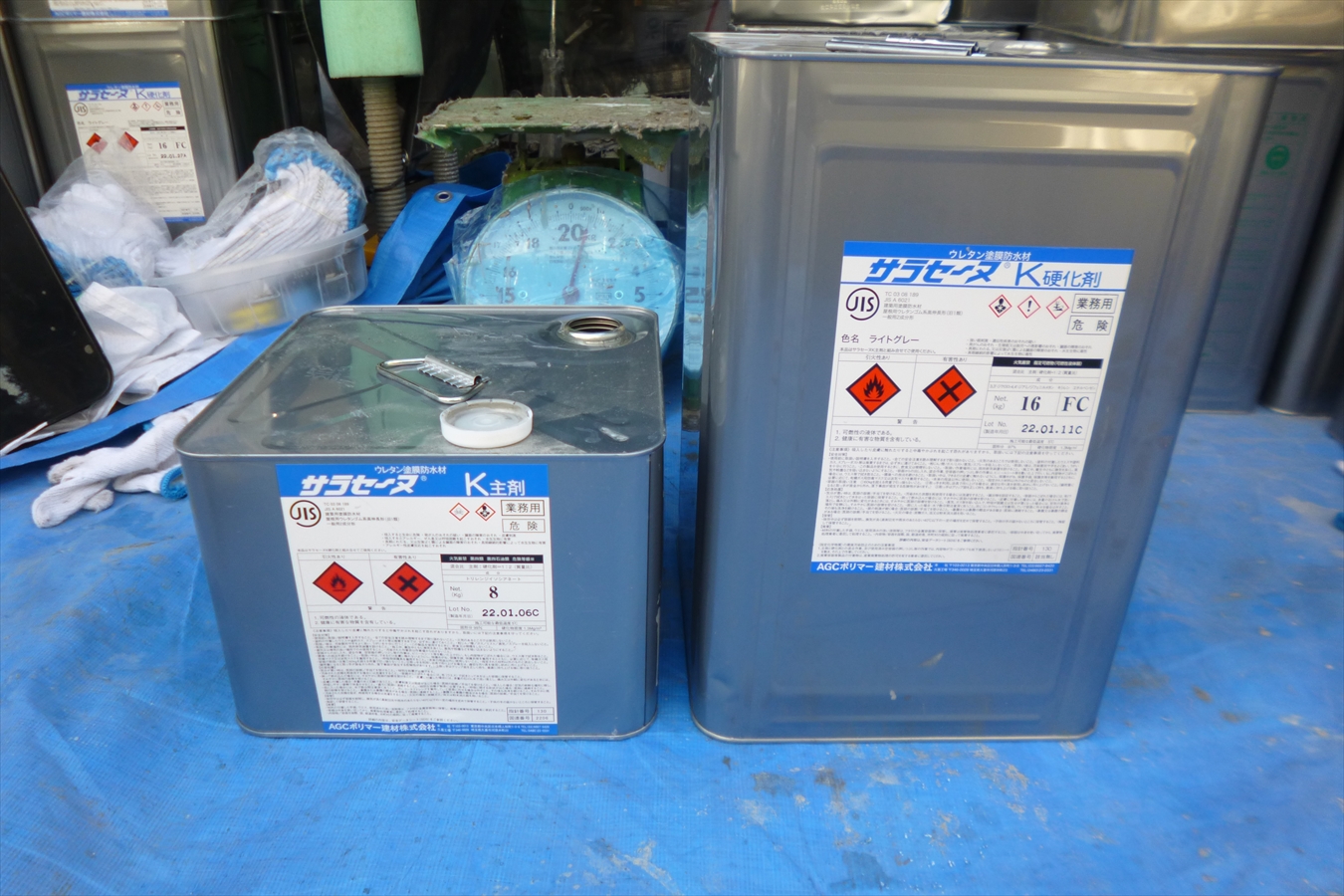
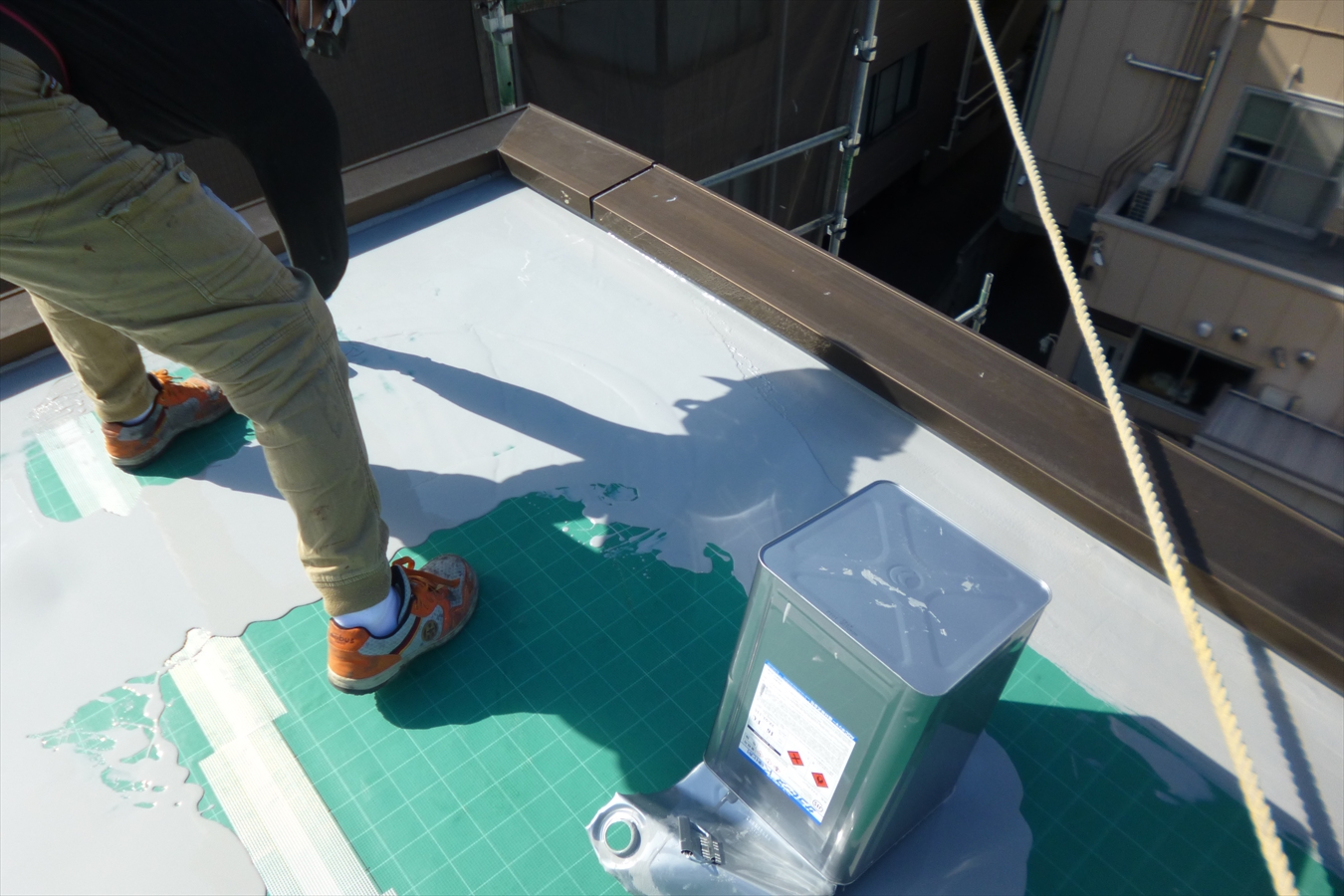
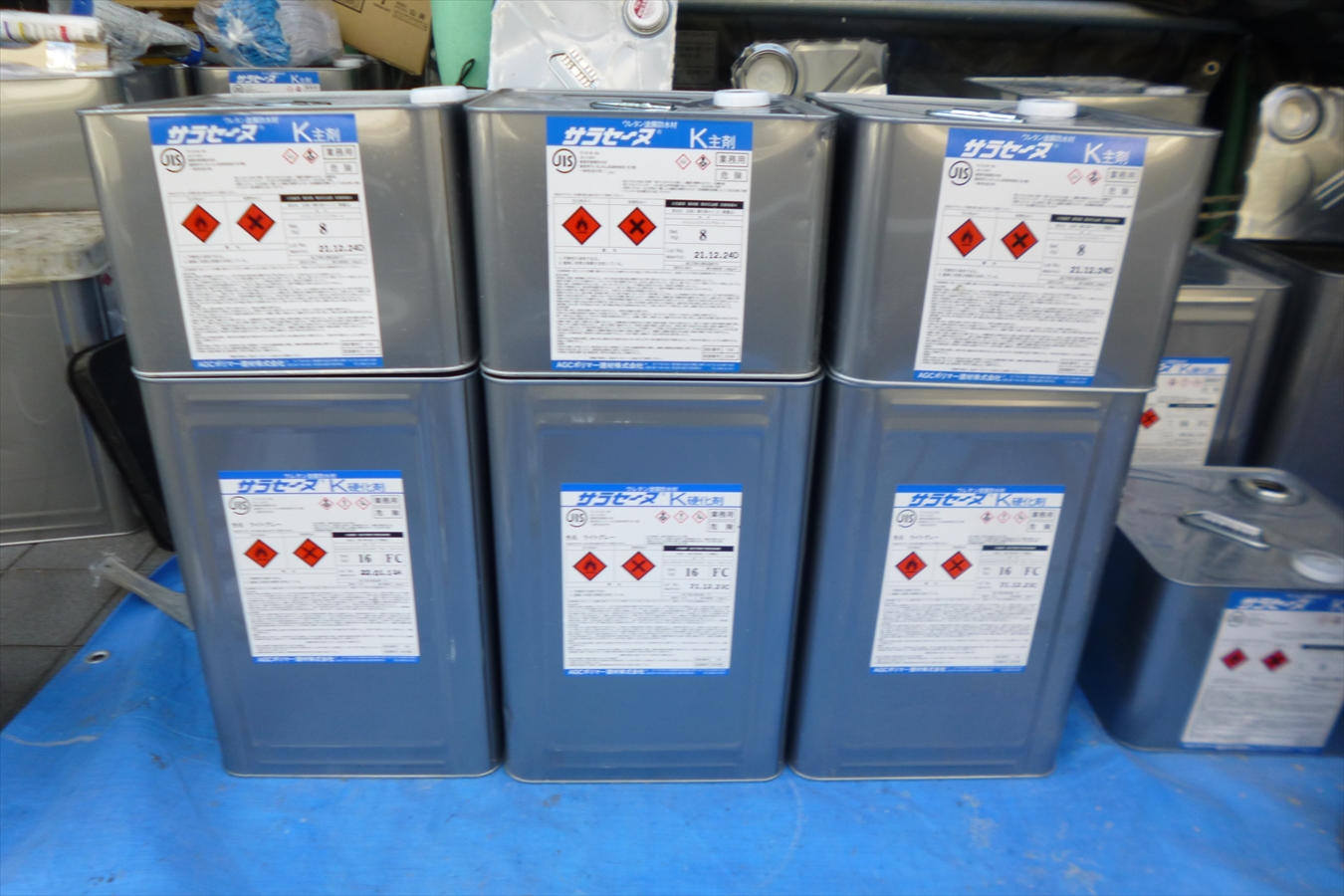
土間のウレタンにはブレンドした材料が使われることが殆どなく、平場材のみで作業することが殆どです。ハイモルスーパー♯10で下地補修した時と同じように、ある程度土間に撒いたウレタンを小手で均一な厚みになるように均していきます。
この作業は小手でもローラーでも問題ありません。この時はこの二つを使い分けながら流しました。
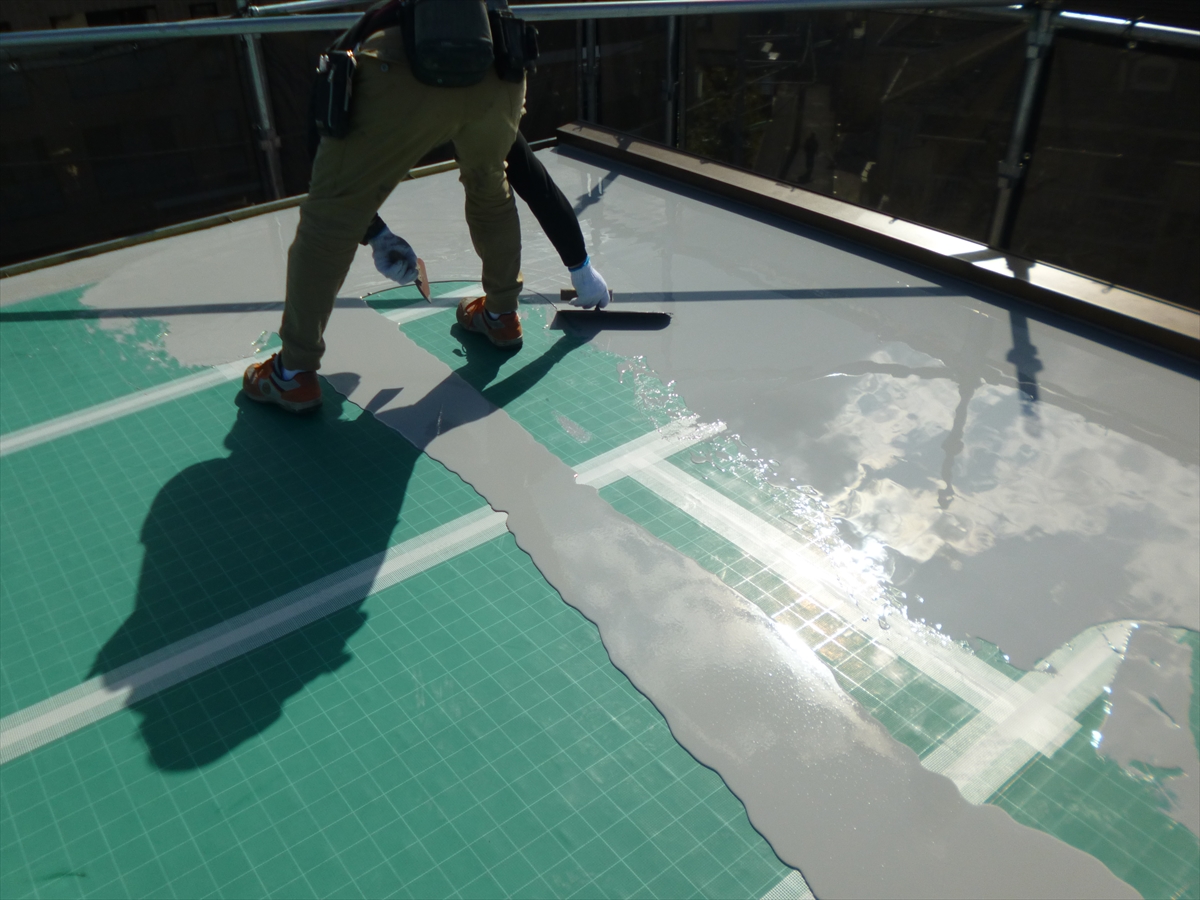
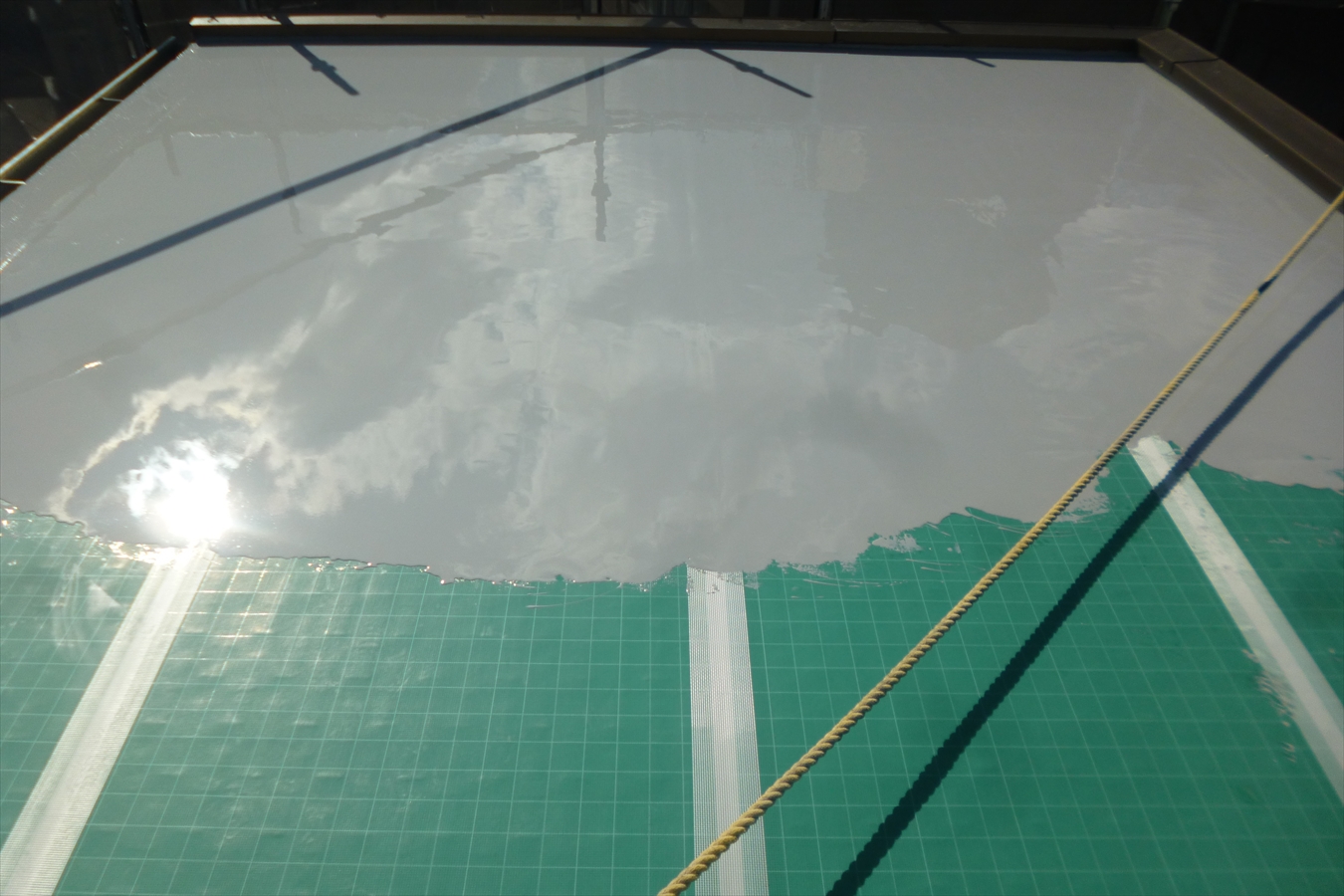
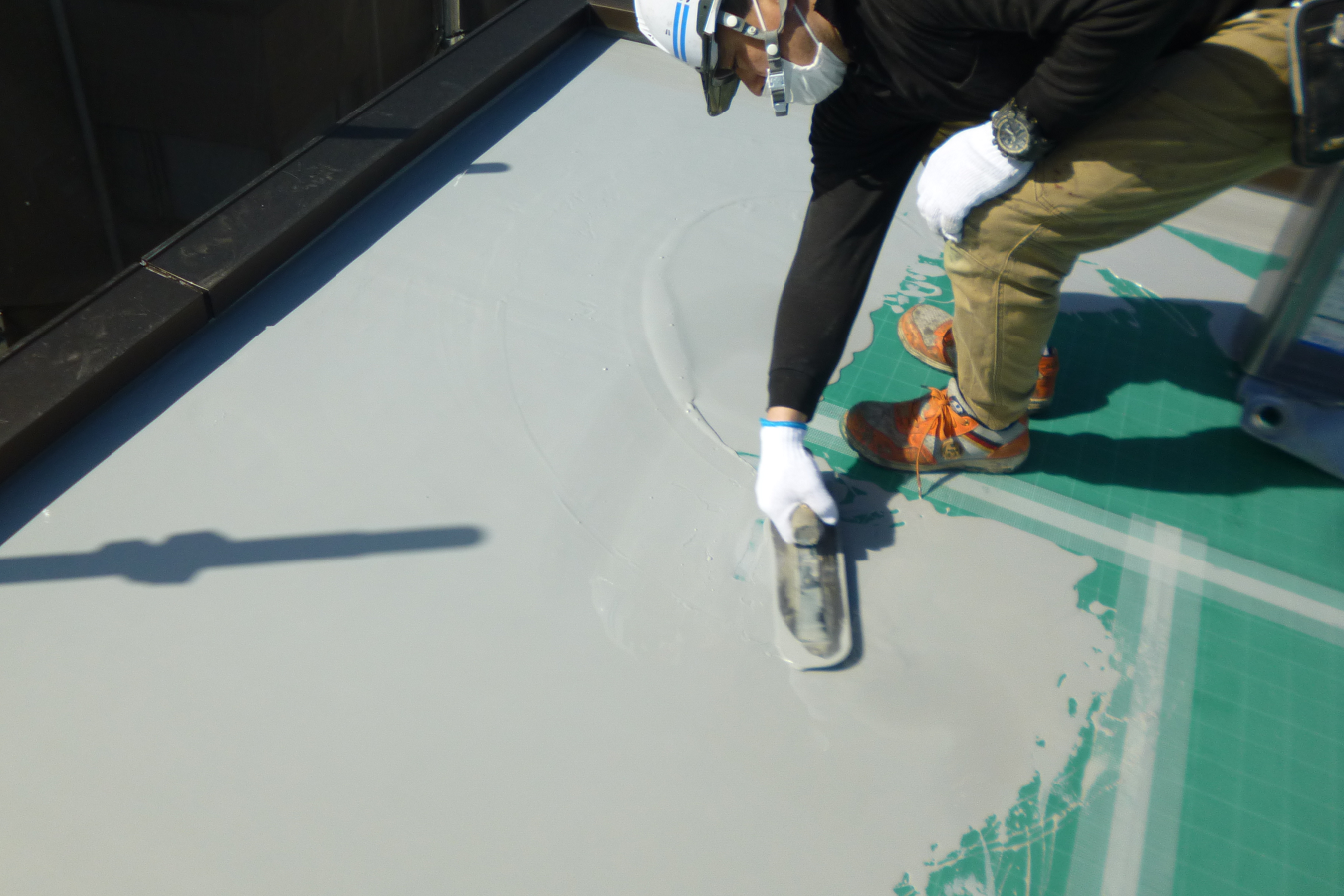
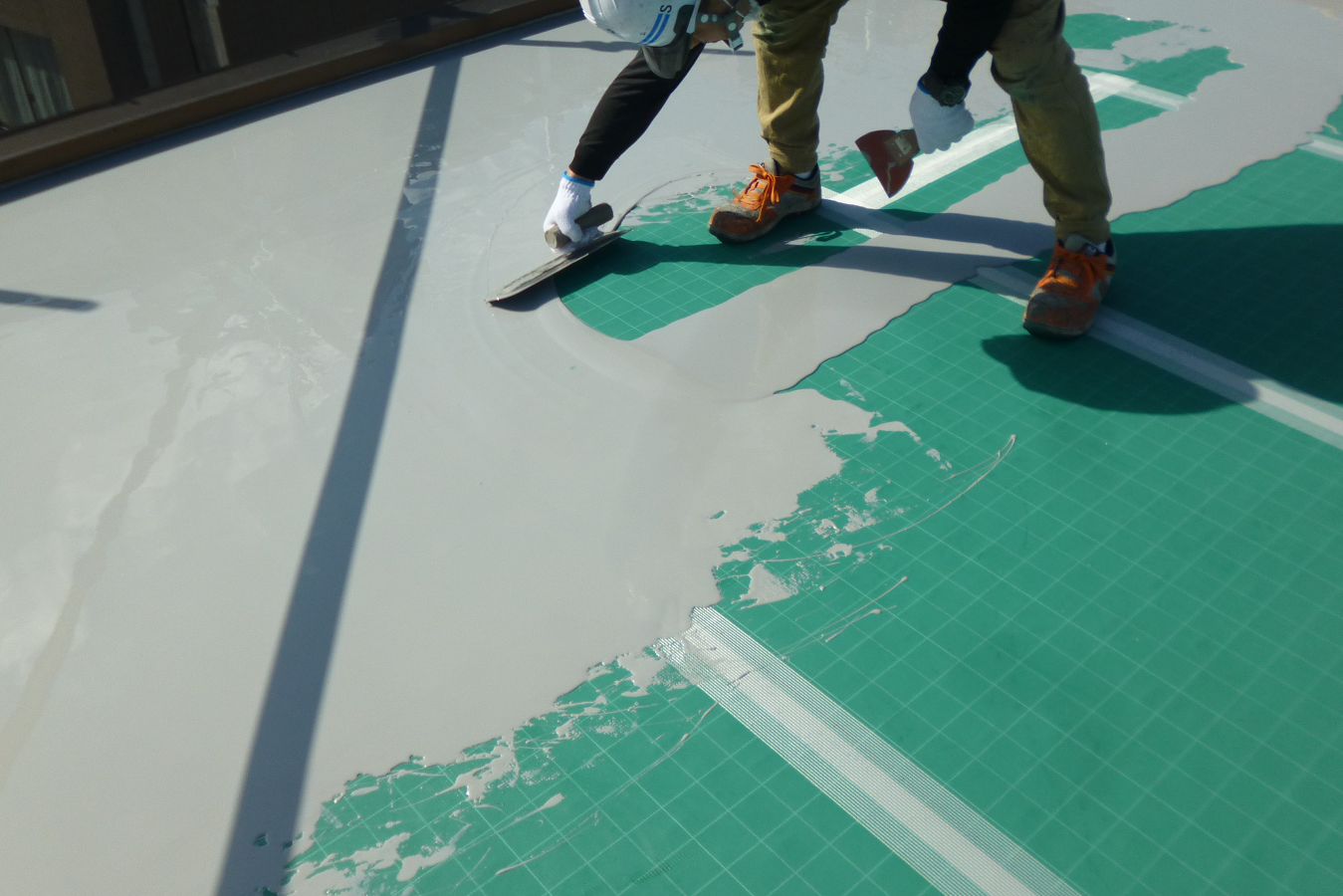
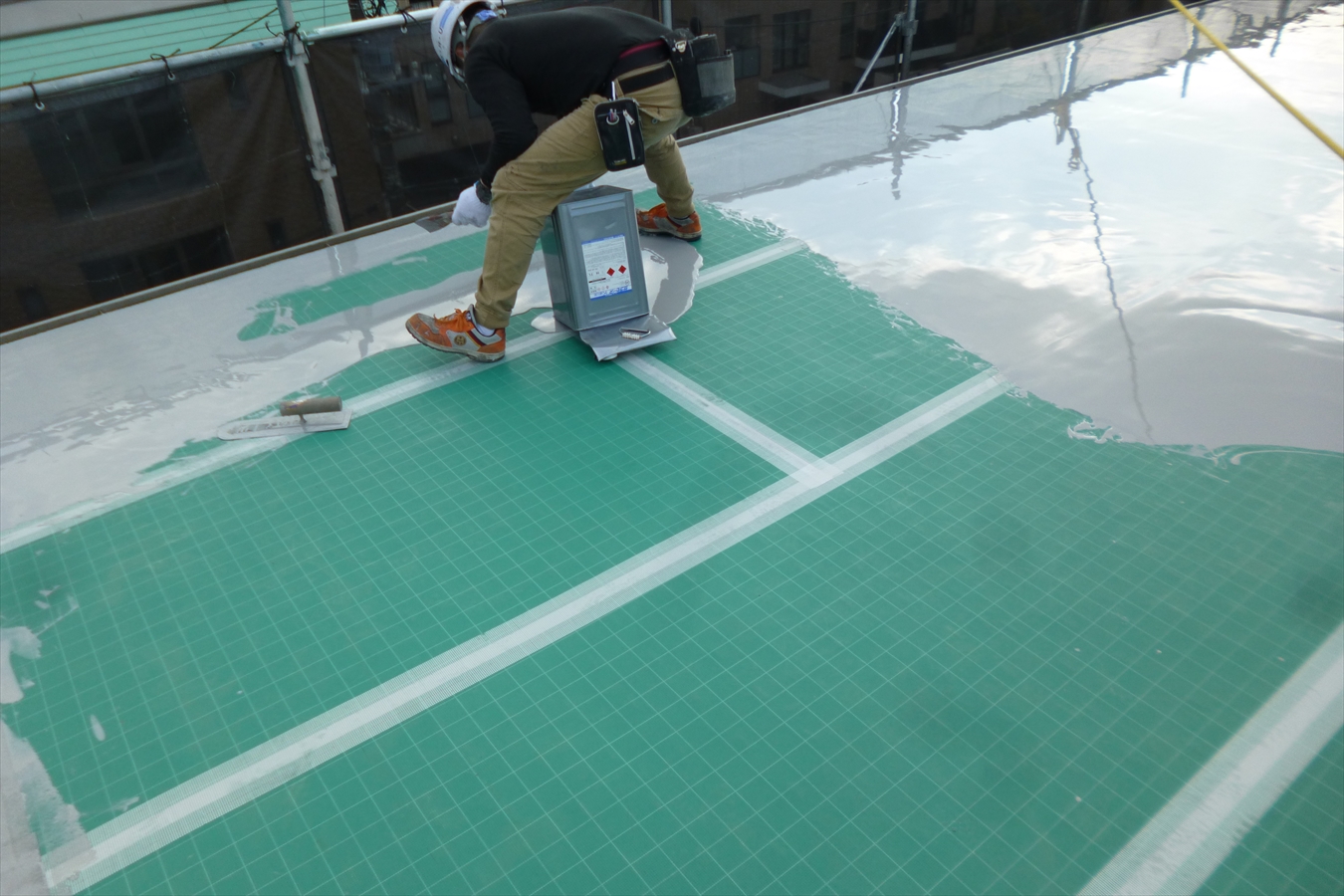
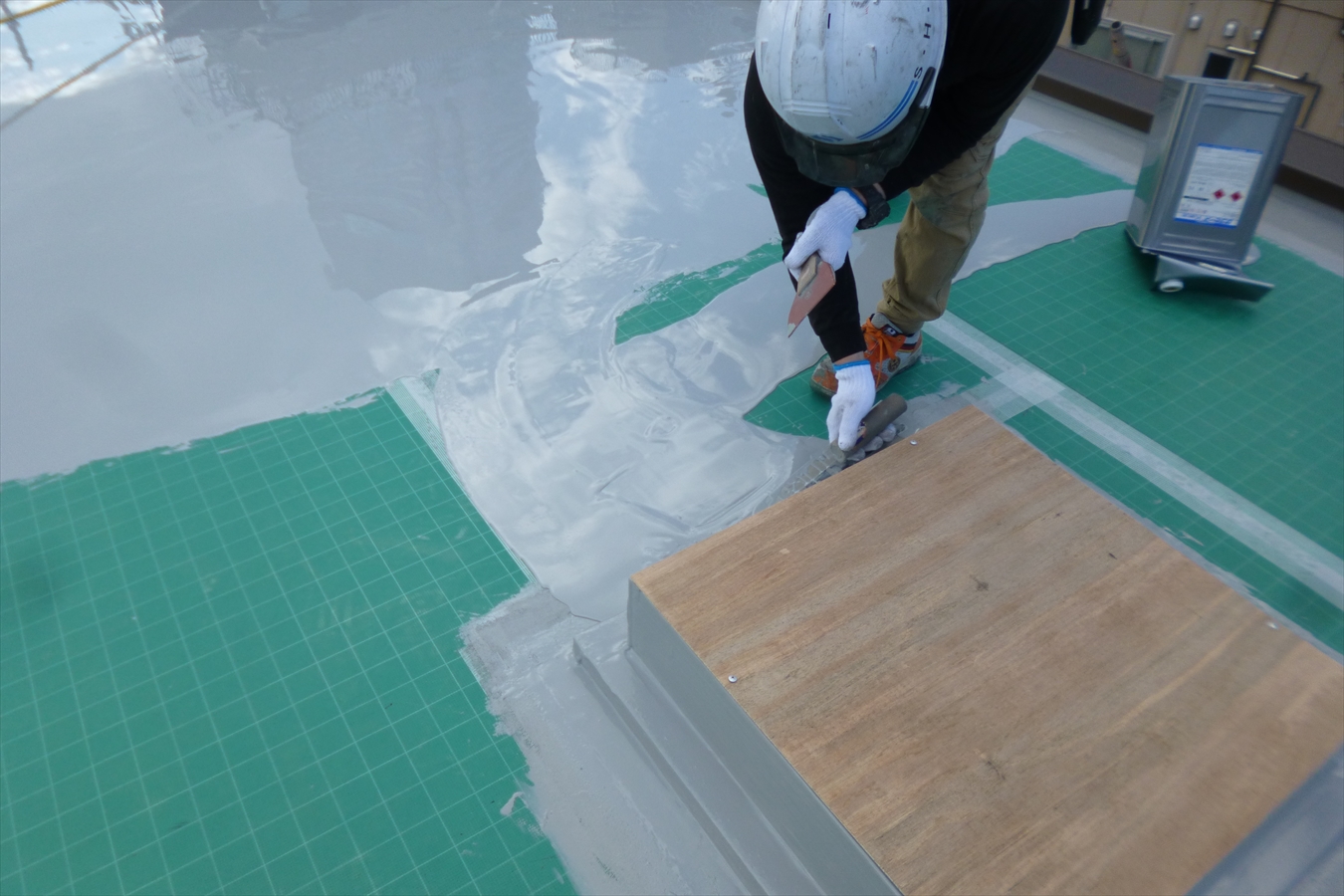
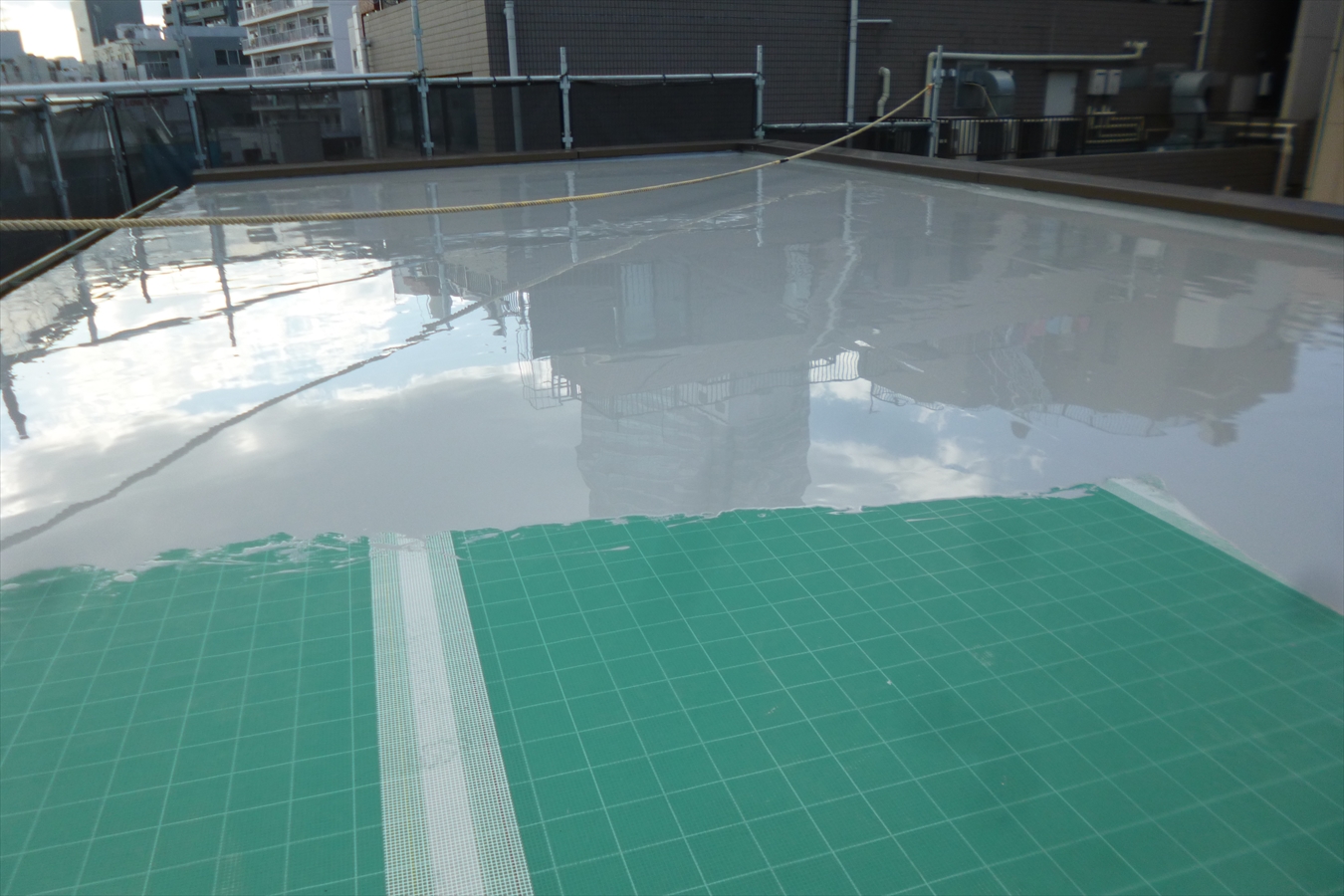
これも下地補修の時と同じように、屋上の出入り口から一番遠い箇所から、そして勾配の低い方から高い方へ流して仕上げています。
勾配の高い方からウレタンを流してしまうと、硬化する前に低い方へウレタンが流れてしまうため、勾配の低いところに撒いたウレタンを上に引き上げるように流しています。
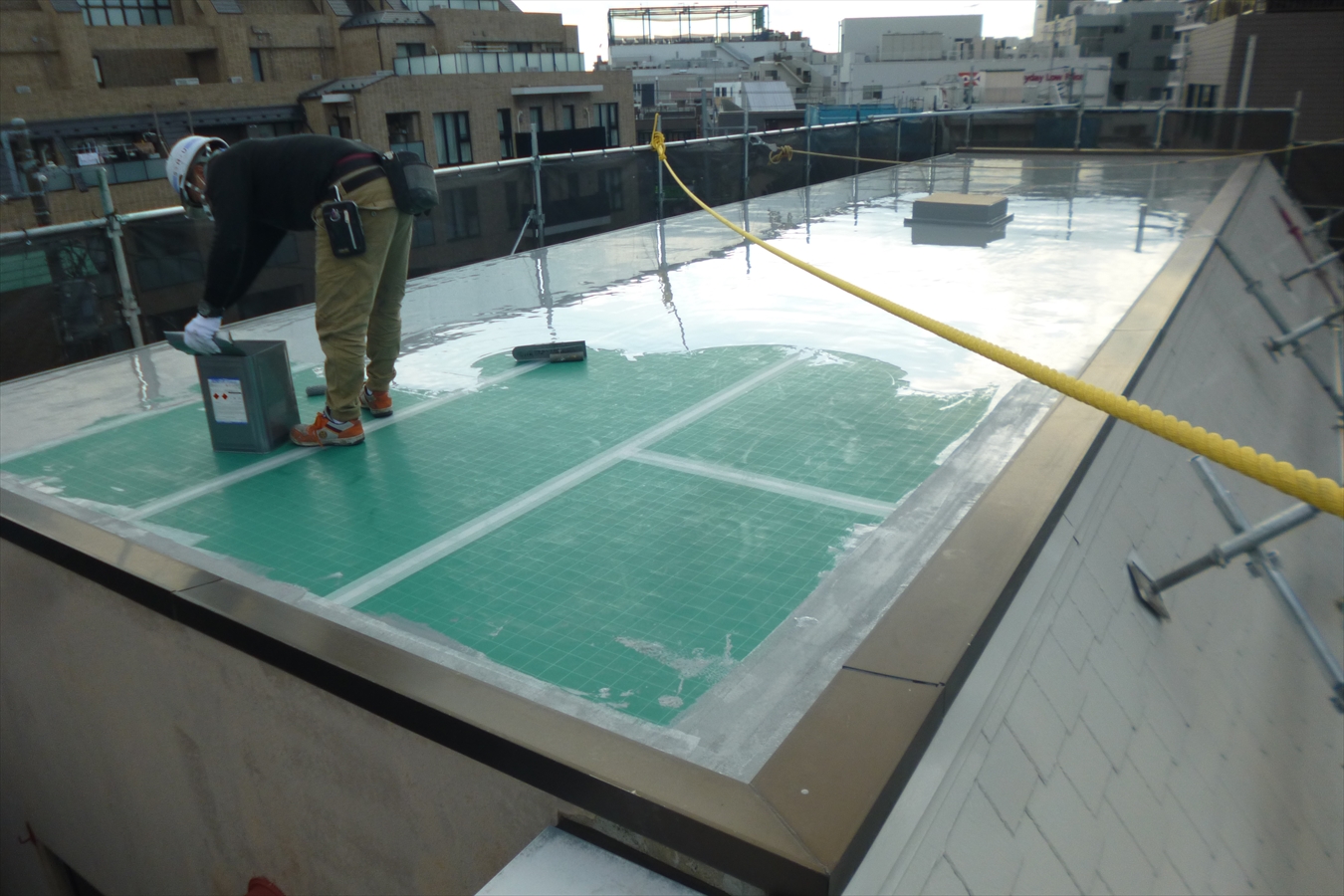
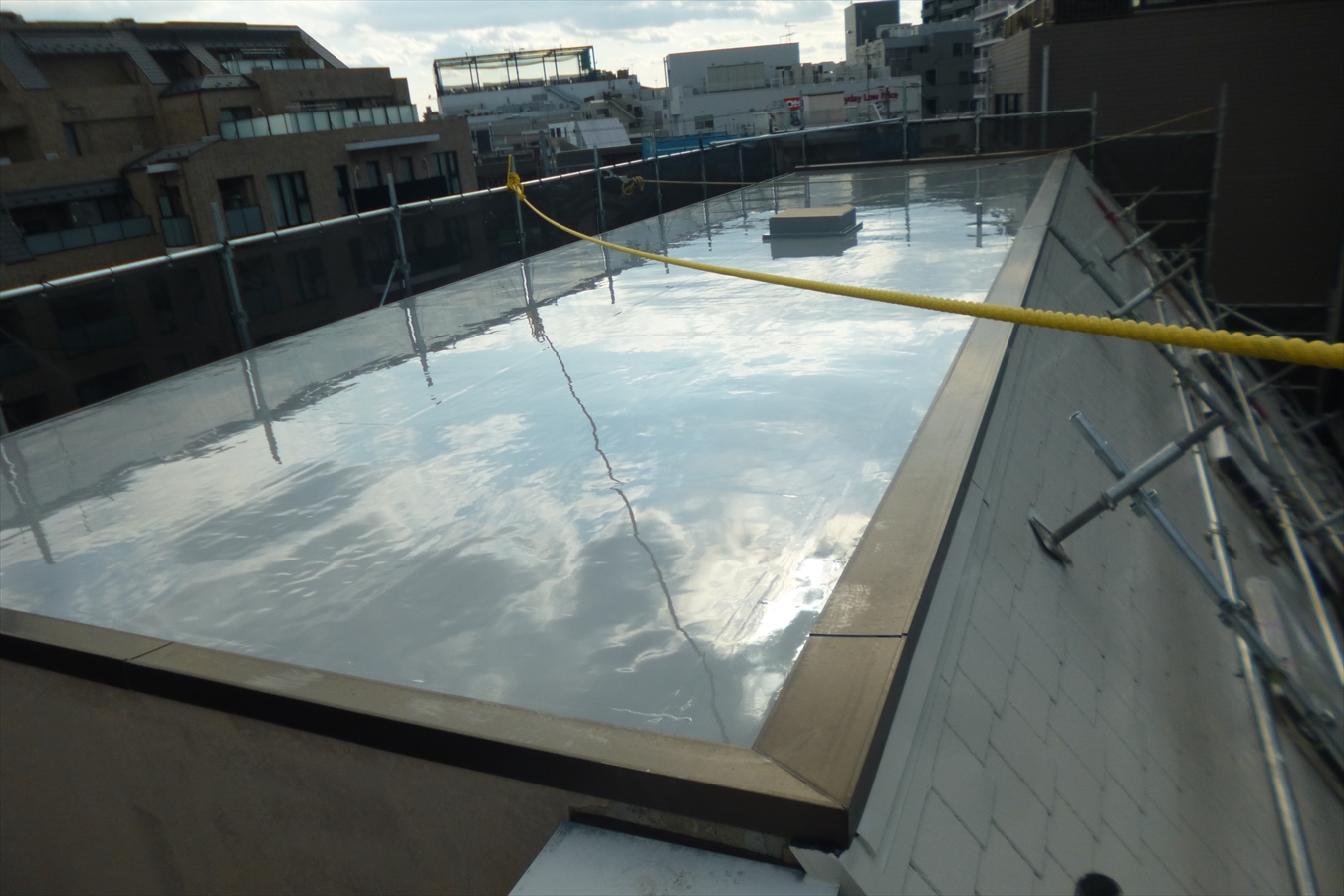
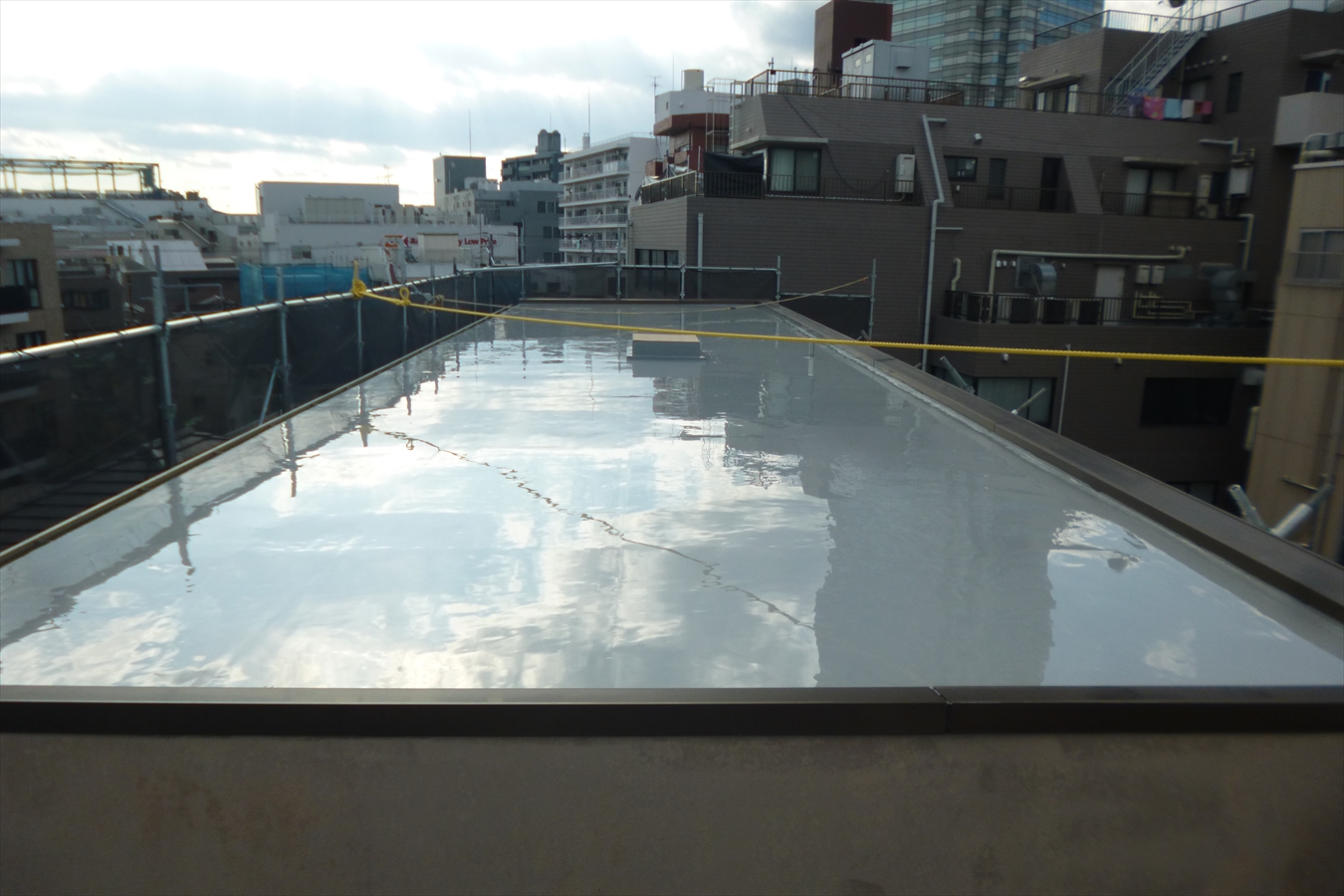
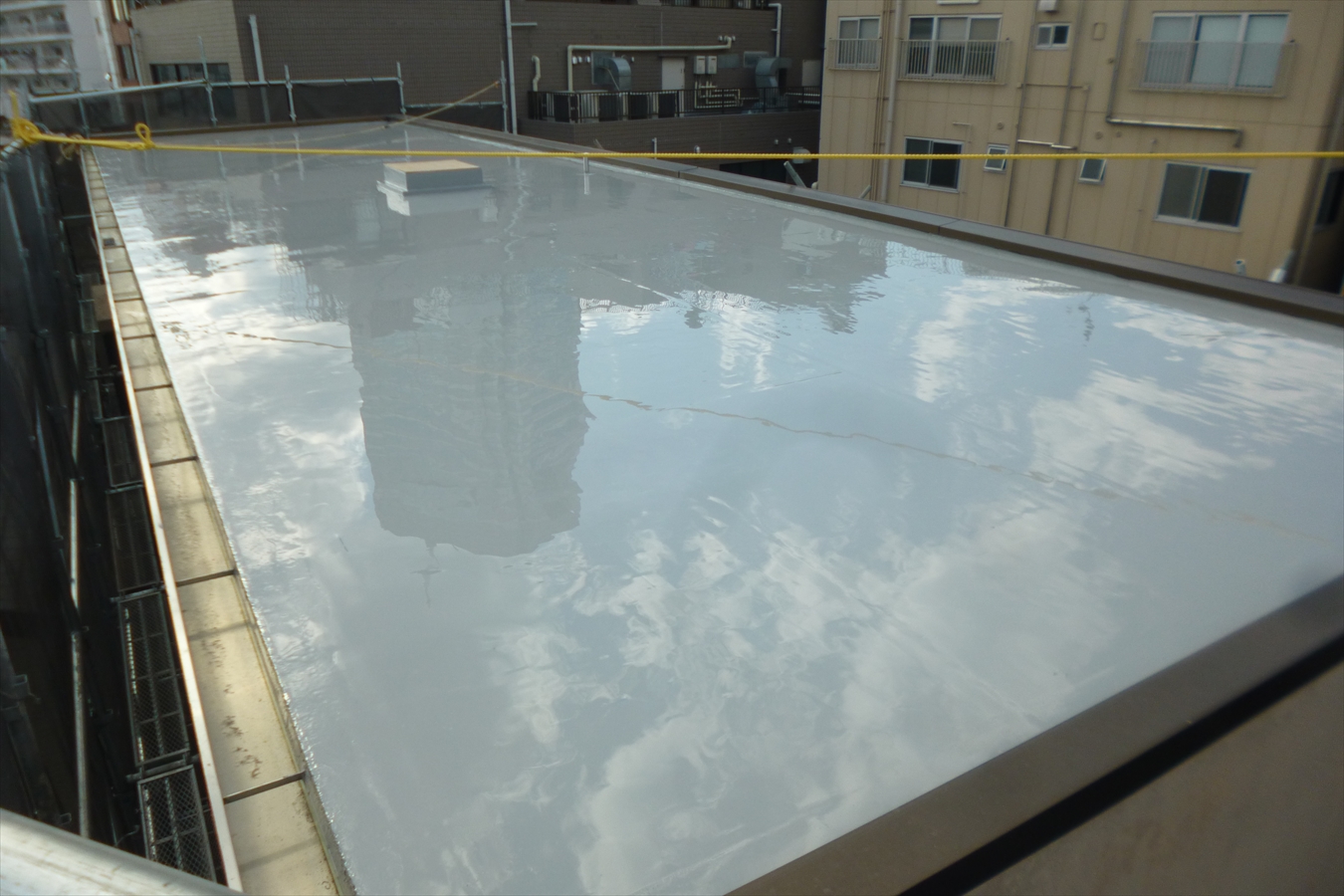
ウレタン塗布2層目
役物 ウレタン2層目塗布
1層目のウレタン塗布の時と同様、ウレタンを完全に硬化させて2層目のウレタンを入れていきます。
ウレタン防水では一定の厚みが必要だ、ということを何度か書いたと思います。それならどうして1度に沢山ウレタンを塗りつけ、1度で終わりにしないのか?と思われるかもしれません。
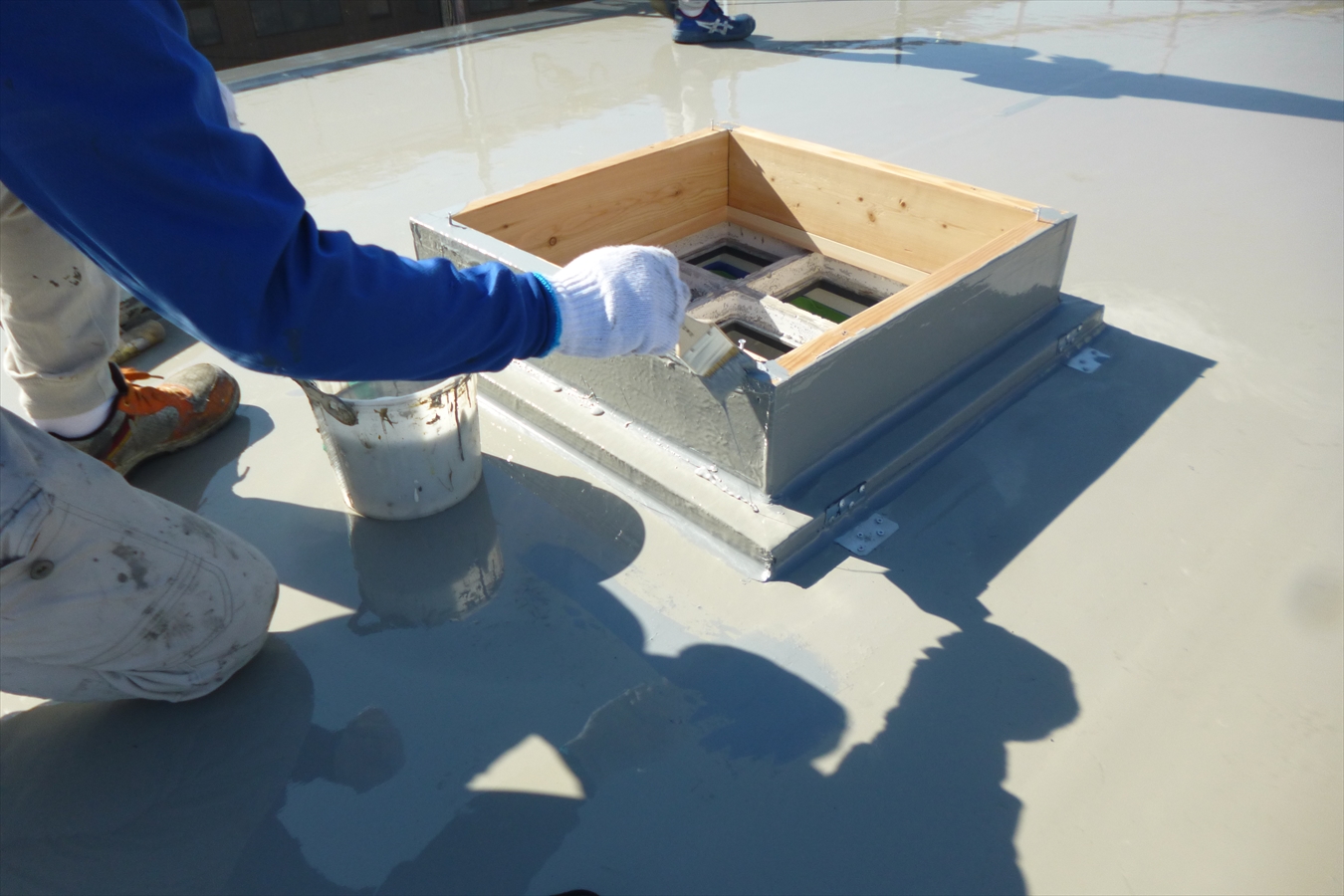
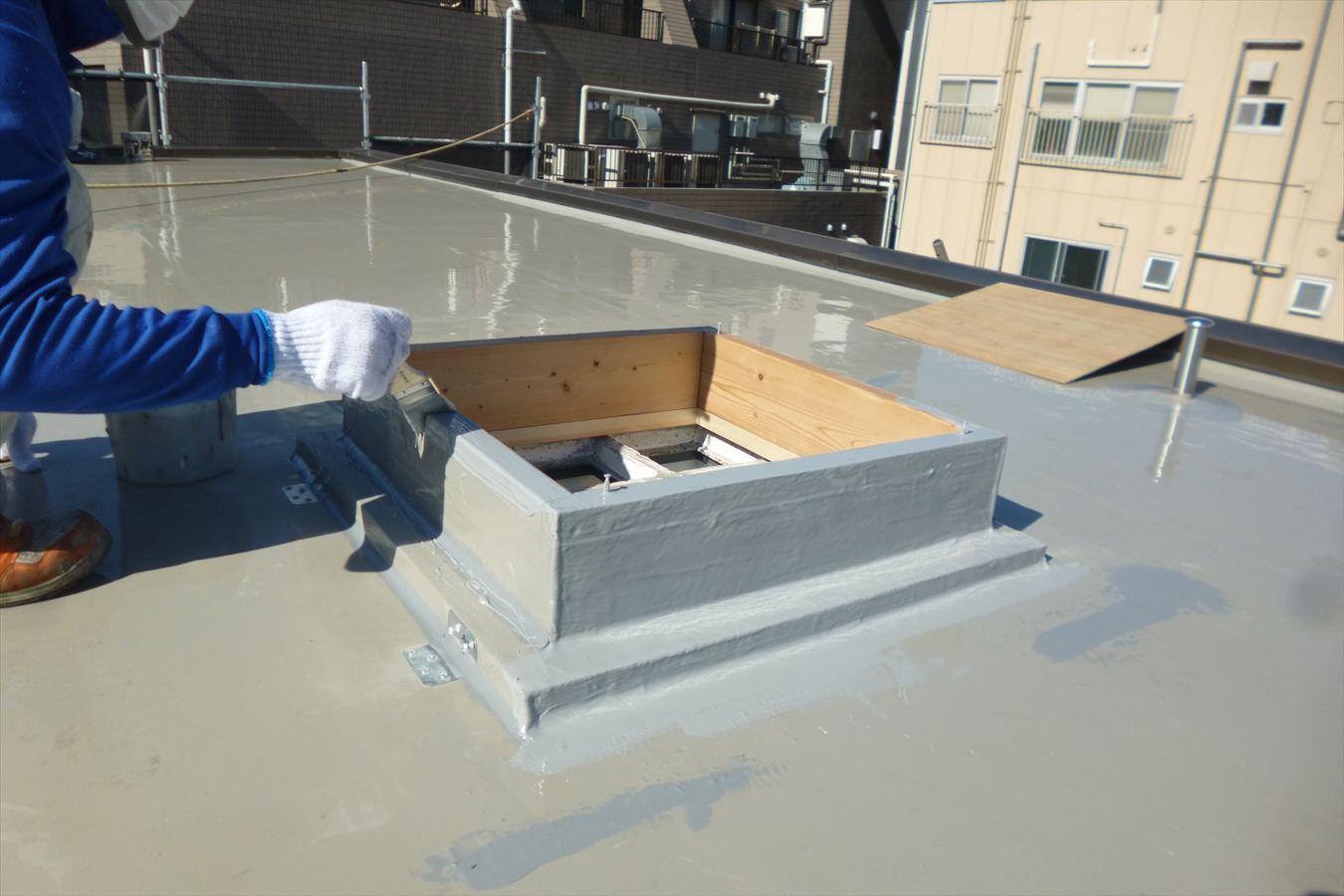
これにはちゃんと理由があり、ウレタン防水はただ厚みがあればそれだけで良いという訳ではなく、ウレタンを複数回に分けて塗ること、そして毎回完全に硬化させその上に重ねる、ということを繰り返すことで、ウレタンの層を作ることを意図しています。
ウレタンを層にすると、ただ分厚く塗ったウレタンよりも強度を得られるというメリットがあるため、わざわざ2回に分けて塗っているのです。
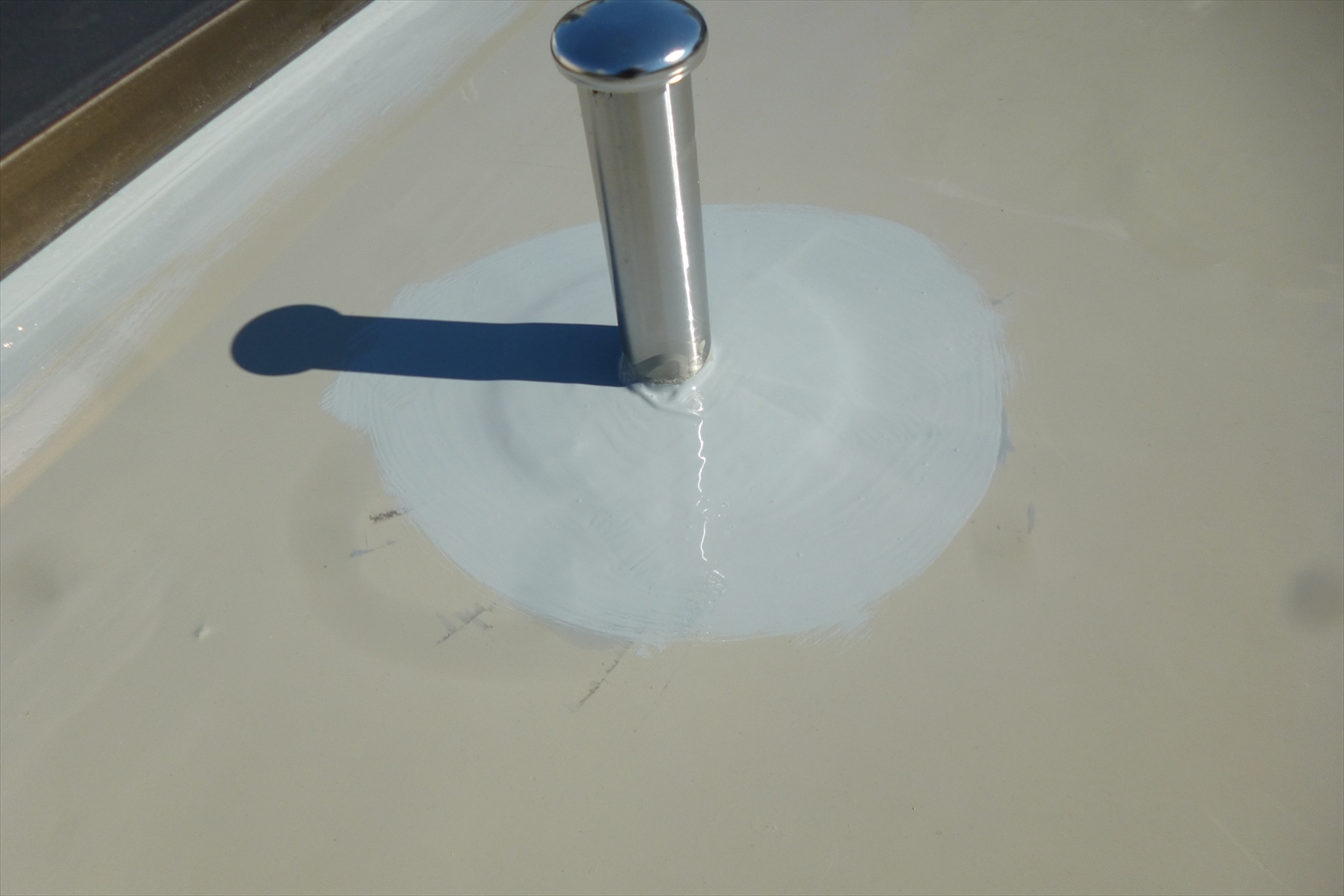
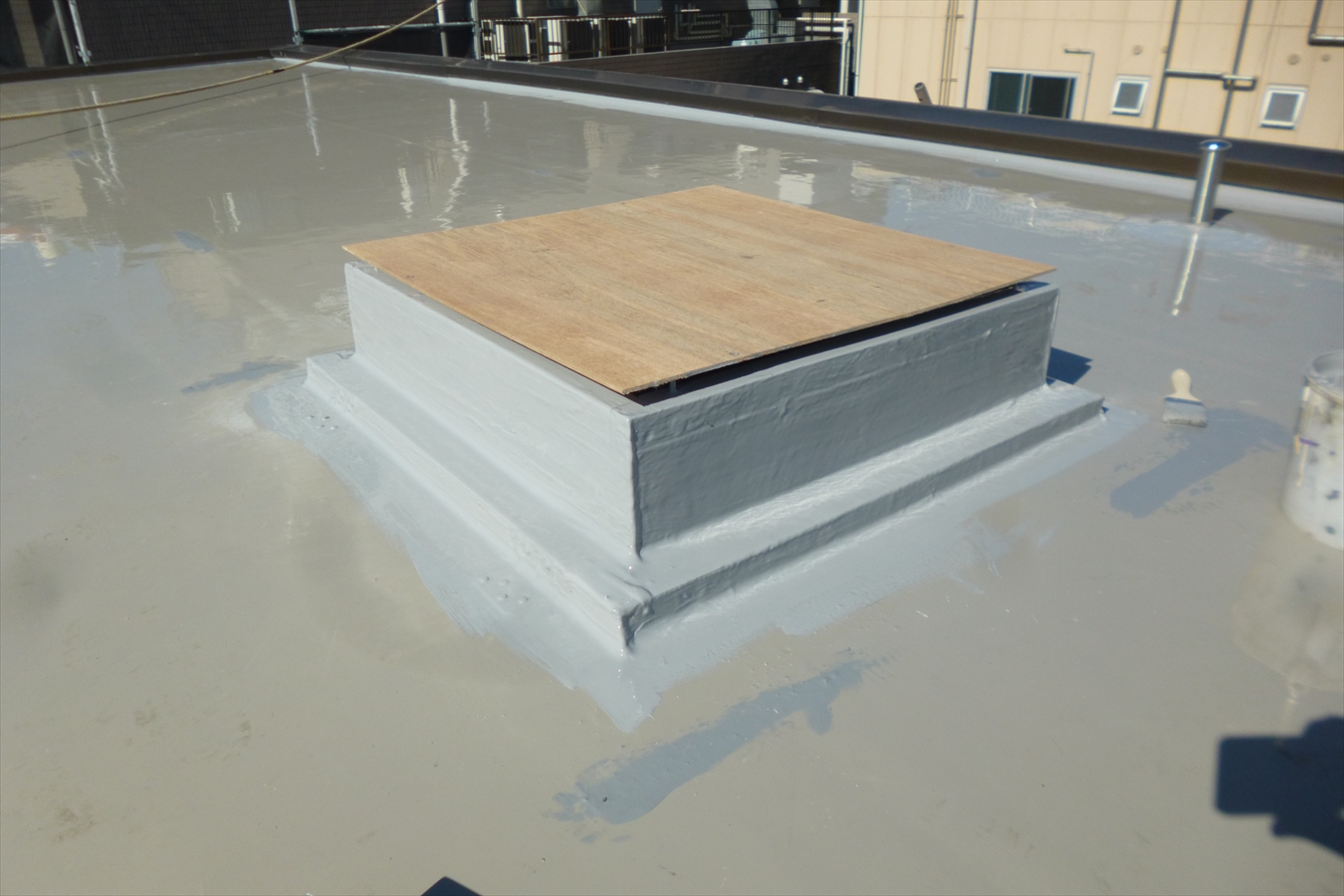
立ち上がり ウレタン塗布 2層目
役物周りとアルミ笠木の下の立ち上がりの2層目は、1層目の時と同じようにブレンドしたウレタンを塗っています。これは立ち上がりにゴムベラを使った作業ができないことと、両方とも立ち上がり材を使う箇所だからです。
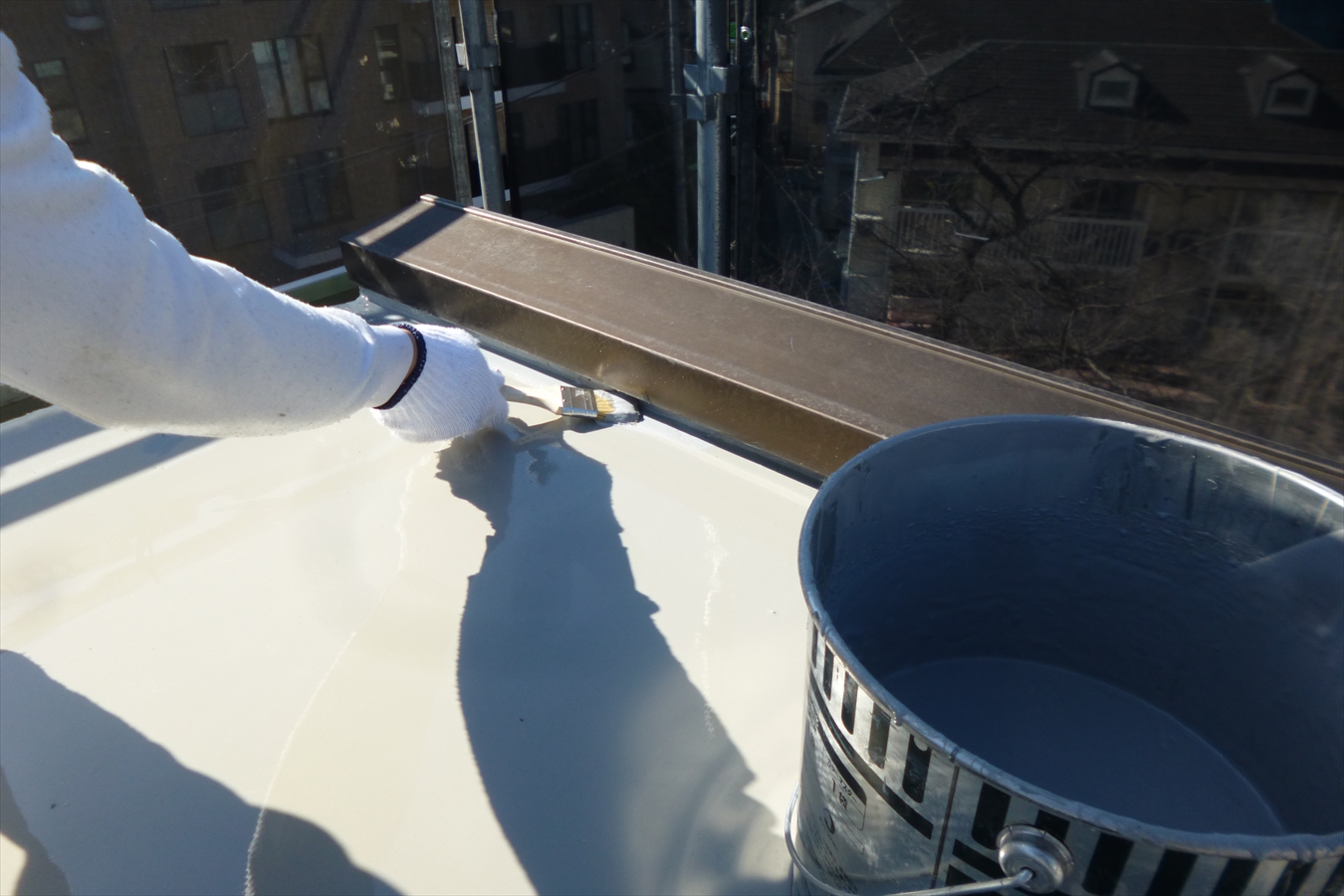
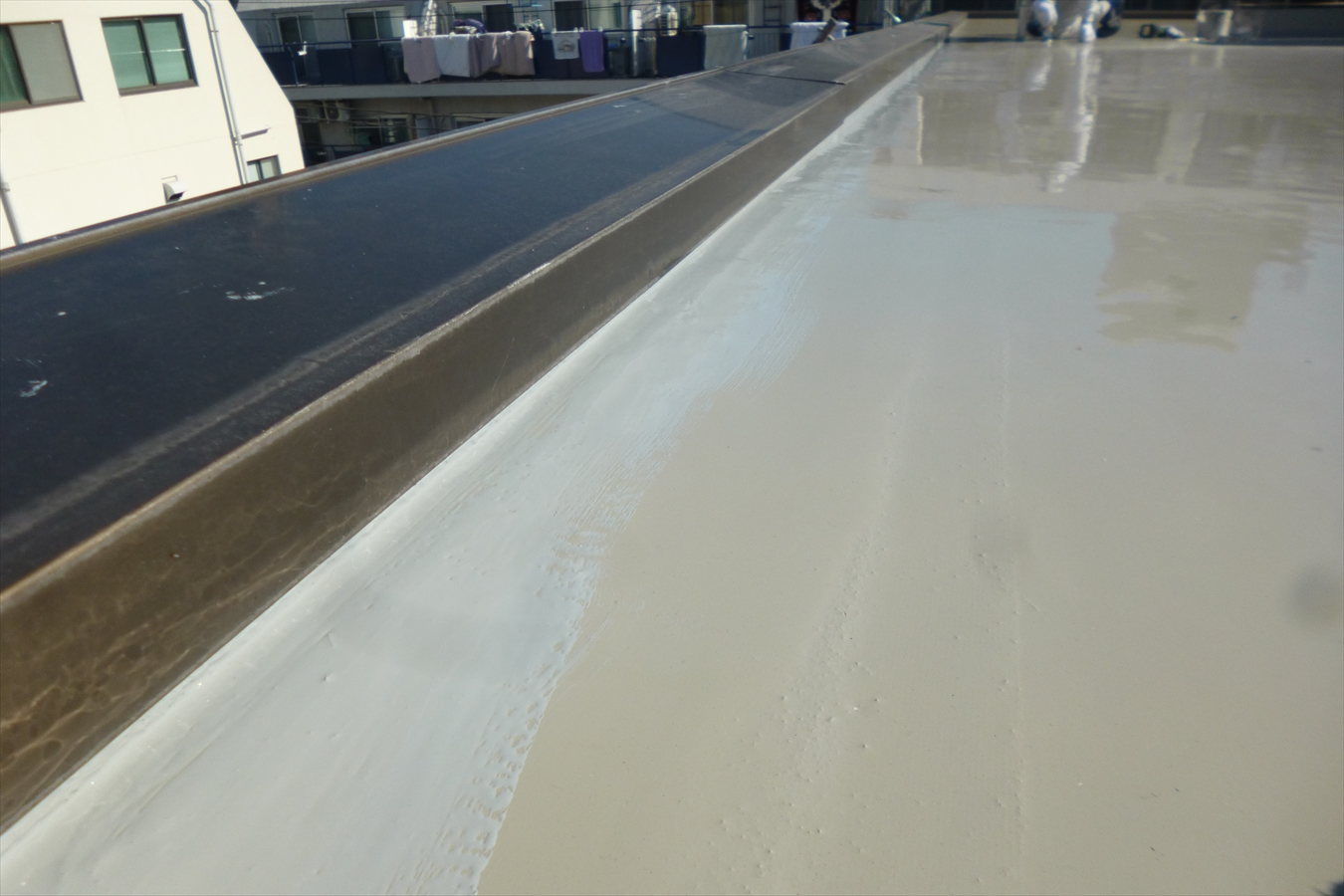
役物はトップライトの枠しか無く、クロス貼り付けと違いウレタンを塗布するだけなら大して時間のかかるものではありません。そして十分な厚みをつけることができるのであれば、ブレンドしたウレタンでも問題ないため、同じ材料で一気に仕上げています。
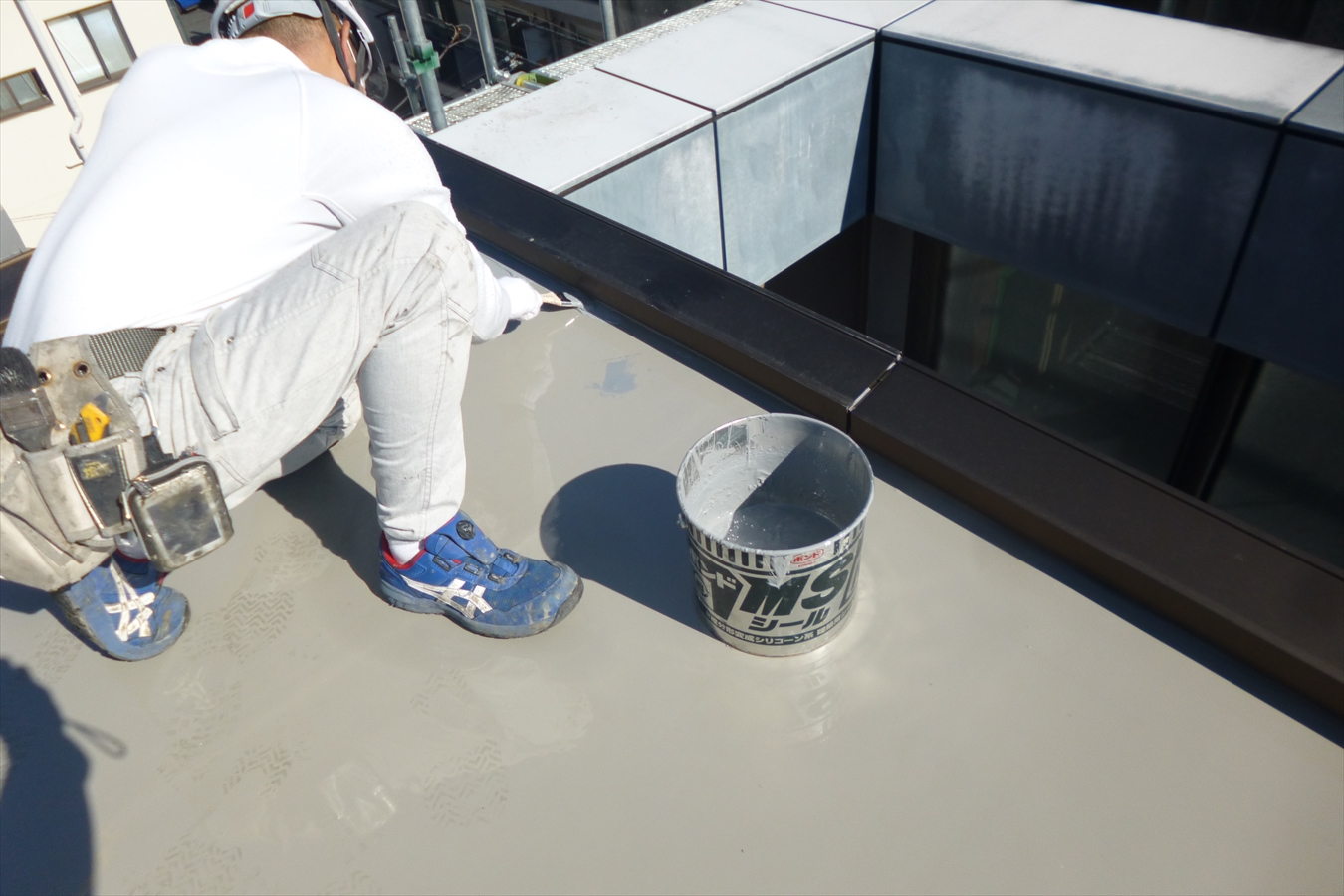
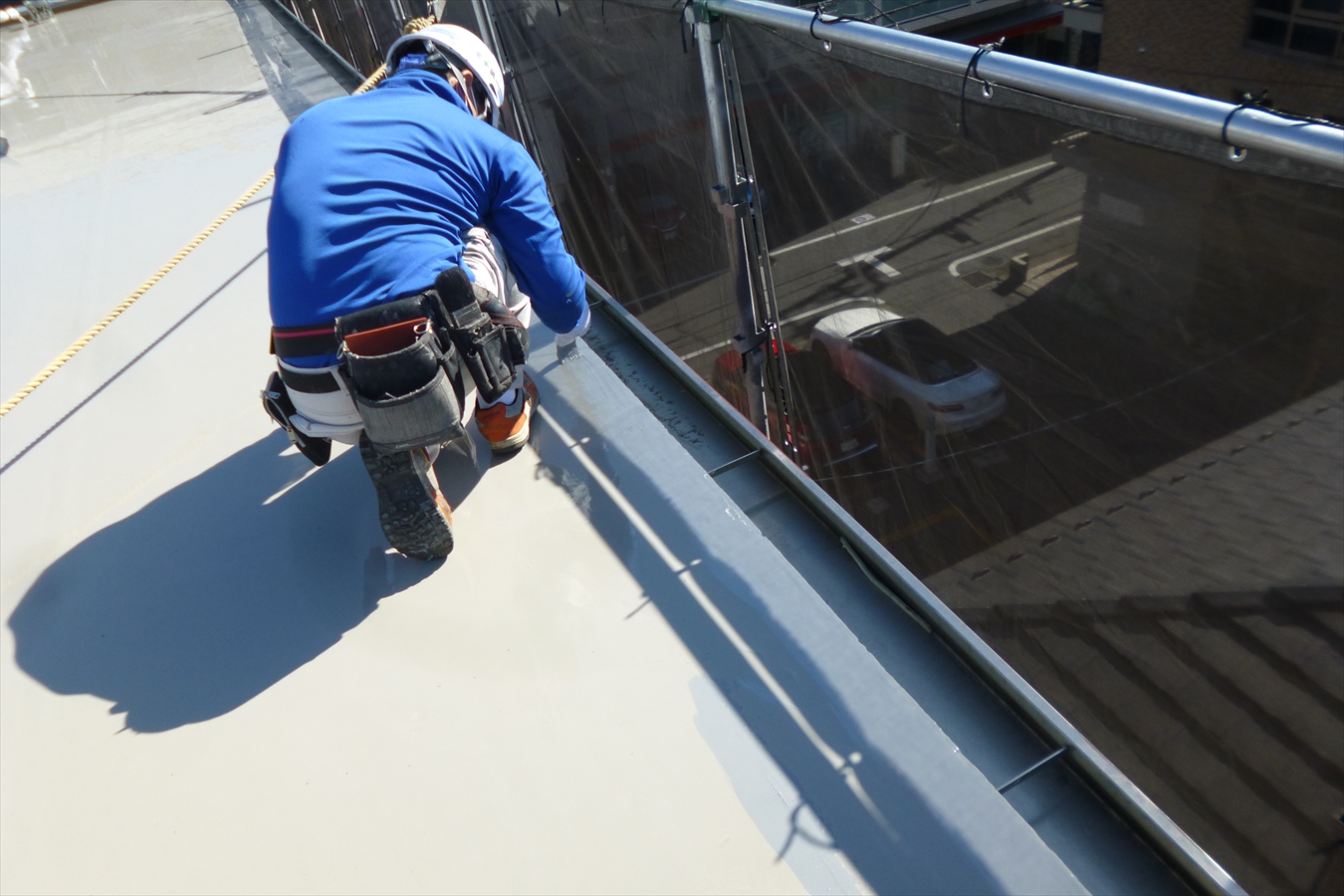
土間 ウレタン塗布 2層目
役物と立ち上がりの2層目が終わったら土間のウレタン2層目を流していきます。ウレタンの2層目は1層目と同じことを繰り返すだけで問題ありません。
今回も屋上の出入り口の遠い、勾配の低いところからウレタンを流していきます。また、流す場所によって小手とローラーを使い分けて作業するのも1層目の時と同じです。
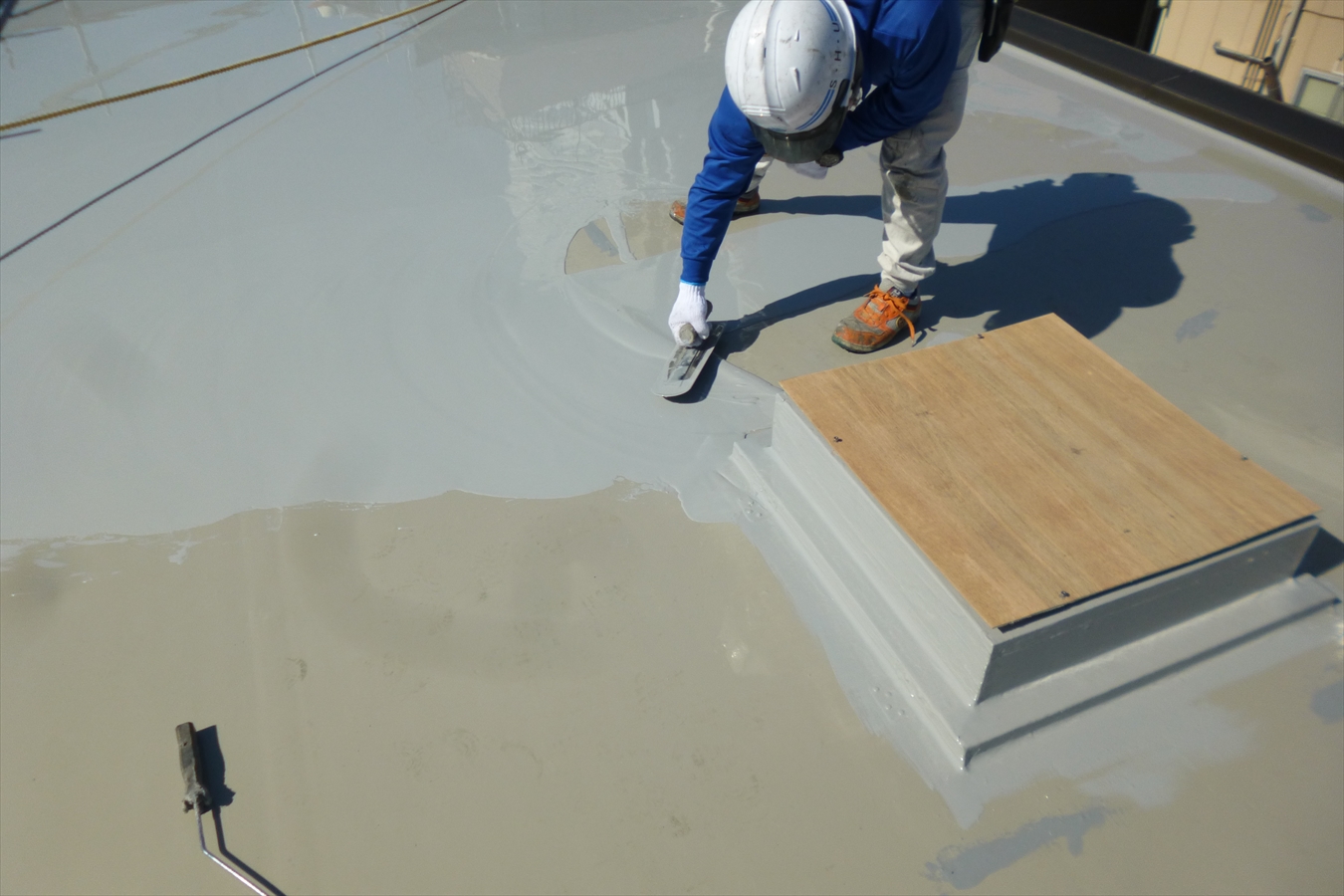
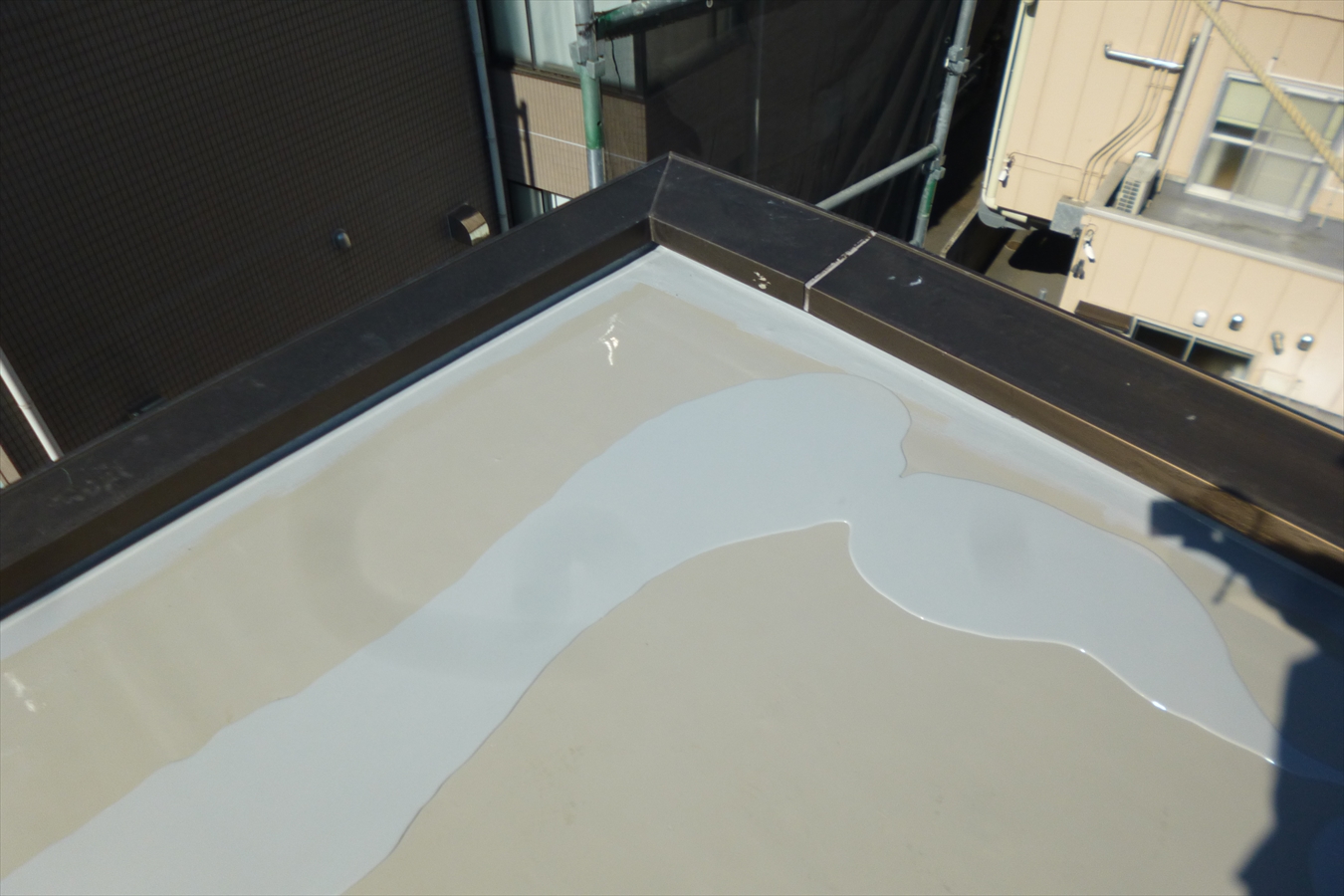
流し終わったら再び時間を置いて、ウレタンが完全に硬化するのを待ちます。
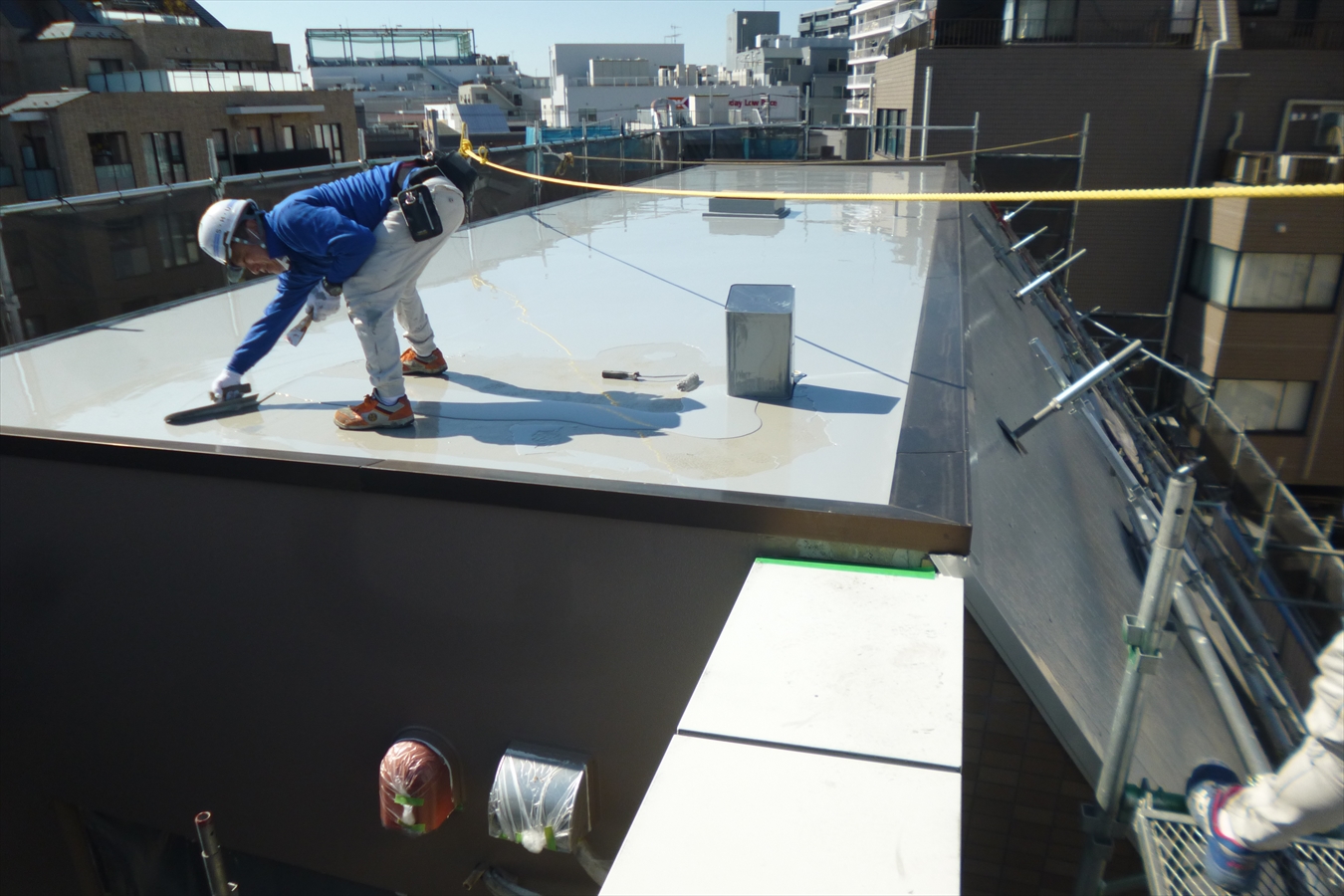
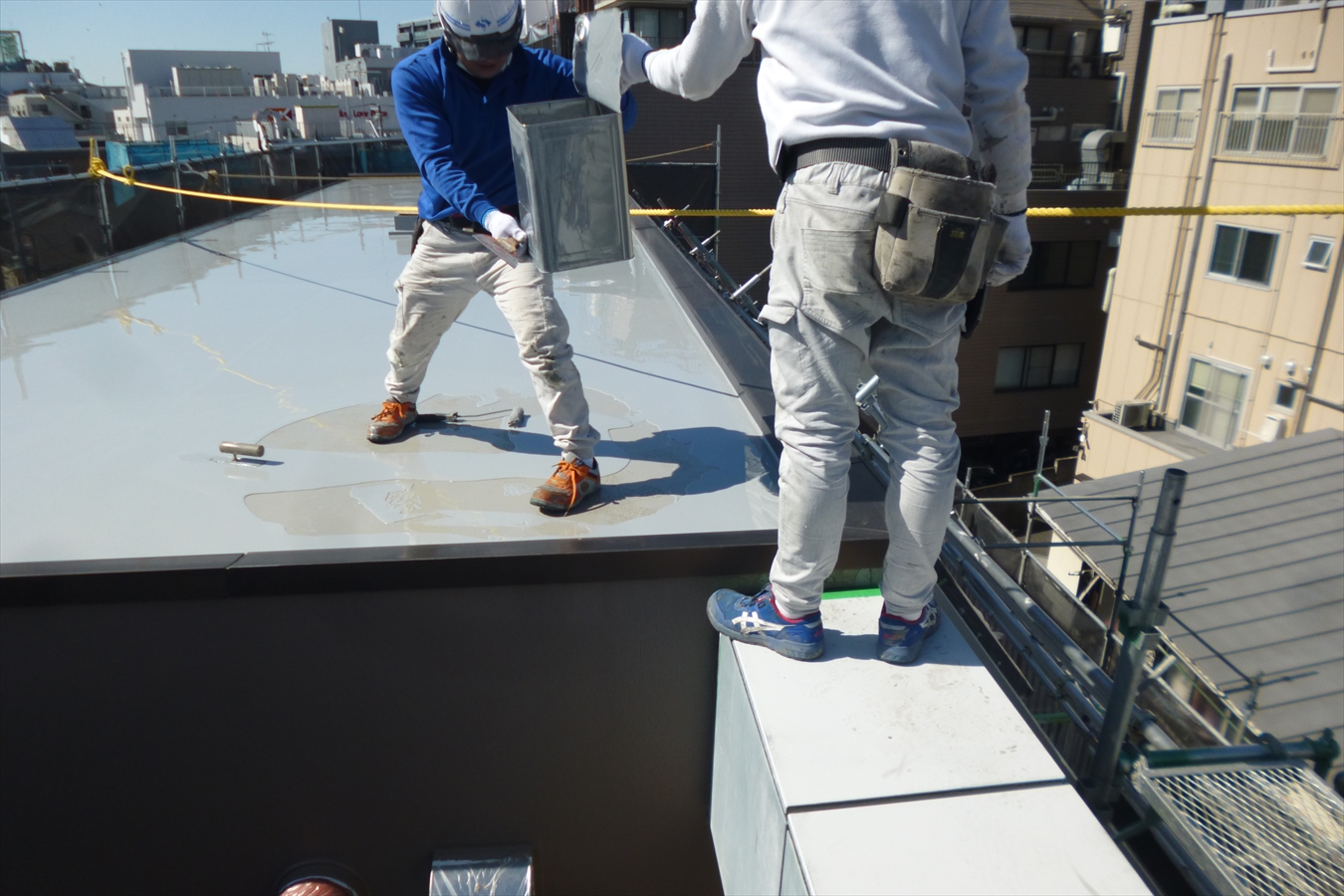
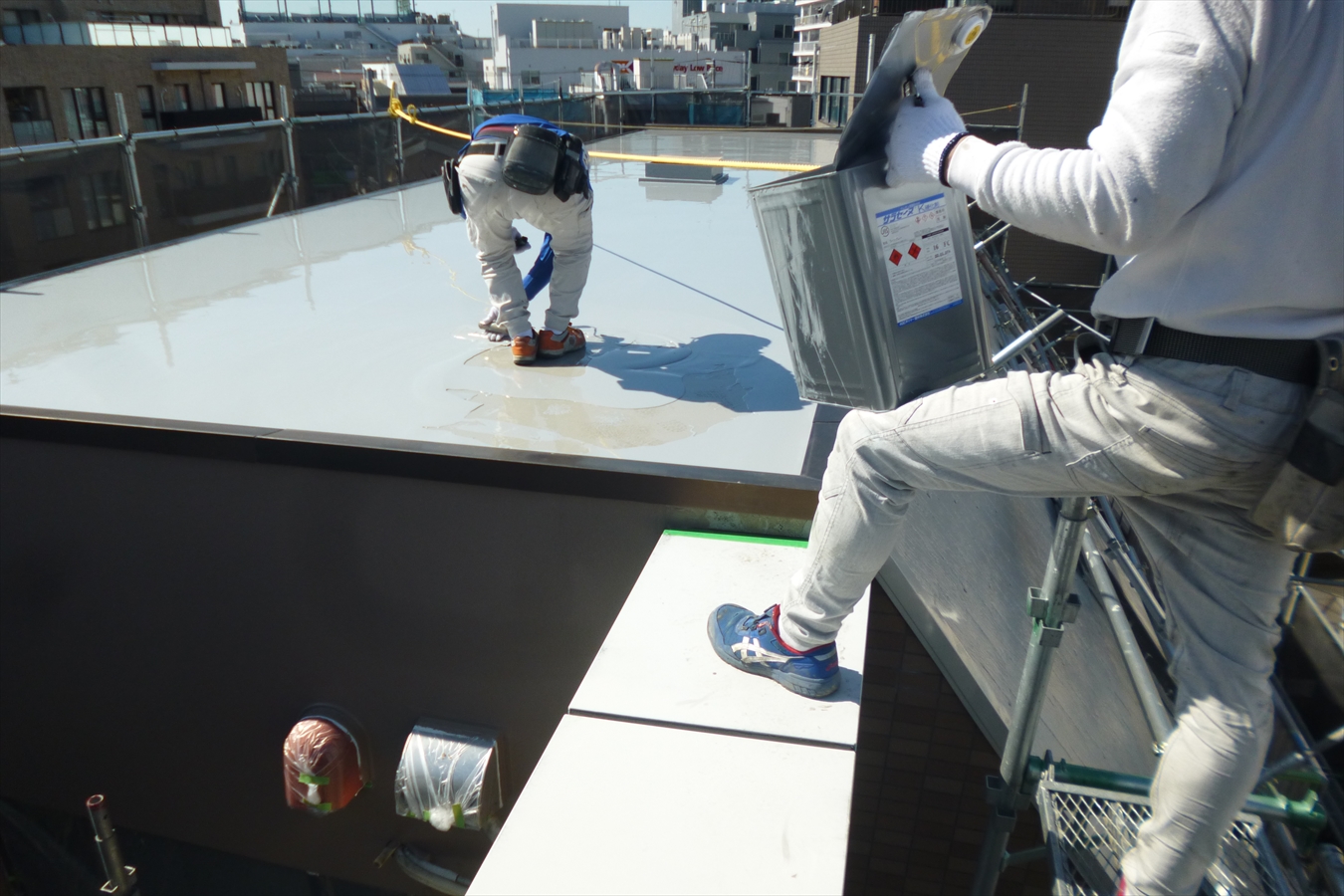
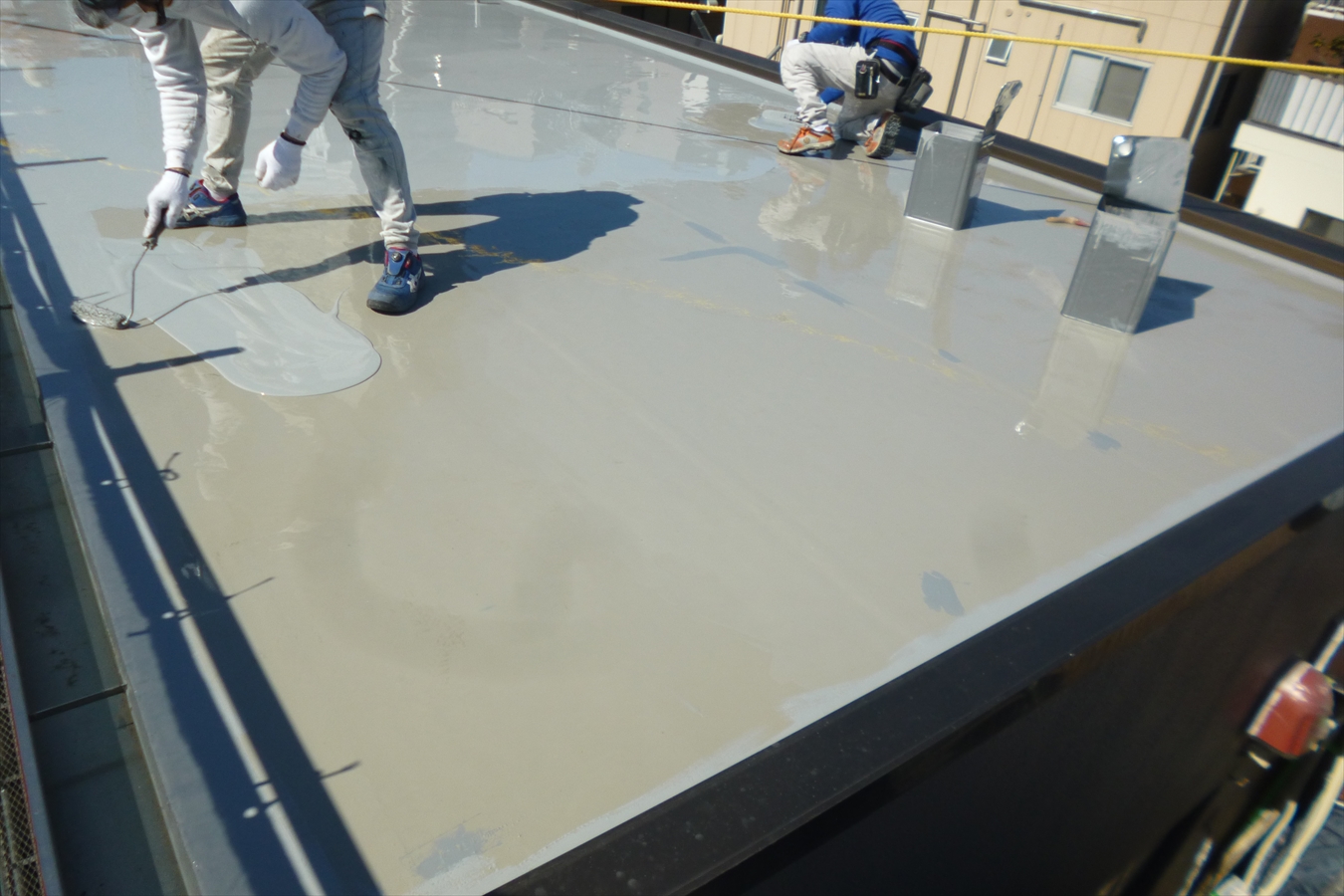
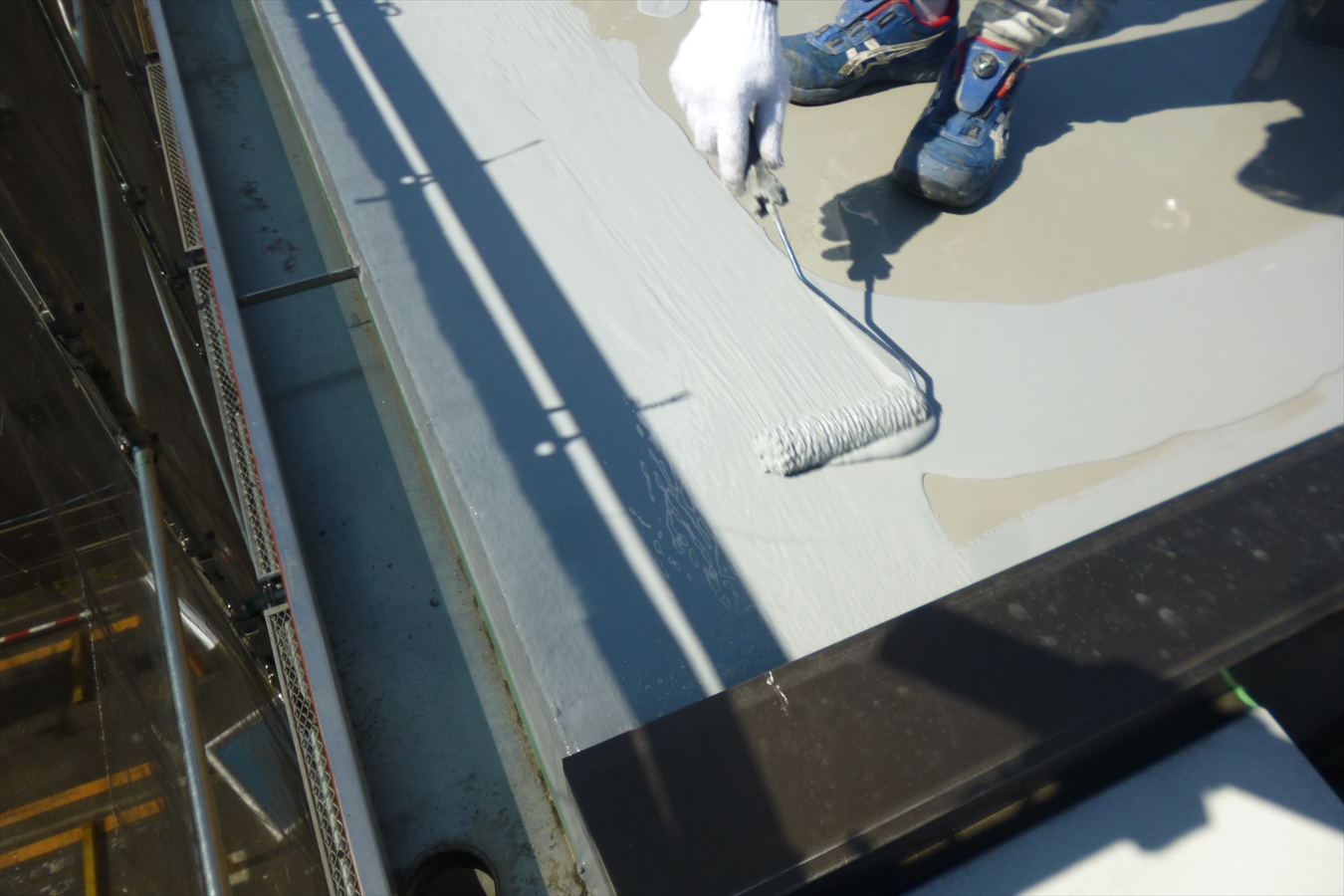
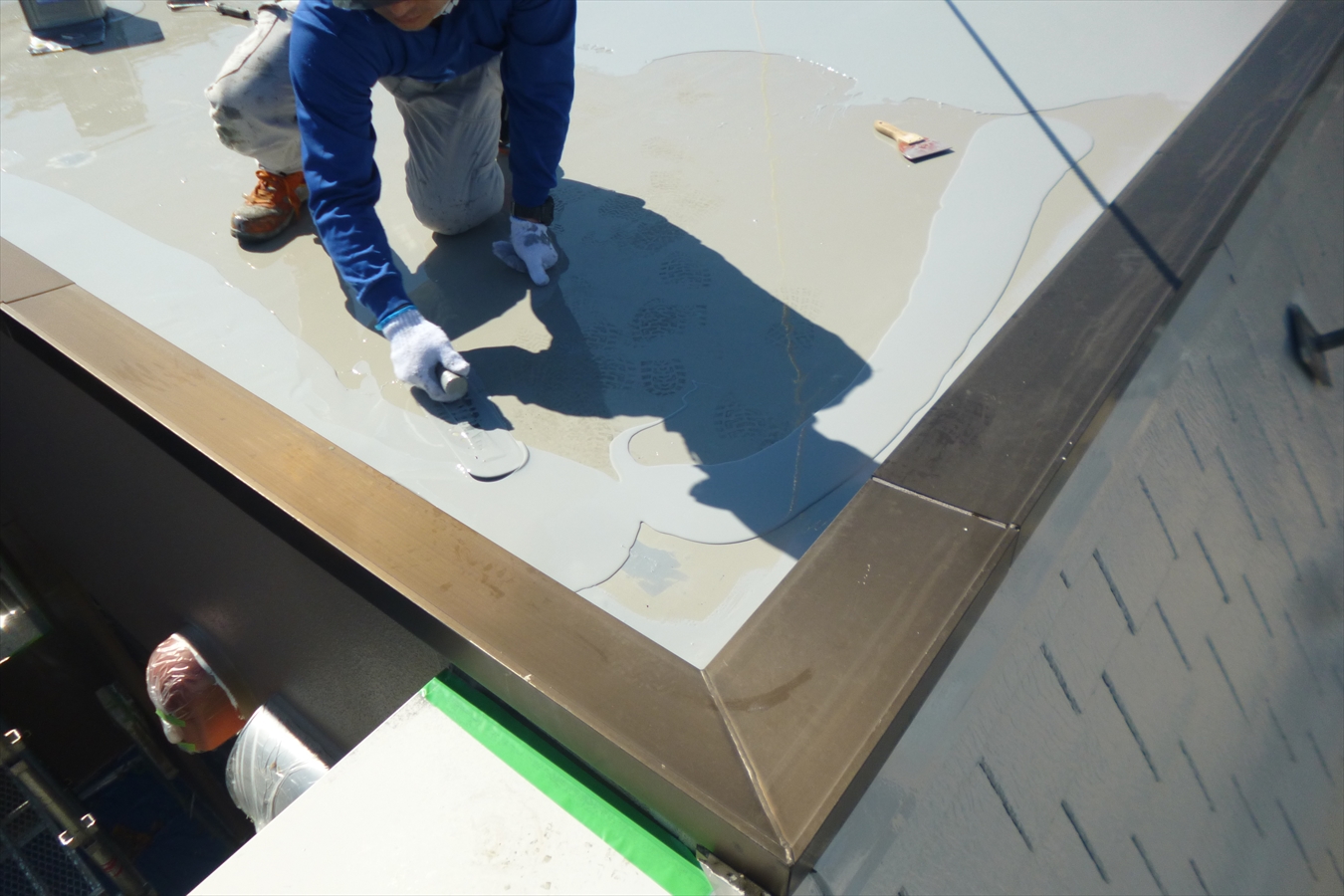
トップコート塗布
施工前
ウレタン2層目の硬化が済んだら、最後にトップコートをウレタンの表面に塗る作業をして防水工事は完了となります。
トップコートとはウレタンの保護剤のこと。ウレタンは紫外線に弱く、保護剤無しの状態で日にさらされ、風雨を受け続けるとあっと言う間に劣化してしまうものです。このトップコートはそれらのダメージからウレタンを守る役割を担う材料となっているため、ウレタン防水工事では必須となっています。
今回の防水工事で実際に使用したトップコート、サラセーヌTです。これが一般的な防水工事で使われるトップコートとなります。もう一種類、フッ素と呼ばれるトップコートも存在していますが、こちらは非常に高価な材料のためあまり使われることはありません。ウレタンが2層入り、完全に硬化させた状態の屋上の写真です。これからウレタンが塗られた箇所全部にこのサラセーヌTを塗っていきます。

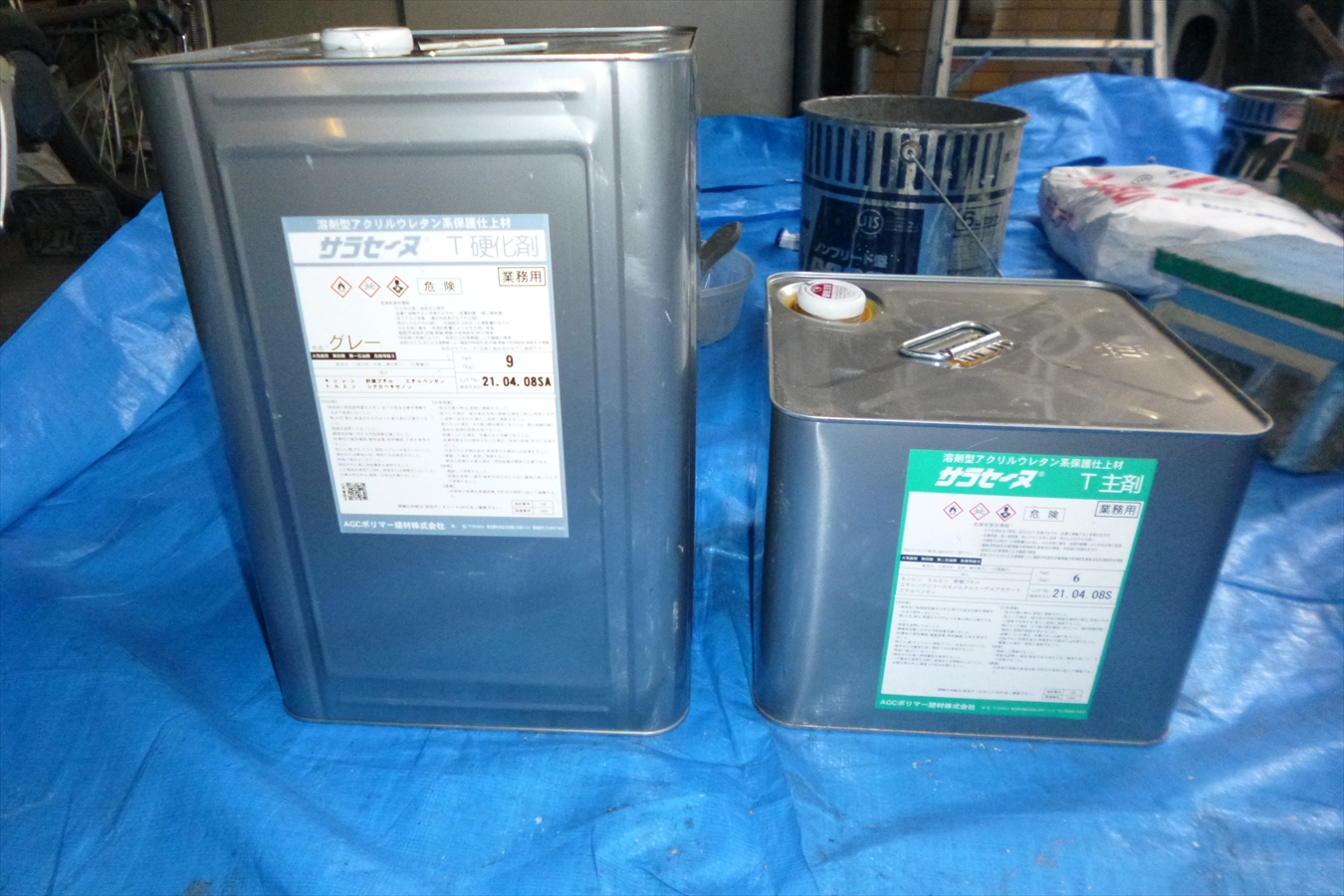
役物
下地補修
早速サラセーヌTを塗る、といきたいところですが、塗る前にしなくてはいけない作業があります。それは下地補修です。屋上防水をしていると、1層目、2層目のウレタンを流した翌日など、トンボやハチ、ヤモリなどの虫がウレタンに貼り付いていることがよくあります。今回それらは幸いありませんでしたが、もしあった場合、当然のことながら対応する必要があるため、ウレタンの下地補修は欠かせない工程となっています。
虫がついていることはありませんでしたが、今回トップライトの枠を固定するためにネジ止めされています。ネジ山のような出っ張り箇所は、ウレタンが傷つき、破れやすい箇所となるためシール材などで補強してやる必要があります。今回はオートンのクイックシールを使いネジ山の補強をしました。これは通常のシールと違い、速乾性のシールのため、長時間待って硬化させる必要がありません。
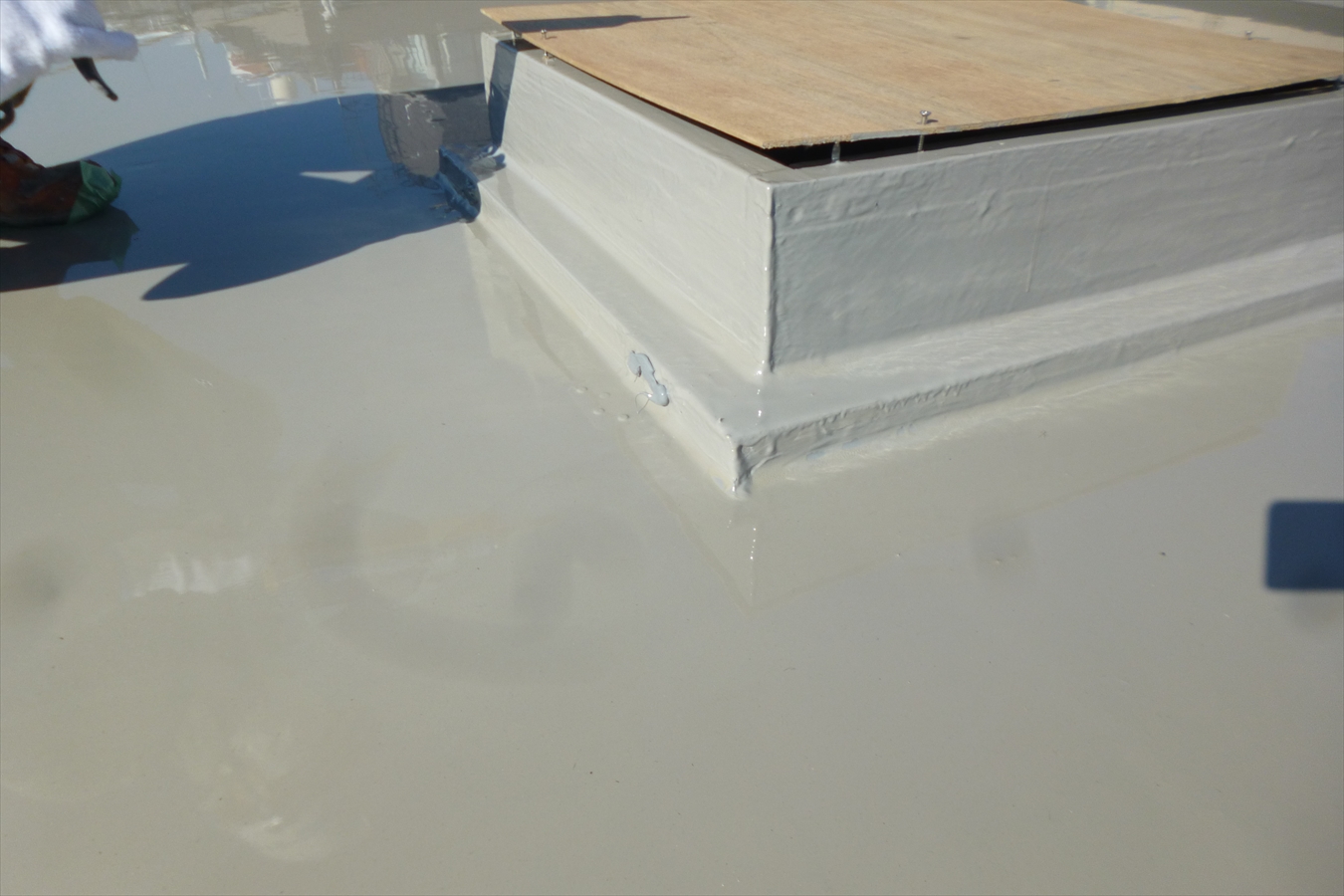
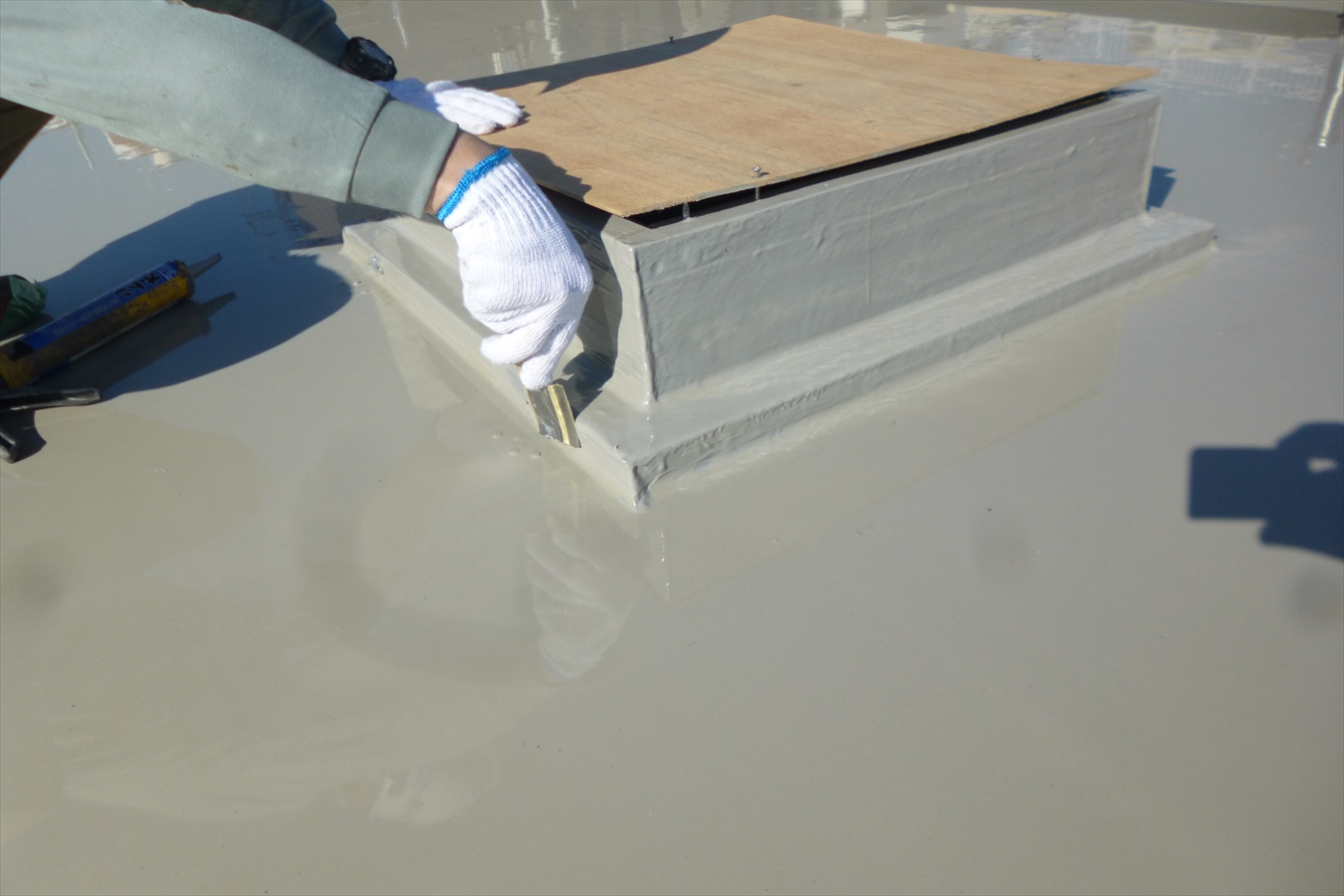
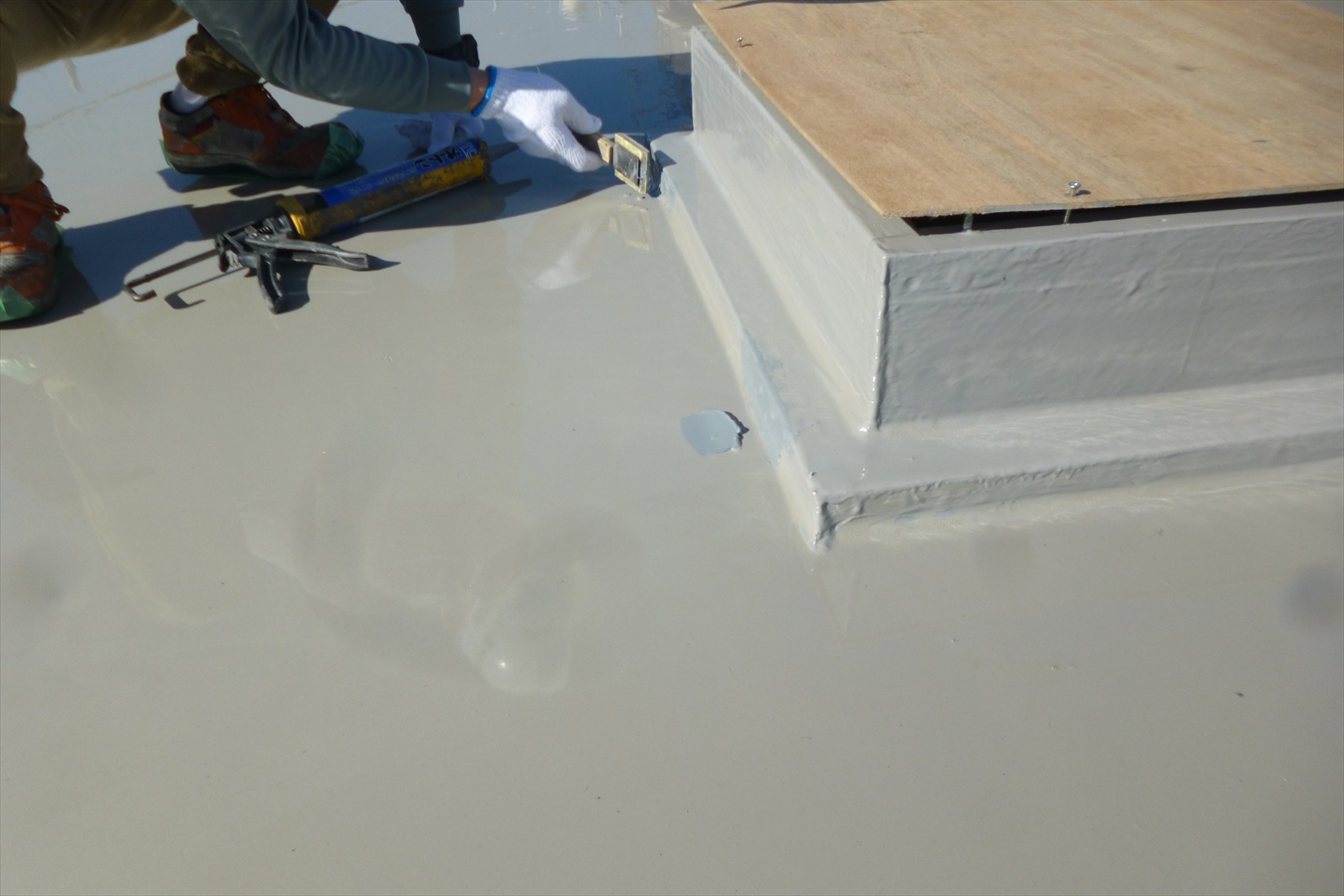
役物 トップコート塗布
下地補修が終わったらトップライトの枠と、その周りからサラセーヌTを塗っていきます。トップコートを塗ること自体はさほど難しい作業ではありません。刷毛とローラーを使い分けながら枠のウレタンの上からサラセーヌTを塗っていきます。
プライマーの時は、この枠の下のシールを充填していなかったことから、プライマーが中へ流れ込む可能性を考えて刷毛のみで仕上げていましたが、今はシールは勿論、ウレタンを巻いた後で内部へ流れ込む心配がないのでローラーも使用しています。
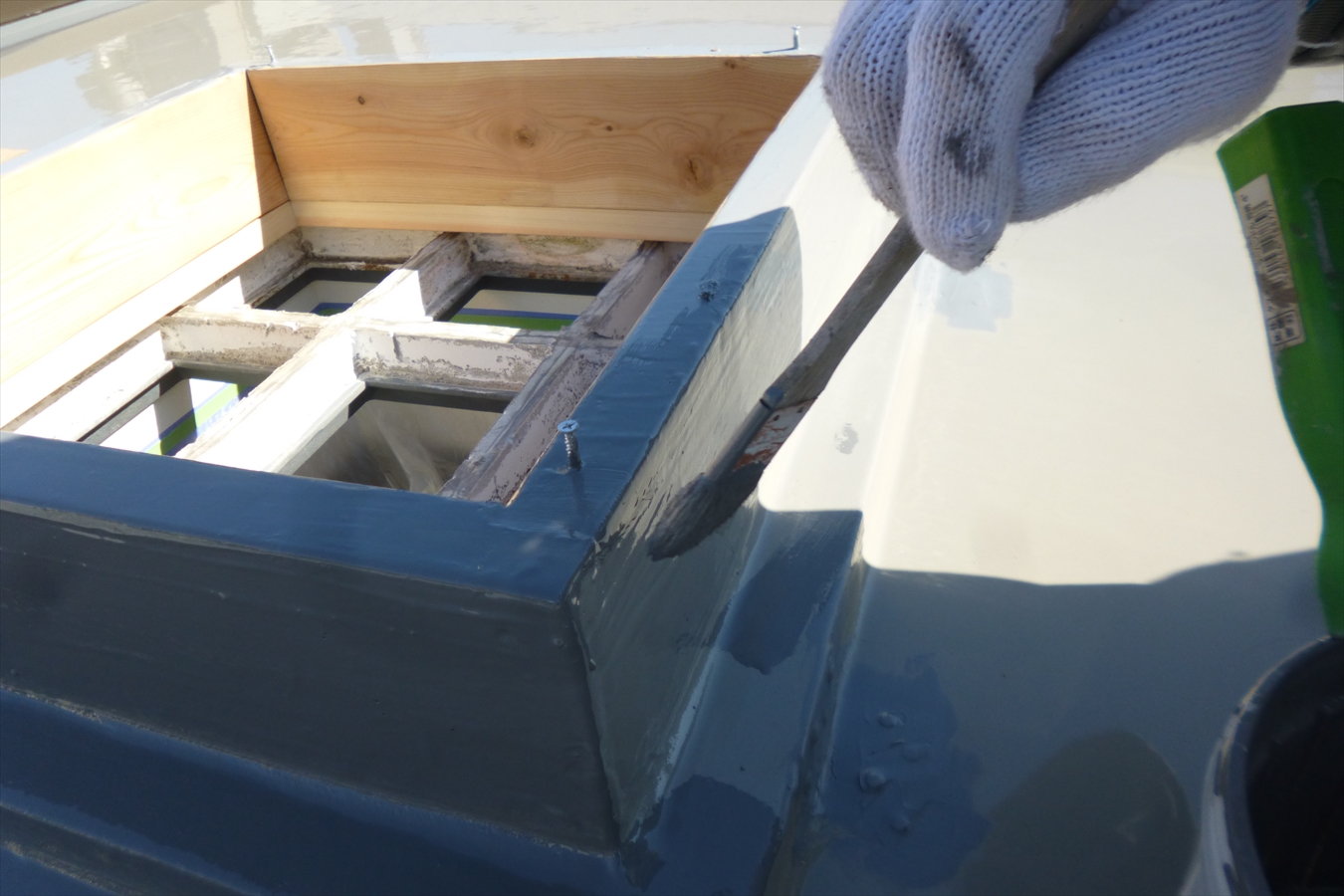
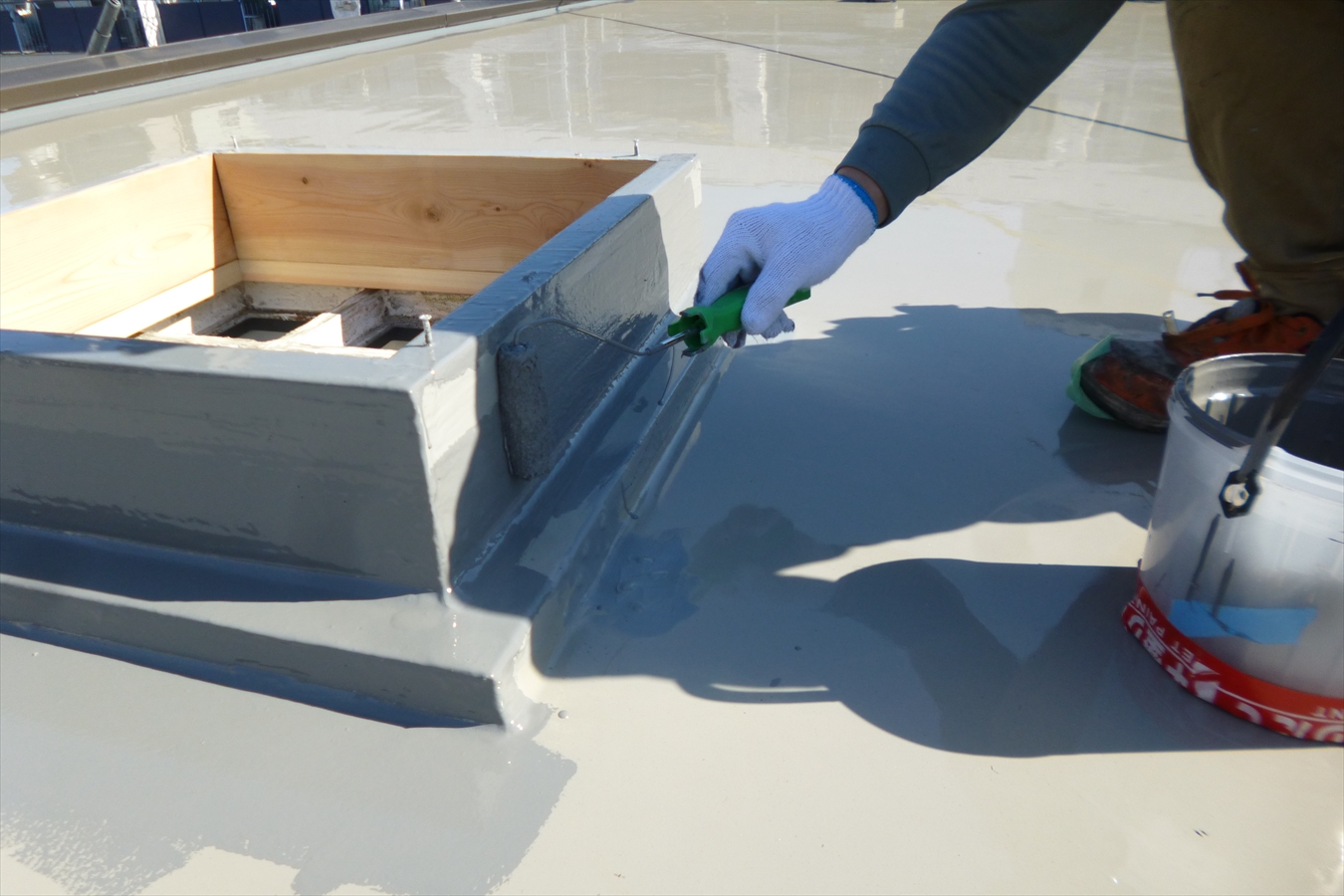
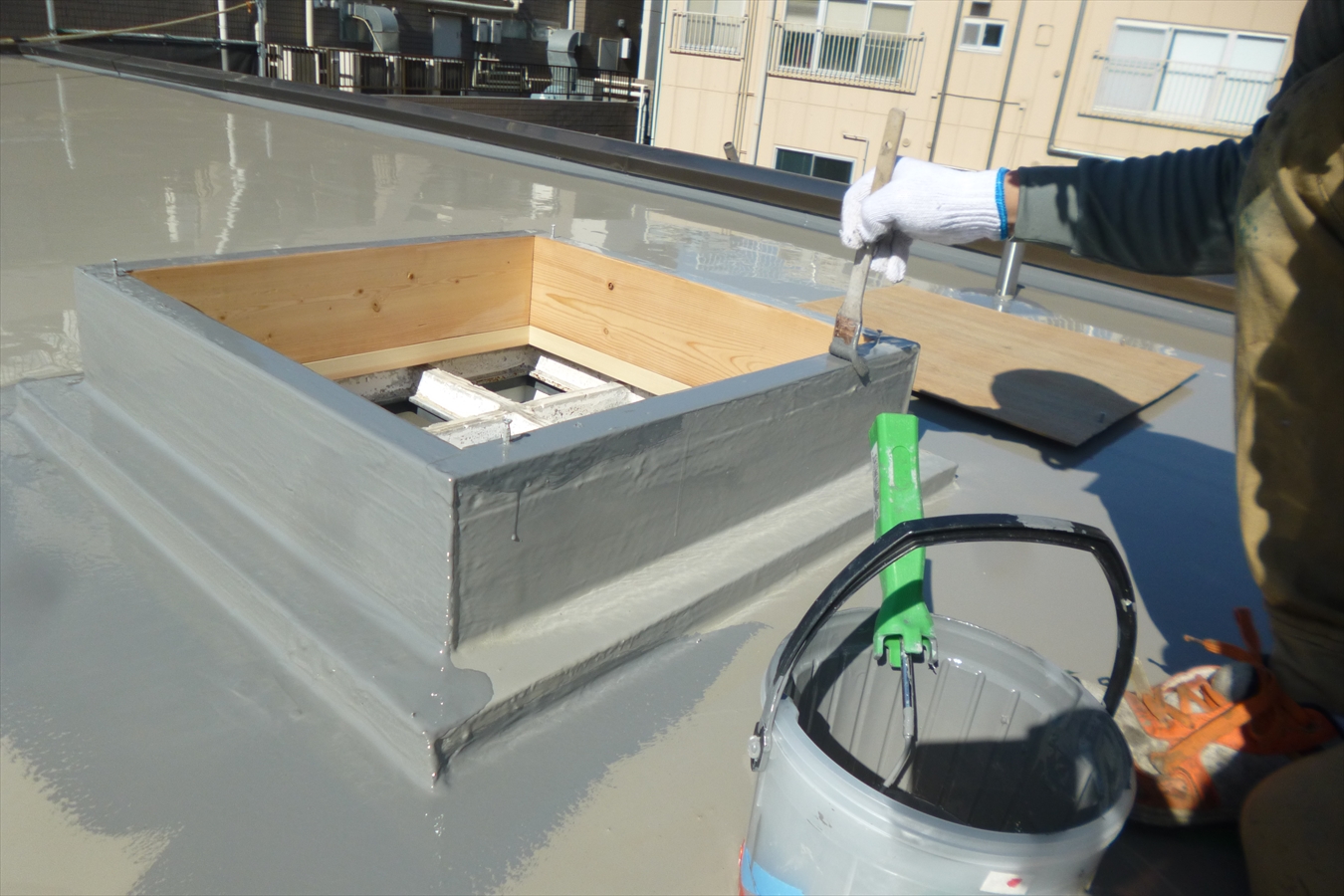
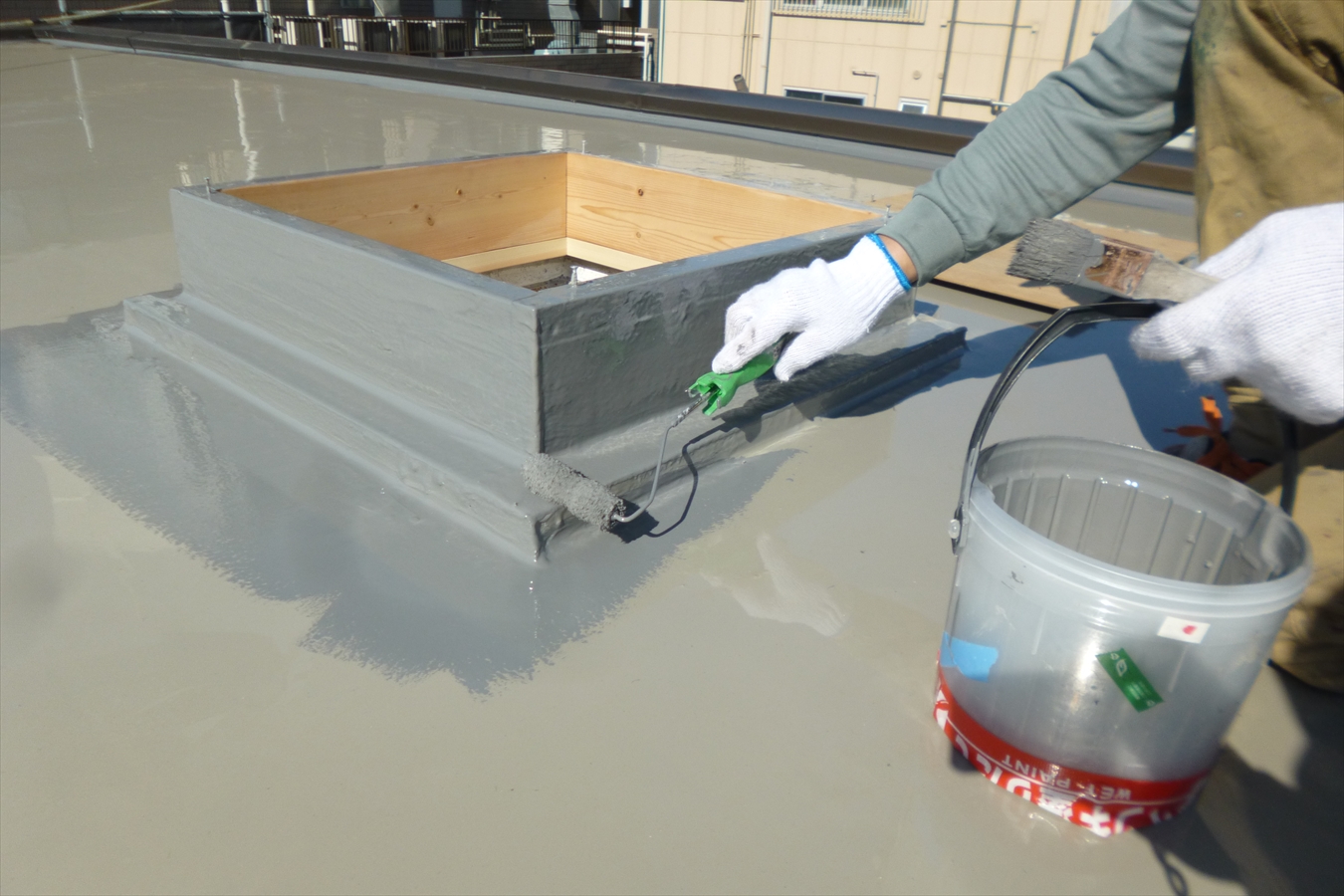
立ち上がりトップコート塗布
ウレタン塗布の時と同じ流れで、トップライトの枠のトップコートを塗ったら周囲の立ち上がりの塗り込みをします。
ここでも刷毛を使い塗っていきます。立ち上がりだけでなく、土間もローラーの幅一本分塗っておきます。こうすることで土間の塗り込みのとき、アルミ笠木にローラーをぶつけて汚してしまうことを避けられるようにしています。
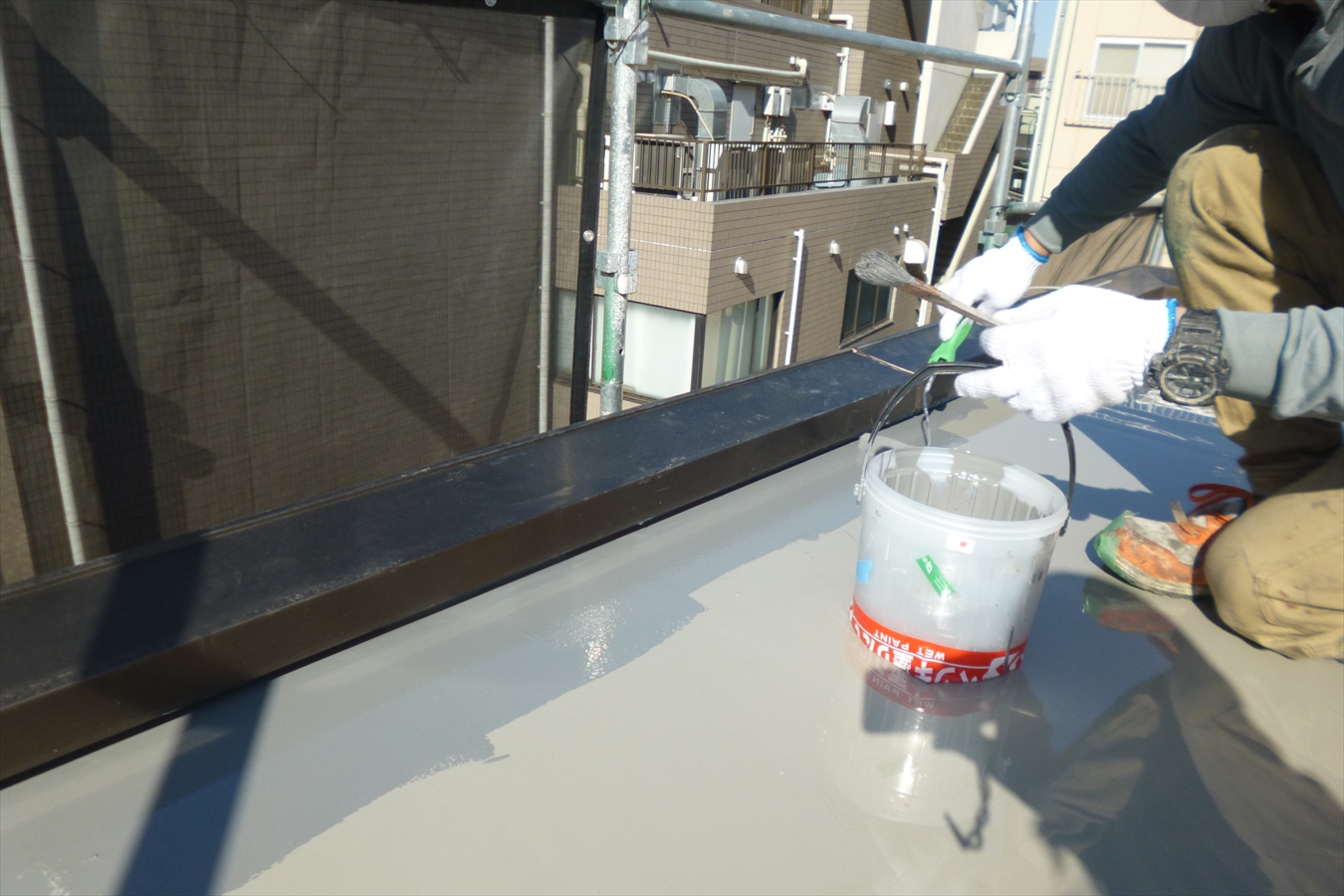

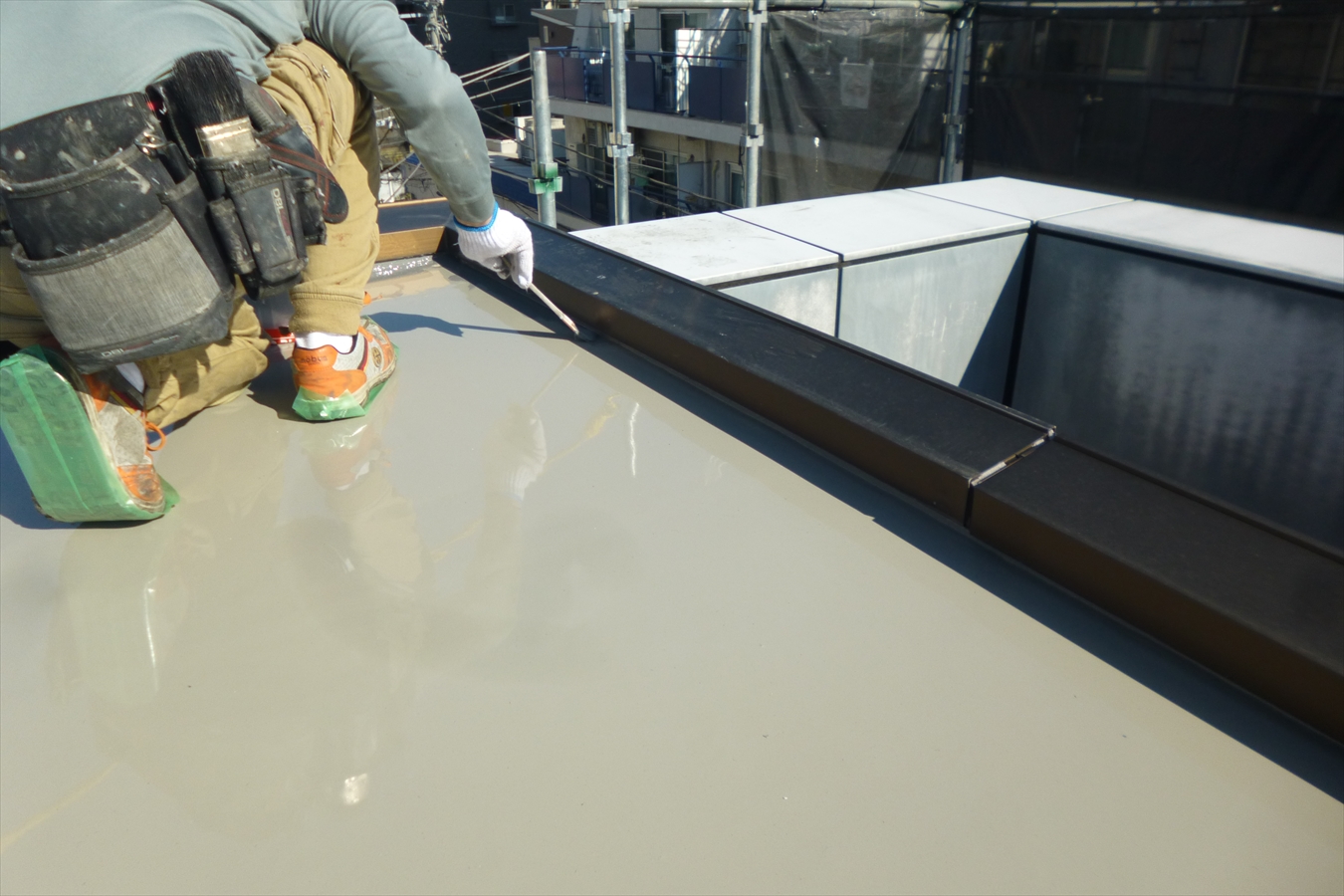
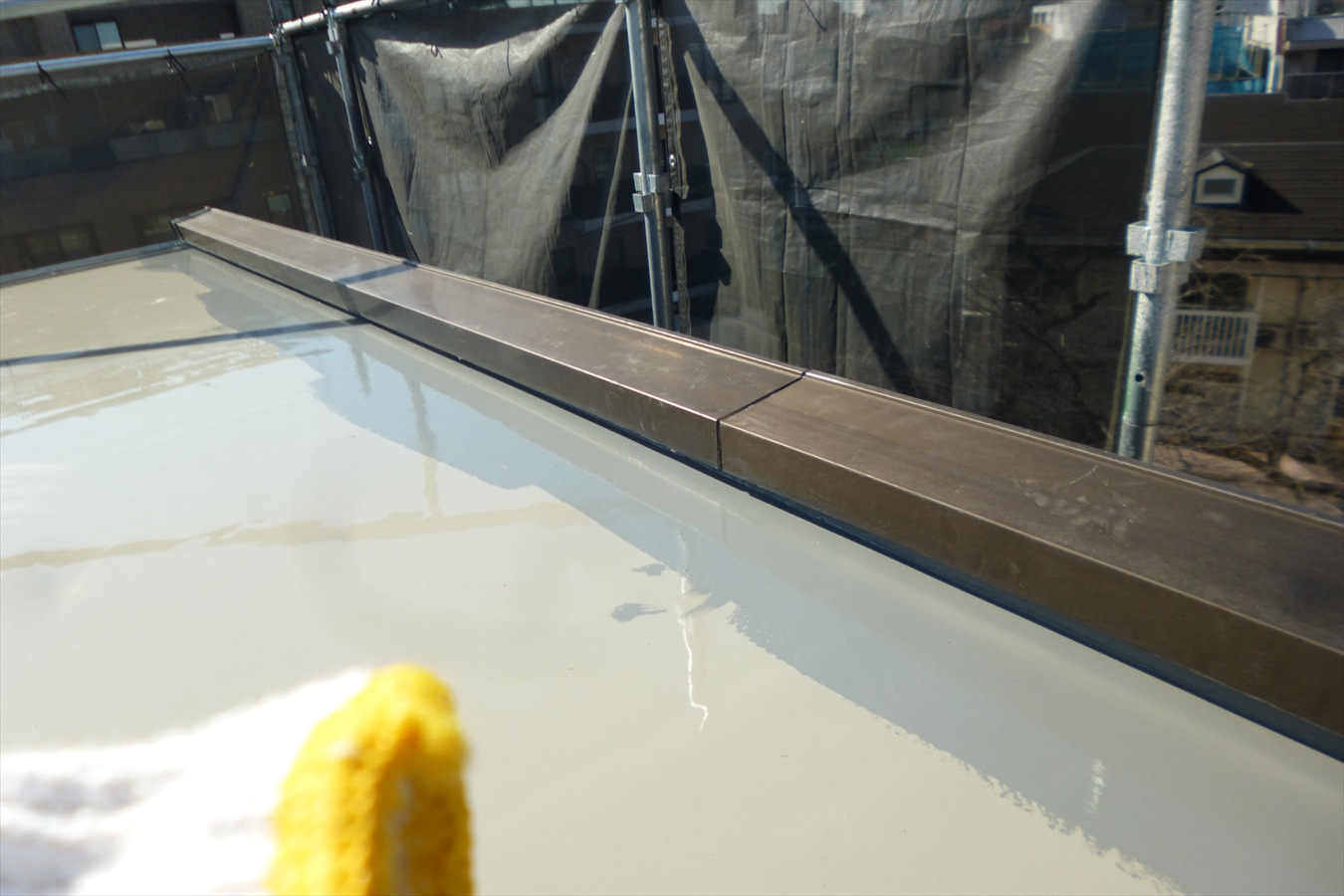
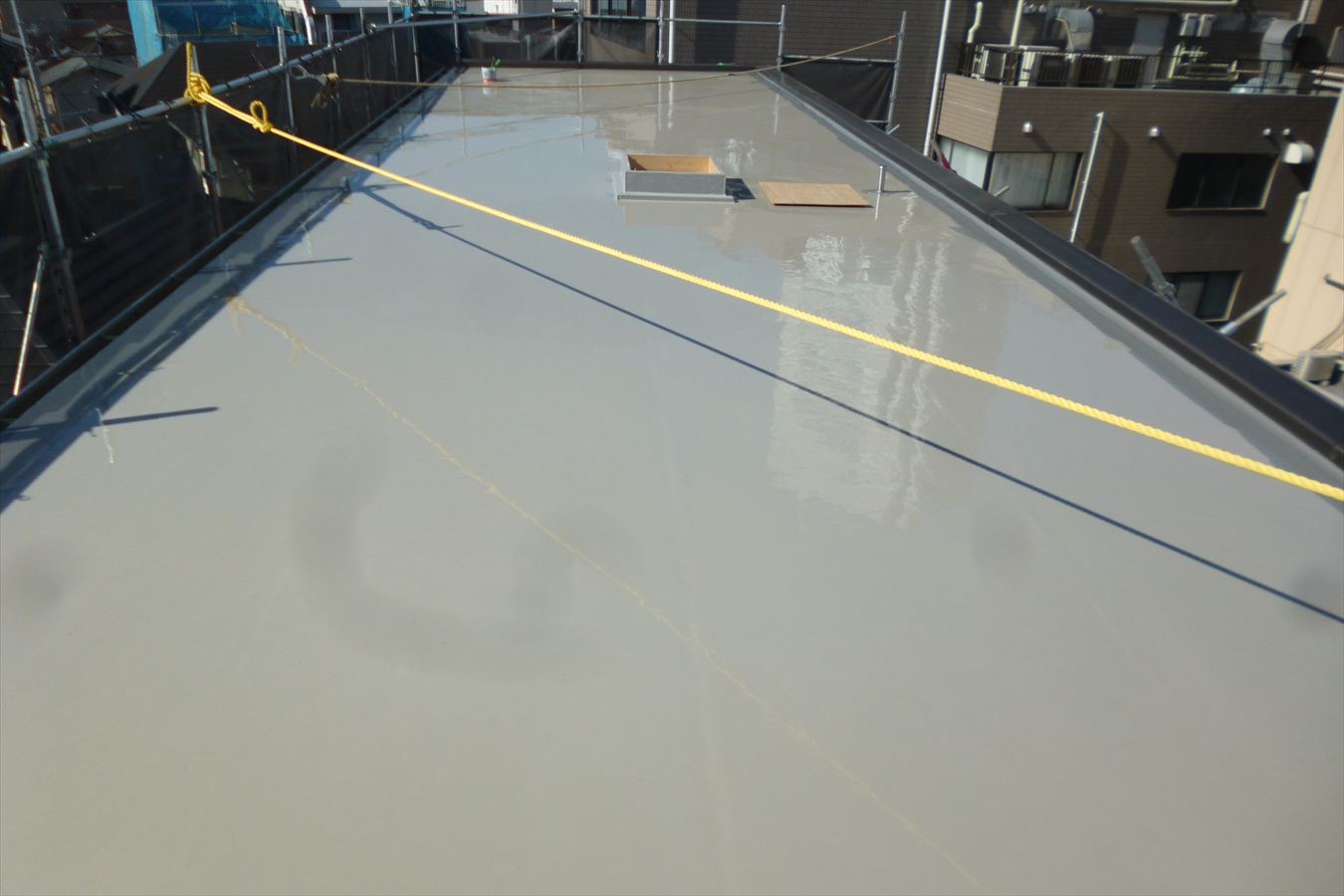
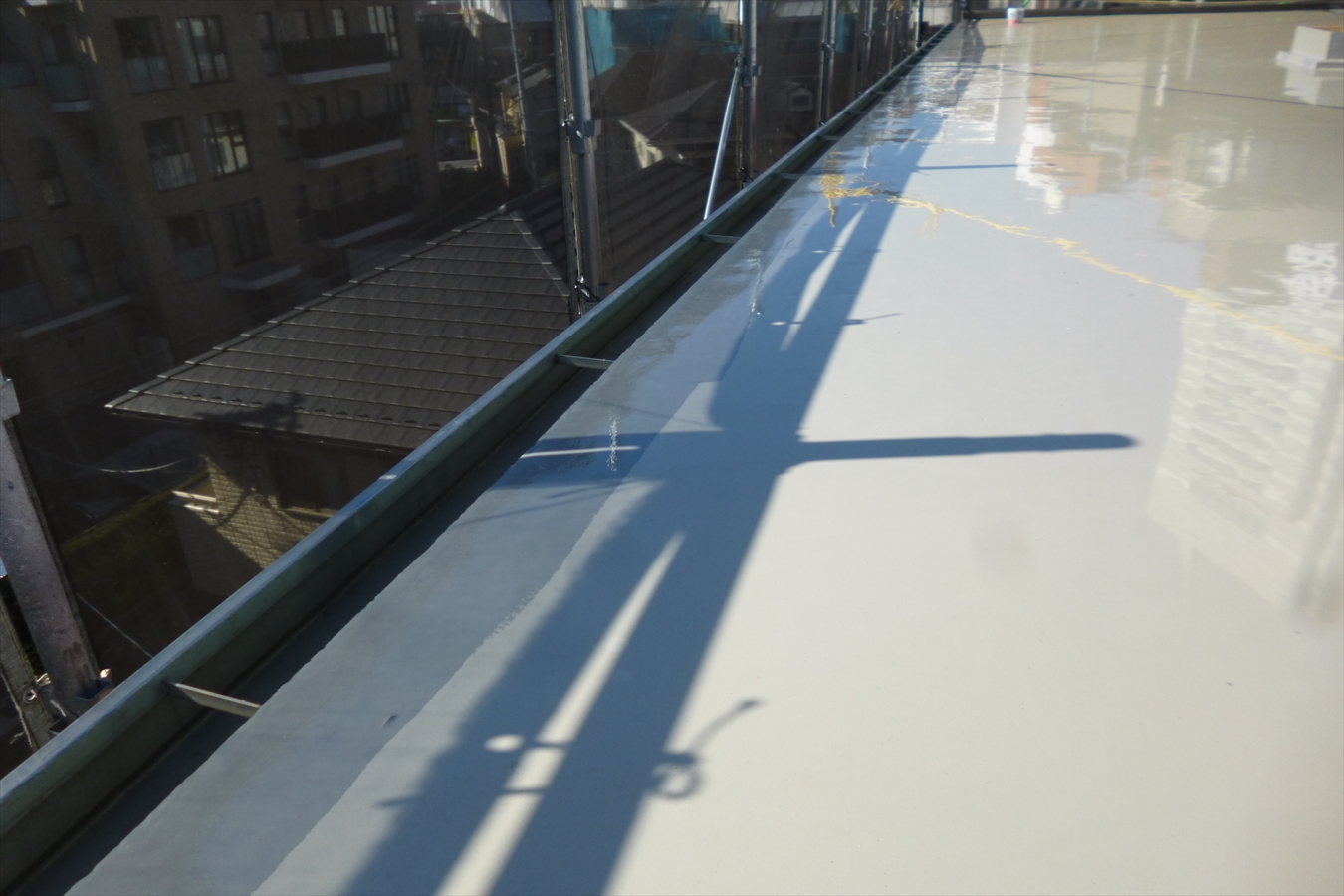
場所によってローラーの幅以上に塗られている箇所がありますが、これは土間にサラセーヌTを垂らしてしまった箇所です。
トップコートそのものは、どのメーカーのものでも一見するとただの液状の材料にしか見えない材料です。しかし土間へ水滴上に垂らし放置しておくと、そのまま硬化してしまうため垂らした箇所だけが出っ張ってしまったりと景観を損なう仕上がりとなってしまいます。
そのためトップコートを垂らしてしまったら、刷毛やローラーで潰す必要があり、そのような箇所のみ余計に塗られることになります。
土間 トップコート塗布
トップライトの枠周り、立ち上がりが終わって一番最後に手をつけるのが土間です。ウレタン防水ではこのように、プライマー、ウレタン、トップコート、これらすべて最初に枠やアンテナ架台などの役物、立ち上がりから手をつけていき、一番最後に土間の作業で終わらせるようになっています。
土間は他と違い、トップコートの塗りムラが非常に目立ちやすい箇所なので、適当に塗ったくるというわけにはいきません。ローラーを同じ方向に、一定の幅を決めて塗っていくという塗り方が一般的な塗り方です。また、絶対に必要ではありませんが、土間のトップコート塗布の時、長柄と台車を用意しておくと作業をスムーズに進めることができます。
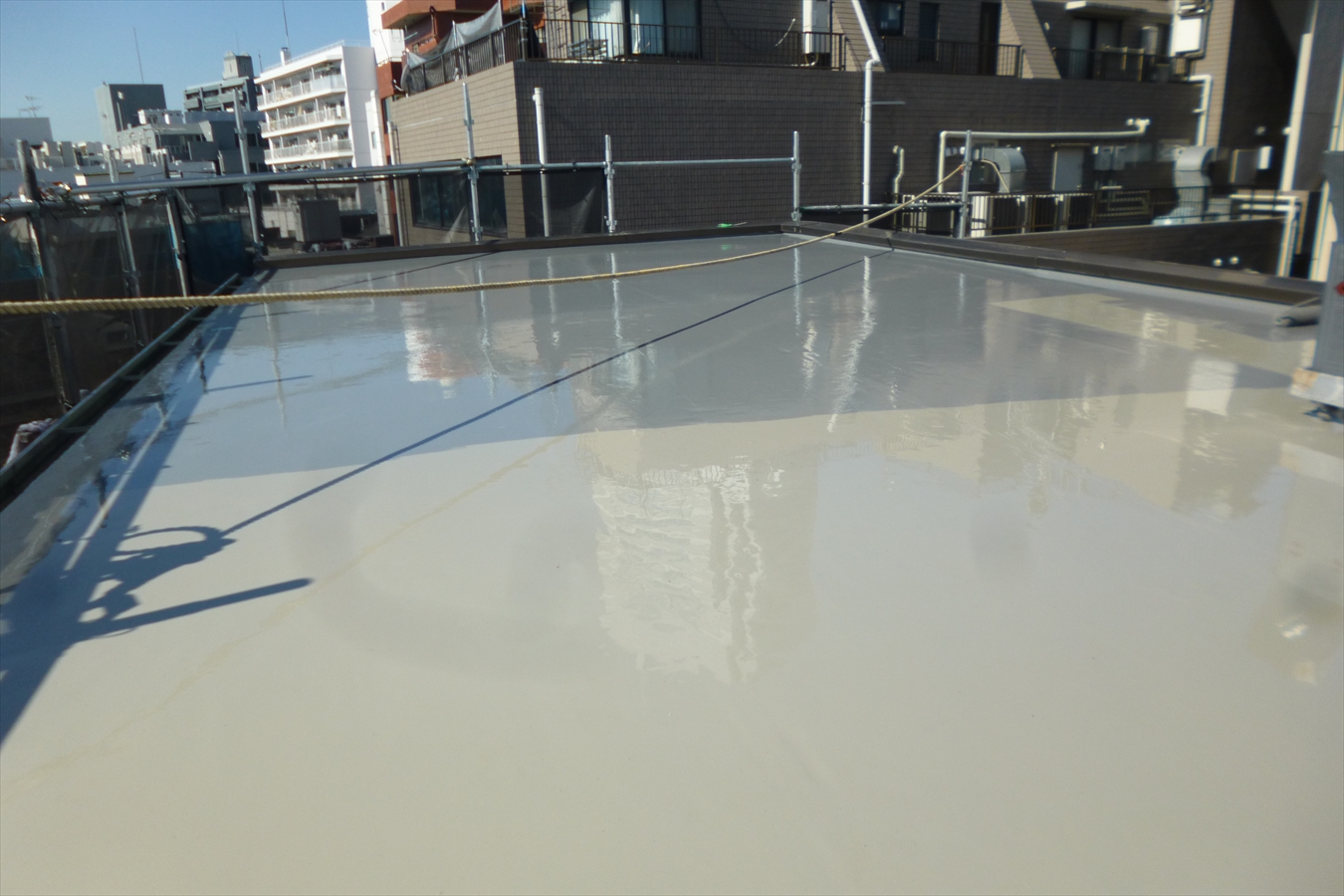
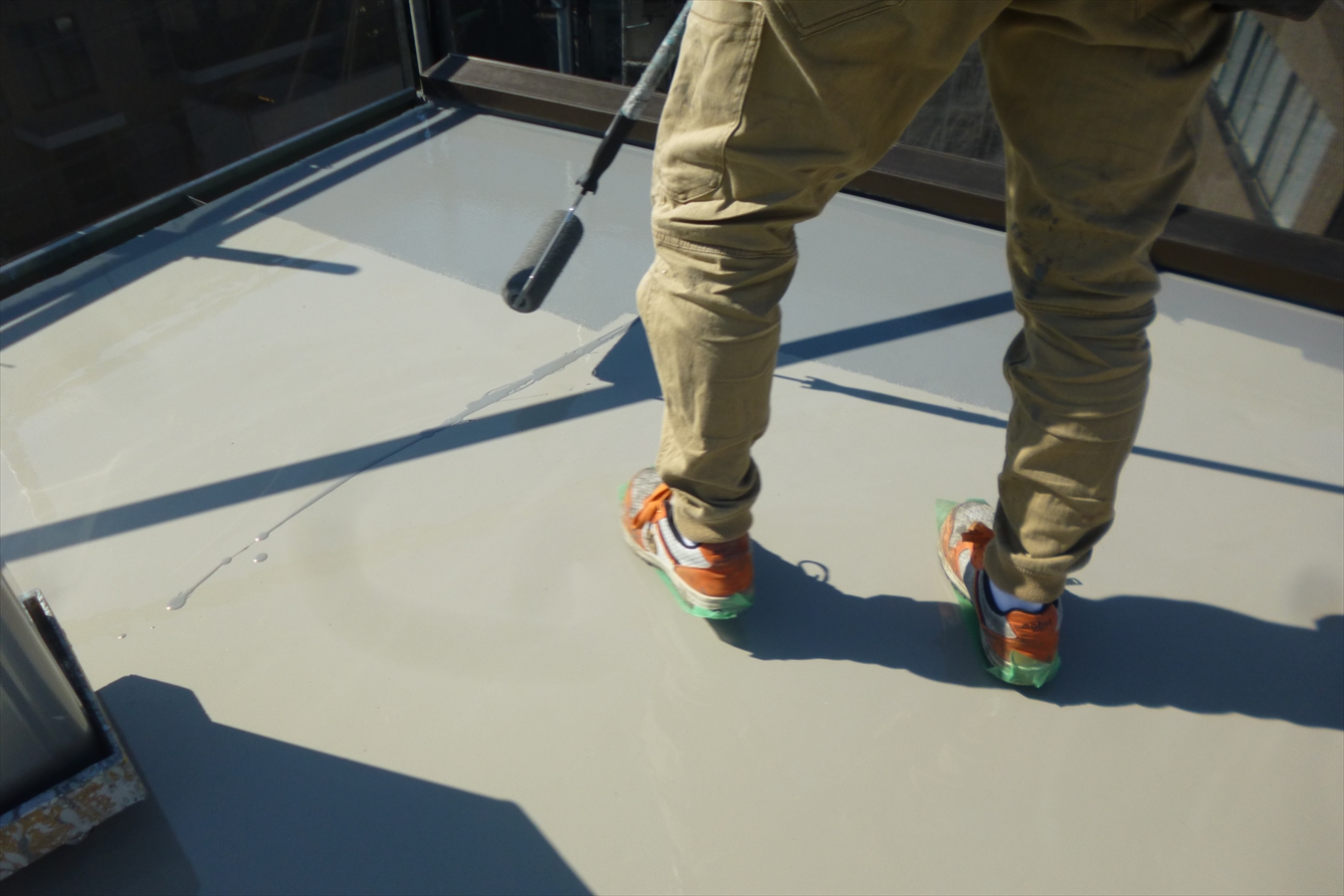
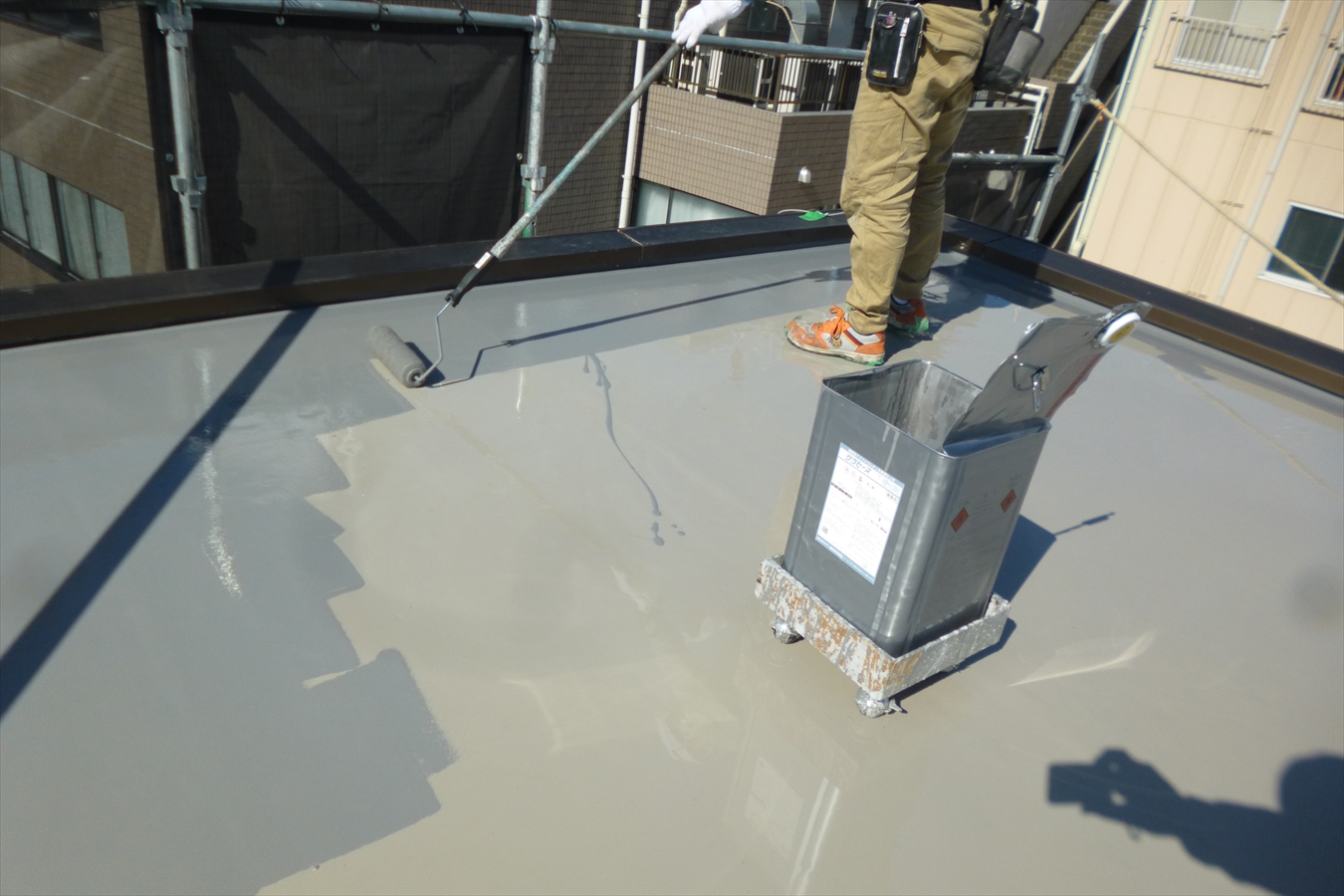
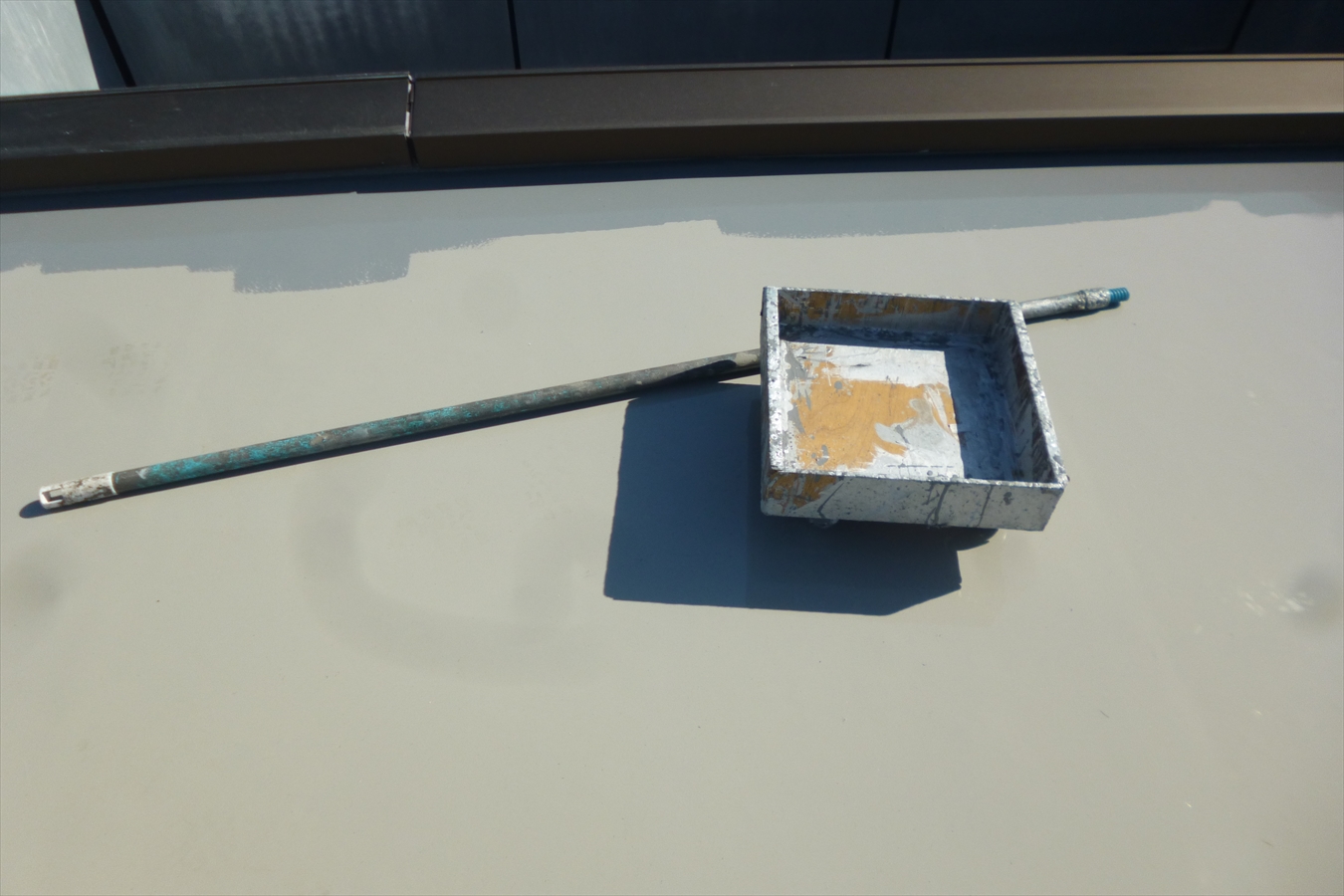
実際にサラセーヌTを塗っているところです。トップコートも屋上の出入り口から一番離れたところから作業を始め、出入口を最後に仕上げるようにしています。一番最後はアルミ笠木の上から塗っています。こうすることで塗ったサラセーヌTを踏まずに仕上げることができます。
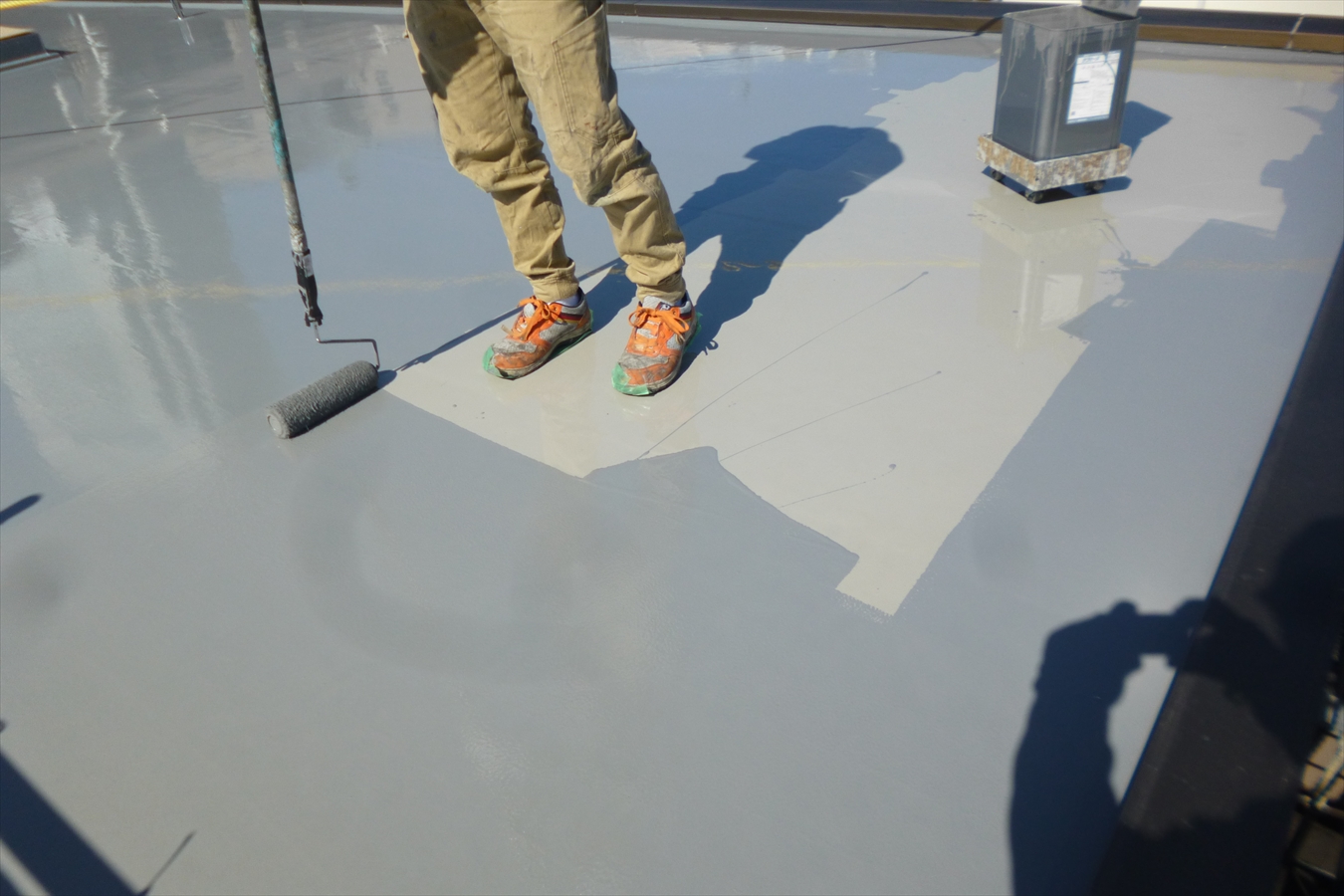
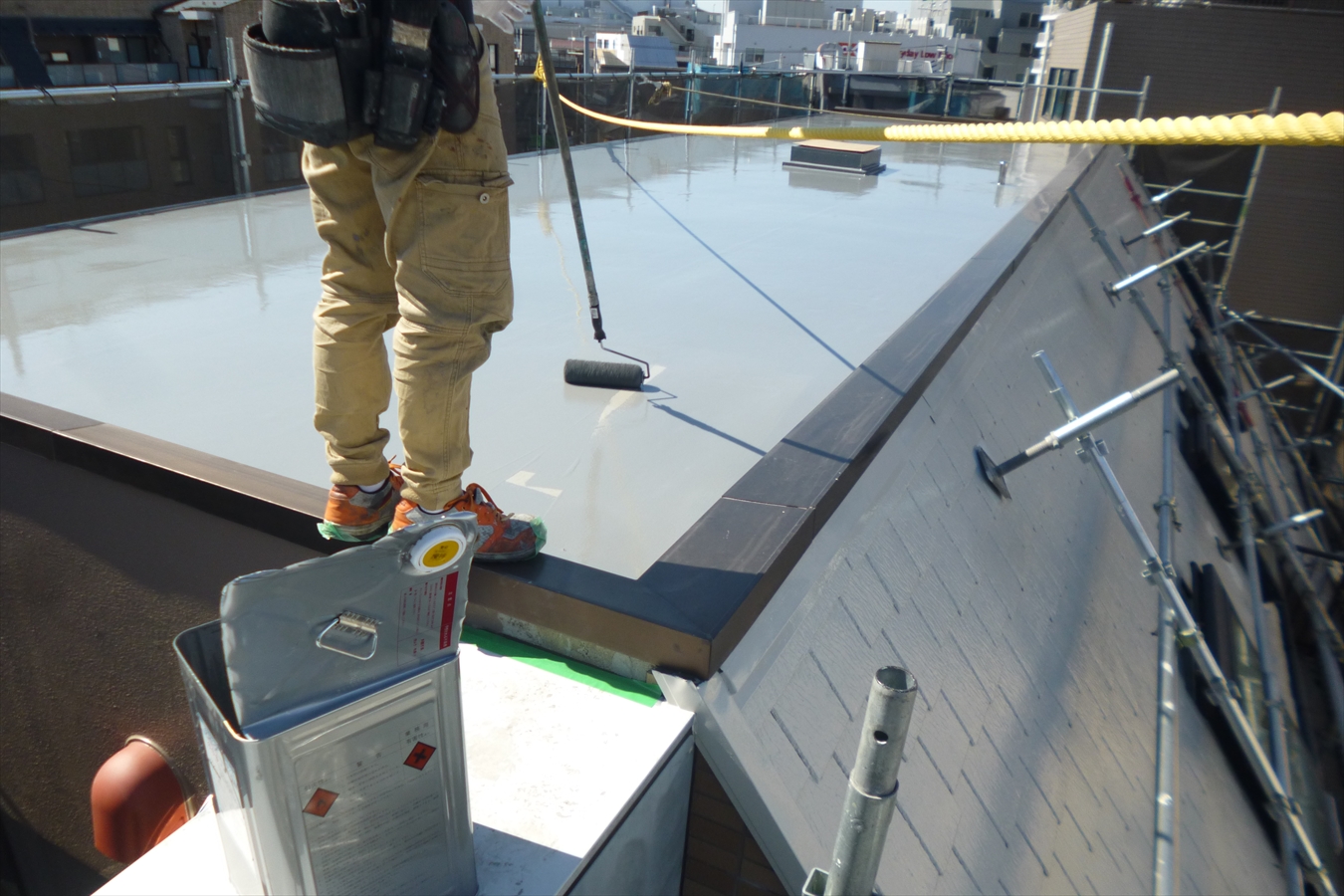
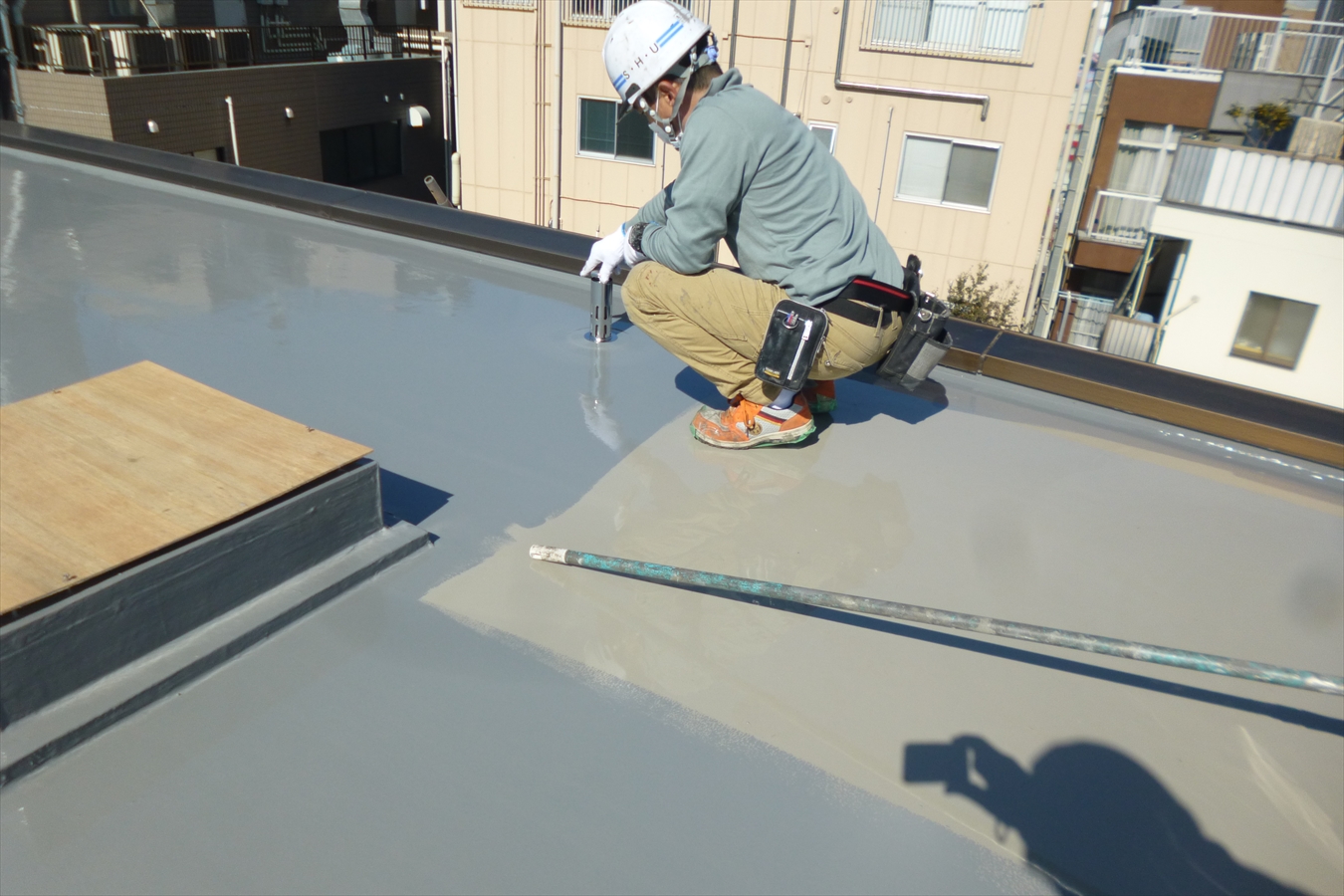
施工後
屋上のウレタン防水、施工後の写真です。土間の表面に、うっすらと近隣の建物が写っています。このような鏡のような仕上がりは、ウレタンの厚みが十分でないと得られないもので、そのことからもウレタンの厚みは十分だということが分かるのではないでしょうか?
雨が降った翌日は雨水を弾いています。これで台風や大雨強風時も雨漏りに不安なく過ごせるかと思います。また、脱気筒も完ぺきかと思います。
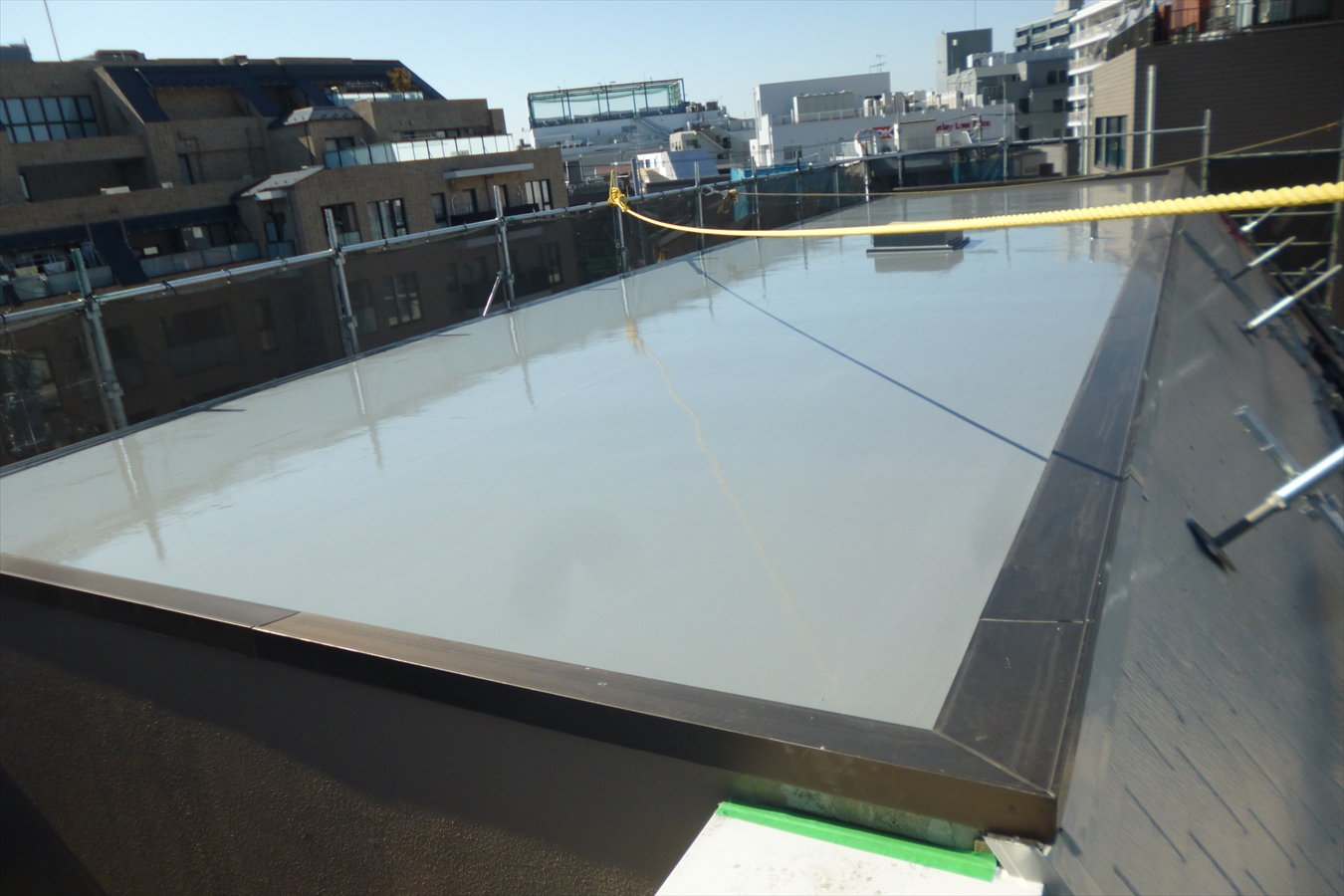
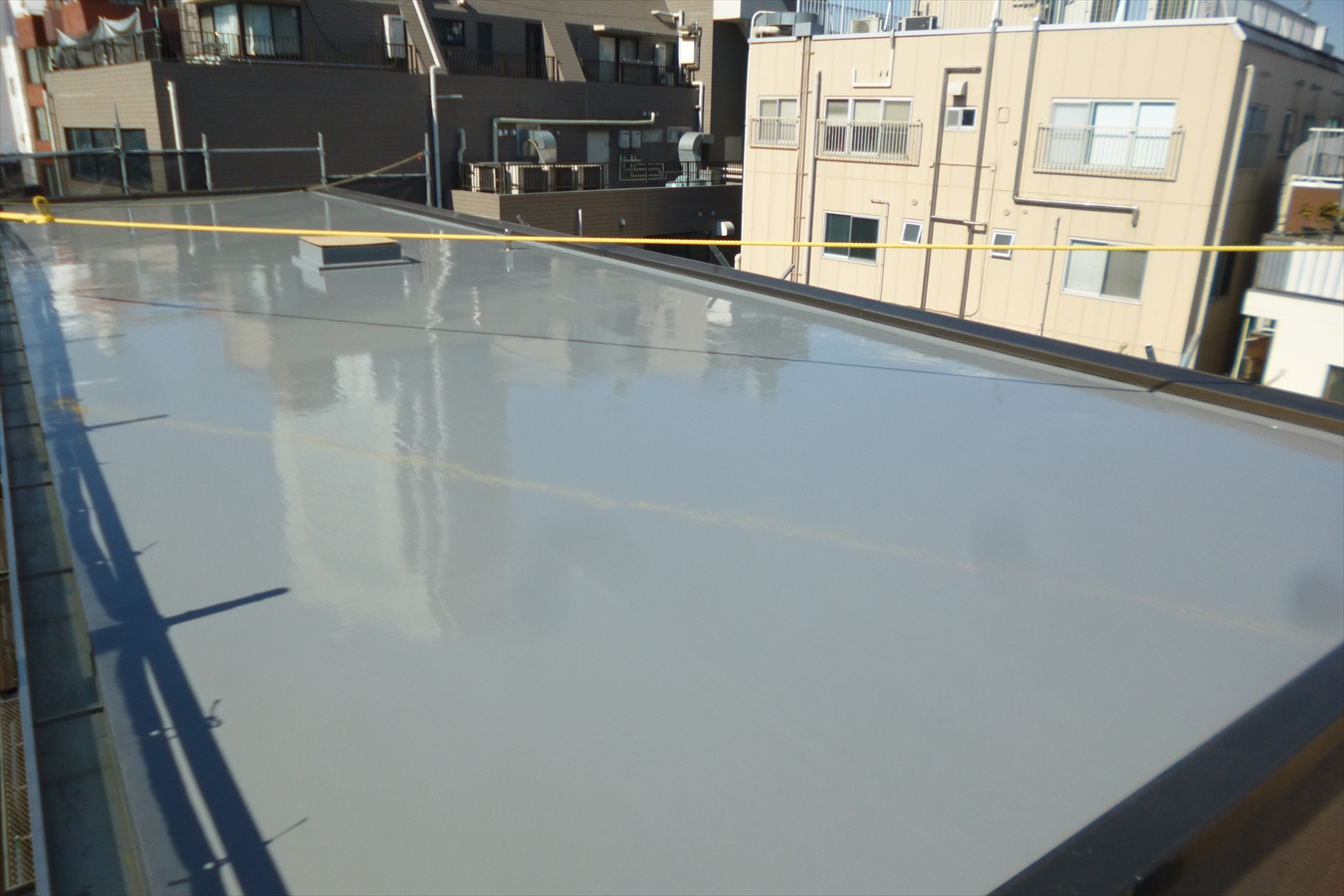
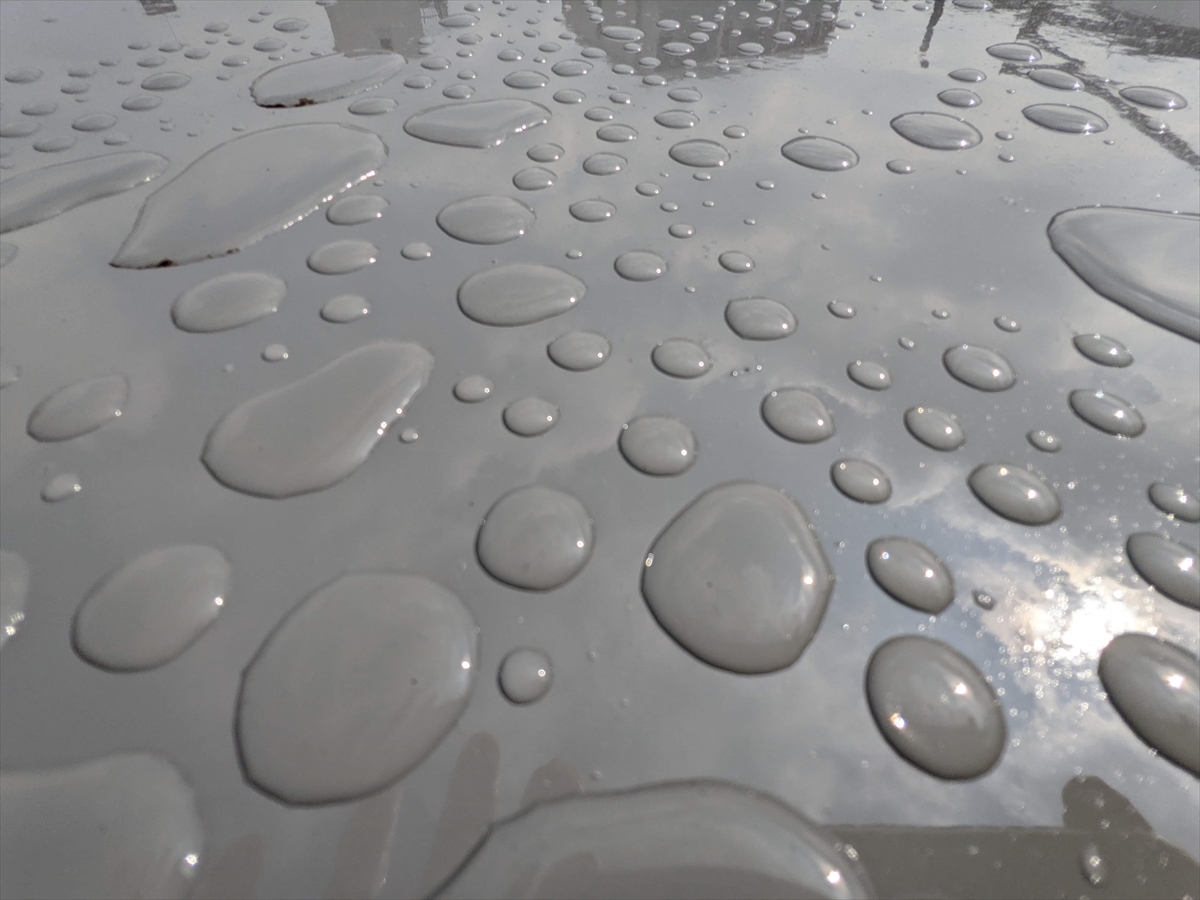
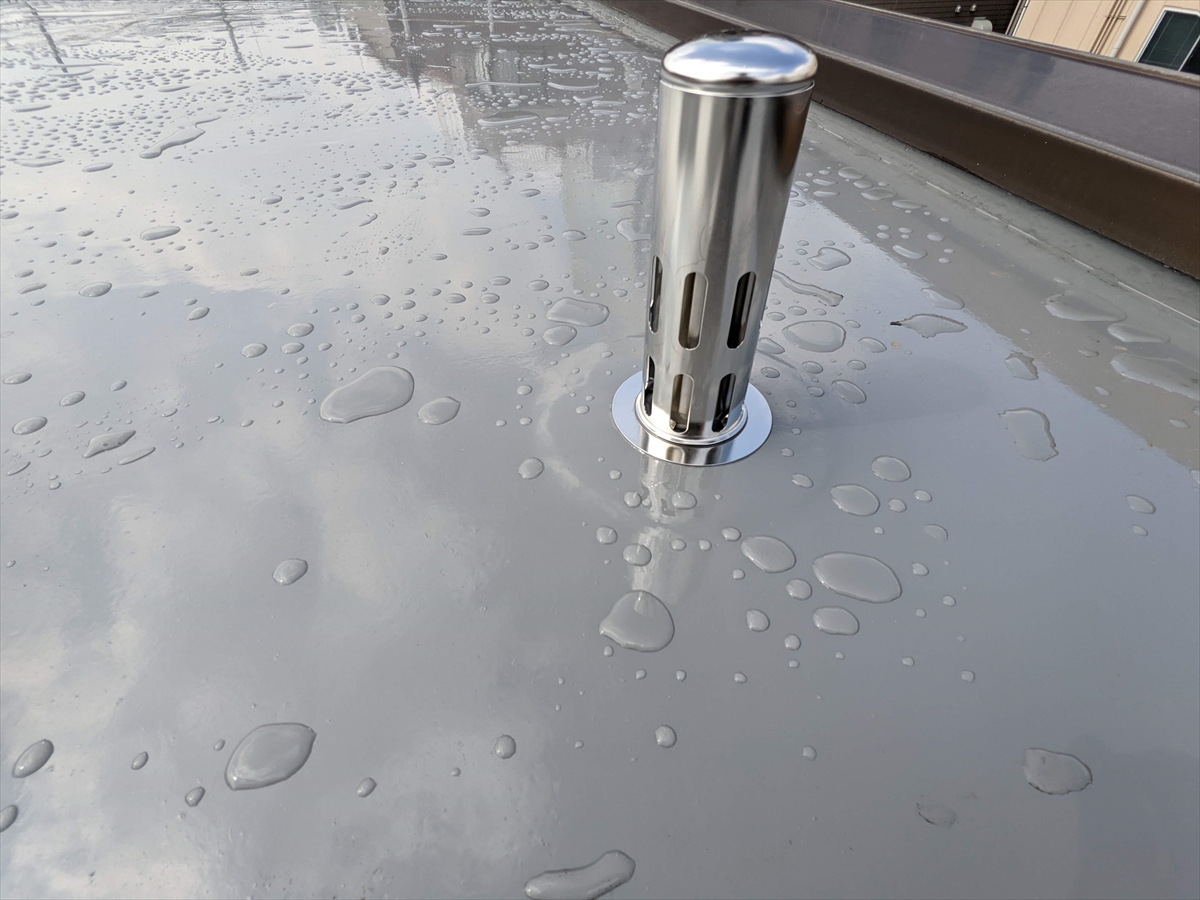
笠木の下のわずかな立ち上がりですが、防水工事は床面の土間からの雨漏りは、よほど悪質な工事でない限りありません。もし漏水するとしたらこのような端末部にある笠木やパラペット付近からです。このわずかな隙間もウレタンをたっぷり塗布しています。
今回雨漏り原因の一つだったトップライトは室内への自然採光が増しました。
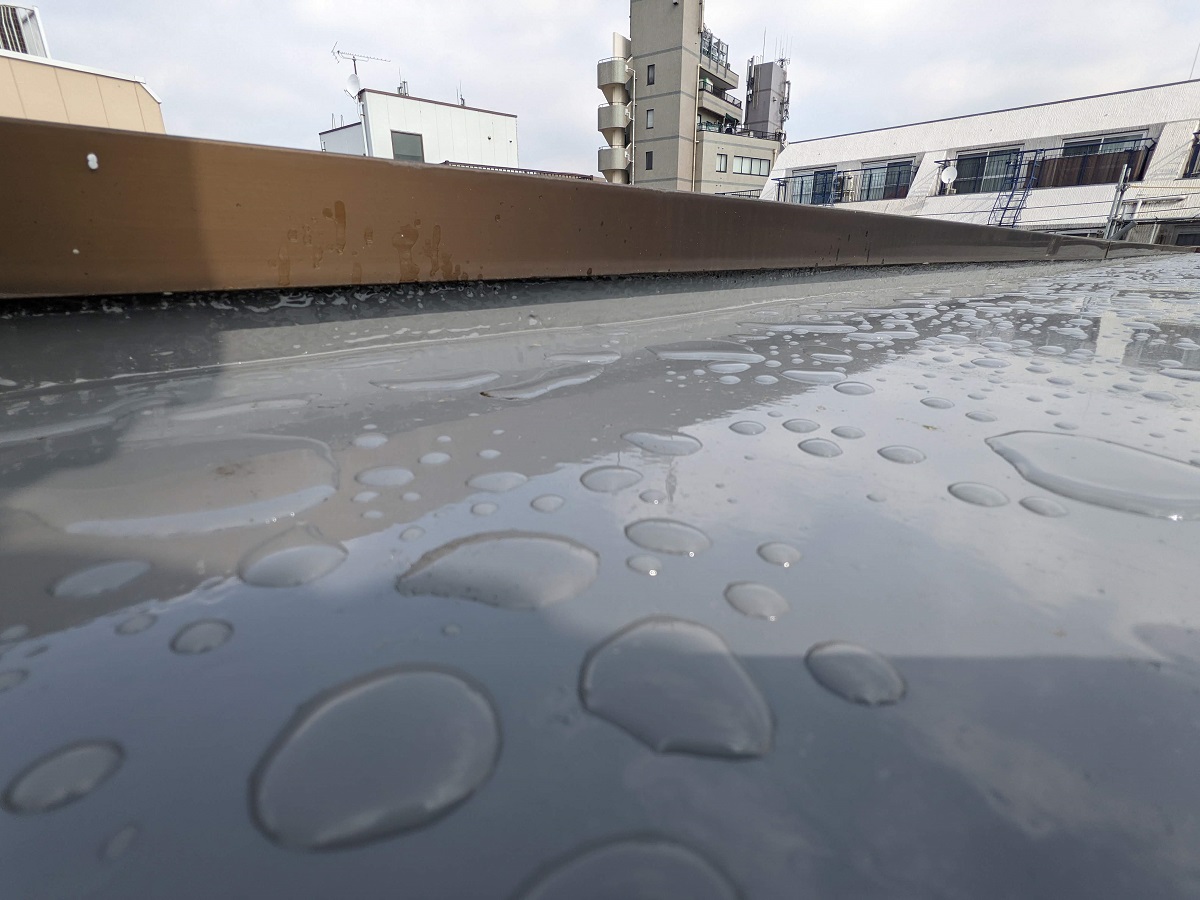
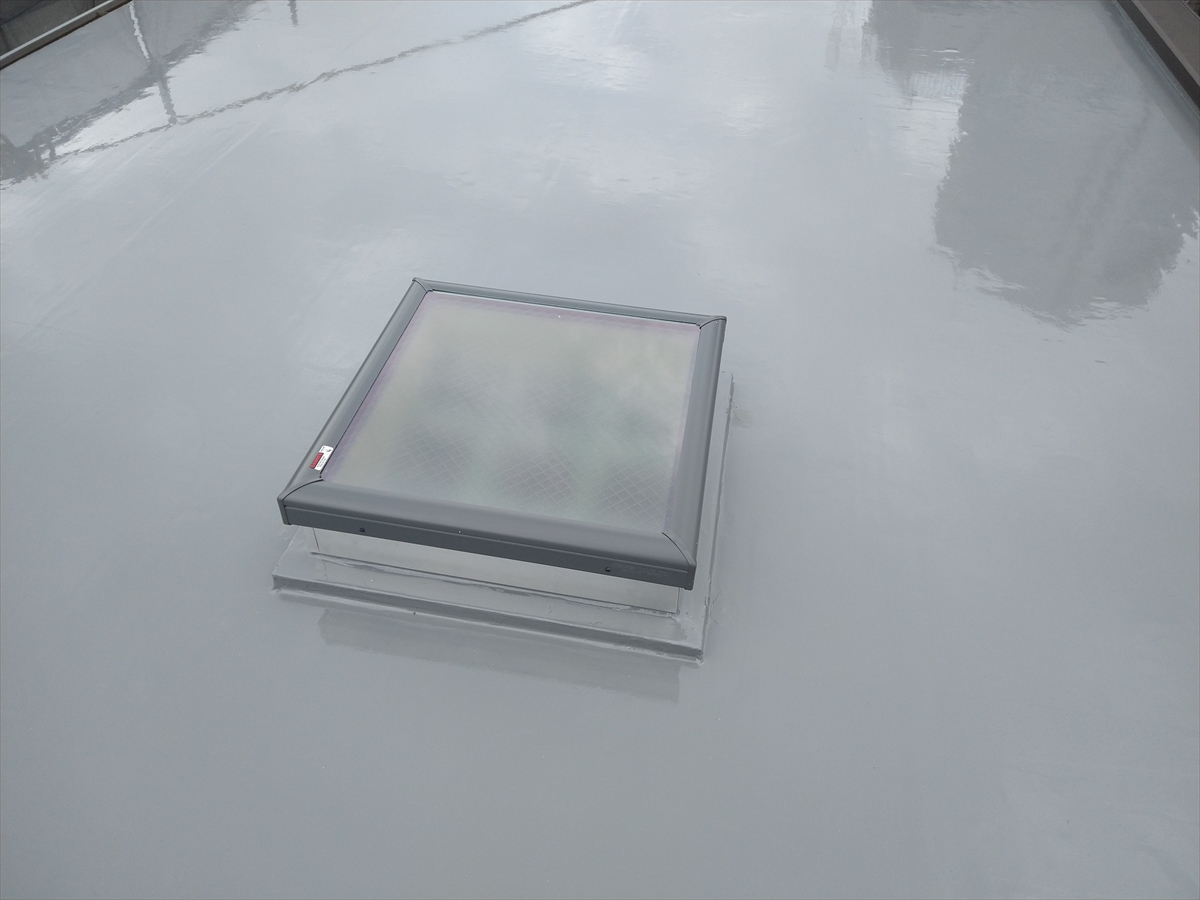
屋上の防水工事はこれで完了となります。
今回は世田谷区での施工でした。ご覧の通り世田谷ビジネススクエアの近くでの工事でしたが、屋上土間にも反射しています。

屋上防水はウレタンの他、塩ビシートやアスファルトなどがありますが、やはり作業性がよく今後のメンテナンスを考えると部分補修も可能なウレタンに軍配が上がると思います。
こちらは過去に何度も業者さんに雨漏り工事をしたものの結局止まらずうちでウレタン防水をさせて頂いた参考の動画です。